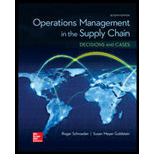
OPERATIONS MANAGEMENT IN THE SUPPLY CHAIN: DECISIONS & CASES (Mcgraw-hill Series Operations and Decision Sciences)
7th Edition
ISBN: 9780077835439
Author: Roger G Schroeder, M. Johnny Rungtusanatham, Susan Meyer Goldstein
Publisher: McGraw-Hill Education
expand_more
expand_more
format_list_bulleted
Concept explainers
Textbook Question
Chapter 11, Problem 2P
The Ace Steel Mill estimates the demand for steel in millions of tons per year as follows:
Millions of Tons | Probability |
10 | .10 |
12 | .25 |
14 | .30 |
16 | .20 |
18 | .15 |
- a. If capacity is set at 18 million tons, how much of a capacity cushion is there?
- b. What is the probability of idle capacity, and what is the average utilization of the plant at 18 million tons of capacity?
- c. If it costs $8 million per million tons of lost business and S8o million to build a million tons of capacity, how much capacity should be built to minimize total costs?
Expert Solution & Answer

Want to see the full answer?
Check out a sample textbook solution
Students have asked these similar questions
1: Suppose the company has identified the following three possible demand scenarios: Demand (Units per year) Probability 25,000 0.3 60,000 0.4 100,000 0.3 1. If the capacity is set at 80,000, how much of a capacity cushion is here? What is the capacity utilization? 2. What is the probability of idle capacity if the capacity is 80,000? 3. If it costs $25 per units lost business and $50 to build a unit of capacity, how much capacity should be built to minimize total cost?
31 please help me please!A company has a factory that is designed so that it is most efficient (average unit cost is minimized) when producing 19,200 units output each month. However, it has an absolute maximum output capability of 23,000 units per month, and can produce as little 7,000 units per month without corporate headquarters shifting production to another plant. If the factory produces 13,280 units ir
October, what is the capacity utilization rate in October for this factory?
Note: Round your answer to 1 decimal place.
A biotech firm is considering abandoning its old plant, built 23 years ago, andconstructing a new facility that has 50% more square footage. The original cost of the old facility was $300,000, and its capacity in terms of standardizedproduction units is 250,000 units per year. The capacity of the new laboratoryis to be 400,000 units per year. During the past 23 years, costs of laboratoryconstruction have risen by an average of 5% per year. If the cost-capacity factor, based on square footage, is 0.80, what is the estimated cost of the newlaboratory?
Chapter 11 Solutions
OPERATIONS MANAGEMENT IN THE SUPPLY CHAIN: DECISIONS & CASES (Mcgraw-hill Series Operations and Decision Sciences)
Ch. 11 - Prob. 1DQCh. 11 - Prob. 2DQCh. 11 - A school district has forecast student enrollment...Ch. 11 - Prob. 4DQCh. 11 - Prob. 5DQCh. 11 - SOP or aggregate planning sometimes is confused...Ch. 11 - The XYZ Company manufactures a seasonal product....Ch. 11 - Prob. 8DQCh. 11 - Every firm has multiple objectives such as good...Ch. 11 - Prob. 10DQ
Ch. 11 - Prob. 11DQCh. 11 - Suppose we are considering the question of how...Ch. 11 - The Ace Steel Mill estimates the demand for steel...Ch. 11 - A barbershop has the following demand for haircuts...Ch. 11 - Prob. 4PCh. 11 - Prob. 5PCh. 11 - eXcel The Chewy Candy Company would like to...Ch. 11 - A company produces to a seasonal demand, with the...Ch. 11 - Prob. 8PCh. 11 - Question: 9. The Restwell Motel in Orlando,...Ch. 11 - eXcel 10. The Ban go Toy Company produces several...Ch. 11 - A small textile company makes several types of...Ch. 11 - Valley View Hospital faces somewhat seasonal...
