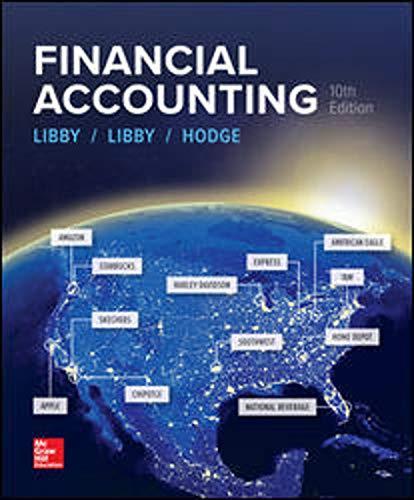
FINANCIAL ACCOUNTING
10th Edition
ISBN: 9781259964947
Author: Libby
Publisher: MCG
expand_more
expand_more
format_list_bulleted
Question
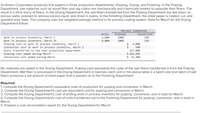
Transcribed Image Text:Scribners Corporation produces fine papers in three production departments-Pulping, Drying, and Finishing. In the Pulping
Department, raw materials such as wood fiber and rag cotton are mechanically and chemically treated to separate their fibers. The
result is a thick slurry of fibers. In the Drying Department, the wet fibers transferred from the Pulping Department are laid down on
porous webs, pressed to remove excess liquid, and dried in ovens. In the Finishing Department, the dried paper is coated, cut, and
spooled onto reels. The company uses the weighted-average method in its process costing system. Data for March for the Drying
Department follow:
Percent Completed
Pulping
Units
Conversion
Work in process inventory, March 1
Work in process inventory, March 31
Pulping cost in work in process inventory, March 1
Conversion cost in work in process inventory, March 1
Units transferred to the next production department
Pulping cost added during March
Conversion cost added during March
5,000
8,000
100%
20%
100%
25%
$4
4,800
$
500
157,000
$ 102,450
$ 31,300
No materials are added in the Drying Department. Pulping cost represents the costs of the wet fibers transferred in from the Pulping
Department. Wet fiber is processed in the Drying Department in batches; each unit in the above table is a batch and one batch of wet
fibers produces a set amount of dried paper that is passed on to the Finishing Department.
Required:
1. Compute the Drying Department's equivalent units of production for pulping and conversion in March.
2. Compute the Drying Department's cost per equivalent unit for pulping and conversion in March.
3. Compute the Drying Department's cost of ending work in process inventory for pulping, conversion, and in total for March.
4. Compute the Drying Department's cost of units transferred out to the Finishing Department for pulping, conversion, and in total in
March.
5. Prepare a cost reconciliation report for the Drying Department for March.
Expert Solution

This question has been solved!
Explore an expertly crafted, step-by-step solution for a thorough understanding of key concepts.
This is a popular solution
Trending nowThis is a popular solution!
Step by stepSolved in 3 steps

Knowledge Booster
Similar questions
- Lead Time iSounds Inc. manufactures electronic stereo equipment. The manufacturing process includes printed circuit (PC) board assembly, final assembly, testing, and shipping. In the PC board assembly operation, a number of individuals are responsible for assembling electronic components into printed circuit boards. Each operator is responsible for soldering components according to a given set of instructions. Operators work on batches of 20 printed circuit boards. Each board requires 5 minutes of board assembly time. After each batch is completed, the operator moves the assembled boards to the final assembly area. This move takes 10 minutes to complete. The final assembly for each stereo unit requires 16 minutes and is also done in batches of 20 units. A batch of 20 stereos is moved into the test building, which is across the street. The move takes 20 minutes. Before conducting the test, the test equipment must be set up for the particular stereo model. The test setup requires 25…arrow_forwardCaricolor Limited operates a paint manufacturing plant, housing two distinct departments: the mixing department and the quality control department. The paint undergoes sequential processing in both of these departments.The company's process-costing system is structured around two primary cost categories: direct materials and conversion costs. Direct materials are introduced at the initial stages of the process, while conversion costs are gradually incurred throughout the process. After completion of the mixing department's tasks on the paint, the product is promptly forwarded to the quality control department. Caricolor employs the weighted-average method for process costing to calculate its manufacturing costs. Data for the mixing department for October 2020 are as follows: Required: 3. Assign total costs to units completed and transferred out and to units in ending work in process? 4. By reference to the above data, explain the concept of equivalent units in process costing?arrow_forwardCarrie’s Limited has two departments, the assembly department and the testing department in its brake-pad manufacturing plant, where each brake-pad is conveyed through each department. Carrie’s process-costing system consist of two cost categories: Single direct cost (direct materials) and a single indirect-cost category (conversion costs). Direct materials are added at the beginning of the process. Conversion costs are added evenly during the process. When the assembly department finishes work on each brake-pad, it is immediately transferred to testing. Carrie’s uses the weighted-average method of process costing. Data for the assembly department for October 2019 are as follows: Physical Units (Brake Pads) Direct Materials Conversion CostsWork in process, October 1x 6,000 $1,200,000 $ 400,750Started during October 2019 21,000Completed during October 2019 23,500Work in process, October 31y 3,500Total costs added during October 2019 $4,600,000 $2,456,500x Degree of completion: direct…arrow_forward
