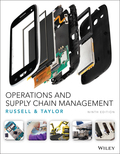
Operations and Supply Chain Management 9th edition
9th Edition
ISBN: 9781119320975
Author: Roberta S. Russell, Bernard W. Taylor III
Publisher: WILEY
expand_more
expand_more
format_list_bulleted
Concept explainers
Textbook Question
Chapter 1, Problem 6P
Omar Industries maintains production facilities in several locations around the globe. Average monthly cost data and output levels are given in the following tables.
- a. Calculate the labor productivity of each facility.
- b. Calculate the multifactor productivity of each facility.
- c. If Omar needed to close one of the plants, which one would you choose?
Expert Solution & Answer

Want to see the full answer?
Check out a sample textbook solution
Students have asked these similar questions
Scenario
You have been given a task to create a demand forecast for the second year of sales of a premium outdoor grill.
Accurate forecasts are important for many reasons, including for the company to ensure they have the materials
they need to create the products required in a certain period of time. Your objective is to minimize the forecast
error, which will be measured using the Mean Absolute Percentage Error (MAPE) with a goal of being below 25%.
You have historical monthly sales data for the past year and access to software that provides forecasts based on
five different forecasting techniques (Naïve, 3-Month Moving Average, Exponential Smoothing for .2, Exponential
Smooth for .5, and Seasonal) to help determine the best forecast for that particular month. Based on the given
data, you will identify trends and patterns to create a more accurate forecast.
Approach
Consider the previous month's forecast to identify which technique is most effective. Use that to forecast the next…
Approach
Consider the previous month's forecast to identify which technique is most effective. Use that to forecast the next
month.
Remember to select the forecasting technique that produces the forecast error nearest to zero. For example:
a. Naïve Forecast is 230 and the Forecast Error is -15.
b. 3-Month Moving Forecast is 290 and the Forecast Error is -75.
c. Exponential Smoothing Forecast for .2 is 308 and the Forecast Error is -93.
d. Exponential Smoothing Forecast for .5 is 279 and the Forecast Error is -64.
e. Seasonal Forecast is 297 and the Forecast Error is -82.
The forecast for the next month would be 230 as the Naïve Forecast had the Forecast Error closest to zero with a
-15. This forecasting technique was the best performing technique for that month. You do not need to do any
external analysis-the forecast error for each strategy is already calculated for you in the tables below.
Naïve
Month Period
Actual
Demand
Naïve Forecast
Error
3-
Month
Moving
Forecast
3-
Month
Moving…
Scenario
You have been given a task to create a demand forecast for the second year of sales of a premium outdoor grill.
Accurate forecasts are important for many reasons, including for the company to ensure they have the materials
they need to create the products required in a certain period of time. Your objective is to minimize the forecast
error, which will be measured using the Mean Absolute Percentage Error (MAPE) with a goal of being below 25%.
You have historical monthly sales data for the past year and access to software that provides forecasts based on
five different forecasting techniques (Naïve, 3-Month Moving Average, Exponential Smoothing for .2, Exponential
Smooth for .5, and Seasonal) to help determine the best forecast for that particular month. Based on the given
data, you will identify trends and patterns to create a more accurate forecast.
