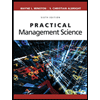
Suppose that the R&B Beverage Company has a soft drink product that shows a constant annual demand rate of 3,600 cases. A case of the soft drink costs R&B $4. Ordering costs are $22 per order and holding costs are 23% of the value of the inventory. R&B has 250 working days per year, and the lead time is 5 days. Identify the following aspects of the inventory policy:
a. Economic order quantity. If required, round your answer to two decimal places.
Q =
b. Reorder point. If required, round your answer to the nearest whole number.
r =
c. Cycle time. If required, round your answer to two decimal places.
T = days
d. Total annual cost. If required, round your answer to two decimal places.
TC = $

Trending nowThis is a popular solution!
Step by stepSolved in 2 steps with 3 images

- A printing company anticipates using 40,000 reams of paper at a uniform rate over the next year. Each time they place an order for X units of reams of paper, it is charged a flat fee of $200. Carrying costs are $4 per unit per year. A. use the formula for Economic Order Quantity to find out how many reams of paper they should purchase in each order. B. how many orders should they place over the year?arrow_forwardA daily newspaper is stocked by a coffee shop so its patrons can purchase and read it while they drink coffee. The newspaper costs $1.17 per unit and sells for $1.75 per unit. If units are unsold at the end of the day, the supplier takes them back at a rebate of $1 per unit. Assume that daily demand is approximately normally distributed with μ = 150 and a = 30. (a) What is your recommended daily order quantity for the coffee shop? (Round your answer to the nearest integer.) (b) What is the probability that the coffee shop will sell all the units it orders? (Round your answer to four decimal places.) (c) In problems such as these, why would the supplier offer a rebate as high as $1? For example, why not offer a nominal rebate? Find the recommended order quantity at 25¢ per unit. (Round your answer to the nearest integer.) What happens to the coffee shop's order quantity as the rebate is reduced? The higher rebate ---Select-- the quantity that the coffee shop should order.arrow_forwardYou are in charge of inventory control of a highly successful product retailed by your firm. Weekly demand for this item varies, with an average of 350 units and a standard deviation of 15 units. It is purchased from a wholesaler at a cost of $25.00 per unit. The supply lead time is 7 weeks. Placing an order costs $55.00, and the inventory carrying rate per year is 15 percent of the item's cost. Your firm operates 6 days per week, 50 weeks per year. Refer to the standard normal table The table below shows the total area under the normal curve for a point that is Z standard deviations to the right of the mean. Z 0.00 0.01 0.02 0.03 0.04 0.05 0.06 0.07 0.08 0.09 0.0 0.5000 0.5040 0.5080 0.5120 0.5160 0.5199 0.5239 0.5279 0.5319 0.5359 0.1 0.5398 0.5438 0.5478 0.5517 0.5557 0.5596 0.5636 0.5675 0.5714 0.5754 0.2 0.5793 0.5832 0.5871 0.5910 0.5948 0.5987 0.6026 0.6064 0.6103 0.6141…arrow_forward
- Yellow Press, Inc., buys paper in 1,500-pound rolls for printing. Annual demand is 3,000 rolls. The cost per roll is $1,000, and the annual holding cost is 28 percent of the cost. Each order costs $75. Part 2 a. How many rolls should Yellow Press order at a time? Yellow Press should order enter your response here rolls at a time. (Enter your response rounded to the nearest whole number.) Part 3 b. What is the time between orders? (Assume 200 workdays per year.) The time between orders is enter your response here days. (Enter your response rounded to one decimal place.)arrow_forwardYour objective is to help company by determining EOQ* (Economic Order Quantity) that minimizes the totalinventory cost for a company that sells ceiling fans. Your worksheet provides information about the currentorder quantity, demand quantity and other costs.Questions: Answer A and Ba. With the current order quantity, what is the total cost of inventory?b. Implement the problem in Excel and find the order quantity (EOQ) (round to nearest integer) that givesminimum inventory cost. Note: this is a Non-linear programming, hence select “GRG Nonlinear” method inSolver- How much money would company save by switching to optimum quantity from current orderquantity?arrow_forwardAn engineer has decided to pursue ordering option for a particular item on an as needed basis as oppose to stocking it. To stock the item, inventory inspection costs $500 annually. The cost to place an order is estimated at $125. For the ordering option, there is an additional $85 special delivery charge per order. Demand for the $20 item is 2,300 units per year. The annual holding cost rate is 40% of the item price. Calculate range of the order quantity that will make it economical to order this item every time. If the engineer decides to stock the item what is the order quantity that is economical.arrow_forward
- Please do not give solution in image format thankuarrow_forwardPlease do not give solution in image format thanku Regional Supermarket is open 360 days per year. Daily use of cash register tape averages 10 rolls. Usage appears normally distributed with a standard deviation of 2 rolls per day. The cost of ordering tape is $1 per order, and carrying costs are 40 cents per roll a year. Lead-time is three days. a) Ignoring the demand uncertainty (i.e., looking only at average values), find the economic order quantity (EOQ) and the reorder point (ROP). b) Consider now the uncertainty. The order quantity remains the same. If the target is to have a 99% annual service level, what should be the ROParrow_forward
- Practical Management ScienceOperations ManagementISBN:9781337406659Author:WINSTON, Wayne L.Publisher:Cengage,Operations ManagementOperations ManagementISBN:9781259667473Author:William J StevensonPublisher:McGraw-Hill EducationOperations and Supply Chain Management (Mcgraw-hi...Operations ManagementISBN:9781259666100Author:F. Robert Jacobs, Richard B ChasePublisher:McGraw-Hill Education
- Purchasing and Supply Chain ManagementOperations ManagementISBN:9781285869681Author:Robert M. Monczka, Robert B. Handfield, Larry C. Giunipero, James L. PattersonPublisher:Cengage LearningProduction and Operations Analysis, Seventh Editi...Operations ManagementISBN:9781478623069Author:Steven Nahmias, Tava Lennon OlsenPublisher:Waveland Press, Inc.
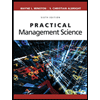
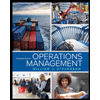
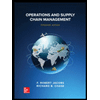
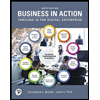
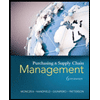
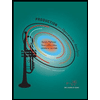