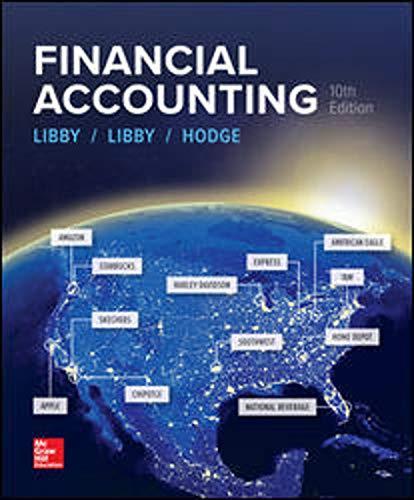
FINANCIAL ACCOUNTING
10th Edition
ISBN: 9781259964947
Author: Libby
Publisher: MCG
expand_more
expand_more
format_list_bulleted
Concept explainers
Topic Video
Question
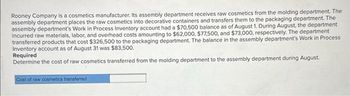
Transcribed Image Text:Rooney Company is a cosmetics manufacturer. Its assembly department receives raw cosmetics from the molding department. The
assembly department places the raw cosmetics into decorative containers and transfers them to the packaging department. The
assembly department's Work in Process Inventory account had a $70,500 balance as of August 1. During August, the department
incurred raw materials, labor, and overhead costs amounting to $62,000, $77,500, and $73,000, respectively. The department
transferred products that cost $326,500 to the packaging department. The balance in the assembly department's Work in Process
Inventory account as of August 31 was $83,500.
Required
Determine the cost of raw cosmetics transferred from the molding department to the assembly department during August.
Cost of raw cosmetics transferred
Expert Solution

This question has been solved!
Explore an expertly crafted, step-by-step solution for a thorough understanding of key concepts.
This is a popular solution
Trending nowThis is a popular solution!
Step by stepSolved in 3 steps with 1 images

Knowledge Booster
Learn more about
Need a deep-dive on the concept behind this application? Look no further. Learn more about this topic, accounting and related others by exploring similar questions and additional content below.Similar questions
- The Assembling Department of Origination Inc. had 10,000 units in process on December 1 and received 30,000 units from the Sewing Department. During the month, it completed 20,000 units and transferred them to the Packaging Department. Calculate the number of units accounted for by the Assembling Department for December. Prepare the production cost report for the Assembling Department for the units for the month of December. Use the FIFO method.arrow_forwardPort Ormond Carpet Company manufactures carpets. Fiber is placed in process in the Spinning Department, where it is spun into yarn. The output of the Spinning Department is transferred to the Tufting Department, where carpet backing is added at the beginning of the process and the process is completed. On January 1, Port Ormond Carpet Company had the following inventories: Finished Goods $6,500 Work in Process-Spinning Department 1,200 Work in Process-Tufting Department 2,300 Materials 4,100 Departmental accounts are maintained for factory overhead, and both have zero balances on January 1. Manufacturing operations for January are summarized as follows: Jan. Materials purchased on account, $84,700 Materials requisitioned for use: Fiber-Spinning Department, $42,800 Carpet backing-Tufting Department, $34,000 Indirect materials-Spinning Department, $3,400 Indirect materials-Tufting Department, $2,700 31 Labor used: Direct labor-Spinning Department, $26,600 Direct labor-Tufting Department,…arrow_forwardPort Ormond Carpet Company manufactures carpets. Fiber is placed in process in the Spinning Department, where it is spun into yarn. The output of the Spinning Department is transferred to the Tufting Department, where carpet backing is added at the beginning of the process and the process is completed. On January 1, Port Ormond Carpet Company had the following inventories: Finished Goods $6,500 Work in Process-Spinning Department 1,200 Work in Process-Tufting Department 2,300 Materials 4,100 Departmental accounts are maintained for factory overhead, and both have zero balances on January 1. Manufacturing operations for January are summarized as follows: Jan. 1 Materials purchased on account, $84,700 2 Materials requisitioned for use: Fiber-Spinning Department, $42,800 Carpet backing-Tufting Department, $34,000 Indirect materials-Spinning Department, $3,400 Indirect materials-Tufting Department, $2,700 31 Labor used:…arrow_forward
