Terex Corporation is a global manufacturer of aerial work platforms and materials processing machinery. They design, build and support products such as large lifting equipment used in construction. The company makes most pieces to order and customizes them to meet customers’ unique preferences. Terex maintained a manual system for yard management at their transfer centre in Washington that is always full of lifting equipment, which generated excessive costs for what should have been a relatively simple process of locating customers’ units to prepare them for delivery. A wallboard and sticker system was a low-tech solution for identifying equipment items in the yard at Terex. While inexpensive in itself, the solution cost around six minutes every time an employee had to locate a unit in the yard. It also required a considerable number of hours to be spent each month taking physical inventories. After a successful pilot, the company approved a new solution, replacing stickers, yard maps, and wallboard with electronic tracking and digital inventory management. This saved the company around 70 weeks per year in labour costs, by cutting the process-time down from six minutes, to a mere 30 seconds per unit. QUESTION: Assess the financial costs of holding too much inventory, with application to the case study.
Terex Corporation is a global manufacturer of aerial work platforms and materials processing
machinery. They design, build and support products such as large lifting equipment used in
construction. The company makes most pieces to order and customizes them to meet customers’
unique preferences.
Terex maintained a manual system for yard management at their transfer centre in Washington
that is always full of lifting equipment, which generated excessive costs for what should have been
a relatively simple process of locating customers’ units to prepare them for delivery. A wallboard
and sticker system was a low-tech solution for identifying equipment items in the yard at Terex.
While inexpensive in itself, the solution cost around six minutes every time an employee had to
locate a unit in the yard. It also required a considerable number of hours to be spent each month
taking physical inventories. After a successful pilot, the company approved a new solution, replacing
stickers, yard maps, and wallboard with electronic tracking and digital inventory management. This
saved the company around 70 weeks per year in labour costs, by cutting the process-time down
from six minutes, to a mere 30 seconds per unit.
QUESTION: Assess the financial costs of holding too much inventory, with application to the
case study.

Step by step
Solved in 2 steps with 2 images

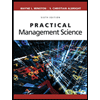
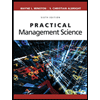