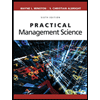
Practical Management Science
6th Edition
ISBN: 9781337406659
Author: WINSTON, Wayne L.
Publisher: Cengage,
expand_more
expand_more
format_list_bulleted
Concept explainers
Topic Video
Question
1) Store A orders on a weekly basis. Its weekly demand is 50 units with a standard deviation of five units. The holding cost is $10 per unit per week and a 0.99 in-stock probability is desired. What is Store A’s average holding cost incurred each week for on-order inventory if lead time is five weeks?
2) Store A orders on a weekly basis. Its weekly demand is 50 units with a standard deviation of five units. The holding cost is $10 per unit per week and a 0.99 in-stock probability is desired. What is Store A’s average on-hand inventory if lead time is five weeks?
Expert Solution

This question has been solved!
Explore an expertly crafted, step-by-step solution for a thorough understanding of key concepts.
This is a popular solution
Trending nowThis is a popular solution!
Step by stepSolved in 4 steps with 5 images

Knowledge Booster
Learn more about
Need a deep-dive on the concept behind this application? Look no further. Learn more about this topic, operations-management and related others by exploring similar questions and additional content below.Similar questions
- Alpha Products, Inc., is having a problem trying to control inventory. There is insufficient time to devote to all its items equally. The following is a sample of some items stocked, along with the annual usage of each item expressed in dollar volume. ITEM ANNUAL DOLLAR USAGE ITEM ANNUAL DOLLAR USAGE a S 30, 100 k S 1,700 b 27,000 120,000 c 93,000 m 111,000 d 1,400 n 3,000 e 1,800 o 500 f 30,000 p 114, 000 g 1,600 q 2,600 h 2,500 г 28,000 i 3, 200 s 2, 800 j 1,500 t 3, 100 a. Suggest a system for allocating control time? multiple choice ABC analysis Cycle counting b. Specify where each item from the list would be placed.arrow_forwardYou are a newsvendor selling the San Pedro Times every morning. Before you get to work, you go to the printer and buy the day's paper for $0.25 a copy. You sell a copy of the San Pedro Times for $1.30. Daily demand is distributed normally with mean = 260 and standard deviation = 46. At the end of each morning, any leftover copies are worthless and they go to a recycle bin. a. How many copies of the San Pedro Times should you buy each morning? Note: Use Excel's NORM.S.INV() function to find the z value. Round your z value and service level to 2 decimal places and final answer to the nearest whole number. Optimal order quantity b. Based on a, what is the probability that you will run out of stock? Note: Round your answer to the nearest whole percent. Probability %arrow_forwardBakery A sells bread for $2 per loaf that costs $0.50 per loaf to make. Bakery A gives an 80% discount for its bread at the end of the day. Demand for the bread is normally distributed with a mean of 300 and a standard deviation of 30. What order quantity maximizes expected profit for Bakery A? (use the normal distribution table posted on Canvas and round up to the nearest integer)arrow_forward
- the economic order quantity (see Chapter 12 for EOQformulas) for its halogen lamps. It currently buys all halogenlamps from Specialty Lighting Manufacturers in Atlanta. Annualdemand is 2,000 lamps, ordering cost per order is $30, and annualcarrying cost per lamp is $12.a) What is the EOQ?b) What are the total annual costs of holding and ordering(managing) this inventory?c) How many orders should D iscount-Mart place with SpecialtyLighting per year?arrow_forwardA medical equipment has an average monthly demand is 134 units. Its unit cost is $385. It costs $486 to place an order, and the inventory carrying cost is $44 per unit per year. The equipment requires a 95% of service level with a safety stock requirement of 20 units. What is the equipment's minimum annual total inventory cost?arrow_forwardSoutheastern Bell stocks a certain switch connector at its central warehouse for supplying field service offices. The yearly demand for these connectors is 15,200 units. Southeastern estimates its annual holding cost for this item to be 323 per unit. The cost to place and process an order from the supplier is $73. The company operates 300 days per year, and the lead time to receive an order from the supplier is 2 working days. a) What is the economic order quantity? units (round your response to the nearest whole number). b) What are the annual holding costs? $ (round your response to the nearest whole number) c) What are the annual ordering costs? S (round your response to the nearest whole number). d) What is the reorder point? units (round your response to the nearest whole number).arrow_forward
