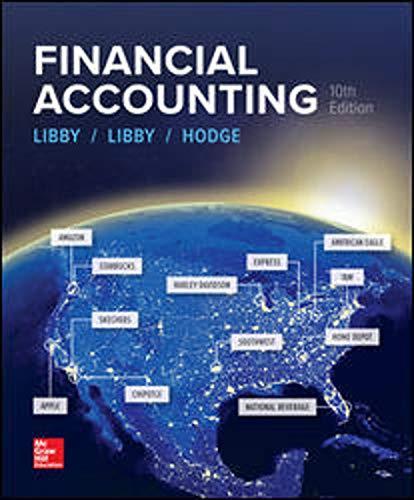
Catch, Inc., is a designer and manufacturer of backpacks and purses. The equipment must be switched over to a new setting and set up to prepare for each new batch of products. This setup process is very technical and requires a highly qualified team of engineers. Setting up each product requires different efforts.
Here is the information about
Direct Manufacturing Costs:
Purses Backpacks
Direct Materials $379,290 $412,920
Direct Manufacturing Labor $98,000 $120,000
Manufacturing
Setup Costs $66,000
Machine-Related Costs $384,000
(Utilities, Maintenance, etc.)
Factory Rent $100,000
Here is some information on potential allocation bases/cost drivers for overheads cost:
Purses Backpacks
Number of batches 120 60
Setup Time 0.5 hours/batch 4 hours/batch
Machine-Hours 2,600 1,400
Number of bags 3,600 6,000
Production area used 4,000 sq. ft. 6,000 sq. ft.
Q1: Using the above information, choose allocation bases for each overhead, allocate overhead, and calculate the production costs of each product line per unit. When choosing allocation bases, explain your choice of allocation base for each cost.
Q2: Suppose you find out that 1,000 sq. ft. space in the Backpacks area is lying unused.
Will the overheads allocate to Backpacks and Purses change, and if so by how much?
By how much will Catch, Inc.’s period costs change as a result?
Q3: Once all the manufacturing overheads have been allocated to come up with production costs for the income statement that needs to go out to shareholders, the management now turns their attention to the non-manufacturing overheads.
The most important of the non-manufacturing overheads is administration costs. The management discusses how difficult it is to find a good allocation base for administration costs. The management team considered three alternative allocation bases: production area used, number of bags made, and machine hours worked. To decide between these three, the management team asks for some additional information about each allocation base in recent six months:
July Aug Sept Oct Nov Dec
Administration Cost $4,000 $5,000 $8,000 $8,000 $10,000 $10000
Total area used 10,000 Sq. ft. 10,000 Sq. ft. 10,000 Sq. ft. 10,000 Sq. ft. 10,000 Sq. ft. 10,000 Sq. ft.
# of phone calls received 500 600 900 1,100 1,300 1,200
# of Invoice Issued 150 187.50 300 305 375 380
Required: Which of these allocation bases would you choose to allocate administration costs across the # of phone calls received or # of Invoice Issued? Why would you choose it?
Q4: Another important non-manufacturing overhead is the warehouse cost. This is the cost paid to a third-party warehouse owner to house all the finished bags, in crates, while they await pickup and shipping to retailers. Usually, this cost is considered a distribution cost, and since that is a non-manufacturing cost, these costs are expensed in the period incurred. Warehousing costs this year are $3,640,000 for the backpacks and $2,000,000 for the purses. The company made 130,000 backpacks this year and sold 120,000. The company made and sold 150,000 purses this year.
This year, however, the management says: “They are under pressure this year to meet the earning targets that our investors have set for us. Can’t you justify reclassifying these warehousing costs as a product cost instead of a period cost? After all, these are directly related to our product.”
Required: IF you were to reclassify the warehousing costs as a product cost instead of a period cost, would that have any effect on reported income for this year? Explain why or why not, with supporting calculations where needed.

Trending nowThis is a popular solution!
