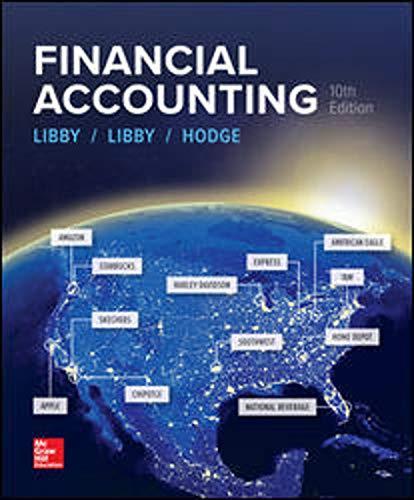
Lansing Electronics Inc. manufactures a variety of printers, scanners, and fax machines in its
two divisions: the PSF Division and the Components Division. The Components Division produces electronic components that can be used by the PSF Division. All the components this
division produces can be sold to outside customers. However, from the beginning, nearly all
of its output has been used internally. The current policy requires that all internal transfers of
components be transferred at full cost.
Recently, Cam DeVonn, the chief executive officer of Lansing Electronics, decided to investigate the transfer pricing policy. He was concerned that the current method of pricing internal
transfers might force decisions by divisional managers that would be suboptimal for the firm. As
part of his inquiry, he gathered some information concerning Component Y34, which is used
by the PSF Division in its production of a basic scanner, Model SC67.
The PSF Division sells 40,000 units of Model SC67 each year at a unit price of $42. Given
current market conditions, this is the maximum price that the division can charge for Model
SC67. The cost of manufacturing the scanner follows:
Component Y34 $ 6.50
Direct materials 12.50
Direct labor 3.00
Variable
Fixed overhead 15.00
Total unit cost $38.00
The scanner is produced efficiently, and no further reduction in
possible.
The manager of the Components Division indicated that she could sell 40,000 units (the
division’s capacity for this part) of Component Y34 to outside buyers at $12 per unit. The PSF
Division could also buy the part for $12 from external suppliers. She supplied the following
details on the manufacturing cost of the component:
Direct materials $2.50
Direct labor 0.50
Variable overhead 1.00
Fixed overhead 2.50
Total unit cost $6.50
Required:
1. Compute the firmwide contribution margin associated with Component Y34 and Model
SC67. Also, compute the contribution margin earned by each division.
2. Suppose that Cam DeVonn abolishes the current transfer pricing policy and gives
divisions autonomy in setting transfer prices. Can you predict what transfer price the
manager of the Components Division will set? What should be the minimum transfer
price for this part? The maximum transfer price?
3. CONCEPTUAL CONNECTION Given the new transfer pricing policy, predict how this
will affect the production decision of the PSF Division manager for Model SC67. How
many units of Component Y34 will the manager of the PSF Division purchase, either
internally or externally?
4. Given the new transfer price set by the Components Division and your answer to
Requirement 3, how many units of Y34 will be sold externally?
5. CONCEPTUAL CONNECTION Given your answers to Requirements 3 and 4, compute
the firmwide contribution margin. What has happened? Was Cam’s decision to grant
additional decentralization good or bad?

Trending nowThis is a popular solution!