- Quality Brick Company produces bricks in two processing departments—Molding and Firing. Information relating to the company’s operations in March follows: Raw materials used in production: Molding Department, $27,600; and Firing Department, $4,500. Direct labor costs incurred: Molding Department, $19,900; and Firing Department, $6,000. Manufacturing overhead was applied: Molding Department, $25,500; and Firing Department, $38,200. Unfired, molded bricks were transferred from the Molding Department to the Firing Department. According to the company’s process costing system, the cost of the unfired, molded bricks was $66,000. Finished bricks were transferred from the Firing Department to the finished goods warehouse. According to the company’s process costing system, the cost of the finished bricks was $107,000. Finished bricks were sold to customers. According to the company’s process costing system, the cost of the finished bricks sold was $105,200. Required: Prepare journal…arrow_forwardGreat Southern Furniture Company (GSFC) produces dining tables in a three-stage process: cutting, assembly and staining. Direct materials (lumber) are added at the beginning of the cutting process, and conversion costs are incurred evenly throughout the process. The Cutting Department of GSFC began June with no work-in-process inventory. During the month work was started on 13,000 metres of lumber. Activity in the Cutting Department included cutting 10,000 metres of lumber, which were transferred to the Assembly Department. Process inspection occurs at the end of the process and normally no losses are expected at this stage. However during the month 1,000 meters of lumber were rejected at inspection and sold as scrap at $75 per meter. The ending work-in-process inventory at June 30 was 70% of the way through the cutting process. Production costs incurred in the Cutting Department during June are summarized as follows: Direct materials…arrow_forwardLogistics Solutions provides order fulfillment services for dot.com merchants. The company maintains warehouses that stock items carried by its dot.com clients. When a client receives an order from a customer, the order is forwarded to Logistics Solutions, which pulls the item from storage, packs it, and ships it to the customer. The company uses a predetermined variable overhead rate based on direct labor-hours. In the most recent month, 180,000 items were shipped to customers using 7.700 direct labor-hours. The company incurred a total of $26,180 in variable overhead costs. According to the company's standards, 0.03 direct labor-hours are required to fulfill an order for one item and the variable overhead rate is $3.45 per direct labor-hour. Required: 1. What is the standard labor-hours allowed (SH) to ship 180,000 items to customers? 2. What is the standard variable overhead cost allowed (SHSR) to ship 180,000 items to customers? 3. What is the variable overhead spending variance?…arrow_forward
- The cost of materials transferred into the Filling Department of Ivy Cosmetics Company is $18,300, including $5,800 from the Blending Department and $12,500 from the materials storeroom. The conversion cost for the period in the Filling Department is $6,620 ($1,320 factory overhead applied and $5,300 direct labor). The total cost transferred to Finished Goods for the period was $23,440. The Filling Department had a beginning inventory of $2,400. Required On June 30, journalize the cost of transferred-in materials.arrow_forwardBayas Corporation uses process costing. A number of transactions that occurred in June are listed below. (1) Raw materials that cost $39,900 are withdrawn from the storeroom for use in the Mixing Department. All of these raw materials are classified as direct materials. (2) Direct labor costs of $16,200 are incurred, but not yet paid, in the Mixing Department. (3) Manufacturing overhead of $45,800 is applied in the Mixing Department using the department's predetermined overhead rate. (4) Units with a carrying cost of $87,700 finish processing in the Mixing Department and are transferred to the Drying Department for further processing. (5) Units with a carrying cost of $111,400 finish processing in the Drying Department, the final step in the production process, and are transferred to the finished goods warehouse. (6) Finished goods with a carrying cost of $98,300 are sold. Required: Prepare journal entries for each of the transactions listed above. (If no entry is required for a…arrow_forwardDomingo Corporation uses the weighted average method in its process costing system. This month, the beginning inventory in the first processing department consisted of 1,700 units. The costs and percentage completion of these units in beginning inventory were: Materials costs Conversion costs Cost $6,800 $3,000 Materials costs Conversion costs A total of 8,100 units were started and 7,400 units were transferred to the second processing department during the month. The following costs were incurred in the first processing department during the month: Percent Complete 50% 20% Cost $160,000 $121,700 The ending inventory was 85% complete with respect to materials and 75% complete with respect to conversion costs. What are the equivalent units for conversion costs for the month in the first processing department?arrow_forward