Step by stepSolved in 5 steps with 1 images

- Metters Cabinets, Inc., needs to choose a production method for its new office shelf, the Maxistand. To help accomplish this, the firm has gathered the following production cost data: Annualized Fixed Cost Variable Costs (per unit) ($) Process Type of Plant & Equipment Labor Material Energy Mass Customization $1,260,000 30 18 12 Intermittent $1,000,000 24 26 20 Repetitive $1.720.000 28 15 12 Continuous $2,100,000 25 15 10 Metters Cabinets projects an annual demand of 60,000 units for the Maxistand. The selling price for the Maxistand is $120 per unit. a) Based on the projected annual demand, the best alternative available is to use the Mass Customization process. b) The value of annual profit using this method is $. (Enter your response as an integer.)arrow_forwardThe Park Avenue Corporation currently makes a part required in its finished product. The company uses 2,054 units of this part annually. Park Avenue Corp has been approached by a vendor to provide this part for $13.29 each. The following cost information is provided Direct Materials per unit $5.71 Direct Labor per unit $7.30 Variable Factory Overhead per unit $2.50 Fixed Factory Overhead per unit $7.50 How much would Park Avenue Corporation save by having the vendor make the part, instead of making it themselves? Enter your answer rounded to the nearest whole number. Don't enter dollar signs or commas. ch ASUS F3 f5 E3 f6 [X f7 f8 f10 f12 & 3 4 7. 8. T. Y U D F G JK L %24arrow_forwardCan anyone help me fix these problems?arrow_forward
- Make or Buy Decision: Zee-Drive Ltd. is a computer manufacturer. One of the items they make is monitors. Zee-Drive has the opportunity to purchase 19,000 monitors from an outside supplier for $202 per unit. One of the company's cost-accounting interns prepared the following schedule of Zee-Drive's cost to produce 19,000 monitors: 19,000 monitors $ 2,185,000 1,292,000 684,000 551,000 798,000 $ 5,510,000 $290 You are asked to look over the intern's estimate before the information is shared with members of management who will decide to continue to make the monitors or buy them. The company's controller believes that the estimate may be incorrect because it includes costs that are not relevant. If Zee-Drive buys the monitors, the direct labor force currently employed in producing the monitors will be terminated and there would be no termination costs incurred. There are no materials on hand and no commitments to suppliers to purchase materials, so all materials would need to be purchased…arrow_forwardPerfect Pet Collar Company makes custom leather pet collars. The company expects each collar to require 2.50 feet of leather and predicts leather will cost $4.50 per foot. Suppose Perfect Pet made 100 collars during February. For these 100 collars, the company actually averaged 2.65 feet of leather per collar and paid $4.10 per foot. Required: 1. Calculate the standard direct materials cost per unit. 2. Without performing any calculations, determine whether the direct materials price variance will be favorable or unfavorable. 3. Without performing any calculations, determine whether the direct materials quantity variance will be favorable or unfavorable. 6. Calculate the direct materials price and quantity variances. Complete this question by entering your answers in the tabs below. Req 1 Req 2 and 3 Req 6 2. Without performing any calculations, determine whether the direct materials price variance will be favorable or unfavorable. 3. Without performing any calculations, determine…arrow_forward1. SIP Inc. (SIP) is plastic injection molding company specializing in front-end grilles. Bilchew Numbers wants to look at using an activity-based costing system. For 2021, he estimated overhead costs of $12,560,000 to be allocated using an activity-based costing system (see the table below). Bilchew also estimated that direct labour will be paid at the rate of $15 per hour. Cost Driver Activity Cost Pool Estimated Cost Total Quantity of Allocation Base (allocation base) Indirect materials $ 1,450,000 Direct materials $6,590,910 Indirect labour and 2,000,000 Direct labour 100,000 hours supervision Utilities 3,598,000 Power 20,000 kilowatt-hours (kWh) consumption Inspection 4,200,000 Inspection 15,000 inspections Depreciation 1,312,000 Machine usage 160,000 machine-hours $12,560,000 During January 2021, Bilchew worked on two jobs, which consumed the following resources: Job 2021-A1 Job 2021-A2 Direct materials cost $ 6,500 $ 22,000 Direct labour cost $42,000 $165,000 Machine-hours 1,800…arrow_forward
