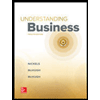
Understanding Business
12th Edition
ISBN: 9781259929434
Author: William Nickels
Publisher: McGraw-Hill Education
expand_more
expand_more
format_list_bulleted
Concept explainers
Question
Discuss on the various costs associated with aggregate planning..
Expert Solution

This question has been solved!
Explore an expertly crafted, step-by-step solution for a thorough understanding of key concepts.
This is a popular solution
Trending nowThis is a popular solution!
Step by stepSolved in 4 steps

Knowledge Booster
Learn more about
Need a deep-dive on the concept behind this application? Look no further. Learn more about this topic, management and related others by exploring similar questions and additional content below.Similar questions
- discuss.. what are the key inputs to aggregate planning?arrow_forward22 es The table below provides Big Lake Bob's production possibilities schedule, which describes various combinations of fishing lures and duck decoys he can carve efficiently in a week. Big Lake Bob's Production Possibilities Schedule Fishing Lures Duck Decoys 100 80 6 60 12 40 18 20 0 24 30 a. Graph Big Lake Bob's production possibilities frontier using the information in the table above. Instructions: Use the tool provided "PPF" to plot the production possibilities frontier point by point (6 points total). Big Lake Bob's Production Possibilities Frontier S 36 30 24 Tools PPFarrow_forwardForecast Data is given within problem. Cost Data is attached Southeast Soda Pop, Inc., has a new fruit drink for which it has high hopes. John Mittenthal, the production planner, has assembled the following cost data and demand forecast: LOADING... Click the icon to view the demand forecast. LOADING... Click the icon to view the cost data. John's job is to develop an aggregate plan. The three initial options he wants to evaluate are: • Plan A: a strategy that hires and fires personnel as necessary to meet the forecast. • Plan B: a level strategy. • Plan C: a level strategy that produces 1,000 cases per quarter and meets the forecast demand with inventory and subcontracting. Part 2 a) Which strategy is the lowest-cost plan? Try hiring and layoffs (to meet the forecast) as necessary (enter your responses as whole numbers). Hiring and Layoff Plan Quarter Forecast Production Hire (Units) Layoff (Units)…arrow_forward
- b) What are the components of service package! S. Prepare an aggregate plan for the following information of demand forecast as given in the table below. Period 1 Demand (units) 55 2 49 Regular Production Cost Overtime production Cost Regular Production capacity 3 60 4 57 5 45 : Rs 60 per unit : Rs 80 per unit : 50 units per period : Rs 5 per unit per period Inventory cost Overtime Production capacity: 10 Units per period : Rs 150 per unit : Unlimited : Nil 6 60 7 8 50 65 9 55 Subcontracting cost Subcontracting capacity Beginning Inventory Use regular production and supplement using inventory, overtime and subcontracting.arrow_forwardDwayne Cole, owner of a F lorida firm that ma nufacturesdisplay cabinets, develops an 8-month aggregate plan.Demand and capacity (in units) a re fo recast as follows: The cost of producing each unit is $1,000 on regular time, $ 1,300 onovertime, and $1,800 on a subcontract. Inventory carrying cost is$200 per unit per month. There is no beginning or ending inventory )in stock, and no backorders are permitted from period to period. ~Let the production (workforce) vary by using regular timefirst, then overtime, and then subcontracting.a) Set up a production plan that minimizes cost by producingexactly what the demand is each month. This plan allows nobackorders or inventory. What is this plan's cost?b) Through better p lanning, regular-time production can be setat exactly