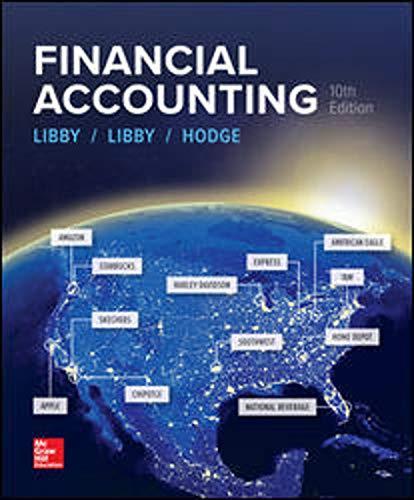
Tidwell, Inc., has two plants that manufacture a line of wheelchairs. One is located in Dallas, and the other in Oklahoma City. Each plant is set up as a profit center. During the past year, both plants sold their tilt wheelchair model for $1,782. Sales volume averages 20,000 units per year in each plant. Recently, the Dallas plant reduced the price of the tilt model to $1,584. Discussion with the Dallas manager revealed that the price reduction was possible because the plant had reduced its manufacturing and selling costs by reducing what was called “non-value-added costs.” The Dallas manufacturing and selling costs for the tilt model were $1,386 per unit. The Dallas manager offered to loan the Oklahoma City plant his cost
The plant controller and the Dallas cost accounting manager have assembled the following data for the most recent year. The actual cost of inputs, their value-added (ideal) quantity levels, and the actual quantity levels are provided (for production of 20,000 units). Assume there is no difference between actual prices of activity units and standard prices.
SQ |
AQ |
Actual Cost |
|
Materials (lbs.) |
940,500 |
990,000 |
$20,790,000 |
Labor (hrs.) |
225,720 |
237,600 |
2,970,000 |
Setups (hrs.) |
— |
15,840 |
1,188,000 |
Materials handling (moves) |
— |
39,600 |
2,772,000 |
Warranties (no. repaired) |
— |
39,600 |
3,960,000 |
Total |
$31,680,000 |
Required:
4. There are four data analytic types: descriptive, diagnostic, predictive, and prescriptive. Choose which data analytic type(s) apply for each of the following (justify your selection):
a. The target cost calculated in Requirement 1.
b. The calculation of the non-value added cost in Requirement 2.
c. The assessment of whether the target cost can be achieved.
d. The actions recommended

Trending nowThis is a popular solution!
Step by stepSolved in 2 steps

- Fusion Metals Company is considering the elimination of its Packaging Department. Management has received an offer from an outside firm to supply all Fusion’s packaging needs. To help her in making the decision, Fusion’s president has asked the controller for an analysis of the cost of running Fusion’s Packaging Department. Included in that analysis is $9,100 of rent, which represents the Packaging Department’s allocation of the rent on Fusion’s factory building. If the Packaging Department is eliminated,the space it used will be converted to storage space. Currently Fusion rents storage space in a nearby warehouse for $11,000 per year. The warehouse rental would no longer be necessary if the Packaging Department were eliminated. Required:1. Discuss each of the figures given in the exercise with regard to its relevance in the departmentclosing decision.2. What type of cost is the $11,000 warehouse rental, from the viewpoint of the costs of the Packaging Department?arrow_forwardBramble Pix currently uses a six-year-old molding machine to manufacture silver picture frames. The company paid $88,000 for the machine, which was state of the art at the time of purchase. Although the machine will likely last another ten years, it will need a $12,000 overhaul in four years. More important, it does not provide enough capacity to meet customer demand. The company currently produces and sells 11,000 frames per year, generating a total contribution margin of $85,500. Martson Molders currently sells a molding machine that will allow Bramble Pix to increase production and sales to 15,000 frames per year. The machine, which has a ten-year life, sells for $131,000 and would cost $12,000 per year to operate. Bramble Pix's current machine costs only $8,000 per year to operate. If Bramble Pix purchases the new machine, the old machine could be sold at its book value of $5,000. The new machine is expected to have a salvage value of $19,500 at the end of its ten-year life.…arrow_forwardJ. Smythe, Incorporated, manufactures fine furniture. The company is deciding whether to introduce a new mahogany dining room table set. The set will sell for $6,130, including a set of eight chairs. The company feels that sales will be 2,600, 2,750, 3,300, 3,150, and 2,900 sets per year for the next five years, respectively. Variable costs will amount to 48 percent of sales and fixed costs are $1,880,000 per year. The new tables will require inventory amounting to 13 percent of sales, produced and stockpiled in the year prior to sales. It is believed that the addition of the new table will cause a loss of 550 tables per year of the oak tables the company produces. These tables sell for $4,200 and have variable costs of 43 percent of sales. The inventory for this oak table is also 13 percent of sales. The sales of the oak table will continue indefinitely. J. Smythe currently has excess production capacity. If the company buys the necessary equipment today, it will cost $16,000,000.…arrow_forward