Approach
Consider the previous month's forecast to identify which technique is most effective. Use that to forecast the next…
Chapter 1 Solutions
Operations and Supply Chain Management 9th edition
Ch. 1.S - Prob. 1PCh. 1.S - Prob. 2PCh. 1.S - Prob. 3PCh. 1.S - Prob. 4PCh. 1.S - Prob. 5PCh. 1.S - In Problem S1-5 assume that Nicole, with the help...Ch. 1.S - Prob. 7PCh. 1.S - Prob. 8PCh. 1.S - Telecomp, a computer manufacturer with a global...Ch. 1.S - Prob. 10P
Ch. 1.S - Prob. 11PCh. 1.S - Prob. 12PCh. 1.S - Prob. 13PCh. 1.S - Prob. 14PCh. 1.S - Prob. 15PCh. 1.S - Prob. 16PCh. 1.S - Prob. 17PCh. 1.S - Prob. 18PCh. 1.S - In Problem S1-18, assume the Weight Club is able...Ch. 1.S - Prob. 20PCh. 1.S - Prob. 21PCh. 1.S - Prob. 22PCh. 1.S - Prob. 23PCh. 1.S - Prob. 24PCh. 1.S - Prob. 25PCh. 1.S - Prob. 26PCh. 1.S - Prob. 27PCh. 1.S - Prob. 28PCh. 1.S - Prob. 29PCh. 1.S - Prob. 30PCh. 1.S - Prob. 31PCh. 1.S - Prob. 33PCh. 1.S - Prob. 34PCh. 1.S - Alex Mason has a wide-curving, uphill driveway...Ch. 1.S - Prob. 36PCh. 1.S - Prob. 39PCh. 1.S - Prob. 40PCh. 1.S - State University has three healthcare plans for...Ch. 1.S - The Orchard Wine Company purchases grapes from one...Ch. 1.S - Prob. 43PCh. 1.S - Prob. 1.1CPCh. 1.S - Prob. 2.1CPCh. 1.S - Evaluating Projects at Nexcom Systems Nexcom...Ch. 1 - Feeding America Each year, the Feeding America...Ch. 1 - Feeding America Each year, the Feeding America...Ch. 1 - Feeding America Each year, the Feeding America...Ch. 1 - Feeding America Each year, the Feeding America...Ch. 1 - Prob. 1QCh. 1 - What constitutes operations at (a) a bank, (b) a...Ch. 1 - Prob. 3QCh. 1 - Prob. 4QCh. 1 - Prob. 5QCh. 1 - Prob. 17QCh. 1 - What is the difference between an order winner and...Ch. 1 - Prob. 21QCh. 1 - Prob. 22QCh. 1 - Prob. 23QCh. 1 - Prob. 24QCh. 1 - Prob. 1PCh. 1 - Prob. 2PCh. 1 - Prob. 3PCh. 1 - Prob. 4PCh. 1 - Prob. 5PCh. 1 - Omar Industries maintains production facilities in...Ch. 1 - Rushing yardage for three Heisman Trophy...Ch. 1 - Carpet City recorded the following data on carpet...Ch. 1 - Prob. 9PCh. 1 - Prob. 10PCh. 1 - Prob. 11PCh. 1 - Prob. 12PCh. 1 - Prob. 13PCh. 1 - Prob. 14PCh. 1 - Prob. 15PCh. 1 - Prob. 1.1CPCh. 1 - Prob. 1.2CPCh. 1 - Prob. 1.3CPCh. 1 - Prob. 1.4CPCh. 1 - Prob. 1.5CPCh. 1 - Prob. 2.1CPCh. 1 - Prob. 2.2CP
Additional Business Textbook Solutions
Find more solutions based on key concepts
Discussion Analysis A13-41 Discussion Questions 1. How do managers use the statement of cash flows? 2. Describ...
Managerial Accounting (5th Edition)
Preparing Financial Statements from a Trial Balance The following accounts are taken from Equilibrium Riding, I...
Fundamentals of Financial Accounting
DECISION-MAKING ACROSS THE ORGANIZATION
CT10-8 On January l, 2015, Picard Corporation issued $3,000,000, 5-year...
Financial Accounting: Tools for Business Decision Making, 8th Edition
Determine the price elasticity of demand if, in response to an increase in price of 10 percent, quantity demand...
Microeconomics
Describe and evaluate what Pfizer is doing with its PfizerWorks.
Management (14th Edition)
The flowchart for the process at the local car wash. Introduction: Flowchart: A flowchart is a visualrepresenta...
