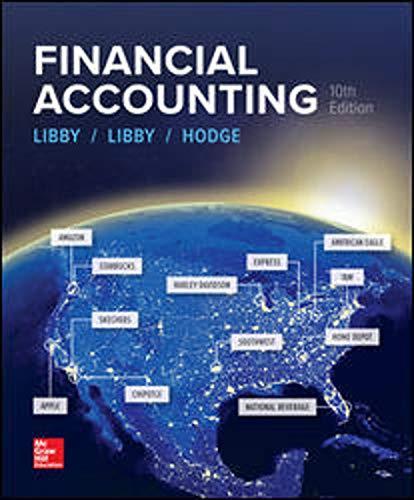
Troy Engines, Ltd., manufactures a variety of engines for use in heavy equipment. The company has always produced all of the necessary parts for its engines, including all of the carburetors. An outside supplier has offered to sell one type of carburetor to Troy Engines, Ltd., for a cost of $35 per unit. To evaluate this offer, Troy Engines, Ltd., has gathered the following information relating to its own cost of producing the carburetor internally:
Per Unit | 15,000 Units Per Year |
|||||
Direct materials | $ | 14 | $ | 210,000 | ||
Direct labor | 10 | 150,000 | ||||
Variable manufacturing |
3 | 45,000 | ||||
Fixed manufacturing overhead, traceable | 6 | * | 90,000 | |||
Fixed manufacturing overhead, allocated | 9 | 135,000 | ||||
Total cost | $ | 42 | $ | 630,000 | ||
*One-third supervisory salaries; two-thirds
Required:
1. Assuming the company has no alternative use for the facilities that are now being used to produce the carburetors, what would be the financial advantage (disadvantage) of buying 15,000 carburetors from the outside supplier?
2. Should the outside supplier’s offer be accepted?
3. Suppose that if the carburetors were purchased, Troy Engines, Ltd., could use the freed capacity to launch a new product. The segment margin of the new product would be $150,000 per year. Given this new assumption, what would be financial advantage (disadvantage) of buying 15,000 carburetors from the outside supplier?
4. Given the new assumption in requirement 3, should the outside supplier’s offer be accepted?

Trending nowThis is a popular solution!
Step by stepSolved in 4 steps with 2 images

- Troy Engines, Limited, manufactures a variety of engines for use in heavy equipment. The company has always produced all of the necessary parts for its engines, including all of the carburetors. An outside supplier has offered to sell one type of carburetor to Troy Engines, Limited, for a cost of $30 per unit. To evaluate this offer, Troy Engines, Limited, has gathered the following information relating to its own cost of producing the carburetor internally: Direct materials Direct labor Variable manufacturing overhead Fixed manufacturing overhead, traceable Fixed manufacturing overhead, allocated Total cost Per 12,000 Units Unit Per Year $ 12 $ 144,000 8 96,000 2 24,000 9* 12 108,000 144,000 $ 43 $ 516,000 *One-third supervisory salaries; two-thirds depreciation of special equipment (no resale value). Required: 1. Assuming the company has no alternative use for the facilities that are now being used to produce the carburetors, what would be the financial advantage (disadvantage) of…arrow_forwardCairney, Incorporated manufactures a specialized part used in internal combustion engines. The annual demand for the part is 261,000 units. The facility has a practical capacity of 276,000 units annually. The company leased the current facility because facilities capable of manufacturing the unit require machines that can produce 69,000 units each. The annual cost of the facility is $1,092,960. The variable cost of a part is $4. Required: a. What cost per unit should the cost system report to facilitate management decision making? Note: Round your answer to 2 decimal places. b. What is the cost of excess capacity? a. Cost per unit b. Cost of excess capacity $ $ 8.19 122,850arrow_forwardStan Fawcett's company currently purchases a gear assembly from Salt Lake Supply, Inc., at $3.80 per unit with a minimum order of 3,000 units. Stan is considering instead producing the gear assembly himself. He estimates that producing it himself will cost $12,000 to set up the process and then $1.82 per unit for labor and materials. a) Using the line drawing tool, add the total cost graph for Stan to produce the assembly instead of purchasing from Salt Lake Supply. Total cost for the purchase option is already plotted. Properly label your line. Note: Carefully follow the instructions above and only draw the required object. Cost 40,000- ¡Minimum Order 36,000 32,000- 28,000- 24,000 20,000- 16,000 12,000 - 8,000- 4,000- 0+ 0 2,000 4,000 Quantity 6,000 8,000arrow_forward