- Christie's Co. manufactures cookies. The company has two departments, Mixing and Baking. For the Baking Department, material is added at the beginning of the process. Work happens evenly throughout the process, so Conversion Costs are added evenly to the product. Once mixing is complete, the cookies pieces are immediately transferred to the Baking Department. Once the baking is complete, the final product is transferred to Finished Goods Inventory. Data for the Baking Department is as follows: Units Transfer $ DirectMaterials $ % Complete Conv Costs % Complete Opening WIP 550 $3,500 $2,800 100% $2,100 30% New units & Costs 2,000 $12,300 $8,100 $14,000 Ending WIP 680 ??? 65% Calculate the physical and equivalent units for Transferred-In, Direct Materials and Conversion Costsarrow_forwardGladden Dock Company manufactures boat docks on an assembly line. Its costing system uses two cost categories, direct materials and conversion costs. Each product must pass through the Assembly Department and the Finishing Department. This problem focuses on the Assembly Department. Direct materials are added at the beginning of the production process. Conversion costs are allocated evenly throughout production. The firm uses FIFO method and the controller prepared the following (correct) equivalent unit calculation. Unitscompleted Physical Units Direct Materials Conversion WIP, beginning 70 0 52.5 Started and completed 30 30 30 WIP, ending 10 10 5 Totals 110 40 87.5 Cost per Equiv Unit $4,000 $16,000 Work in process, beginning inventory: Current Costs:Direct materials $140,000 Direct materials $ 160,000Conversion costs $260,000 Conversion…arrow_forwardVishnuarrow_forward
- Muskoge Company uses a process-costing system. The company manufactures a product that isprocessed in two departments: Molding and Assembly. In the Molding Department, directmaterials are added at the beginning of the process; in the Assembly Department, additionaldirect materials are added at the end of the process. In both departments, conversion costs areincurred uniformly throughout the process. As work is completed, it is transferred out. Thefollowing table summarizes the production activity and costs for February: Molding AssemblyBeginning inventories: Physical units 10,000 8,000 Costs: Transferred in — $ 45,400 Direct materials $22,000 — Conversion costs $13,800 $ 16,700Current production: Units started 25,000 ? Units transferred out 30,000 35,000 Costs: Transferred in — ? Direct materials $ 56,250 $ 40,250 Conversion costs $103,500 $142,845 Percentage of completion: Beginning inventory 40% 55% Ending inventory 80 50Required:3. Using the FIFO method, prepare the following for…arrow_forwardSound Tek Inc. manufactures electronic stereo equipment. The manufacturing process includes printed circuit (PC) board assembly, final assembly, testing, and shipping. In the PC board assembly operation, a number of individuals are responsible for assembling electronic components into printed circuit boards. Each operator is responsible for soldering components according to a given set of instructions. Operators work on batches of 50 printed circuit boards. Each board requires 4 minutes of board assembly time. After each batch is completed, the operator moves the assembled boards to the final assembly area. This move takes 12 minutes to complete. The final assembly for each stereo unit requires 19 minutes and is also done in batches of 50 units. A batch of 50 stereos is moved into the test building, which is across the street. The move takes 20 minutes. Before conducting the test, the test equipment must be set up for the particular stereo model. The test setup requires 30 minutes. The…arrow_forwardWatertime inc. manufactures old fashioned grandfather clocks. The production utilizes a highly automated assembly line. The firm has identified two cost categories: direct materials and conversion costs. During the production process each clock moves first through the Assembly Department, where materials are added and the clock is assembled, then through the Testing Department, where the clock is inspected for quality control. All direct materials are added at the beginning of the production process but conversion costs are allocated evenly throughout production. Spartans Inc. uses weighted-average costing. Data for Department A for June 2020 are: Beginning WiP Inventory 320 units Direct Materials (100% complete) Conversion (35% complete) Units started during June 750 units Ending WiP Inventory June 30 300 units Direct…arrow_forward