- Naturalmaid processes organic milk into plain yogurt. Naturalmaid sells plain yogurt to hospitals, nursing homes, and restaurants in bulk, one-gallon containers. Each batch, processed at a cost of $880, yields 750 gallons of plain yogurt. The company sells the one-gallon tubs for $5.00 each and spends $0.14 for each plastic tub. Naturalmaid has recently begun to reconsider its strategy. Management wonders if it would be more profitable to sell individual-sized portions of fruited organic yogurt at local food stores. Naturalmaid could further process each batch of plain yogurt into 16,000 individual portions (3/4 cup each) of fruited yogurt. A recent market analysis indicates that demand for the product exists. Naturalmaid would sell each individual portion for $0.58. Packaging would cost $0.06 per portion, and fruit would cost $0.10 per portion. Fixed costs would not change. Should Naturalmaid continue to sell only the gallon-sized plain yogurt (sell as is) or convert the plain yogurt…arrow_forwardYardwork Tools Corp manufactures garden tools in a factory in Taneytown, Maryland. Recently, the company designed a collection of tools for professional use rather than consumer use. Management needs to make a good decision about whether to produce this line in their existing space in Maryland, where space is available or to accept an offer from a manufacturer in Taiwan. Data concerning the decision are as follows: Expected annual sales of tools (in units) 660,000 Average selling price of tools $11 Price quoted by Taiwanese company, in New Taiwanese Dollars (NTD) 27,300 Current exchange rate 9,100 NTD = $1 Variable manufacturing costs $2.85 per unit Incremental annual fixed manufacturing costs associated with the new product line $310,000 Variable selling and distribution costsª $0.50 per unit Annual fixed selling and distribution costsª $250,000 ªSelling and distribution costs are the same regardless of whether the tools…arrow_forwardGrant Industries, a manufacturer of electronic parts, has recently received an invitation to bid on a special order for 20,500 units of one of its most popular products. Grant currently manufactures 41,000 units of this product in its Loveland, Ohio, plant. The plant is operating at 50% capacity. There will be no marketing costs on the special order. The sales manager of Grant wants to set the bid at $15 because she is sure that Grant will get the business at that price. Others on the executive committee of the firm object, saying that Grant would lose money on the special order at that price. Units Manufacturing costs: Direct materials Direct labor Factory overhead 41,000 61,500 $ 164,000 205,000 328,000 $ 246,000 307,500 430,500 $ 984,000 Total manufacturing costs $ 697,000 $ 17 Unit cost $ 16 Required: 2. What is the relevant cost per unit? What do you think the minimum short-term bid price per unit should be? What would be the impact on short-term operating income if the order is…arrow_forward
- Deli's Fudge Factory currently makes fudge for retail and mail order customers. It also offers a variety of roasted nuts. Fudge sales have increased over the past year, so Deli is considering outsourcing the roasted nuts and using the roasting space to make additional fudge. A reliable supplier has quoted a price of £0.85 per pound for the roasted nuts. The following amounts reflect the in-house manufacturing costs per pound for the roasted nuts: Direct materials Direct labour Unit-related support costs Batch-related support costs Product-sustaining support costs Facility-sustaining support costs Total cost per pound £0.50 0.06 0.10 0.04 0.05 0.15 £0.90 Required: Should Deli's Fudge Factory outsource the roasted nuts? Why or why not? Discuss all items that should be considered. a.arrow_forwardCPT incorporated is a local manufacturer of conveyor systems. Last year, CPT sold over $2 million worth of conveyor systems that netted the company $100,000 in profits. Raw materials and labor are CPT's biggest expenses. Spending on structural steel alone amounted to over $500,000, or 25 percent of total sales. In an effort to reduce costs, CPT now uses an online procurement procedure that is best described as a first-price, sealed-bid auction. The bidders in these auctions utilize the steel for a wide variety of purposes. ranging from art to skyscrapers. This suggests that bidders value the steel independently, although it is perceived that bidder valuations are