- Blossom Company manufactures products ranging from simple automated machinery to complex systems containing numerous components. Unit selling prices range from $200,000 to $1,500,000 and are quoted inclusive of installation. The installation process does not involve changes to the features of the equipment and does not require proprietary information about the equipment in order for the installed equipment to perform to specifications. Blossom has the following arrangement with Sheridan Inc. Sheridan purchases equipment from Blossom for a price of $926,400 and contracts with Blossom to install the equipment. Blossom charges the same price for the equipment irrespective of whether it does the installation or not. Using market data, Blossom determines installation service is estimated to have a standalone selling price of $38,600. The cost of the equipment is $640,000. Sheridan is obligated to pay Blossom the $926,400 upon the delivery of the equipment. Blossom delivers the equipment on…arrow_forwardEach year, Basu Company produces 24,000 units of a component used in microwave ovens. An outside supplier has offered to supply the part for $1.17. The unit cost is: Direct materials $0.72 Direct labor 0.25 Variable overhead 0.13 Fixed overhead 2.95 Total unit cost $4.05 Required: 1. What are the alternatives for Basu Company? 2. Assume that none of the fixed cost is avoidable. List the relevant cost(s) of internal production. List the relevant cost(s) of external purchase. 3. Which alternative is more cost effective and by how much? _____ by $___ 4. What if $18,560 of fixed overhead is rental of equipment used only in production of the component that can be avoided if the component is purchased? Which alternative is more cost effective and by how much? ____ by $____arrow_forward! Required information [The following information applies to the questions displayed below.] Kinnear Plastics manufactures various components for the aircraft and marine industry. Kinnear buys plastic from two vendors: Tappan Corporation and Hill Enterprises. Kinnear chooses the vendor based on price. Once the plastic is received, it is inspected to ensure that it is suitable for production. Plastic that is deemed unsuitable is disposed of. The controller at Kinnear collected the following information on purchases for the past year: Total purchases (tons) Plastic discarded Tappan 5,000 200 The purchasing manager has just received bids on an order for 330 tons of plastic from both Tappan and Hill. Tappan bid $2,112 and Hill bid $2,109 per ton. Effective cost per ton Hill 7,500 375 Required: 1-a. Assume that the average quality, measured by the amounts discarded from the two companies, will continue as in the past. What is the effective cost per ton for both Tappan and Hill? (Do not…arrow_forward
- Troy Engines, Limited, manufactures a variety of engines for use in heavy equipment. The company has always produced all of the necessary parts for its engines, including all of the carburetors. An outside supplier has offered to sell one type of carburetor to Troy Engines, Limited, for a cost of $35 per unit. To evaluate this offer, Troy Engines, Limited, has gathered the following information relating to its own cost of producing the carburetor internally: Per Unit 22,000 Units Per Year Direct materials $ 15 $ 330,000 Direct labor 8 176,000 Variable manufacturing overhead 3 66,000 Fixed manufacturing overhead, traceable 3*Footnote asterisk 66,000 Fixed manufacturing overhead, allocated 6 132,000 Total cost $ 35 $ 770,000 *Footnote asteriskOne-third supervisory salaries; two-thirds depreciation of special equipment (no resale value). Required: Assuming the company has no alternative use for the facilities that are now being used to produce the carburetors, what…arrow_forwardLeach Finishing makes various metal fittings for the construction industry. Three of the fittings, models X-12, X-24, and X-30, require grinding on a patented machine of which Leach has only one. The cost of production information for the three products follow: X-12 $35 $ 20 18.0 Price per fitting Variable cost per fitting Units per hour of grinding The testing machine used for both models has a capacity of 3,230 hours annually. Fixed manufacturing costs are $496,000 annually. Required A Required B X-24 $ 51 $ 27 12.5 Required: a. Suppose that Leach Finishing can sell at most 59,200 units of any one fitting. How many units of each fitting model should Leach Finishing produce annually? b. Suppose that Leach Finishing can sell at most 18,000 units of any one fitting. How many units of each fitting should Leach Finishing produce annually? X-30 $ 70 $ 44 10.0 Complete this question by entering your answers in the tabs below. X-12 X-24 X-30 units units units Suppose that Leach Finishing can…arrow_forwardTroy Engines, Limited, manufactures a variety of engines for use in heavy equipment. The company has always produced all of the necessary parts for its engines, including all of the carburetors. An outside supplier has offered to sell one type of carburetor to Troy Engines, Limited, for a cost of $36 per unit. To