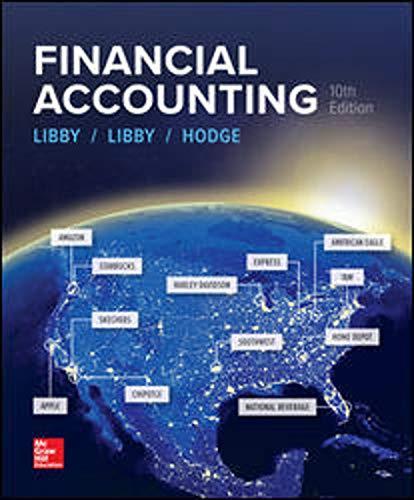
FINANCIAL ACCOUNTING
10th Edition
ISBN: 9781259964947
Author: Libby
Publisher: MCG
expand_more
expand_more
format_list_bulleted
Concept explainers
Topic Video
Question
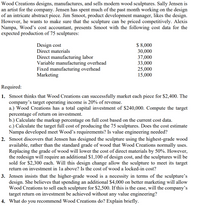
Transcribed Image Text:Wood Creations designs, manufactures, and sells modern wood sculptures. Sally Jensen is
an artist for the company. Jensen has spent much of the past month working on the design
of an intricate abstract piece. Jim Smoot, product development manager, likes the design.
However, he wants to make sure that the sculpture can be priced competitively. Alexis
Nampa, Wood's cost accountant, presents Smoot with the following cost data for the
expected production of 75 sculptures:
$ 8,000
30,000
37,000
33,000
25,000
15,000
Design cost
Direct materials
Direct manufacturing labor
Variable manufacturing overhead
Fixed manufacturing overhead
Marketing
Required:
1. Smoot thinks that Wood Creations can successfully market each piece for $2,400. The
company's target operating income is 20% of revenue.
a.) Wood Creations has a total capital investment of $240,000. Compute the target
percentage of return on investment.
b.) Calculate the markup percentage on full cost based on the current cost data.
c.) Calculate the target full cost of producing the 75 sculptures. Does the cost estimate
Nampa developed meet Wood's requirements? Is value engineering needed?
2. Smoot discovers that Jensen has designed the sculpture using the highest-grade wood
available, rather than the standard grade of wood that Wood Creations normally uses.
Replacing the grade of wood will lower the cost of direct materials by 50%. However,
the redesign will require an additional $1,100 of design cost, and the sculptures will be
sold for $2,300 each. Will this design change allow the sculpture to meet its target
return on investment in la above? Is the cost of wood a locked-in cost?
3. Jensen insists that the higher-grade wood is a necessity in terms of the sculpture's
design. She believes that spending an additional $4,000 on better marketing will allow
Wood Creations to sell each sculpture for $2,500. If this is the case, will the company's
target return on investment be achieved without any value engineering?
4. What do you recommend Wood Creations do? Explain briefly.
Expert Solution

This question has been solved!
Explore an expertly crafted, step-by-step solution for a thorough understanding of key concepts.
Step by stepSolved in 4 steps with 3 images

Knowledge Booster
Learn more about
Need a deep-dive on the concept behind this application? Look no further. Learn more about this topic, accounting and related others by exploring similar questions and additional content below.Similar questions
- Ethics and pricing. Instyle Interior Designs has been requested to prepare a bid to decorate four model homes for a new development. Winning the bid would be a big boost for sales representative Jim Doogan, who works entirely on commission. Sara Groom, the cost accountant for Instyle, prepares the bid based on the following cost information: Based on the company policy of pricing at 120% of full cost, Groom gives Doogan a figure of $165,600 to submit for the job. Doogan is very concerned. He tells Groom that at that price, Instyle has no chance of winning the job. He confides in her that he spent $600 of company funds to take the developer to a basketball playoff game where the developer disclosed that a bid of $156,000 would win the job. He hadn’t planned to tell Groom because he was confident that the bid she developed would be below that amount. Doogan reasons that the $600 he spent will be wasted if Instyle doesn’t capitalize on this valuable information. In any case, the company…arrow_forwardA furniture company manufactures desks and chairs. Each desk requires 29 hours to manufacture and contributes $400 to profit, and each chair requires 19 hours to manufacture and contributes $250 to profit. Due to marketing restrictions, a total of 2000 hours are available. Use Solver to maximize the company’s profit. What is the maximum profit? How many desks and chairs should the company manufacture? Of the 2000 available hours, how many hours will be used?arrow_forwardSid's Skins makes a variety of covers for electronic organizers and portable music players. The company's designers have discovered a market for a new clear plastic covering with college logos for a popular music player. Market research indicates that a cover like this would sell well in the market priced at $24.00. Sid's desires an operating profit of 25 percent of costs. Required: What is the highest acceptable manufacturing cost for which Sid's would be willing to produce the cover? (Round your answer to 2 decimal places.)arrow_forward
