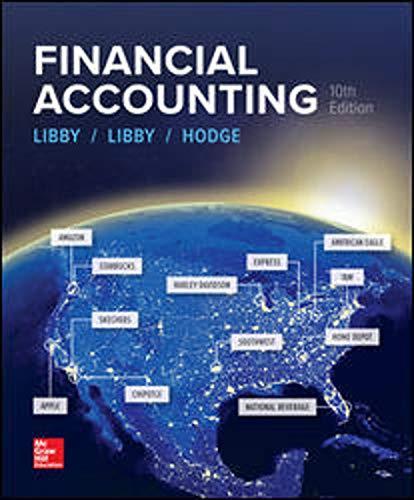
FINANCIAL ACCOUNTING
10th Edition
ISBN: 9781259964947
Author: Libby
Publisher: MCG
expand_more
expand_more
format_list_bulleted
Question
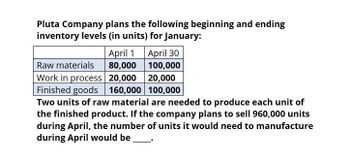
Transcribed Image Text:Pluta Company plans the following beginning and ending
inventory levels (in units) for January:
Raw materials
April 1
April 30
80,000
100,000
Work in process 20,000 20,000
Finished goods
160,000 100,000
Two units of raw material are needed to produce each unit of
the finished product. If the company plans to sell 960,000 units
during April, the number of units it would need to manufacture
during April would be
Expert Solution

This question has been solved!
Explore an expertly crafted, step-by-step solution for a thorough understanding of key concepts.
Step by stepSolved in 2 steps with 2 images

Knowledge Booster
Similar questions
- Wisdom Corporation plans to sell 23,000 units during August. If the company has 8,000 units on hand at the start of the month, and plans to have 9,000 units on hand at the end of the month, how many units must be produced during the month? O 24,000 O 22,000 O 32,000 O 31,000arrow_forwardThe Company manufactures foam cushions. The number of cushions to be produced in the upcoming three months follows: Number of foam cushions to be produced in July 13,000 Number of foam cushions to be produced in August 19,000 Number of foam cushions to be produced in September 12,000 Each cushion requires 2 pounds of the foam used as stuffing. The Company has a policy that the ending inventory of foam each month must be equal to 30% of the following month's expected production needs. How many pounds of foam does the Company need to purchase in August?arrow_forwardPonderosa, Inc., produces wiring harness assemblies used in the production of semi-trailer trucks. The wiring harness assemblies are sold to various truck manufacturers around the world. Projected sales in units for the coming five months are given below. January 10,000 February 10,500 March 13,900 April 16,000 May 18,500 The following data pertain to production policies and manufacturing specifications followed by Ponderosa: Finished goods inventory on January 1 is 900 units. The desired ending inventory for each month is 20 percent of the next month’s sales. The data on materials used are as follows: Direct Material Per-Unit Usage Unit Cost Part #K298 2 $4 Part #C30 3 7 Inventory policy dictates that sufficient materials be on hand at the beginning of the month to satisfy 30 percent of the next month’s production needs. This is exactly the amount of material on hand on January 1. The direct labor used per unit of…arrow_forward
- Lens Junction has required production of 15,400 units in January and 18,100 in February. Each lens consists of 2 pounds of silicon costing $2.50 per pound and 3 ounces of solution costing $3 per ounce. Desired inventory levels are: Jan. Feb. Mar. Beginning Inventory: Finished Goods 4,500 4,900 5,000 DM - Silicon 8,500 9,100 9,200 DM - Solution 11,200 12,000 13,000 PLEASE NOTE: Units are rounded to whole numbers with commas as needed (i.e. 1,234) - no labels. All dollar amounts are rounded to whole dollars and shown with "$" and commas as needed (i.e. $12,345), except for any "per" amounts (units or dollars), which are rounded to two decimal places and shown with "$" and commas as needed (i.e. $1,234.56) - no labels. Cost per Pound Desired Ending Inventory DM per Unit Units to be Produced Pounds Needed for Production Required DM Pounds Beginning Inventory Total Cost of DM Purchase Total DM Required Using the information above, along with the terms…arrow_forwardCrest Products expects the following sales of its single product Units September October November December January Required: Crest has an ending finished goods Inventory policy of 30% of the next month's sales needs. September 1 Inventory is projected to be 7,400 units. Each finished unit requires 2 units of Component X and 3 units of Component Z. August 1 materials Inventory includes 3,000 units of Component X and 159,000 units of Component Z. Crest desires to maintain a Component X Inventory equal to 10% of next month's production needs and a Component Z Inventory equal to 20% of next month's production needs. a. Prepare a production budget for Crest for the quarter ending December 31. 26,800 19,700 16,100 18,700 16,000 Crest Products Production Budget For the Quarter Ending December 31 October November Budgeted unit sales Plus: Ending finished goods inventory Less: Beginning finished goods inventory Budgeted production (units) Budgeted production (units) Direct materials…arrow_forwardFiarrow_forward
