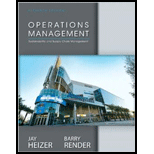
Operations Management
11th Edition
ISBN: 9780132921145
Author: Jay Heizer
Publisher: PEARSON
expand_more
expand_more
format_list_bulleted
Concept explainers
Textbook Question
Chapter 11.S, Problem 13P
Question
•• S11.13 Your options for shipping $100,000 of machine parts from Baltimore to Kuala Lumpur Malaysia, are (1) use a ship that will take 30 days at a cost of $3,800 or (2) truck the parts to Los Angeles and then ship at a total cost of $4,800. The second option will take only 20 days. You are paid via a letter of credit the day the parts arrive. Your holding cost is estimated at 30% of the value per year.
- a. Which option is more economical?
- b. What customer issues are not included in the data presented?
Expert Solution & Answer

Want to see the full answer?
Check out a sample textbook solution
Students have asked these similar questions
Question 2: Metro Tech buys three components from a local wholesaler. The annual demand
for components A, B, and C is 500, 3000, and 6000 units respectively. The agreed purchase
price is $20, $15, and $10per unit for A, B, and C respectively for each product. The holding
cost is estimated to be 20% per year. The ordering cost consists of handling and trucking
costs. The handling cost is $100 for each type of component regardless of the number of items
ordered. In addition to the handling cost, Metro Tech must pay a trucking cost of $500 for each
delivery regardless of the total number of components in the order. Currently, all three items
are being ordered independently using EOQ models. A proposal has been made to combine the
ordering of the three items to save on trucking costs. Analyze the current and the prosed
scenario and show the results below.
Input Data:
Demand items/year
Item Cost in $/item
Holding Cost as %/year
Ordering Cost $/order
# of Orders/ year
Economic Order Quantity…
Q 7. Explain the importance of multi-channel marketplace models.
Question 2
Adopting new technologies into logistics enables companies to plan, forecast, and replenish inventories and keep up with customer demands. The application of information technology in logistical approaches helps businesses improve delivery time and accuracy.
Besides new technology adoption to support inventory purchasing, further elaborate on any FIVE (5) considerations between social and environmental factors in the purchasing
Chapter 11 Solutions
Operations Management
Ch. 11.S - Prob. 1DQCh. 11.S - Question: 2. It the probability of a super-event...Ch. 11.S - Question: 3. If the probability of a super-event...Ch. 11.S - Question: 4. Describe some ramifications of the...Ch. 11.S - Question: 5. Describe causes of the bullwhip...Ch. 11.S - Question: 6. Describe how the bullwhip measure can...Ch. 11.S - Question: 7. Describe some potentially useful...Ch. 11.S - Prob. 8DQCh. 11.S - Question: 9. Describe some disadvantages of using...Ch. 11.S - Question S11.1 How would you go about attempting...
Ch. 11.S - Question S11.2 Phillip Witt, president of Witt...Ch. 11.S - Question S11.3 Still concerned about the risk in...Ch. 11.S - Question S11.4 Johnson Chemicals is considering...Ch. 11.S - Prob. 5PCh. 11.S - Question S11.6 Consider the supply chain...Ch. 11.S - Question S11.7 Over the past 5 weeks, demand for...Ch. 11.S - Prob. 8PCh. 11.S - Prob. 9PCh. 11.S - Question S11.10 As purchasing agent for Woolsey...Ch. 11.S - Question S11.11 Using the data in Problem S11.10,...Ch. 11.S - Question S11.12 Develop a vendor-rating form that...Ch. 11.S - Question S11.13 Your options for shipping 100,000...Ch. 11.S - Prob. 14PCh. 11.S - Prob. 15PCh. 11.S - Question S11.16 Recently, Abercrombie Fitch (AF)...Ch. 11 - Prob. 1DQCh. 11 - Prob. 2DQCh. 11 - Prob. 3DQCh. 11 - Prob. 4DQCh. 11 - Question 5. What is vertical integration? Give...Ch. 11 - Question 6 What are three basic approaches to...Ch. 11 - Prob. 7DQCh. 11 - Question 8. What is the difference between...Ch. 11 - Question 9. What is CPFR?Ch. 11 - Question 10. What is the value of online auctions...Ch. 11 - Question: 11. Explain how FedEx uses the Internet...Ch. 11 - Question 12. How does Walmart use drop shipping?Ch. 11 - Prob. 13DQCh. 11 - Question: 14. What can purchasing do to implement...Ch. 11 - Question 15. What is e-procurement?Ch. 11 - Prob. 16DQCh. 11 - Question: 17. What is SCOR, and what purpose