- Sweeties, Inc., manufactures a sugar product by a continuous process involving three production departments—Refining, Sifting, and Packing. Assume that records indicate that direct materials, direct labor, and applied factory overhead for the first department, Refining, were $371,000, $142,000, and $98,400, respectively. Also, work in process in the Refining Department at the beginning of the period totaled $29,200, and work in process at the end of the period totaled $28,400. Required: a. 1. On September 30, journalize the entry to record the flow of costs into the Refining Department during the period for direct materials.* 2. On September 30, journalize the entry to record the flow of costs into the Refining Department during the period for direct labor.* 3. On September 30, journalize the entry to record the flow of costs into the Refining Department during the period for factory overhead.* b. On September 30, journalize the entry to record the transfer of…arrow_forwardMukhiarrow_forwardBayas Corporation uses process costing. A number of transactions that occurred in June are listed below. (1) Raw materials that cost $40,700 are withdrawn from the storeroom for use in the Mixing Department. All of these raw materials are classified as direct materials. (2) Direct labor costs of $17,000 are incurred, but not yet paid, in the Mixing Department. (3) Manufacturing overhead of $46,600 is applied in the Mixing Department using the department’s predetermined overhead rate. (4) Units with a carrying cost of $88,500 finish processing in the Mixing Department and are transferred to the Drying Department for further processing. (5) Units with a carrying cost of $112,200 finish processing in the Drying Department, the final step in the production process, and are transferred to the finished goods warehouse. (6) Finished goods with a carrying cost of $99,100 are sold. Required: Prepare journal entries for each of the transactions listed above. (If no entry is…arrow_forward
arrow_back_ios
SEE MORE QUESTIONS
arrow_forward_ios
Recommended textbooks for you
- AccountingAccountingISBN:9781337272094Author:WARREN, Carl S., Reeve, James M., Duchac, Jonathan E.Publisher:Cengage Learning,Accounting Information SystemsAccountingISBN:9781337619202Author:Hall, James A.Publisher:Cengage Learning,
- Horngren's Cost Accounting: A Managerial Emphasis...AccountingISBN:9780134475585Author:Srikant M. Datar, Madhav V. RajanPublisher:PEARSONIntermediate AccountingAccountingISBN:9781259722660Author:J. David Spiceland, Mark W. Nelson, Wayne M ThomasPublisher:McGraw-Hill EducationFinancial and Managerial AccountingAccountingISBN:9781259726705Author:John J Wild, Ken W. Shaw, Barbara Chiappetta Fundamental Accounting PrinciplesPublisher:McGraw-Hill Education
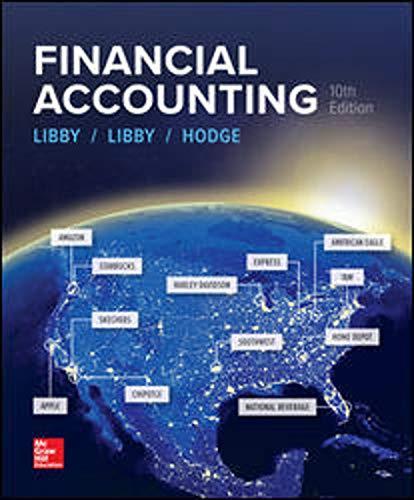
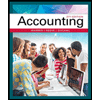
Accounting
Accounting
ISBN:9781337272094
Author:WARREN, Carl S., Reeve, James M., Duchac, Jonathan E.
Publisher:Cengage Learning,
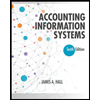
Accounting Information Systems
Accounting
ISBN:9781337619202
Author:Hall, James A.
Publisher:Cengage Learning,
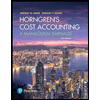
Horngren's Cost Accounting: A Managerial Emphasis...
Accounting
ISBN:9780134475585
Author:Srikant M. Datar, Madhav V. Rajan
Publisher:PEARSON
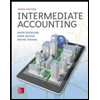
Intermediate Accounting
Accounting
ISBN:9781259722660
Author:J. David Spiceland, Mark W. Nelson, Wayne M Thomas
Publisher:McGraw-Hill Education
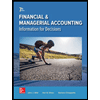
Financial and Managerial Accounting
Accounting
ISBN:9781259726705
Author:John J Wild, Ken W. Shaw, Barbara Chiappetta Fundamental Accounting Principles
Publisher:McGraw-Hill Education