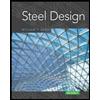
Steel Design (Activate Learning with these NEW titles from Engineering!)
6th Edition
ISBN: 9781337094740
Author: Segui, William T.
Publisher: Cengage Learning
expand_more
expand_more
format_list_bulleted
Question
The bell-crank mechanism is in equilibrium for an applied load of P= 40 kN. Assume that a = 300 mm, b = 245 mm, and 0 = 61° The pin
at B has a diameter of d = 12 mm, and the bell crank has a thickness of t= 12 mm. Calculate the average shear stress in the pin at B.
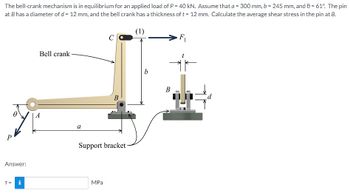
Transcribed Image Text:The bell-crank mechanism is in equilibrium for an applied load of P = 40 kN. Assume that a = 300 mm, b = 245 mm, and 0 = 61°. The pin
at B has a diameter of d = 12 mm, and the bell crank has a thickness of t = 12 mm. Calculate the average shear stress in the pin at B.
(1)
P
Answer:
T = i
Bell crank
A
a
C
MPa
B
Support bracket
b
B
F₁
IF
d
Expert Solution

This question has been solved!
Explore an expertly crafted, step-by-step solution for a thorough understanding of key concepts.
This is a popular solution
Trending nowThis is a popular solution!
Step by stepSolved in 3 steps with 3 images

Knowledge Booster
Learn more about
Need a deep-dive on the concept behind this application? Look no further. Learn more about this topic, civil-engineering and related others by exploring similar questions and additional content below.Similar questions
- Verify the value of Zx for a W1850 that is tabulated in the dimensions and properties tables in Part 1 of the Manual.arrow_forwardUse an elastic analysis and determine the maximum load in the weld (in kips per inch of length).arrow_forwardA plate girder must be designed for the conditions shown in Figure P10.7-4. The given loads are factored, and the uniformly distributed load includes a conservative estimate of the girder weight. Lateral support is provided at the ands and at the load points. Use LRFD for that following: a. Select the, flange and web dimensions so that intermediate stiffeners will he required. Use Fy=50 ksi and a total depth of 50 inches. Bearing stiffeners will be used at the ends and at the load points, but do not proportion them. b. Determine the locations of the intermediate stiffeners, but do not proportion them.arrow_forward
- A beam is part of the framing system for the floor of an office building. The floor is subjected to both dead loads and live loads. The maximum moment caused by the service dead load is 45 ft-kips, and the maximum moment for the service live load is 63 ft-kips (these moments occur at the same location on the beam and can therefore be combined). a. If load and resistance factor design is used, determine the maximum factored bending moment (required moment strength). What is the controlling AISC load combination? b. What is the required nominal moment strength for a resistance factor of 0.90? c. If allowable strength design is used, determine the required moment strength. What is the controlling AISC lead combination? d. What is the required nominal moment strength for a safety factor of 1.67?arrow_forwardSelect an American Standard Channel shape for the following tensile loads: dead load = 54 kips, live load = 80 kips, and wind load = 75 kips. The connection will be with longitudinal welds. Use an estimated shear lag factor of U = 0.85. (In a practical design, once the member was selected and the connection designed, the value of U would be computed and the member design could be revised if necessary.) The length is 17.5 ft. Use Fy=50 ksi and Fu=65 ksi. a. Use LRFD. b. Use ASD.arrow_forward
arrow_back_ios
arrow_forward_ios
Recommended textbooks for you
- Steel Design (Activate Learning with these NEW ti...Civil EngineeringISBN:9781337094740Author:Segui, William T.Publisher:Cengage Learning
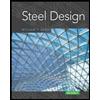
Steel Design (Activate Learning with these NEW ti...
Civil Engineering
ISBN:9781337094740
Author:Segui, William T.
Publisher:Cengage Learning