does...Ch. 11 - Question: 11.1 Choose a local establishment that...Ch. 11 - Prob. 2PCh. 11 - Question: 11.3 Hau Lee Furniture, Inc., described...Ch. 11 - Question: 11.4 Kamal Fatehl, production manager...Ch. 11 - Question: 11.5 Baker Mfg. Inc. (see Table 11.9)...Ch. 11 - Question: 11.6 Arrow Distributing Corp. (see...Ch. 11 - Question: 11.7 The grocery industry has an annual...Ch. 11 - Question: 11.8 Mattress Wholesalers, Inc., is...Ch. 11 - Question: Dardens Global Supply Chains Video Case...Ch. 11 - Prob. 2CSCh. 11 - Question: Dardens Global Supply Chains Video Case...Ch. 11 - Prob. 4CSCh. 11 - Question Supply Chain Management at Regal Marine ...Ch. 11 - Question Supply Chain Management at Regal Marine ...Ch. 11 - Question Supply Chain Management at Regal Marine ...Ch. 11 - Prob. 2.1VCCh. 11 - Prob. 2.2VCCh. 11 - Prob. 2.3VCCh. 11 - Prob. 2.4VC
Knowledge Booster
Learn more about
Need a deep-dive on the concept behind this application? Look no further. Learn more about this topic, operations-management and related others by exploring similar questions and additional content below.Similar questions
- QUESTION 2a. A manufacturing company Glass Items Manufacturing Limited (GIM), operating under acontinuous review system, has an average demand of 150 units per week for the item it produces.The standard deviation in weekly demand is 30 units. The lead-time for the item is seven weeks,and it costs the company $70 to process each order. The holding cost for each unit is $30 per year.The company operates 52 weeks per year.A normal distribution table is appended to this assignment. (ii) Use the information in 2 a. above. What is the Reorder Point, if the company has a policy ofmaintaining a 98% cycle-service level? Please answer the question abovearrow_forwardQUESTION 2a. A manufacturing company Glass Items Manufacturing Limited (GIM), operating under acontinuous review system, has an average demand of 150 units per week for the item it produces.The standard deviation in weekly demand is 30 units. The lead-time for the item is seven weeks,and it costs the company $70 to process each order. The holding cost for each unit is $30 per year.The company operates 52 weeks per year.A normal distribution table is appended to this assignment. (i) Use the information in 2 a. above. What is the desired safety stock level, if the company has apolicy of maintaining a 98% cycle-service level?arrow_forwardQuestion 2, Problem 12arrow_forward
- Question 2 Prince Electronics, a manufacturer of consumer electronic goods, has five distribution centers in different regions of the country. For one of its products, a highspeed modem priced at $340 per unit, the average weekly demand at each distribution center is 70 units. Average shipment size to each distribution center is 400 units, and average lead time for delivery is 2 weeks. Each distribution center carries 2 week's supply as safety stock but holds no anticipation inventory. On average, how many dollars of pipeline inventory will be in transit to each distribution center? $________________________ (Enter your response as an integer.) How much total inventory (cycle, safety, and pipeline) does Prince hold for all five distribution centers? __________________________units. (Enter your response as an integer.)arrow_forwardAnswer full questionarrow_forwardQuestion: The purchasing agent for a company that assembles and sells air- conditioning equipment in a Latin American country noted that the cost of compressors has increased significantly each time they have been reordered. The company uses an EOQ model to determine order size. What are the implications of this price escalation with respect to order size? What factors other than price must be taken into consideration?arrow_forward
