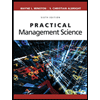
Practical Management Science
6th Edition
ISBN: 9781337406659
Author: WINSTON, Wayne L.
Publisher: Cengage,
expand_more
expand_more
format_list_bulleted
Concept explainers
Topic Video
Question
The primary objective of the basic economic order quantity model is
a. to calculate the reorder point so that resupply takes place at the proper time.
|
||
b. to minimize the sum of carrying cost and holding cost.
|
||
c. to maximize the customer service level.
|
||
d. to minimize the sum of the total ordering and holding costs.
|
||
e. to calculate the optimum safety stock.
|
Expert Solution

This question has been solved!
Explore an expertly crafted, step-by-step solution for a thorough understanding of key concepts.
This is a popular solution
Trending nowThis is a popular solution!
Step by stepSolved in 2 steps

Knowledge Booster
Learn more about
Need a deep-dive on the concept behind this application? Look no further. Learn more about this topic, operations-management and related others by exploring similar questions and additional content below.Similar questions
- Mr. Beautiful, an organization that sells weight training sets, has an ordering cost of $40 for the BB-1 set (BB-1 stands for Body Beautiful Number 1). The carrying cost for BB-1 is $5 per set per year. To meet demand, Mr. Beautiful orders large quantities of BB-1 7 times a year. The stockout cost for BB-1 is estimated to be $50 per set. Over the past several years, Mr. Beautiful has observed the following demand during the lead time for BB-1: Demand During Lead Time 40 50 60 70 80 90 The reorder point for BB-1 is 60 sets. What level of safety stock should be maintained for BB-1? The optimal quantity of safety stock which minimizes expected total cost is Probability 0.1 0.2 0.2 0.2 0.2 0.1 sets (enter your response as a whole number).arrow_forwardHenderson Furniture sells reproductions of 18th-century furniture. For a particular table, the assumptions of the inventory model with backorders are valid. Annual Demand: D = 200 tables per year Inventory holding cost (as a percent of the item cost): 1 = 25% per year Item cost: C = $800 per table Ordering cost: Co = $80 per order Backordering cost: Cb = $50 per table per year The store is open 250 days a year. What is the economic order quantity that will minimize the total cost? Results are expected to be rounded to the nearest whole number. ○ A. 28 B. 5 ○ C. 13 OD. 23 E. 14 QUESTION 4 What is the backorder quantity that will minimize the total cost? Results are expected to be rounded to the nearest whole number. ○ A. 14 B. 23 C. 13 OD. 28 ○ E. 5arrow_forwardA popular, local coffeeshop in one of the suburbs of New York City (NYC) estimates they use 3,000 pounds of coffee annually. They have to determine how many pounds to order each time in order to minimize their total annual cost. a. Determine the optimal size of the order assuming an EOQ model with a holding cost of $10 per pound annually and an ordering cost of $100. (Do not round intermediate calculations. Round your answer to 2 decimal places.) ✓ Answer is complete and correct. Optimal Q 244.95 b. The owner has recently opened another store of the same size in New York City; however, the demand for coffee is increased to 3,800 pounds annually, and the holding cost is $60 per pound. Those numbers are much higher as is the cost of real estate in NYC. The owner places orders of the same size as the first store because they are the same size stores. How much will the total cost be in the new coffeeshop? (Do not round intermediate calculations. Round your answer to 2 decimal places.)arrow_forward
- You are conducting a retrospective analysis for an Order-Up-To system (thus, the unsold inventory at the end of a week is carried over to the next week). The beginning inventory in week 1 is 150 units, the demand in week 1 is 180 units and the demand during week 2 is 250 units. If you receive a shipment of 115 units every week, at the end of week 2, the inventory level is 180 the inventory level is 200 the inventory level is 310 the backorder level is 30 the backorder level is 50 none of the above is correctarrow_forwardA company is planning for its financing needs and uses the basic fixed-order quantity inventory model. Which of the following is the total cost (TC) of the inventory given an annual demand of 10,000, setup cost of $32, a holding cost per unit per year of $4, an EOQ of 400 units, and a cost per unit of inventory of $150?arrow_forwardA small mail-order company uses 19,500 boxes a year. Holding cost rate is 19 percent of unit cost per year, and ordering cost is $27 per order. The following quantity discounts are available. Number of Boxes Price per Box 1,000 to 1,999 $1.20 2,000 to 4.999 1.15 5,000 to 9,999 1.10 10,000 or more 1.05 a. Determine the optimal order quantity. Optimal order quantity 2, 297 Numeric Response 1. Edit Unavailable. 2,297 incorrect.boxes b. Determine the number of orders per year. (Round the final answer to 1 decimal place.) No. of orders per year 8.4 Numeric Response 2. Edit Unavailable. 8.4 incorrect.arrow_forward
