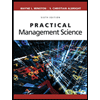
The Makonsel Company is a fully integrated company that both produces goods and sells them at its retail outlets. After production, the goods are stored in the company's two warehouses until needed by the retail outlets. Trucks are used to transport the goods from the two plants to the warehouses, and then from the warehouses to the three retail outlets. Using units of full truckloads, the following table shows each plant's monthly output, its shipping cost per truckload sent to each warehouse, and the maximum amount that it can ship per month to each warehouse. To Unit Shipping Cost Shipping Capacity From Warehouse 1 Warehouse 2 Warehouse 1 Warehouse 2 Output Plant 1 $425 $560 125 150 200 Plant 2 $510 $600 175 200 300 For each retail outlet (RO), the next table shows its monthly demand, its shipping cost per truckload from each warehouse, and the maximum amount that can be shipping per month from each warehouse. To Unit Shipping Cost Shipping Capacity From RO1 RO2 RO3 RO1 RO2 RO3 Warehouse 1 $470 $505 $490 100 150 100 Warehouse 2 $390 $410 $440 125 150 75 Demand 150 200 150 150 200 150 Management now wants to determine a distribution plan (number of truckloads shipped per month from each plant to each warehouse and from each warehouse to each retail outlet) that will minimize the total shipping cost. (a) Draw a network that depicts the company's distribution network. Identify the supply nodes, transshipment nodes, and demand nodes in this network. (b) Formulate this problem as a minimum cost flow problem by inserting all the necessary data into this network (c) Use Excel Solve to solve this problem.
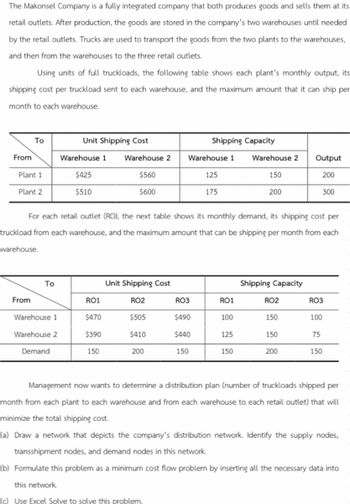

Trending nowThis is a popular solution!
Step by stepSolved in 3 steps with 5 images

- Yang's Material Company hauls gravel to a construction site, using a small truck and a large truck. The carrying capacity and operating cost per load are given in the accompanying table. Yang must deliver a minimum of 120 cubic yards per day to satisfy his contract with the builder. The union contract with his drivers requires that the total number of loads per day is a minimum of 5. How many loads should be made in each truck per day to minimize the total cost? Small Truck Large Truck 40 $44 Capacity (yd³) Cost per Load 30 $76 In order to minimize the total cost, the number of loads in a small truck that should be made is loads in a large truck that should be made is and the number ofarrow_forwardKala is one of the top manufacturer of ukuleles. The manufacturer produces three different types of ukuleles. Its Concert produce $6 in profit per unit; its Soprano produce $4 in profit per unit; and its Tenor produce $8 in profit per unit. Each type of ukulele passes through three manufacturing stages as a part of the entire production process. The three process centers of modelling, curing and assembly has an available production time per day of 12 hours, 14 hours and 16 hours, respectively. To produce one hundred units of Concert, the time required for the process of modelling, curing and assembly is 2 hours, 3 hours and 2 hours, respectively. To produce one hundred units of Soprano, 2 hours of modelling, 2 hours of curing and 1 hour of assembly is required. Whereas 4 hours of modelling, 2 hours of curing and 2 hours of assembly is required to produce one hundred units of Tenor. Sensitivity report of the problem is given as below where C = unit of Concert to be produced each day, S…arrow_forwardwhat is a conitnues location problem in supply chain? how can we solve it? what are the givens and what is the output? briefly give a way to solve a continues location problemarrow_forward
- The Petoskey Potato Chip Company produces 3 varieties of gourmet potato chip. The varieties and average daily demand are given below: Bar-B-Que: 325 cases/day Sour Cream & Onion: 215 cases/day Classic Cut: 360 ases/day The company runs 24 hours/day and can produce 1,300 cases of potato chips per day. Each case of potato chip costs $20 to produce and Petoskey assumes 18% of this cost as the annual holding cost. It takes Petoskey 5 hours to setup for production of a different variety at a cost of $715. Calculate the minimum cost cycle time in days. Answer: 25.2 How is this calculated?arrow_forwardThe Dahlia Medical Center has 34 labor rooms, 18 combination labor and delivery rooms, and 5 delivery rooms. All of these facilities operate around the clock. Time spent in labor rooms varies from hours to days, with an average of about a day. The average uncomplicated delivery requires about one hour in the delivery room. The average time in a combination labor-delivery room is about 24 hours. During an exceptionally busy three-day period, 101 healthy babies were born at Dahlia Medical Center. 