the same amount, 275 units, per month. If demandcannot be met there is no cost assigned to shortages and theywill not be filled. Does this a lter…arrow_forwardThe S&OP team at Kansas Furniture, led by David Angelow, has received estimates of demand requirements as shown in the table. Assuming one-time stockout costs for lost sales of $125 per unit, Kinventory carrying costs of $25 per unit per month, and zero beginning and ending inventory, evaluate the following plan on an incremental cost basis: Plan B: Vary the workforce to produce the prior month's demand. Demand was 1,300 units in June. The cost of hiring additional workers is $30 per unit produced. The cost of layoffs is $65 per unit cut back. (Enter all responses as whole numbers.) Note: Both hiring and layoff costs are incurred in the month of the change (i.e., going from production of 1,300 in July to 1200 in August requires a layoff (and related costs) of 100 units in August). Stockouts (Units) Month 1 July Demand 1200 Hire Production (Units) Layoff Ending (Units) Inventory 2 August 1300 3 September 1200 4 October 1700 5 November 1650 6 December 1650arrow_forward
- Solve all this question compulsory........arrow_forwardcpmpute for 4 quarters plsarrow_forwardJAYB, manager of a Fabrication company, has the following aggregate demand requirements and other data for the upcoming four quarters. Table 5: Forecast and cost information [Jadual 5: Maklumat Ramalan dan kos] Quarter [Suku] Demand [Permintaan] Previous quarter's output [Keluaran suku sebelumnya] 1,500 units 1 1,400 Beginning inventory [Inventori awal] 200 units 2 1,000 Hiring workers [Pengambilan pekerja] RM6 per unit 3 1,500 Laying off workers [Pembuangan pekerja] RM11 per unit 4 1,300 Unit cost [Kos unit] RM30 per unit With the information given, JAYB wants you to calculate the total cost of using chase strategy by hiring and layoff workers.arrow_forward
arrow_back_ios
SEE MORE QUESTIONS
arrow_forward_ios
Recommended textbooks for you
- Understanding BusinessManagementISBN:9781259929434Author:William NickelsPublisher:McGraw-Hill EducationManagement (14th Edition)ManagementISBN:9780134527604Author:Stephen P. Robbins, Mary A. CoulterPublisher:PEARSONSpreadsheet Modeling & Decision Analysis: A Pract...ManagementISBN:9781305947412Author:Cliff RagsdalePublisher:Cengage Learning
- Management Information Systems: Managing The Digi...ManagementISBN:9780135191798Author:Kenneth C. Laudon, Jane P. LaudonPublisher:PEARSONBusiness Essentials (12th Edition) (What's New in...ManagementISBN:9780134728391Author:Ronald J. Ebert, Ricky W. GriffinPublisher:PEARSONFundamentals of Management (10th Edition)ManagementISBN:9780134237473Author:Stephen P. Robbins, Mary A. Coulter, David A. De CenzoPublisher:PEARSON
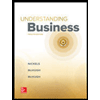
Understanding Business
Management
ISBN:9781259929434
Author:William Nickels
Publisher:McGraw-Hill Education
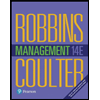
Management (14th Edition)
Management
ISBN:9780134527604
Author:Stephen P. Robbins, Mary A. Coulter
Publisher:PEARSON
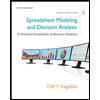
Spreadsheet Modeling & Decision Analysis: A Pract...
Management
ISBN:9781305947412
Author:Cliff Ragsdale
Publisher:Cengage Learning
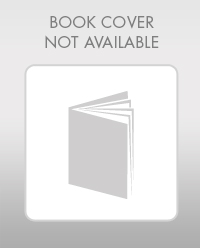
Management Information Systems: Managing The Digi...
Management
ISBN:9780135191798
Author:Kenneth C. Laudon, Jane P. Laudon
Publisher:PEARSON
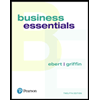
Business Essentials (12th Edition) (What's New in...
Management
ISBN:9780134728391
Author:Ronald J. Ebert, Ricky W. Griffin
Publisher:PEARSON
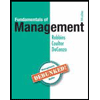
Fundamentals of Management (10th Edition)
Management
ISBN:9780134237473
Author:Stephen P. Robbins, Mary A. Coulter, David A. De Cenzo
Publisher:PEARSON