evenly distributed between $7,000 and $26,000. You are the purchasing manager at CPT and are bidding on three tons of six-inch hot-rolled channel steel against four other bidders Your company values the three tons of channel steel at $18,000. What is your optimal bid?arrow_forwardGrant Industries, a manufacturer of electronic parts, has recently received an invitation to bid on a special order for 25,000 units of one of its most popular products. Grant currently manufactures 50,000 units of this product in its Loveland, Ohio, plant. The plant is operating at 50% capacity. There will be no marketing costs on the special order. The sales manager of Grant wants to set the bid at $14 because she is sure that Grant will get the business at that price. Others on the executive committee of the firm object, saying that Grant would lose money on the special order at that price. Units Manufacturing costs: Direct materials Direct labor Factory overhead Total manufacturing costs Unit cost 50,000 Required 2 Required 4 75,000 $ 200,000 250,000 350,000 $ 800,000 $ 1,125,000 $ 16 $15 Required: 2. What is the relevant cost per unit? What do ou think the minimum short-term bid price per unit should be? What would be the impact on short-term operating income if the order is…arrow_forward
- In the last 6 months, demand for one of Appleby Company's products has dropped off considerably, due mainly to it becoming obsolescent as a result of technological change. Knowing that the equipment used in the manufacture of this product may not be easy to sell, Appleby spent $50,000 on consultants to determine whether it could use the equipment to produce a new product under license by another company. The consultant has determined that this product would have variable production costs of $65 per unit and should sell at a price of $90/unit. The licensing royalty is 5% of gross product revenue. Estimated annual demand is 20,000 units per year. Additional annual operating costs related to this product are $30,000/year (excluding depreciation). Depreciation on the equipment is $15,000. Annual depreciation expense is a: O a. Sunk cost O b. Relevant cost O c. Both sunk and Irrelevant cost Od. Irrelevant costarrow_forwardAn auto supplies company has retail stores located in eight cities in California. The price they charge for a particular product in each city varies because of differing competitive conditions. For instance, the price they charge for a case of a popular brand of motor oil in each city follows. Also shown are the number of cases that the company sold last quarter in each city. Price ($) Sales (cases) City Bakersfield Los Angeles Modesto Oakland Sacramento San Diego San Francisco San Jose 34.99 38.99 36.00 33.59 40.99 38.59 39.59 37.99 411 1,375 394 872 755 1,138 1,634 729 Compute the average sales price per case for this product during the last quarter. (Round your answer to two decimal places.) $ 33.75 Xarrow_forwardJupiter Game Company manufactures pocket electronic games. Last year Jupiter sold 25,000 games at $25 each. Total costs amounted to $525,000, of which $150,000 were considered fixed costs. In an attempt to improve its product, the company is considering replacing a component part that has a cost of $2.50 with a new and better part costing $4.50 per unit in the coming year. A new machine also would be needed to increase plant capacity. The machine would cost $18,000 with a useful life of six years and no salvage value. The company uses straight-line depreciation on all plant assets. (Ignore income taxes). 1) If the firm holds the sales price constant and makes the suggested changes, how many units of product will the company have to sell to make the same net income as last year?arrow_forward
- AccountingAccountingISBN:9781337272094Author:WARREN, Carl S., Reeve, James M., Duchac, Jonathan E.Publisher:Cengage Learning,Accounting Information SystemsAccountingISBN:9781337619202Author:Hall, James A.Publisher:Cengage Learning,
- Horngren's Cost Accounting: A Managerial Emphasis...AccountingISBN:9780134475585Author:Srikant M. Datar, Madhav V. RajanPublisher:PEARSONIntermediate AccountingAccountingISBN:9781259722660Author:J. David Spiceland, Mark W. Nelson, Wayne M ThomasPublisher:McGraw-Hill EducationFinancial and Managerial AccountingAccountingISBN:9781259726705Author:John J Wild, Ken W. Shaw, Barbara Chiappetta Fundamental Accounting PrinciplesPublisher:McGraw-Hill Education
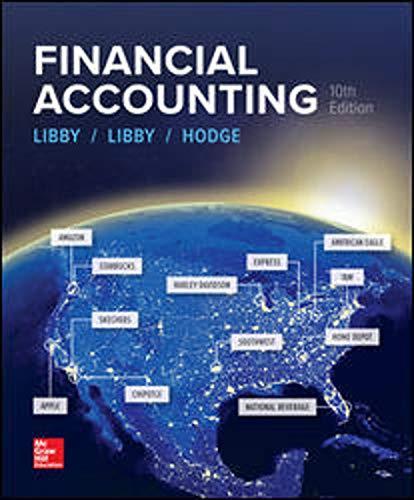
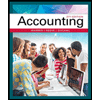
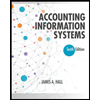
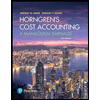
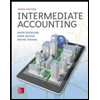
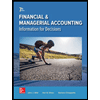