59 babies were born in separate labor and delivery rooms and 42 were born in combined labor and delivery rooms. Which of the facilities (labor rooms, combination labor and delivery rooms, or delivery rooms) had the greatest utilization rate? ▼had the highest utilization rate of %. (Enter your response as a percent rounded to two decimal places.) The combination labor and delivery rooms delivery rooms labor roomsarrow_forwardABC Apple Juice Company produces and markets fresh fruit juice. During the apple harvest season, trucks bring apples from the fields to the process plant during a workday that runs long hours from 7AM. On peak days, approximately 3,000 kg of apples are trucked in per hour. Trucks dump their contents in a holding bin with a storage capacity of 9,000 kg. When the bin is full, incoming trucks must wait until it has sufficient available space. A conveyor moves apples from bin to the processing plant. The plant is configured to process apples at the rate of 2,000 kg per hour. Trucks arrive uniformly between 7:00AM to 5:00PM. Each truck holds about 1,000 kg of apples. The truck drivers are paid at the rate of $10 per hour. As ABC makes fresh juice, it does not store apples. Processing plant starts at 10:00AM and ends when all the apples received during the day have been processed. It takes 2 hours to clean the empty plant that must be kept ready for the next day production. Trucks are owned…arrow_forward
- Tarmac was established in 1903 and is the UK’s leading supplier of building materials and aggregates to the building industry. Tarmac is most often associated with constructing roads or major building projects such as the new Heathrow terminal and Wembley Stadium. However, materials derived from quarrying are used within many different sectors, including manufacturing light bulbs, chewing gum and toothpaste. Tarmac’s operational structure is divided into two key areas: Tarmac UK and Tarmac International. Tarmac UK is sub-divided into two separate businesses: Tarmac Ltd extracts key building aggregates and materials; and Tarmac Building Products Ltd focuses on turning raw materials into products useable by the building sector. Tarmac International develops building products for supply around the world, especially in the United Arab Emirates. Nearly 11,000 employees work for Tarmac in a variety of work settings that include: 135 quarries 13 wharves 73 asphalt plants 172 concrete plants…arrow_forwardPol Industries uses a job order cost system and applies manufacturing overhead costs to jobs using a predetermined overhead rate based on direct labour-hours. The following data were extracted from the company's accounting records for Year 6 Estimated Actual Manufacturing overhead costs 50,000 54,000 direct labour-hours 20,000 hours 24,000 hoursJob #461 was completed during the year and the following costs had been incurred on that job:direct materials 4000 direct labour 1500(at $5.00 per direct labour hour) Suppose Job #461 contained 100 units. What unit cost would appear on the job cost sheet for job #461? Show ALL calculations.arrow_forwardSusan manages the packaging supplies for the New Zealand distributorship of AllBirds product lines. It;s her job to order all the shoe boxes that house each pair of shoes (whether going to retail stores, or shipping directly to consumers via the online store). She purchases shoe boxes from a local printing supplier. The NZ distributor ships on average 325 boxes of shoes each month. Boxes cost $2.25 each, and each order costs $18 to process. Because of limited storage space, Susan's manager wants to charge inventory holding at 25% of the unit cost. The lead time is 7 days. Assume 360 working days per year. Calculate the following: a. Economic order Wuantity b. Reorder Point (assuming no safety stocks) c.Number of orders-per-Year d.Total annual cost e.If storage space was so limited, Susan estimates that inventory holding cots would only be 15% of unit cost. How would that change total annual costs?arrow_forward
- Practical Management ScienceOperations ManagementISBN:9781337406659Author:WINSTON, Wayne L.Publisher:Cengage,Operations ManagementOperations ManagementISBN:9781259667473Author:William J StevensonPublisher:McGraw-Hill EducationOperations and Supply Chain Management (Mcgraw-hi...Operations ManagementISBN:9781259666100Author:F. Robert Jacobs, Richard B ChasePublisher:McGraw-Hill Education
- Purchasing and Supply Chain ManagementOperations ManagementISBN:9781285869681Author:Robert M. Monczka, Robert B. Handfield, Larry C. Giunipero, James L. PattersonPublisher:Cengage LearningProduction and Operations Analysis, Seventh Editi...Operations ManagementISBN:9781478623069Author:Steven Nahmias, Tava Lennon OlsenPublisher:Waveland Press, Inc.
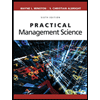
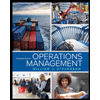
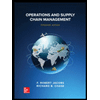
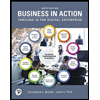
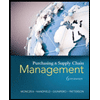
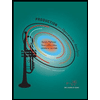