- Devereaux Cycles makes three models of scooter: Commuter, Sport, and X-treme. The scooters are produced in four departments: Assembly, Detailing, Customization, and Packaging. All three models are started in Assembly, where all materials are assembled. The Commuter is then sent to Packaging, where it is packaged and transferred to finished goods inventory. The Sport is then transferred to Detailing. Once the detailing process is completed, the Sport models are transferred to Packaging and then finished goods. The X- Treme model is assembled and then transferred to Customization, and then Packaging. When packaged, it is transferred to finished goods. Data for February are shown in the following table. Conversion costs are allocated based on the number of units processed in each department. No work-in-process inventories are maintained in any department. Materials Conversion costs: Assembly Detailing Customization Packaging Total conversion costs Commuter Sport X-Treme Total $ 3,694,000…arrow_forwardFerdon Watches, Inc., makes four models of watches, Gag-Gift, Commuter, Sport, and Retirement. Ferdon manufactures the watches in four departments: Assembly, Polishing, Special Finishing, and Packaging. All four models are started in Assembly where all material is assembled. The Gag-Gift is transferred to Packaging, where it is packaged and transferred to finished goods inventory. The Commuter and Sport are assembled, then transferred to Polishing. Once the polishing process is completed, they are transferred to Packaging and then finished goods. The Retirement model is assembled and then transferred to Special Finishing, and then Packaging. When packaged, it is transferred to finished goods. Data for October are shown in the following table. Conversion costs are allocated based on the number of units processed in each department. Total Gag-Gift(5,000 units) Commuter(10,000 units) Sport(13,000 units) Retirement(2,000 units) Materials $ 321,000 $ 15,000 $ 90,000…arrow_forwardAlchemy Manufacturing produces a pesticide chemical and uses process costing. There are three processing departments Mixing, Refining, and Packaging. On January 1, the first department-Mixing-had no beginning inventory. During January, 52,000 fl. oz. of chemicals were started in production. Of these, 36,000 fl. oz. were completed and 16,000 fl. oz. remained in process. In the Mixing Department, all direct materials are added at the beginning of the production process, and conversion costs are applied evenly throughout the process. The weighted average method is used. At the end of the month, Alchemy calculated equivalent units of production. The ending inventory in the Mixing Department was 70% complete with respect to conversion costs. With respect to direct materials, what is the number of equivalent units of production in the ending inventory? OA. 16,000 equivalent units B. 36,000 equivalent units OC. 52,000 equivalent units OD. 11,200 equivalent units ***arrow_forward
arrow_back_ios
arrow_forward_ios
Recommended textbooks for you
- AccountingAccountingISBN:9781337272094Author:WARREN, Carl S., Reeve, James M., Duchac, Jonathan E.Publisher:Cengage Learning,Accounting Information SystemsAccountingISBN:9781337619202Author:Hall, James A.Publisher:Cengage Learning,
- Horngren's Cost Accounting: A Managerial Emphasis...AccountingISBN:9780134475585Author:Srikant M. Datar, Madhav V. RajanPublisher:PEARSONIntermediate AccountingAccountingISBN:9781259722660Author:J. David Spiceland, Mark W. Nelson, Wayne M ThomasPublisher:McGraw-Hill EducationFinancial and Managerial AccountingAccountingISBN:9781259726705Author:John J Wild, Ken W. Shaw, Barbara Chiappetta Fundamental Accounting PrinciplesPublisher:McGraw-Hill Education
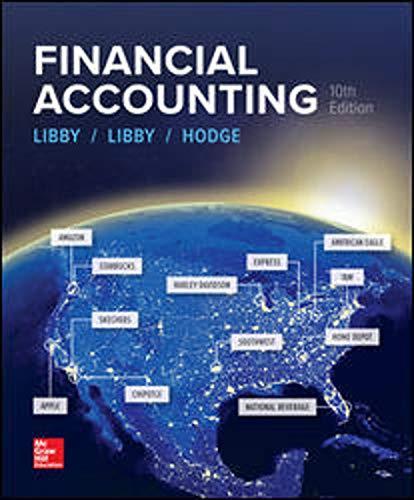
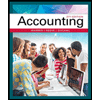
Accounting
Accounting
ISBN:9781337272094
Author:WARREN, Carl S., Reeve, James M., Duchac, Jonathan E.
Publisher:Cengage Learning,
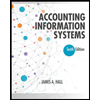
Accounting Information Systems
Accounting
ISBN:9781337619202
Author:Hall, James A.
Publisher:Cengage Learning,
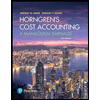
Horngren's Cost Accounting: A Managerial Emphasis...
Accounting
ISBN:9780134475585
Author:Srikant M. Datar, Madhav V. Rajan
Publisher:PEARSON
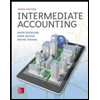
Intermediate Accounting
Accounting
ISBN:9781259722660
Author:J. David Spiceland, Mark W. Nelson, Wayne M Thomas
Publisher:McGraw-Hill Education
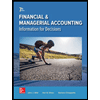
Financial and Managerial Accounting
Accounting
ISBN:9781259726705
Author:John J Wild, Ken W. Shaw, Barbara Chiappetta Fundamental Accounting Principles
Publisher:McGraw-Hill Education