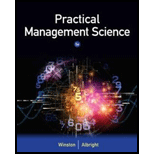
Practical Management Science
5th Edition
ISBN: 9781305250901
Author: Wayne L. Winston, S. Christian Albright
Publisher: Cengage Learning
expand_more
expand_more
format_list_bulleted
Question
Chapter 12, Problem 33P
Summary Introduction
To determine: The number of cases of soda the company should order.
Inventory and supply chain models:
The functions of inventory and supply chain are one of the most important business decision areas for an organization. The first important aspect of these concepts is to have adequate inventory on hand. The second important aspect is to carry a little amount of inventory as possible.
Expert Solution & Answer

Want to see the full answer?
Check out a sample textbook solution
Students have asked these similar questions
Already got wrong answer
Plz Don't use chatgpt
The RTY calculation for the following process steps would be:
A ➡
○ A.YA+YB+YC+YD
OB. (YA)(YB)(YCYD)
OC. ((YA+YB+YC+YD)/4)*4
○ D. (1/YA)+(1/YB)+(1/YC)+YD
B
C D
Can you guys help me with this?
1. What did you learn about the case, the concepts of transformational leadership; transactional leadership; Herzberg's Two Factors; Maslow's Hierarchy of needs theories that been applied through the case?
Here is the case: Theranos (2003-2018):Overview: Theranos promised to revolutionize blood testing but was exposed formisleading claims about its technology, leading to its collapse
2. What did you learn about the case between Elon Musk and Twitter, the concepts of transformational leadership; transactional leadership; Herzberg's Two Factors Theory; Maslow's Hierarchy of needs theories that been applied through the case?
3. What did you learn about the case of Blockbuster's decline and their failure to adapt with digital streaming, the concepts of autocratic leadership; transactional leadership; Herzberg's Two Factors; Maslow's Hierarchy of needs theories that been applied through the case?
Chapter 12 Solutions
Practical Management Science
Ch. 12.4 - Prob. 1PCh. 12.4 - Prob. 2PCh. 12.4 - Prob. 3PCh. 12.4 - Prob. 4PCh. 12.4 - Prob. 5PCh. 12.4 - Prob. 6PCh. 12.4 - Prob. 7PCh. 12.4 - Prob. 8PCh. 12.4 - Prob. 9PCh. 12.4 - Prob. 10P
Ch. 12.4 - Prob. 11PCh. 12.5 - Prob. 12PCh. 12.5 - Prob. 13PCh. 12.5 - Prob. 14PCh. 12.5 - Prob. 15PCh. 12.5 - Prob. 16PCh. 12.5 - Prob. 17PCh. 12.5 - Prob. 18PCh. 12.5 - Prob. 19PCh. 12.5 - Prob. 20PCh. 12.5 - Prob. 21PCh. 12 - Prob. 27PCh. 12 - Prob. 28PCh. 12 - Prob. 29PCh. 12 - Prob. 30PCh. 12 - Prob. 31PCh. 12 - Prob. 32PCh. 12 - Prob. 33PCh. 12 - Prob. 34PCh. 12 - Prob. 35PCh. 12 - Prob. 36PCh. 12 - Prob. 38PCh. 12 - Prob. 39PCh. 12 - Prob. 40PCh. 12 - Prob. 42PCh. 12 - Prob. 43PCh. 12 - Prob. 44PCh. 12 - Prob. 45PCh. 12 - Prob. 46PCh. 12 - Prob. 47PCh. 12 - Prob. 48PCh. 12 - Prob. 49PCh. 12 - Prob. 53PCh. 12 - Prob. 54PCh. 12 - In terms of K, D, and h, what is the average...Ch. 12 - Prob. 56PCh. 12 - Prob. 57PCh. 12 - Prob. 58PCh. 12 - Prob. 59PCh. 12 - Prob. 60PCh. 12 - Prob. 61PCh. 12 - Prob. 62PCh. 12 - Prob. 63PCh. 12 - Prob. 64PCh. 12 - Prob. 65PCh. 12 - Prob. 66PCh. 12 - Prob. 67PCh. 12 - Prob. 68PCh. 12 - Prob. 69PCh. 12 - Prob. 70PCh. 12 - Prob. 71PCh. 12 - Prob. 1.1CCh. 12 - Prob. 1.2CCh. 12 - Prob. 1.3C
Knowledge Booster
Similar questions