- QUESTION 1:A confectioner buys plastic boxes in bulk and uses them to pack chocolates. The annual requirement of these boxes is 1,200, and each box costs $30. The ordering and carrying costs are $10 per order and 20%, respectively. The supplier from whom the confectioner purchases these boxes sells them only in lots of 25, that is, you only purchase quantities in multiples of 25 boxes.(a) How many boxes should the confectioner order so as to minimise inventory total stocking costs?(b) If the supplier offers 2% discount on the cost of each box when the purchases are in quantities of 300 at a time, should the confectioner accept this offer?(c) Suppose the supplier has decided that instead of the 2% discount offer the following price breaks will be used:ORDER QUANTITY COST PER BOXLess than 100 $30.00100 to 199 $29.75200 or more $29.60What order quantity should the confectioner make?arrow_forwardQUESTION 1 Identify each of the following as an asset, contra asset, liability, or equity.arrow_forwardQUESTION 10 You plan to get in a position of short-the-basis by selling cash corn in June basis JUL and buying it in August when the basis is trading against the SEP. Which of the following pre-spread orders would you want to enter to provide you with the most favorable structure for your anticipated short-the-basis position? O Buy JUL / Sell SEP at a 25¢ premium to the JUL Buy JUL/Sell SEP at a 25¢ premium to the SEP Buy SEP / Sell JUL at a 25¢ premium to the SEP O Buy SEP / Sell JUL at a 25¢ premium to the JULarrow_forward
- Q.2 AI Muhannad Industrial and Domestic Services, Oman requires on average 4000 sheets of A4 size papers per day at its different office locations in Muscat. Each time the purchase manager orders centrally the A4 size papers, the total expenses incurred to the company are estimated to be 10.6 OMR per order. Presently the company orders 350 reams of papers per order at a flat rate of 2.1 OMR per ream (one ream contains 500 A4 size papers). It takes almost a day for the local supplier to deliver the order. Considering the overall cost of the inventory and the manpower involved, the annual carrying costs for the company is estimated to be 35% of the cost for each ream of the paper. The company operates on 5 days a week over 46 weeks per year. (i) Is the present purchase policy economical for the company? If not, guide the purchase manager in selecting the best economical policy in terms of expected number of orders annually, ordered quantity per order, reorder point and the expected time…arrow_forwardQ6. Discuss the challenges and opportunities of multichannel distribution system highlighting the keyfunctions performed by them.arrow_forwardQuestion 6 (ABC Analysis) Use the information provided below and classifies the inventory items according to the ABC classification. Item: Annual demand: Unit Price N$: 1 1000 0.50 2 100 250 3 50 1000 4 50 800 5 300 50 6 500 10 7 500 7arrow_forward
arrow_back_ios
SEE MORE QUESTIONS
arrow_forward_ios
Recommended textbooks for you
- Practical Management ScienceOperations ManagementISBN:9781337406659Author:WINSTON, Wayne L.Publisher:Cengage,Operations ManagementOperations ManagementISBN:9781259667473Author:William J StevensonPublisher:McGraw-Hill EducationOperations and Supply Chain Management (Mcgraw-hi...Operations ManagementISBN:9781259666100Author:F. Robert Jacobs, Richard B ChasePublisher:McGraw-Hill Education
- Purchasing and Supply Chain ManagementOperations ManagementISBN:9781285869681Author:Robert M. Monczka, Robert B. Handfield, Larry C. Giunipero, James L. PattersonPublisher:Cengage LearningProduction and Operations Analysis, Seventh Editi...Operations ManagementISBN:9781478623069Author:Steven Nahmias, Tava Lennon OlsenPublisher:Waveland Press, Inc.
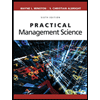
Practical Management Science
Operations Management
ISBN:9781337406659
Author:WINSTON, Wayne L.
Publisher:Cengage,
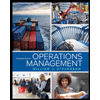
Operations Management
Operations Management
ISBN:9781259667473
Author:William J Stevenson
Publisher:McGraw-Hill Education
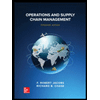
Operations and Supply Chain Management (Mcgraw-hi...
Operations Management
ISBN:9781259666100
Author:F. Robert Jacobs, Richard B Chase
Publisher:McGraw-Hill Education
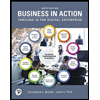
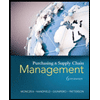
Purchasing and Supply Chain Management
Operations Management
ISBN:9781285869681
Author:Robert M. Monczka, Robert B. Handfield, Larry C. Giunipero, James L. Patterson
Publisher:Cengage Learning
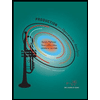
Production and Operations Analysis, Seventh Editi...
Operations Management
ISBN:9781478623069
Author:Steven Nahmias, Tava Lennon Olsen
Publisher:Waveland Press, Inc.
Inventory Management | Concepts, Examples and Solved Problems; Author: Dr. Bharatendra Rai;https://www.youtube.com/watch?v=2n9NLZTIlz8;License: Standard YouTube License, CC-BY