- kaiarrow_forwardABC Corporation resells one type of candle. It has 250 working days. Each day, it sells an average of 500 boxes but maysometimes sell a maximum of 600 boxes. The supplier takes an average of 5 days to deliver the order. During busier times, thesupplier may take 7 days.Based on ABC’s records, ordering cost average P400 per order. Storage cost per box average P5 per year. There is also anopportunity cost of 1% per year for every peso invested in inventories. Each box of candles costs P450. If ABC would continue its current inventory management policy, it would keep 10,000 boxes as safety stock and order ten-days-worth of inventory. (B) Economic Order Quantity 1. How much would the total inventory related (ordering plus carrying) costs be if the economic order quantity wasfollowed (excluding safety stock)? (D) Cost-Benefit Analysis: If ABC maintains its current inventory policy for the year,1. How much would the entity save it followed the reorder point and economic order quantity models?…arrow_forwardAssuming Normal Distribution, what would the optimal (s,Q) policy be for the given parameters below? Given data: Demand daily has mu = 1768, sigma = 5.37, with a unit purchased cost is $15 (annual interest rate is 20%). The order cost is $50 with a back ordering cost of $25. The order lead time is 3 days.arrow_forward
- 3. Skinner’s Fish Market buys fresh Boston bluefish daily for $4.20 per pound and sells it for $6 per pound. At the end of each business day, any remaining bluefish is sold to a producer of cat food for $3 per pound. Daily demand can be approximated by a normal distribution with a mean of 64 pounds and a standard deviation of 11 pounds. What is the optimal order quantity (stocking level)? Round your answer to 2 decimal places. Answer:_______arrow_forwardPalin’s Muffler Shop has one standard muffler that fits a large variety of cars. The shop wishes to establish a periodic review system to manage inventory of this standard muffler. Use the information in the following table to answer the below questions. Annual demand 3,000 mufflers Standard deviation of daily demand 6 mufflers per working day Item cost $30 per muffler Annual holding cost 25% of item value Review period 15 working days Ordering cost $50 per order Service probability 90% Lead time 2 working days Working days 300 per year What is the optimal target level (order-up-to level)? Note: Use Excel's NORM.S.INV() function to find the z value. Round z value to 2 decimal places and final answer to the nearest whole number. If the service probability requirement is 95 percent, the optimal target level will: multiple choice Increase Decrease Stay the samearrow_forwardAnnual demand for a product is 11,960 units; weekly demand is 230 units with a standard deviation of 50 units. The cost of placing an order is $125, and the time from ordering to receipt is four weeks. The annual inventory carrying cost is $0.80 per unit. To provide a 98 percent service probability, what must the reorder point be? Suppose the production manager is told to reduce the safety stock of this item by 125 units. If this is done, what will the new service probability be?arrow_forward
arrow_back_ios
SEE MORE QUESTIONS
arrow_forward_ios
Recommended textbooks for you
- Practical Management ScienceOperations ManagementISBN:9781337406659Author:WINSTON, Wayne L.Publisher:Cengage,Operations ManagementOperations ManagementISBN:9781259667473Author:William J StevensonPublisher:McGraw-Hill EducationOperations and Supply Chain Management (Mcgraw-hi...Operations ManagementISBN:9781259666100Author:F. Robert Jacobs, Richard B ChasePublisher:McGraw-Hill Education
- Purchasing and Supply Chain ManagementOperations ManagementISBN:9781285869681Author:Robert M. Monczka, Robert B. Handfield, Larry C. Giunipero, James L. PattersonPublisher:Cengage LearningProduction and Operations Analysis, Seventh Editi...Operations ManagementISBN:9781478623069Author:Steven Nahmias, Tava Lennon OlsenPublisher:Waveland Press, Inc.
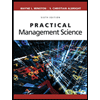
Practical Management Science
Operations Management
ISBN:9781337406659
Author:WINSTON, Wayne L.
Publisher:Cengage,
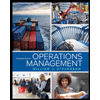
Operations Management
Operations Management
ISBN:9781259667473
Author:William J Stevenson
Publisher:McGraw-Hill Education
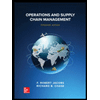
Operations and Supply Chain Management (Mcgraw-hi...
Operations Management
ISBN:9781259666100
Author:F. Robert Jacobs, Richard B Chase
Publisher:McGraw-Hill Education
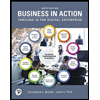
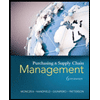
Purchasing and Supply Chain Management
Operations Management
ISBN:9781285869681
Author:Robert M. Monczka, Robert B. Handfield, Larry C. Giunipero, James L. Patterson
Publisher:Cengage Learning
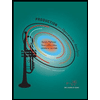
Production and Operations Analysis, Seventh Editi...
Operations Management
ISBN:9781478623069
Author:Steven Nahmias, Tava Lennon Olsen
Publisher:Waveland Press, Inc.