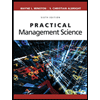
Practical Management Science
6th Edition
ISBN: 9781337406659
Author: WINSTON, Wayne L.
Publisher: Cengage,
expand_more
expand_more
format_list_bulleted
Concept explainers
Topic Video
Question
MRP II stands for:
a) material resource planning.
b) management requirements planning.
c) management resource planning.
d) material revenue planning.
e) material risk planning.
Expert Solution

This question has been solved!
Explore an expertly crafted, step-by-step solution for a thorough understanding of key concepts.
This is a popular solution
Trending nowThis is a popular solution!
Step by stepSolved in 2 steps

Knowledge Booster
Learn more about
Need a deep-dive on the concept behind this application? Look no further. Learn more about this topic, operations-management and related others by exploring similar questions and additional content below.Similar questions
- Assume you are the manager of a shop that assembles power tools. You have just received an order for 55 chain saws, which are to be shipped at the start of week 8. Pertinent information on the saws follows: Item Lead Time (weeks) On Hand Saw A B C D E F 2 1 2 2 1 1 2 Gross requirements Scheduled receipts Projected on hand Net requirements Planned order receipt Planned order release Ĉ E(3) & E(2) LT = 1 week Lot size: Lot-for-Lot 15 10 5 65 20 10 30 Skip Extension Tip: Double click to open in new tab Show Transcribed Text Develop the material requirements plan for component E using lot-for-lot ordering for all items. (Leave no cells blank - be certain to enter "0" wherever required.) Components A(2), B(1), C(4) E(3), D(1) D (2), F(3) E(2), D (2) Beg. Inv. 1 2 3 190 5 210 6arrow_forwardadding personnel, equipment, additional shifts as well as building or using inventory are activities within intermediate-range planning horizon or Short-range planning horizon or long-range planning horizon?arrow_forwardGiven the following MRP matrix: LLC: 0 ITEM: X LOT SIZE: MIN 100 Gross Requirements Gross Scheduled Receipts Projected on Hand Net Requirements Net Planned Order Receipts Planned Order Releases Shown smaller: ITEM: X LOT SIZE: MIN 100 Requirements Scheduled Receipts Projected on Hand Requirements Planned Order Receipts Planned Order Releases Answer: LLC: 0 LT: 2 LT: 2 30 PERIOD 1 2 100 PERIOD 50 1 20 10 100 20 2 30 100 50 100 100 30 3 If the ordering cost is $176 and the carrying cost is $1 per unit per period, what is the total inventory related cost for periods 1 through 7? Give answer to 2 decimal WITHOUT the $ symbol. 50 80 20 20 30 50 50 60 80 80 100 30 10 30 80 30 70 90 10 100 100 7 30 10 4 100 100 50 30 5 60 70 6 80 90 30 10 100 100 7 80 10arrow_forward
- The Alpha Beta Company produces two products; A and B, that are made from components C and D. Given the follow-ing product structures, master scheduling requirements, and inventory information, determine when orders shouldbe released for A, B, C, and D and the size of those orders.arrow_forward1.1 discuss the four benefits of an MRP system in relation to apple benefits: expediting is eliminated outstanding orders are decreased closer relationship with suppliers and other departments are formed the production schedules are based on actual demand and forecast 1.2 discuss how the just in time inventory system could benefit apple explain the benefits first benefits: it reduces lot sizes required in production and purchasing It decreases setup times it reduces lead times it encourages preventative maintenance of the inventory control systemarrow_forwardWhy do companies prefer regid over flexible processarrow_forward