Principles of Operations Management: Sustainability and Supply Chain Management (10th Edition)
Knowledge Booster
Learn more about
Need a deep-dive on the concept behind this application? Look no further. Learn more about this topic, operations-management and related others by exploring similar questions and additional content below.Similar questions
- Use the internet to obtain crash safety ratings for passenger vehicles. Then, answer thesequestions:a. Which vehicles received the highest ratings? The lowest ratings?b. How important are crash-safety ratings to new car buyers? Does the degree of importancedepend on the circumstances of the buyer?c. Which types of buyers would you expect to be the most concerned with crash-safety ratings?d. Are there other features of a new car that might sway a buyer from focusing solely on crashsafety? If so, what might they be?arrow_forward“Implementing a Performance Management Communication Plan at Accounting, Inc.” Evaluate Accounting Inc.’s communication plan. Specifically, does it answer all of the questions that a good communication plan should answer? Which questions are left unanswered? How would you provide answers to the unanswered questions? “Implementing an Appeals Process at Accounting, Inc.” If you were to design an appeals process to handle these complaints well, what would be the appeal process? Describe the recommended process and why.arrow_forwardThe annual demand for water bottles at Mega Stores is 500 units, with an ordering cost of Rs. 200 per order. If the annual inventory holding cost is estimated to be 20%. of unit cost, how frequently should he replenish his stocks? Further, suppose the supplier offers him a discount on bulk ordering as given below. Can the manager reduce his costs by taking advantage of either of these discounts? Recommend the best ordering policy for the store. Order size Unit cost (Rs.) 1 – 49 pcs. 20.00 50 – 149 pcs. 19.50 150 – 299 pcs. 19.00 300 pcs. or more 18.00arrow_forward
- Help answer showing level work and formulasarrow_forwardI need to forecast using a 3-Period-Moving-Average-Monthly forecasting model which I did but then I need to use my forecast numbers to generate a Master Production Schedule (MPS) I have to Start with actual sales (my own test data numbers) for August-2022 Oct-2022 i need to create MPS to supply demand starting November-2022 April 2023 I just added numbers without applying formulas to the mps on the right side of the spreadsheet because I do not know how to do it. The second image is the example of what it should look like. Thank You.arrow_forwardSolve the following Question 1. How do volume and variety affect the process selection and layout types? Discuss 2. How is the human resource aspect important to operation function? Discuss 3. Discuss the supply network design and its impact on the overall performance of the organization.arrow_forward
- The supply chain is a conventional notion, but organizations are only really interested in making products that they can sell to customers. Provided they have reliable supplies of materials and reasonable transport for finished products, logistics is irrelevant. Do you think this is true? If yes, explain, and if no, clearly explain as well.arrow_forwardworking as a program operations managerarrow_forward12 X1, X230 1 x =0x2 write the Following linear Programming model by 1- general Form Canonical Forms Canonical formY 2- Standard Form Max Z=35X+ 4 X 2 +6 X3 ST. X+2X2-5x3 = 40 3X, + 6X2 + 7x 3 = 30 7x, +lox2 x3 = 50 X3 X 2 X 3 <0arrow_forward
arrow_back_ios
SEE MORE QUESTIONS
arrow_forward_ios
Recommended textbooks for you
- Practical Management ScienceOperations ManagementISBN:9781337406659Author:WINSTON, Wayne L.Publisher:Cengage,Operations ManagementOperations ManagementISBN:9781259667473Author:William J StevensonPublisher:McGraw-Hill EducationOperations and Supply Chain Management (Mcgraw-hi...Operations ManagementISBN:9781259666100Author:F. Robert Jacobs, Richard B ChasePublisher:McGraw-Hill Education
- Purchasing and Supply Chain ManagementOperations ManagementISBN:9781285869681Author:Robert M. Monczka, Robert B. Handfield, Larry C. Giunipero, James L. PattersonPublisher:Cengage LearningProduction and Operations Analysis, Seventh Editi...Operations ManagementISBN:9781478623069Author:Steven Nahmias, Tava Lennon OlsenPublisher:Waveland Press, Inc.
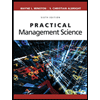
Practical Management Science
Operations Management
ISBN:9781337406659
Author:WINSTON, Wayne L.
Publisher:Cengage,
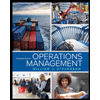
Operations Management
Operations Management
ISBN:9781259667473
Author:William J Stevenson
Publisher:McGraw-Hill Education
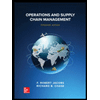
Operations and Supply Chain Management (Mcgraw-hi...
Operations Management
ISBN:9781259666100
Author:F. Robert Jacobs, Richard B Chase
Publisher:McGraw-Hill Education
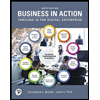
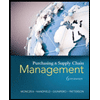
Purchasing and Supply Chain Management
Operations Management
ISBN:9781285869681
Author:Robert M. Monczka, Robert B. Handfield, Larry C. Giunipero, James L. Patterson
Publisher:Cengage Learning
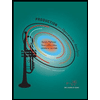
Production and Operations Analysis, Seventh Editi...
Operations Management
ISBN:9781478623069
Author:Steven Nahmias, Tava Lennon Olsen
Publisher:Waveland Press, Inc.
Introduction to Forecasting; Author: Ekeeda;https://www.youtube.com/watch?v=5eIbVXrJL7k;License: Standard YouTube License, CC-BY