Knowledge Booster
Learn more about
Need a deep-dive on the concept behind this application? Look no further. Learn more about this topic, operations-management and related others by exploring similar questions and additional content below.Similar questions
- Differentiate between design capacity and capacity utilization. Briefly describe three capacity expansion strategies. An airline company must plan its fleet capacity and long-term schedule of aircraft usage. For one flight segment, the average number of customers per day is 70, which represents a 65 percentage utilization rate of the equipment assigned to the flight segment. If demand is expected to increase to 84 customers for this flight segment in three years, and management requires a capacity cushion of 25 percent, calculate the following:- the planned capacity requirement. the maximum number of customers the flight segment can accommodate. the efficiency rate of the flight segment assuming that the current effective capacity of the flight segment is 93 customers.arrow_forwardHow does planning for capacity in service differ from planning for capacity in manufacturing?arrow_forwardAn airline company must plan its fleet capacity and long-term schedule of aircraft usage. For oneflight segment, the average number of customers per day is 70, which represents a 65 percentageutilization rate of the equipment assigned to the flight segment. If demand is expected toincrease to 84 customers for this flight segment in three years, and management requires acapacity cushion of 25 percent, calculate the following: i. the planned capacity requirement. ii. the maximum number of customers the flight segment can accommodate.iii. the efficiency rate of the flight segment assuming that the current effective capacity of theflight segment is 93 customers.arrow_forward
- Expando, Inc, is considering the possibility of building an additional factory that would produce a new addition to its product line. The company is currently considering two options. The first is a small facility that it could build at a cost of $7 million. If demand for new products is low, the company expects to receive $9 million in discounted revenues (present value of future revenues) with the small facility. On the other hand, if demand is high, it expects $14 milon in discounted revenues using the small facility. The second option is to build a large factory at a cost of $8 million. Were demand to be low, the company would expect $9 million in discounted revenues with the large plant. If demand is high, the company estimates that the discounted revenues would be $15 million. In either case, the probability of demand being high is 0.30, and the probability of it being low is 070. Not constructing a new factory would result in no additional revenue being generated because the…arrow_forwardSpectrum Hair Salon is considering expanding itsbusiness, as it is experiencing a large growth. Th e question iswhether it should expand with a bigger facility than needed,hoping that demand will catch up, or with a small facility,knowing that it will need to reconsider expanding in three years.Th e management at Spectrum has estimated the followingchances for demand:• Th e likelihood of demand being high is 0.70.• Th e likelihood of demand being low is 0.30.Estimated profi ts for each alternative are as follows:• Large expansion has an estimated profi tability of either$100,000 or $70,000, depending on whether demand turnsout to be high or low.• Small expansion has a profi tability of $50,000, assuming thatdemand is low.• Small expansion with an occurrence of high demand wouldrequire considering whether to expand further. If thebusiness expands at this point, the profi tability is expected tobe $90,000. If it does not expand further, the profi tability isexpected to be $60,000.arrow_forwardSpectrum Hair Salon is considering expanding itsbusiness, as it is experiencing a large growth. Th e question iswhether it should expand with a bigger facility than needed,hoping that demand will catch up, or with a small facility,knowing that it will need to reconsider expanding in three years.Th e management at Spectrum has estimated the followingchances for demand:• Th e likelihood of demand being high is 0.70.• Th e likelihood of demand being low is 0.30.Estimated profi ts for each alternative are as follows:• Large expansion has an estimated profi tability of either$100,000 or $70,000, depending on whether demand turnsout to be high or low.• Small expansion has a profi tability of $50,000, assuming thatdemand is low.• Small expansion with an occurrence of high demand wouldrequire considering whether to expand further. If thebusiness expands at this point, the profi tability is expected tobe $90,000. If it does not expand further, the profi tability isexpected to be $60,000.Draw a…arrow_forward