- Bodin Company budgets on an annual basis. The following beginning and ending inventory levels (in units) are plannned for the year 20x1. Five units of raw material are required to produce each unit of finished product. Raw material Work in process Finished goods Required: January 1 41,000 December 31 48,000 20,000 20,000 92,000 59,000 1. If Bodin Company plans to sell 452,000 units during the year, compute the number of units the firm would have to manufacture during the year. 2. If 520,000 finished units were to be manufactured by Bodin Company during the year, determine the amount of raw material to be purchased. 1. Required production in units 2. Raw material purchases in unitsarrow_forwardNyanza, Incorporated anticipates sales of 55,000 units, 53,000 units, and 56,000 units in July, August, and September, respectively. Company policy is to maintain an ending finished-goods inventory equal to 30% of the following month's sales. On the basis of this information, how many units would the company plan to produce in July?arrow_forwardPridgeon Corporation plans to sell 23,000 units during August. If the company has 8,000 units on hand at the start of the month, and plans to have 9,000 units on hand at the end of the month, how many units must be produced during the month? O 24,000 O 22,000 O 32,000 O 31,000arrow_forward
- If there were 40000 pounds of direct materials on hand on January 1, 120000 pounds are desired for inventory at January 31, and 560000 pounds are required for January production, how many pounds of direct materials should be purchased in January? a. 480000 pounds b. 680000 pounds c. 440000 pounds d. 640000 poundsarrow_forwardEarrow_forwardGarza Electronics expects to sell 500 units in January, 250 units in February, and 1,000 units in March. January's beginning inventory is 700 units. Expected sales for the whole year are 7,200 units. Garza has decided on a level monthly production schedule of 600 units (7,200 units/12 months = 600 units per month). What is the expected end- of-month inventory for January, February, and March?arrow_forward
arrow_back_ios
SEE MORE QUESTIONS
arrow_forward_ios
Recommended textbooks for you
- AccountingAccountingISBN:9781337272094Author:WARREN, Carl S., Reeve, James M., Duchac, Jonathan E.Publisher:Cengage Learning,Accounting Information SystemsAccountingISBN:9781337619202Author:Hall, James A.Publisher:Cengage Learning,
- Horngren's Cost Accounting: A Managerial Emphasis...AccountingISBN:9780134475585Author:Srikant M. Datar, Madhav V. RajanPublisher:PEARSONIntermediate AccountingAccountingISBN:9781259722660Author:J. David Spiceland, Mark W. Nelson, Wayne M ThomasPublisher:McGraw-Hill EducationFinancial and Managerial AccountingAccountingISBN:9781259726705Author:John J Wild, Ken W. Shaw, Barbara Chiappetta Fundamental Accounting PrinciplesPublisher:McGraw-Hill Education
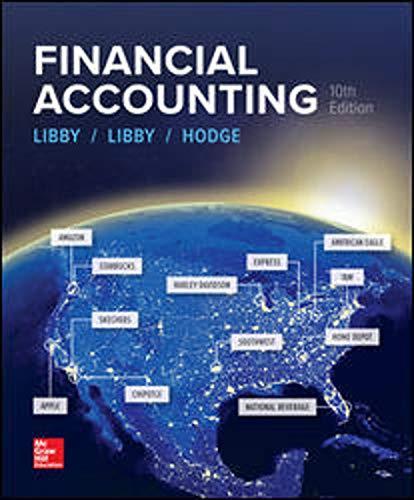
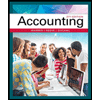
Accounting
Accounting
ISBN:9781337272094
Author:WARREN, Carl S., Reeve, James M., Duchac, Jonathan E.
Publisher:Cengage Learning,
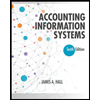
Accounting Information Systems
Accounting
ISBN:9781337619202
Author:Hall, James A.
Publisher:Cengage Learning,
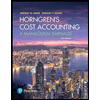
Horngren's Cost Accounting: A Managerial Emphasis...
Accounting
ISBN:9780134475585
Author:Srikant M. Datar, Madhav V. Rajan
Publisher:PEARSON
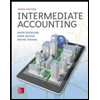
Intermediate Accounting
Accounting
ISBN:9781259722660
Author:J. David Spiceland, Mark W. Nelson, Wayne M Thomas
Publisher:McGraw-Hill Education
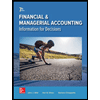
Financial and Managerial Accounting
Accounting
ISBN:9781259726705
Author:John J Wild, Ken W. Shaw, Barbara Chiappetta Fundamental Accounting Principles
Publisher:McGraw-Hill Education