- Riders, Ltd. is a manufacturer that produces motorized scooters. Currently, it is producing the motor used to power the scooter, but is considering buying the motor from an outside supplier. The manufacturing costs for Riders to make 20,000 motors are as follows: Cost per motor Direct material $28.50 Direct labor $13.25 Overhead $18.00 An outside supplier offers to supply Riders with all the motors it needs at $55.00 per unit. If Riders buys the motors from the supplier, it will still incur 80% of its overhead costs. Based on the above information, the financial advantage (disadvantage) of buying the 20,000 motors from the outside supplier is: a. ($265,000) b. None of the other answers are correct c. $95,000 d. ($193,000) e. $23,000arrow_forwardLakeside Inc. produces a product that currently sells for $60 per unit. Current production costs per unit include direct materials, $16; direct labor, $18; variable overhead, $11; and fixed overhead, $11. Product engineering has determined that certain production changes could refine the product quality and functionality. These new production changes would increase material and labor costs by 20% per unit. Lakeside has received an offer from a nonprofit organization to buy 9,200 units at $46 per unit. Lakeside currently has unused production capacity. Required: a. Calculate the effect on Lakeside's operating income of accepting the order from the nonprofit organization. Increase in operating incomearrow_forwardBirkenstock is considering adding a new Big Buckle sandal to its current product offerings. Birkenstock expects to price the shoes at $125 per pair. The variable costs to produce one pair are estimated to be: $20 per pair direct materials; $25 per pair direct labor; $5 per pair shipping costs and $5 per pair miscellaneous overhead. The fixed costs for this line of shoes are: $50,000 advertising/promotion; $125,000 manufacturing plant manager salary; $350,000 depreciation expense on manufacturing equipment; and $50,000 other miscellaneous fixed costs. • Birkenstock's best guess is that they will sell 12,000 pairs of Big Buckle sandals in 2021. What is Birkenstock's expected 2021 profit on this product? Type your answer in the first blank below.arrow_forward
- Marvel Parts, Incorporated, manufactures auto accessories. One of the company’s products is a set of seat covers that can be adjusted to fit nearly any small car. The company has a standard cost system in use for all of its products. According to the standards that have been set for the seat covers, the factory should work 990 hours each month to produce 1,980 sets of covers. The standard costs associated with this level of production are: Total Per Set of Covers Direct materials $ 45,738 $ 23.10 Direct labor $ 6,930 3.50 Variable manufacturing overhead (based on direct labor-hours) $ 3,168 1.60 $ 28.20 During August, the factory worked only 1,000 direct labor-hours and produced 2,500 sets of covers. The following actual costs were recorded during the month: Total Per Set of Covers Direct materials (10,000 yards) $ 56,000 $ 22.40 Direct labor $ 9,250 3.70 Variable manufacturing overhead $ 4,500 1.80 $ 27.90 At standard, each set of covers…arrow_forwardMarvel Parts, Incorporated, manufactures auto accessories. One of the company’s products is a set of seat covers that can be adjusted to fit nearly any small car. The company has a standard cost system in use for all of its products. According to the standards that have been set for the seat covers, the factory should work 1,035 hours each month to produce 2,070 sets of covers. The standard costs associated with this level of production are: Total Per Set of Covers Direct materials $ 31,878 $ 15.40 Direct labor $ 6,210 3.00 Variable manufacturing overhead (based on direct labor-hours) $ 4,347 2.10 $ 20.50 During August, the factory worked only 500 direct labor-hours and produced 1,700 sets of covers. The following actual costs were recorded during the month: Total Per Set of