- Id-6c An aggregate plan provides justification for: Select one: a. the budget amount requested b. demand for individual products c. demand for product families d. the demand for the parts of each product and. number of customersarrow_forwardQtyI Standard Labor Hour Raw Material Standard Labor 2 Hours Raw Material INDEPENDENT DEMAND Period 2 3 4 5 Total 6 Product A 1,000 1,000 1,000 1,000 1,000 1,000 6,000 Product B 500 500 500 1,500 15. The standard labor capacity required to support this plan is A. 9,000 hours B. 13,500 hours C. 18,000 hours D. 21,000 hours 16. Products A and B are produced on two different dedicated production lines. If both lines work on the same shift schedule, the ratio of workers on line A to workers on line B is A. 2:1 В. 2:3 С. 2:5 D. 4:1arrow_forwarda. How much should be produced each period? b. What is ending inventory for each period? c. If inventory carrying cost is $3 per case per period based on ending inventory, what is the total cost of carrying inventory? d. What is the total plan cost and why? 4. The opening backlog is 1200 units. Forecast demand is shown below. a. Calculate the weekly production for level production if the backlog is to be reduced to 1000 units, b. Calculate the projected backlog for each week. Week 2 4 3 1200 1200 Forecast 1200 Demand Planned Production Projected Backlog 1200 1100 5 1100 25 20 6 1000 Total 5. A firm plans to make 400 wagons, 200 carts, and 100 sleds. The resource bill shown below displays the amount of critical resources needed to make one average unit of product family: Wood (Board Feet) Labor (Standard Hours) Product Wagon 0.75 0.50 1.00 Cart Sled 30 Calculate the total wood AND labor needed to make the total number of items in the product family.arrow_forward
- (1) What are the three most common core components of 1st generation ERPs? Group of answer choices Accounting and finance Human resources Building and faculty management IT services management Occupational health and safety Production and materials management (2) In information systems, what does ERP actually stand for? Group of answer choices Entity Relationship Programming Enterprise Requirements Planning Enterprise Resource Planning Entity Requirements Planningarrow_forwardAssistance with question five please. Please provide at least 5 referencesarrow_forwardNeed urgent assist with the below.arrow_forward
arrow_back_ios
SEE MORE QUESTIONS
arrow_forward_ios
Recommended textbooks for you
- Practical Management ScienceOperations ManagementISBN:9781337406659Author:WINSTON, Wayne L.Publisher:Cengage,Operations ManagementOperations ManagementISBN:9781259667473Author:William J StevensonPublisher:McGraw-Hill EducationOperations and Supply Chain Management (Mcgraw-hi...Operations ManagementISBN:9781259666100Author:F. Robert Jacobs, Richard B ChasePublisher:McGraw-Hill Education
- Purchasing and Supply Chain ManagementOperations ManagementISBN:9781285869681Author:Robert M. Monczka, Robert B. Handfield, Larry C. Giunipero, James L. PattersonPublisher:Cengage LearningProduction and Operations Analysis, Seventh Editi...Operations ManagementISBN:9781478623069Author:Steven Nahmias, Tava Lennon OlsenPublisher:Waveland Press, Inc.
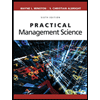
Practical Management Science
Operations Management
ISBN:9781337406659
Author:WINSTON, Wayne L.
Publisher:Cengage,
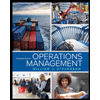
Operations Management
Operations Management
ISBN:9781259667473
Author:William J Stevenson
Publisher:McGraw-Hill Education
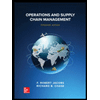
Operations and Supply Chain Management (Mcgraw-hi...
Operations Management
ISBN:9781259666100
Author:F. Robert Jacobs, Richard B Chase
Publisher:McGraw-Hill Education
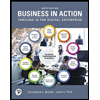
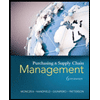
Purchasing and Supply Chain Management
Operations Management
ISBN:9781285869681
Author:Robert M. Monczka, Robert B. Handfield, Larry C. Giunipero, James L. Patterson
Publisher:Cengage Learning
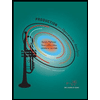
Production and Operations Analysis, Seventh Editi...
Operations Management
ISBN:9781478623069
Author:Steven Nahmias, Tava Lennon Olsen
Publisher:Waveland Press, Inc.