- Can you guys help me with this? 1. What did you learn about the case, the concepts of transformational leadership; transactional leadership; Herzberg's Two Factors; and Maslow's Hierarchy of needs theories that have been applied through the case? Here is the case: The COVID-19 Pandemic Response (2020-Present): Overview: Global leaders had to navigate an unprecedented health crisis, balancingpublic health needs with economic pressures. 2. What did you learn about the case, the concepts of transformational leadership; transactional leadership; Herzberg's Two Factors Theory; and Maslow's Hierarchy of Needs theories that have been applied through the case? Here's the case: Google Glass (2013):Overview: Google launched its augmented reality glasses with high expectations, butprivacy concerns and limited functionality led to poor adoption 3. What did you learn about the case of Kodak's failure to keep up with digital photography, the concepts of autocratic leadership; transformational…arrow_forwardWith the above information do the following:1. Based on the From-To chart presented develop an ActivityRelationship Chart for this operation.2. Develop a Space-Relationship Diagram for this operation.3. Evaluate the actual layout using the “Distance Traveled byProduct” technique discussed in class (use rectilinear distance inall calculations).4. Develop two layout improvement alternatives.5. Evaluate alternatives using the “Distance Traveled by Product”technique discussed in class (use rectilinear distance in allcalculations).6. Make a layout recommendation based on alternatives evaluatedarrow_forwardProvide at least two examples of layouts strategies for the table attached. We provided an example for office. Office Retail Warehouse (storage) Project (fixed position) Job shop (process oriented) Work cell (product families) Repetitive/Continuous (product oriented)arrow_forward
- By integrating theory and application by referencing pertinent theories and practical corporate examples, detail the evolution of qualityarrow_forwardI need typing clear urjent no chatgpt used i will give 5 upvotes pls full explainarrow_forwardBy integrating theory and application by referencing pertinent theories and practical corporate examples,detail the philosophy of quality managementarrow_forward
- Quality professionals in quality-focused organizations often assume four roles. Identify these four responsibilities and detail their application throughout an organization to improve quality.arrow_forwardAs a Quality Management Consultant tasked to deliver a thorough presentation to corporate board members to augment their understanding and appreciation of quality management.Detail the significance of qualityarrow_forwardIn recent times, there has been a substantial decrease in client volume inside an organization, resulting in a notable loss in sales revenue. Senior management is inquiring why numerous clients abruptly ceased patronizing the organization. As the Quality Manager, tasked with gathering data to determine the source of the decrease in customer numbers,elaborate on the two ways for collecting pertinent customer data and specify the type of information to be gathered to resolve the issue.arrow_forward
- James McGregor delineates approximately seven characteristics of an effective leader. From these seven characteristics, detail five and elucidate their application within an organization to exemplify effective leadership.arrow_forwardBy integrating theory and application by referencing pertinent theories and practical corporate examples,detail the costs associated with poor qualityarrow_forwardHenry Mintzberg recognized ten managerial positions relevant to an organization, categorized into three overarching groups. Identify the 10 responsibilities across all three categories and illustrate how each might be utilized to improve quality of service delivery at the Meatco of Namibia or similar organization.Detail in essay formatarrow_forward
arrow_back_ios
SEE MORE QUESTIONS
arrow_forward_ios
Recommended textbooks for you
- Practical Management ScienceOperations ManagementISBN:9781337406659Author:WINSTON, Wayne L.Publisher:Cengage,
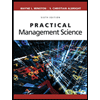
Practical Management Science
Operations Management
ISBN:9781337406659
Author:WINSTON, Wayne L.
Publisher:Cengage,