- A restaurant has an annual demand for 886 bottles of California wine. It costs $2 to store 1 bottle for 1 year, and it costs $10 to place a reorder. Find the optimum number of bottles per order.arrow_forwardBlue Wave corp will need 275,000 units of raw materials next year. The purchase price of the raw materials per unit is 950. The ordering cost for each order is 2,000, while the carrying cost is 30% of the average inventory value. Calculate:a. The most economical order quantity (EOQ)b. How many times should the company order in a year?c. How many days should the company place an order once (1 year = 365 days)?arrow_forwardThe following statements refer to the Economic Order Quantity (EOQ) model. Which of the following are true? I. The EOQ is found by minimizing the total demand function. II. Total annual purchasing costs affects the EOQ. III. The EOQ model takes the timing of reordering into account.arrow_forward
- The two most basic inventory questions answered by the typical inventory model are: A Housing costs B Material handling costs с Investment costs D Pilferage, scrap, and obsolescence E All of these are elements of inventory holding costsarrow_forwardthe economic order quantity (see Chapter 12 for EOQformulas) for its halogen lamps. It currently buys all halogenlamps from Specialty Lighting Manufacturers in Atlanta. Annualdemand is 2,000 lamps, ordering cost per order is $30, and annualcarrying cost per lamp is $12.a) What is the EOQ?b) What are the total annual costs of holding and ordering(managing) this inventory?c) How many orders should D iscount-Mart place with SpecialtyLighting per year?arrow_forwardSuppose that the R&B Beverage Company has a soft drink product that shows a constant annual demand rate of 3,600 cases. A case of the soft drink costs R&B $4. Ordering costs are $22 per order and holding costs are 23% of the value of the inventory. R&B has 250 working days per year, and the lead time is 5 days. Identify the following aspects of the inventory policy: a. Economic order quantity. If required, round your answer to two decimal places.Q = b. Reorder point. If required, round your answer to the nearest whole number.r =c. Cycle time. If required, round your answer to two decimal places.T = daysd. Total annual cost. If required, round your answer to two decimal places.TC = $arrow_forward
arrow_back_ios
SEE MORE QUESTIONS
arrow_forward_ios
Recommended textbooks for you
- Practical Management ScienceOperations ManagementISBN:9781337406659Author:WINSTON, Wayne L.Publisher:Cengage,Operations ManagementOperations ManagementISBN:9781259667473Author:William J StevensonPublisher:McGraw-Hill EducationOperations and Supply Chain Management (Mcgraw-hi...Operations ManagementISBN:9781259666100Author:F. Robert Jacobs, Richard B ChasePublisher:McGraw-Hill Education
- Purchasing and Supply Chain ManagementOperations ManagementISBN:9781285869681Author:Robert M. Monczka, Robert B. Handfield, Larry C. Giunipero, James L. PattersonPublisher:Cengage LearningProduction and Operations Analysis, Seventh Editi...Operations ManagementISBN:9781478623069Author:Steven Nahmias, Tava Lennon OlsenPublisher:Waveland Press, Inc.
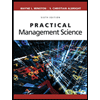
Practical Management Science
Operations Management
ISBN:9781337406659
Author:WINSTON, Wayne L.
Publisher:Cengage,
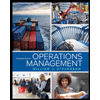
Operations Management
Operations Management
ISBN:9781259667473
Author:William J Stevenson
Publisher:McGraw-Hill Education
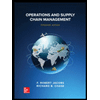
Operations and Supply Chain Management (Mcgraw-hi...
Operations Management
ISBN:9781259666100
Author:F. Robert Jacobs, Richard B Chase
Publisher:McGraw-Hill Education
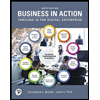
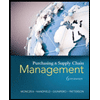
Purchasing and Supply Chain Management
Operations Management
ISBN:9781285869681
Author:Robert M. Monczka, Robert B. Handfield, Larry C. Giunipero, James L. Patterson
Publisher:Cengage Learning
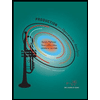
Production and Operations Analysis, Seventh Editi...
Operations Management
ISBN:9781478623069
Author:Steven Nahmias, Tava Lennon Olsen
Publisher:Waveland Press, Inc.