evaluate this offer, Troy Engines, Limited, has gathered the following information relathng to its own cost of producing the carburetor internally:. Per 20,000 Units Per Unit Year $ 340,000 200,000 40,000 180, 000 240,000 Direct materials $ 17 Direct labor 10 2 Variable manufacturing overhead Fixed manufacturing overhead, traceable Fixed manufacturing overhead, allocated 9* 12 $ 50 $ 1,000,000 Total cost *One-third supervisory salaries; two-thirds depreciation of special equipment (no resale value). Required: 1. Assuming the company has no alternative use for the facilities that are now being used to produce the carburetors, what would be the financial advantage (disadvantage)…arrow_forward
- Pronghorn Company manufactures equipment. Pronghorn’s products range from simple automated machinery to complex systems containing numerous components. Unit selling prices range from $200,000 to $1,500,000 and are quoted inclusive of installation. The installation process does not involve changes to the features of the equipment and does not require proprietary information about the equipment in order for the installed equipment to perform to specifications. Pronghorn has the following arrangement with Winkerbean Inc. ● Winkerbean purchases equipment from Pronghorn for a price of $1,070,000 and contracts with Pronghorn to install the equipment. Pronghorn charges the same price for the equipment irrespective of whether it does the installation or not. The cost of the equipment is $599,000. ● Winkerbean is obligated to pay Pronghorn the $1,070,000 upon the delivery and installation of the equipment. Pronghorn delivers the equipment on June 1, 2020, and completes the…arrow_forwardCarla Vista Company manufactures products ranging from simple automated machinery to complex systems containing numerous components. Unit selling prices range from $200,000 to $1,500,000 and are quoted inclusive of installation. The installation process does not involve changes to the features of the equipment and does not require proprietary information about the equipment in order for the installed equipment to perform to specifications, Carla Vista has the following arrangement with Pharoah Inc. Pharoah purchases equipment from Carla Vista for a price of $1,008,900 and contracts with Carla Vista to install the equipment. Carla Vista charges the same price for the equipment irrespective of whether it does the installation or not. The cost of the equipment is $654,000. Pharoah is obligated to pay Carla Vista the $1.008,900 upon the delivery of the equipment. Carla Vista delivers the equipment on June 1, 2025, and completes the installation of the equipment on September 30, 2025. The…arrow_forwardCulver Company manufactures equipment. Culver’s products range from simple automated machinery to complex systems containing numerous components. Unit selling prices range from $200,000 to $1,500,000 and are quoted inclusive of installation. The installation process does not involve changes to the features of the equipment and does not require proprietary information about the equipment in order for the installed equipment to perform to specifications. Culver has the following arrangement with Winkerbean Inc. ● Winkerbean purchases equipment from Culver for a price of $1,040,000 and contracts with Culver to install the equipment. Culver charges the same price for the equipment irrespective of whether it does the installation or not. The cost of the equipment is $581,000. ● Winkerbean is obligated to pay Culver the $1,040,000 upon the delivery and installation of the equipment. Culver delivers the equipment on June 1, 2020, and completes the installation of the equipment…arrow_forward
- AccountingAccountingISBN:9781337272094Author:WARREN, Carl S., Reeve, James M., Duchac, Jonathan E.Publisher:Cengage Learning,Accounting Information SystemsAccountingISBN:9781337619202Author:Hall, James A.Publisher:Cengage Learning,
- Horngren's Cost Accounting: A Managerial Emphasis...AccountingISBN:9780134475585Author:Srikant M. Datar, Madhav V. RajanPublisher:PEARSONIntermediate AccountingAccountingISBN:9781259722660Author:J. David Spiceland, Mark W. Nelson, Wayne M ThomasPublisher:McGraw-Hill EducationFinancial and Managerial AccountingAccountingISBN:9781259726705Author:John J Wild, Ken W. Shaw, Barbara Chiappetta Fundamental Accounting PrinciplesPublisher:McGraw-Hill Education
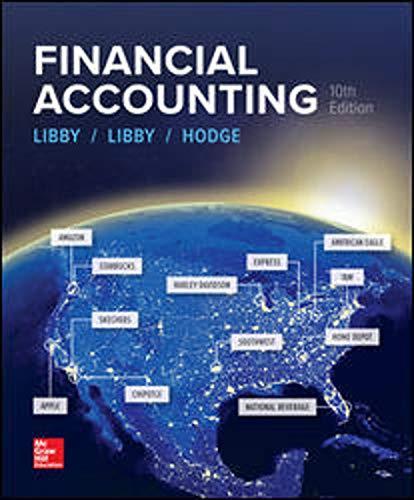
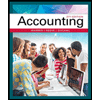
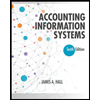
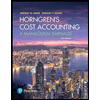
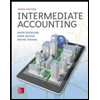
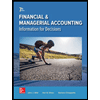