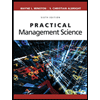
Practical Management Science
6th Edition
ISBN: 9781337406659
Author: WINSTON, Wayne L.
Publisher: Cengage,
expand_more
expand_more
format_list_bulleted
Question
thumb_up100%
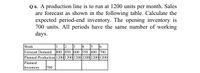
Transcribed Image Text:Q 6. A production line is to run at 1200 units per month. Sales
are forecast as shown in the following table. Calculate the
expected period-end inventory. The opening inventory is
700 units. All periods have the same number of working
days.
Week
Forecast Demand
3
|5 6
1
2
4
800 850 600 550 600 700
Planned Production 1200 1200|1200 1200 1200|1200
Planned
Inventory
700
Expert Solution

This question has been solved!
Explore an expertly crafted, step-by-step solution for a thorough understanding of key concepts.
This is a popular solution
Trending nowThis is a popular solution!
Step by stepSolved in 2 steps

Knowledge Booster
Similar questions
- The president of Hill Enterprises, Terri Hill, projects the firm's aggregate demand requirements over the next 8 months as follows: 2,200 January 1,400 May February 1,600 June 2,200 March April 1,800 1,800 July August 1,800 1,400 Her operations manager is considering a new plan, which begins in January with 200 units of inventory on hand. Stockout cost of lost sales is $100 per unit. Inventory holding cost is $25 per unit per month. Ignore any idle-time costs. The plan is called plan C. Plan C: Keep a stable workforce by maintaining a constant production rate equal to the average gross requirements excluding initial inventory and allow varying inventory levels. Conduct your analysis for January through August.arrow_forwardOQ14arrow_forwardQ2) Eagle Fabrication has the following aggregate demand requirements and other data for the upcoming four quarters. Quarter Demand Previous quarter's output 1500 units 1 1400 Beginning inventory 200 units 2 1000 Stockout cost $50 per unit 3 1500 Inventory holding cost $8 per unit at end of quarter 4 1300 Hiring workers $5 per unit Laying off workers $10 per unit Unit cost $30 per unit Overtime $10 extra per unit Which of the following production plans is better: Plan A—chase demand by hiring and layoffs; or Plan B—produce at a constant rate of 1200 and obtain the remainder from overtime? Finish the calculation. imagearrow_forward
- 2.9 A company wants to develop a level production plan. The beginning inventory is zero. Demand for the next four periods is given in what follows. a. What production rate per period will give a zero inventory at the end of period 4? b. When and in what quantities will back orders occur? c. What level production rate per period will avoid back orders? What will be the end- ing inventory in period 4? Period Forecast Demand Planned Production Planned Inventory 0 1 2 3 4 Total 9 5 9 9arrow_forward1arrow_forwardSheet 9: Q8 Planning model Q8. Use below table to to find the profit of the company, (production plan is 3000) Y slope 2500 2000 5500 65000 7500 95000 Unit price 15.5 Units 3000 Fixed cost 19000 Y(pkp) X(pkp) alope Var cot sotal cost Salearrow_forward
- 7. Nowjuice, Inc., produces Shakewell fruit juice. A planner has developed an aggregate forecast for demand (in cases) for the next six months. Month May Jun Jul Forecast 4,000 4,800 5,600 Aug Sep 7,200 Oct 6,400 5,000 Use the following information to develop aggregate plans. Regular production cost Regular production capacity Overtime production cost Subcontracting cost Holding cost Beginning inventory $10 per case 5,000 cases $16 per case $20 per case $1 per case per month 0 Develop an aggregate plan using each of the following guidelines and compute the total cost for each plan. Which plan has the lowest total cost? a. Use level production. Supplement using overtime as needed. b. Use a combination of overtime (500 cases per period maximum), inventory, and subcontracting (500 cases per period maximum) to handle variations in demand. c. Use overtime up to 750 cases per period and inventory to handle variations in demand.arrow_forwardPP.71 A small manufacturer of specialty welding equipment has developed a combination production plan for the next four quarters, as seen below. Supply/Demand Info Pre-Q1 Q1 4,620 4,620 Forecast (demand) Regular production Subcontract production Ending inventory Hired employees Fired employees Total employees 