- Sardi Incorporated is considering whether to continue to make a component or to buy it from an outside supplier. The company uses 12,600 of the components each year. The unit product cost of the component according to the company's cost accounting system is given as follows: Direct materials $ 8.40 Direct labor 5.40 Variable manufacturing overhead 1.20 Fixed manufacturing overhead 3.20 Unit product cost $ 18.20 Assume that direct labor is a variable cost. Of the fixed manufacturing overhead, 35% is avoidable if the component were bought from the outside supplier. In addition, making the component uses 1 minutes on the machine that is the company's current constraint. If the component were bought, time would be freed up for use on another product that requires 2 minutes on this machine and that has a contribution margin of $4.80 per unit. When deciding whether to make or buy the component, what cost of making the component should be compared to the price of buying the…arrow_forwardHansabenarrow_forwardi need the answer quicklyarrow_forward
- Power Trampolines produces fitness trampolines for both personal and commercial use. An up-and-coming fitness. facility brand, Bounce It Out, has just asked Power Trampolines for a quote to purchase 300 trampolines for use in its facilities. Power Trampolines provided the following quote to Bounce It Out: Quote for Bounce It Out Manufacturing Costs Direct Materials $11,850 Direct Labor 8, 500 Manufacturing Overhead 15,800 Total Costs $36, 150 Markup (per company policy) 60% Total Estimated Price $57,840 As a fairly new company, Bounce It Out is unable to pay this amount. They provide a counter-offer of $45,000 for the 300 trampolines. The company asks for your help in deciding whether or not to accept this offer. They provide you with the following information to aid in your decision: - They have excess capacity and could manufacture the 300 trampolines without impacting their other manufacturing needs - Manufacturing overhead is allocated based on direct labor dollars -Budgeted…arrow_forwardThe following details taken from the books of DiDi Sdn Bhd for the year ending 31 December 2020. DiDi Sdn Bhd Statement Profit or Loss for the year ending 31 December 2020 (extract) RM RM Gross profit 44,700 Add : Discount received 410 Profit on sale of van 620 1,030 45,730 Less: Expenses Motor expenses 1,940 Wages 17,200 General expenses 830 Bad debts 520 Increase in allowance for doubtful debts 200 Depreciation : van 1,800 22,490 23,240 Statement of Financial Position as at 31 December 2019 2020 RM RM RM RM Non-current Assets Vans at cost 15,400 8,200 less Depreciation (5,300) (3,100) 10,100 5,100 Current Assets Inventory 18,600 24,000 Trade accounts receivables less provision*…arrow_forwardMarvel Parts, Incorporated, manufactures auto accessories including a set of seat covers that can be adjusted to fit most cars. According to its standards, the factory should work 1,015 hours each month to produce 2,030 sets of seat covers. The standard costs associated with this level of production are: Direct materials Direct labor Variable manufacturing overhead (based on direct labor-hours) Direct materials (8,400 yards) Direct labor Variable manufacturing overhead Total $ 59,276 $ 8,120 $ 3,857 1. Materials price vanance 1. Materials quantity variance 2. Labor rate variance 2 Labor efficiency variance 3. Vanable overhead rate variance 3. Variable overhead efficiency variance Per Set of Covers During August, the factory worked 700 direct labor-hours and produced 1,500 sets of covers. The following actual costs were recorded during the month: Total $ 42,000 $ 6,300 $3,150 $ 29.20 4.00 1.90 $ 35.10 Per Set of Covers $28.00 4.20 2.10 $34.30 At standard, each set of covers should…arrow_forward
- AccountingAccountingISBN:9781337272094Author:WARREN, Carl S., Reeve, James M., Duchac, Jonathan E.Publisher:Cengage Learning,Accounting Information SystemsAccountingISBN:9781337619202Author:Hall, James A.Publisher:Cengage Learning,
- Horngren's Cost Accounting: A Managerial Emphasis...AccountingISBN:9780134475585Author:Srikant M. Datar, Madhav V. RajanPublisher:PEARSONIntermediate AccountingAccountingISBN:9781259722660Author:J. David Spiceland, Mark W. Nelson, Wayne M ThomasPublisher:McGraw-Hill EducationFinancial and Managerial AccountingAccountingISBN:9781259726705Author:John J Wild, Ken W. Shaw, Barbara Chiappetta Fundamental Accounting PrinciplesPublisher:McGraw-Hill Education
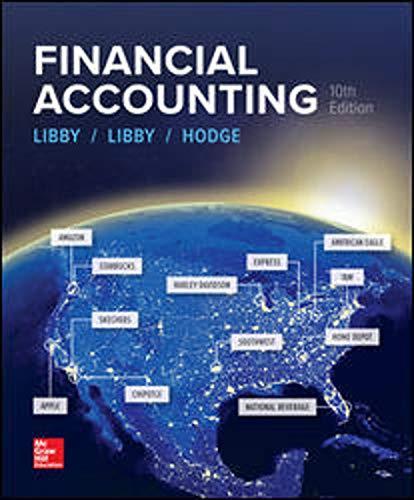
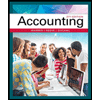
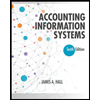
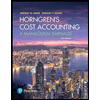
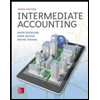
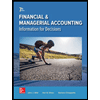