Covers Direct materials (5,000 yards) $ 25,500 $ 15.00 Direct labor $ 5,440 3.20 Variable manufacturing overhead $ 4,080 2.40 $ 20.60 At standard, each set of covers…arrow_forwardDeli's Fudge Factory currently makes fudge for retail and mail order customers. It also offers a variety of roasted nuts. Fudge sales have increased over the past year, so Deli is considering outsourcing the roasted nuts and using the roasting space to make additional fudge. A reliable supplier has quoted a price of £0.85 per pound for the roasted nuts. The following amounts reflect the in-house manufacturing costs per pound for the roasted nuts: Direct materials Direct labour Unit-related support costs Batch-related support costs Product-sustaining support costs Facility-sustaining support costs Total cost per pound £0.50 0.06 0.10 0.04 0.05 0.15 £0.90 Required: Should Deli's Fudge Factory outsource the roasted nuts? Why or why not? Discuss all items that should be considered. a.arrow_forward
- In its production process, Purple Tree Inc uses a specialized part in the manufacturing of their fancy widget. The costs to make a part are: direct material, $15; direct labor, $27; variable overhead, $15; and applied fixed overhead, $32. Purple Tree has received a quote of $60 from a potential supplier for this part. If Purple Tree buys the part, 75 percent of the applied fixed overhead would continue. They need 12,000 units of the specialized part. Purple Tree Company would be better off by Group of answer choices $60,000 to buy the part. $348,000 to buy the part. $30,000 to manufacture the part. $216,000 to manufacture the part.arrow_forwardTS Electronics is a manufacturer with two departments: computer chips and cell phones. The computer chip that is produced in the Chips Department can be sold to customers at $6.25 per chip. The costs associated with the computer chips are as follows: (Click the icon to view the computer chip costs.) The Cell Phone Department has been purchasing the chips that it needs for $4.00 per chip from Chip Universe, but the manager was thinking that if the Chips Department could supply the chips for less than what Chip Universe is asking, then it would arrange a transfer between departments instead of giving the business to an external company. If the Cell Phone Department needs 240,000 computer chips and current production in the Chips Department is 480,000 chips, should a transfer take place? If so, at what price? (Note: For internal transfers, the selling and administrative costs are reduced to $0.45 per unit.) What other qualitative factors might need to be considered? First, let's determine…arrow_forwardVikramarrow_forward
arrow_back_ios
SEE MORE QUESTIONS
arrow_forward_ios
Recommended textbooks for you
- AccountingAccountingISBN:9781337272094Author:WARREN, Carl S., Reeve, James M., Duchac, Jonathan E.Publisher:Cengage Learning,Accounting Information SystemsAccountingISBN:9781337619202Author:Hall, James A.Publisher:Cengage Learning,
- Horngren's Cost Accounting: A Managerial Emphasis...AccountingISBN:9780134475585Author:Srikant M. Datar, Madhav V. RajanPublisher:PEARSONIntermediate AccountingAccountingISBN:9781259722660Author:J. David Spiceland, Mark W. Nelson, Wayne M ThomasPublisher:McGraw-Hill EducationFinancial and Managerial AccountingAccountingISBN:9781259726705Author:John J Wild, Ken W. Shaw, Barbara Chiappetta Fundamental Accounting PrinciplesPublisher:McGraw-Hill Education
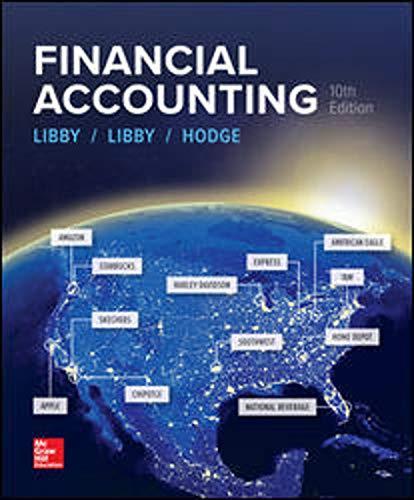
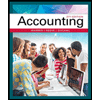
Accounting
Accounting
ISBN:9781337272094
Author:WARREN, Carl S., Reeve, James M., Duchac, Jonathan E.
Publisher:Cengage Learning,
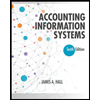
Accounting Information Systems
Accounting
ISBN:9781337619202
Author:Hall, James A.
Publisher:Cengage Learning,
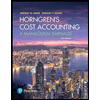
Horngren's Cost Accounting: A Managerial Emphasis...
Accounting
ISBN:9780134475585
Author:Srikant M. Datar, Madhav V. Rajan
Publisher:PEARSON
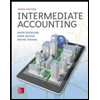
Intermediate Accounting
Accounting
ISBN:9781259722660
Author:J. David Spiceland, Mark W. Nelson, Wayne M Thomas
Publisher:McGraw-Hill Education
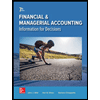
Financial and Managerial Accounting
Accounting
ISBN:9781259726705
Author:John J Wild, Ken W. Shaw, Barbara Chiappetta Fundamental Accounting Principles
Publisher:McGraw-Hill Education