42 42 Q2 Q3 Q4 4,730 5,390 5,170 5.080 5.060 5.080 330 4 46 The table below shows additional relevant information: Capacity Information & Cost Variables Production rate (units/employee/quarter) Subcontractor capacity (units/quarter) Regular production cost/unit Holding cost'unit/quarter Hiring cost/employee Firing cost/employee Subcontract cost/unit 110 480 $85 $13 $820 $2,150 $119 110 110 46 46 What is the overall total cost for this production plan? (Display your answer to the nearest whole number.) Number What is the total subcontract cost for this production plan? (Display your answer to the nearest whole number.) Number What is the total holding cost for this production plan?…arrow_forward2arrow_forward
- Q7.An example of a leading performance measure is: a. Number of new customers b. Production cycle timearrow_forward3. The MPS planner at Murphy Motors uses MPS time-phased records for planning end-item pro- duction. The planner is currently working on a schedule for the P24, one of Murphy's top-selling motors. The planner uses a production lot size of 70 and a safety stock of 5 for the P24 motor. Week On hand 30 30 30 1 2 3 4 5 6 7 8 40 40 40 45 45 13 8 4 Item: P24 Forecast Orders Projected available balance 20 Available-to-promise MPS a. Complete the MPS time-phased record for product P24. b. Can Murphy accept the following orders? Update the MPS time-phased record for accepted orders. Amount 40 Order Desired Week 1 4 2 6 3 30 2 4 25 3 30 4882 7623arrow_forwardProblem 1 Dr. Song will go to McDonald's for dinner tonight. After studying operations research, he feels that he should at least be "smart" enough to figure out the way he eats it. Let's build a model to determine what to eat at McDonald's. QP AD BM FF MC FR SM 1M OJ Required Cost 3.79 4.49 3.99 3.79 1.29 1.79 1.19 1.00 1.89 Prot 28 24 25 14 31 3 15 1 55 VitA 15 15 6 8 4 10 2 100 VitC 10 2 15 15 4 120 100 Calc 30 20 25 15 15 20 30 2 100 Iron 20 20 20 10 8 15 100 Cals 510 370 500 370 400 220 345 110 80 2000 Carb 34 33 42 38 42 26 27 12 20 350 The tables gives the menu (Quarter Pounder, Angus Deluxe, etc.) along with their unit cost (in $) and amount of nutrients contained (Protain, Vitamin A, etc.) The last column of the table gives the daily required amount of nutrients suggested by Dr. Song's doctor. Suppose Dr. Song aims to minimize the cost of his dinner, while he wants to satisfy all the nutrient requirements. Formulate this problem as a linear programming model, and solve it in…arrow_forward
arrow_back_ios
SEE MORE QUESTIONS
arrow_forward_ios
Recommended textbooks for you
- Practical Management ScienceOperations ManagementISBN:9781337406659Author:WINSTON, Wayne L.Publisher:Cengage,Operations ManagementOperations ManagementISBN:9781259667473Author:William J StevensonPublisher:McGraw-Hill EducationOperations and Supply Chain Management (Mcgraw-hi...Operations ManagementISBN:9781259666100Author:F. Robert Jacobs, Richard B ChasePublisher:McGraw-Hill Education
- Purchasing and Supply Chain ManagementOperations ManagementISBN:9781285869681Author:Robert M. Monczka, Robert B. Handfield, Larry C. Giunipero, James L. PattersonPublisher:Cengage LearningProduction and Operations Analysis, Seventh Editi...Operations ManagementISBN:9781478623069Author:Steven Nahmias, Tava Lennon OlsenPublisher:Waveland Press, Inc.
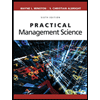
Practical Management Science
Operations Management
ISBN:9781337406659
Author:WINSTON, Wayne L.
Publisher:Cengage,
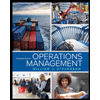
Operations Management
Operations Management
ISBN:9781259667473
Author:William J Stevenson
Publisher:McGraw-Hill Education
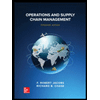
Operations and Supply Chain Management (Mcgraw-hi...
Operations Management
ISBN:9781259666100
Author:F. Robert Jacobs, Richard B Chase
Publisher:McGraw-Hill Education
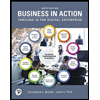
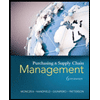
Purchasing and Supply Chain Management
Operations Management
ISBN:9781285869681
Author:Robert M. Monczka, Robert B. Handfield, Larry C. Giunipero, James L. Patterson
Publisher:Cengage Learning
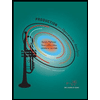
Production and Operations Analysis, Seventh Editi...
Operations Management
ISBN:9781478623069
Author:Steven Nahmias, Tava Lennon Olsen
Publisher:Waveland Press, Inc.