Sandhill has unused productive capacity that is expected to continue indefinitely: management has concluded that some of this capacity could be used to assemble the bikes and sell them at $491 each. Assembling the bikes will increase direct materials by $5 per bike and direct labor by $10 per bike. Additional variable overhead will be incurred at the normal rates, but there will be no additional fixed overhead as a result of assembling the bikes.
Sandhill has unused productive capacity that is expected to continue indefinitely: management has concluded that some of this capacity could be used to assemble the bikes and sell them at $491 each. Assembling the bikes will increase direct materials by $5 per bike and direct labor by $10 per bike. Additional variable overhead will be incurred at the normal rates, but there will be no additional fixed overhead as a result of assembling the bikes.
Chapter1: Financial Statements And Business Decisions
Section: Chapter Questions
Problem 1Q
Related questions
Question

Transcribed Image Text:Sandhill Bikes could sell its bicycles to retailers either assembled or unassembled. The cost of an unassembled bike is as follows.
Direct materials
$147
Direct labor
70
Variable overhead (70% of direct labor)
49
Fixed overhead (30% of direct labor)
21
Manufacturing cost per unit
$287
The unassembled bikes are sold to retailers at $451 each.
Sandhill has unused productive capacity that is expected to continue indefinitely: management has concluded that some of this
capacity could be used to assemble the bikes and sell them at $491 each. Assembling the bikes will increase direct materials by $5 per
bike and direct labor by $10 per bike. Additional variable overhead will be incurred at the normal rates, but there will be no additional
fixed overhead as a result of assembling the bikes.

Transcribed Image Text:Prepare an incremental analysis for the sell-or-process-further decision. (Enter negative amounts using either a negative sign
preceding the number eg -45 or parentheses eg. (45). Do not leave any field blank. Enter O for the amounts.)
Net Income
Process
Increase
Sell
Further
(Decrease)
Total
Sales per unit
Materials
Labor
Variable overhead
Fixed overhead
Costs per unit
%$4
Net income per unit
Should Sandhill sell or process further?
Sandhill Bikes should
%24
Expert Solution

This question has been solved!
Explore an expertly crafted, step-by-step solution for a thorough understanding of key concepts.
This is a popular solution!
Trending now
This is a popular solution!
Step by step
Solved in 3 steps with 2 images

Knowledge Booster
Learn more about
Need a deep-dive on the concept behind this application? Look no further. Learn more about this topic, accounting and related others by exploring similar questions and additional content below.Recommended textbooks for you
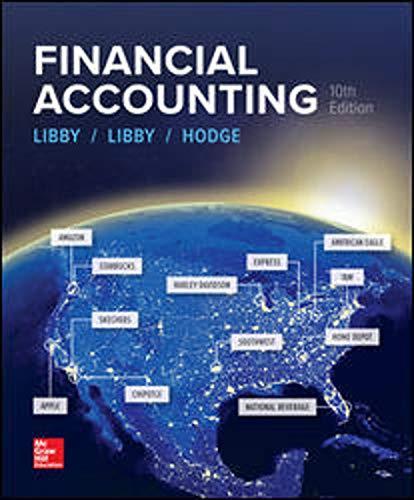
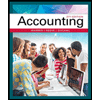
Accounting
Accounting
ISBN:
9781337272094
Author:
WARREN, Carl S., Reeve, James M., Duchac, Jonathan E.
Publisher:
Cengage Learning,
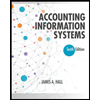
Accounting Information Systems
Accounting
ISBN:
9781337619202
Author:
Hall, James A.
Publisher:
Cengage Learning,
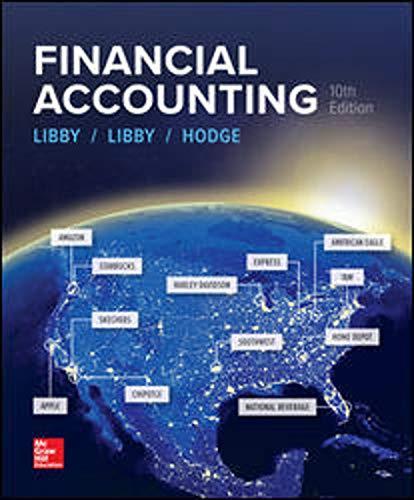
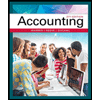
Accounting
Accounting
ISBN:
9781337272094
Author:
WARREN, Carl S., Reeve, James M., Duchac, Jonathan E.
Publisher:
Cengage Learning,
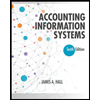
Accounting Information Systems
Accounting
ISBN:
9781337619202
Author:
Hall, James A.
Publisher:
Cengage Learning,
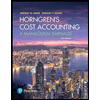
Horngren's Cost Accounting: A Managerial Emphasis…
Accounting
ISBN:
9780134475585
Author:
Srikant M. Datar, Madhav V. Rajan
Publisher:
PEARSON
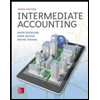
Intermediate Accounting
Accounting
ISBN:
9781259722660
Author:
J. David Spiceland, Mark W. Nelson, Wayne M Thomas
Publisher:
McGraw-Hill Education
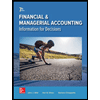
Financial and Managerial Accounting
Accounting
ISBN:
9781259726705
Author:
John J Wild, Ken W. Shaw, Barbara Chiappetta Fundamental Accounting Principles
Publisher:
McGraw-Hill Education