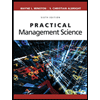
ABC Corporation resells one type of candle. It has 250 working days. Each day, it sells an average of 500 boxes but may
sometimes sell a maximum of 600 boxes. The supplier takes an average of 5 days to deliver the order. During busier times, the
supplier may take 7 days.
Based on ABC’s records, ordering cost average P400 per order. Storage cost per box average P5 per year. There is also an
opportunity cost of 1% per year for every peso invested in inventories. Each box of candles costs P450.
If ABC would continue its current inventory management policy, it would keep 10,000 boxes as safety stock and order ten-
days-worth of inventory.
(B) Economic Order Quantity
1. How much would the total inventory related (ordering plus carrying) costs be if the economic order quantity was
followed (excluding safety stock)?
(D) Cost-Benefit Analysis: If ABC maintains its current inventory policy for the year,
1. How much would the entity save it followed the reorder point and economic order quantity models?
2. How would you describe the entity’s current policy?

Step by stepSolved in 3 steps with 13 images

- The purchasing agent for a company that assembles and sells air-conditioning eqpt in US has noted that the cost of compressors has increased significantly each time they have reordered. The company uses EOQ model to determine order size. What are the implications of this price escalation with respect to order size? What factors other than price must be taken into consideration?arrow_forwardCaring Hospital's dispensary reorders doses of a drug when the supply on hand falls to 18 units. Lead time for resupply is three days. Given the typical usage over the last 10 days, what service level is achieved with the hospital's reorder policy? (Hint. Use the following formula.) (Do not round intermediate calculations. Round your "z" value and final answer to 2 decimal places.) Use Table. ROP =dLT +2 (od) √LT Day Units 1 3 2 3 4 4 7 5 Service level Click here for the Excel Data File 5 5 % 6 6 7 4 8 3 9 4 10 5arrow_forwardA produce distributor uses 720 packing crates a month, which it purchases at a cost of $10 each. The manager has assigned an annual carrying cost of 35 percent of the purchase price per crate. Ordering costs are $28. Currently the manager orders once a month. How much could the firm save annually in ordering and carrying costs by using the EOQ? (Round intermediate calculations and final answer to 2 decimal places. Omit the "$" sign in your response.) Savings$ ____per yeararrow_forward
- Southern Markets, Inc. is considering the use of ABCanalysis to focus on the most critical SKUs in its inventory.Currently, there are approximately 20,000 different SKUswith a total dollar usage of $10,000,000 per year.a. What would you expect to be the number of SKUs and thetotal annual dollar usage for A items, B items, and C itemsat Southern Markets, Inc.? b. The following table provides a random sample of the unitvalues and annual demands of eight SKUs. Categorizethese SKUs as A, B, and C items.arrow_forwardPlease do not give solution in image format thanku A small mail-order company uses 14,000 boxes a year. Holding cost rate is 18 percent of unit cost per year, and ordering cost is $33 per order. The following quantity discounts are available. Number of Boxes Price per Box 1,000 to 1,999 $1.15 2,000 to 4,999 1.10 5,000 to 9,999 1.05 10,000 or more 1.00 a. Determine the optimal order quantity. Optimal order quantity boxes b. Determine the number of orders per year. (Round the final answer to 1 decimal place.) No. of orders per yeararrow_forwardEE Co has calculated the following in relation to its inventories.Buffer inventory level 60 unitsReorder size 250 itemsFixed order costs $40 per orderCost of holding onto one item pa $1.5 per yearAnnual demand 10,000 itemsPurchase price $2 per itemWhat is the total inventory related costs for a year (to the nearest whole $)?arrow_forward
- At a recent manufacturing workshop, XYZ, Incorporated explained that demand for disposable masks increase rapidly in March 2020 when quarantine mandates first took effect. At the time, retailers could only place a single order to cover demands through the end of the summer. A certain retailer purchased disposal masks from a supplier at a cost of $20 per unit and sold them for $30 per unit. By the end of summer, demand for masks subsided considerably and all masks that weren't sold during the summer could be sold at a discounted price of $18 per unit. The retailer estimated that demand between March and August would be Normally distributed with mu = 10,000 and sigma = 1525 units With, supply chains becoming more stable since March 2020, the retailer is currently in the process of establishing a contract with a disposable mask supplier. The supplier has agreed to sell masks to the retailer for $18 per unit and will make deliveries any time the supplier places an order for a cost of $100…arrow_forwardDemand during lead time for one brand of TV is normallydistributed with a mean of 36 TVs and a standard deviationof 15 TYs. What safety stock should be carried for DennisYu's Appliance Outlet to provide a 90% service level? What is theappropriate reorder point?arrow_forwardPaul’s Toy Distributor (PTD) sells 200 game consoles every week. PTD charges a $300 fixed cost for every delivery. PTD’s annual inventory holding cost is $45 per console. Assume that there are 52 weeks a year. Assume that PTD orders 1000 game consoles at a time. What is the average amount of time the consoles stay as PTD’s inventory before being sold? Find the closest answer.arrow_forward
- A pipe manufacturer requires a chemical for making plastic at the rate of 6,000 gallons per year. The cost of keeping the chemical storage includes both the cost of the special security precautions in the storage space and borrowing money on short-term loans to pay for the purchase; this works out to about $10 per gallon per year. Ordering costs, which include cost of special transportation, work out to $200 per order. The chemical is bought at $45 per gallon. What is the EOQ and annual total cost?arrow_forwardIn an ABC system based on revenue, C items individually make the lowest annual revenue contribution. TRUE FALSEarrow_forwardGive typed full explanationarrow_forward
- Practical Management ScienceOperations ManagementISBN:9781337406659Author:WINSTON, Wayne L.Publisher:Cengage,Operations ManagementOperations ManagementISBN:9781259667473Author:William J StevensonPublisher:McGraw-Hill EducationOperations and Supply Chain Management (Mcgraw-hi...Operations ManagementISBN:9781259666100Author:F. Robert Jacobs, Richard B ChasePublisher:McGraw-Hill Education
- Purchasing and Supply Chain ManagementOperations ManagementISBN:9781285869681Author:Robert M. Monczka, Robert B. Handfield, Larry C. Giunipero, James L. PattersonPublisher:Cengage LearningProduction and Operations Analysis, Seventh Editi...Operations ManagementISBN:9781478623069Author:Steven Nahmias, Tava Lennon OlsenPublisher:Waveland Press, Inc.
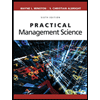
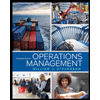
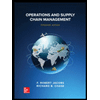
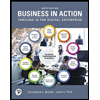
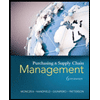
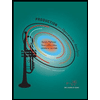