- After deciding to have three machines to meet the forecast demand for the coming five years, you are considering the following information to decide on the best machines to buy. Alternative Economic life Investment/machine Salvage value/machine Capacity Italian 9 $200000 12000 100 unit/hour German 9 $250000 25000 100 unit/hour Japanese 9 220000 30000 100 unit/hour You are expecting to sell 2500 units a day 5 days a week at a unit cost of $3 with annual incease of 1%. Labor per hour per machine is $10 and expected to remain the same over the whole period. Annual material cost (including waste) is expected to be $250000 for the German machine, $220000 for the Italian and $200000 for the Japanese. Maintenance and other operating expenses (excluding depreciation) are expected to total $180000 per year with annual increase of 3%. Which machine would you buy if the the cost of capital (discount rate is 12%).arrow_forwardDeforrest Marine Motors manufactures engines for the speedboat racing circuit. As part of their annual planning cycle, they forecasted demand for the next four quarters. The number of available days of production and the anticipated demand are given below. Employees Production Rate Production Cost Backorder Cost Overtime Cost Overtime Limit Demand Q1 2,400 6,019,000 They also estimated many of the costs required to conduct operations planning. Some of these key figures are listed below. 30 70 units/employee/quarter Q2 2,200 $1,000/unit $200/unit/quarter $1,500/unit <= 25% of Reg. Production Q3 1,700 Q4 1,800 Hire Cost Fire Cost Subcontracting Cost Subcontracting Limit Inventory Cost Initial Inventory $1,200/employee $800/employee $1,800/unit 400 units maximum $100/unit/quarter 280 units Deforrest Marine Motors wishes to maintain the current number of employees for the entire year to follow a level strategy balanced with inventory and backorders as needed. What is the total cost of this…arrow_forwardProblem #3 – At Freeze Inc. the manufacturing of each air conditioning has a variable cost of $400 per unit and it takes place in a facility that has a monthly fixed cost of $200,000. A) If Freeze Inc. sells each unit at $1,200 how many units do they need to sell every month to break-even? B) What is the monthly revenue at the break-even point? C) What is the monthly variable cost at the break-even point?arrow_forward
- The Soma Inn is trying to determine its break-even point. The inn has 75 rooms that are rented at $60 a night. Operating costs are as follows. Salaries $10,600 per month Utilities 2,400 per month Depreciation 1,500 per month Maintenance 800 per month Maid service 8 per room Other costs 34 per room (a) Determine the inn’s break-even point in (1) number of rented rooms per month and (2) dollars. 1. Break-even point in rooms 2. Break-even point $ per montharrow_forwardA firm plans to begin production of a new small appliance. The manager must decide whether to purchase the motors for the appliance from a vendor at $7 each or to produce them in-house. Either of two processes could be used for in-house production; one would have an annual fixed cost of $160,000 and a variable cost of $5 per unit, and the other would have an annual fixed costof $190,000 and a variable cost of $4 per unit. Determine the range of annual volume for which each of the alternatives would be best.arrow_forwardExpando, Inc., is considering the possibility of building an additional factory that would produce a new addition to its product line. The company is currently considering two options. The first is a small facility that it could build at a cost of $6 million. If demand for new products is low, the company expects to receive $10 million in discounted revenues (present value of future revenues) with the small facility. On the other hand, if demand is high, it expects $12 million in discounted revenues using the small facility. The second option is to build a large factory at a cost of $9 million. Were demand to be low, the company would expect $10 million in discounted revenues with the large plant. If demand is high, the company estimates that the discounted revenues would be $14 million. In either case, the probability of demand being high is 40, and the probability of it being low is 60. Not constructing a new factory would result in no additional revenue being generated because the…arrow_forward
arrow_back_ios
SEE MORE QUESTIONS
arrow_forward_ios
Recommended textbooks for you
- Practical Management ScienceOperations ManagementISBN:9781337406659Author:WINSTON, Wayne L.Publisher:Cengage,
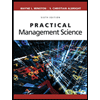
Practical Management Science
Operations Management
ISBN:9781337406659
Author:WINSTON, Wayne L.
Publisher:Cengage,
Inventory Management | Concepts, Examples and Solved Problems; Author: Dr. Bharatendra Rai;https://www.youtube.com/watch?v=2n9NLZTIlz8;License: Standard YouTube License, CC-BY