Step by stepSolved in 4 steps

- Shady Fabrication Group (SFG) manufactures components for manufacturing equipment at several facilities. The company produces two, related, parts at its Park River Plant, the models SF-08 and SF-48. The differences in the models are the quality of the materials and the precision to which they are produced. The SF-48 model is used in applications where the precision is critical and thus requires greater oversight in the production process. Although sales remain reasonably strong, managers at SFG have noticed that the company is meeting more resistance to the pricing for SF-08, although there seems to be little need for negotiation on the price of the SF-48 model. As a result, the marketing manager at SFG has asked the financial staff to review the costs of the two products to understand better what might be happening in the market. Manufacturing overhead is currently assigned to products based on their direct labor costs. For the most recent month manufacturing overhead was $201,600.…arrow_forwardArmada Shipping is a global logistics company. The company is organized into two divisions: Contracts and Retail. The Contracts Division, which is by far the larger division, handles customers who have regular shipping requirements and have signed contracts specifying costs and schedule for up to one year. The Retail Division handles shipments for customers who have only occasional shipping requirements and pay on an as-used basis. Billing for all customers is handled by the corporate Accounts Receivable Department. Accounts Receivable performs two major activities: billing and accounts. Billing refers to preparing and sending the bills as well as processing the payments. Accounts refers to establishing accounts, ensuring credit status, following up on collection, and so on. The costs of the Accounts Receivable Department are allocated to the two divisions based on the number of bills prepared. The manager of the Contracts Division has complained that the allocated costs from Accounts…arrow_forwardAnswer the given question with a proper explanation and step-by-step solution. Please help me find an answer.arrow_forward
- Utica Manufacturing (UM) was recently acquired by MegaMachines, Inc. (MM). and organized as a separate division within the company. Most manufacturing plants at MM use an ABC system, but UM has always used a traditional product costing system. Bob Miller, the plant controller at UM, has decided to experiment with ABC and has asked you to help develop a simple ABC system that would help him decide if it was useful. The controller's staff has identified costs for the first month in the four overhead cost pools along with appropriate cost drivers for each pool. Activity Drivers Direct material cost Costs 154, 000 1,600, 900 900, 000 450, 000 Cost Pools Incoming inspection Production Machine-hours Machine setup Shipping Setups Units shipped The company manufactures two basic products with model numbers 308 and 510. The following are data for production for the first month as part of MM. Products 308 510 $ 45,000 $173,800 50,000 $ 32,000 $283,809 118,800 Total direct material costs Total…arrow_forwardCarol Components operates a Production Division and a Packaging Division. Both divisions are evaluated as profit centers. Packaging buys components from Production and assembles them for sale. Production sells many components to third parties in addition to Packaging. Selected data from the two operations follow: Capacity (units) Sales price Variable costsb Fixed costs a For Production, this is the price to third parties. b For Packaging, this does not include the transfer price paid to Production. Suppose Production is located in Country A with a tax rate of 30 percent and Distribution in Country B with a tax rate of 10 percent. All other facts remain the same. a. Optimal transfer price b. Transfer price c Transfer price Required: a. Current output in Production is 25,300 units. Packaging requests an additional 5,960 units to produce a special order. What transfer price would you recommend? to search b. Suppose Production is operating at full capacity. What transfer price would you…arrow_forwardStark and Company is a manufacturer that sells robots predominantly in the Asian market. Times have been tough for the auto industry and Stark and Company is no different. The company is under tremendous pressure to turn a profit. Several years ago, as analysts were predicting a large downturn in the robot industry, Stark decided to purchase a smaller niche robot maker in the hopes of capturing a different segment of the consumer market and to better learn the manufacturing processes of other robot makers. Starks still operates as two separate divisions, Classic and New Age, with each division manager employing a different manufacturing philosophy. The Classic manager is concerned with low input costs and quantity in production in addition to brand recognition and robot power. The New Age manager is concerned with quality and innovation in manufacturing, fuel-efficient and environmentally friendly robots. SAC continued to suffer losses even with the addition of the New Age division.…arrow_forward
- Hall, Incorporated manufactures two components, Standard and Ultra, that are designed for the same function, but are made of different metals for operational performance reasons. The metal used in Standard is easy to work with and there are few quality issues or reworking required on the machines. The metal used in Ultra is more difficult to work with and often needs additional machine time and rework. Data on expected operations and direct costs for the next fiscal year follow: Account Administration Engineering Machine operation and maintenance Standard Miscellaneous Supervision Total 48,000 144,000 24,000 Ultral $ 3,384,000 2,520,000 Units produced Direct labor-hours used Machine-hours used Direct materials costs $5,163,000 Direct labor costs 855,000 The planning process team at Hall, Incorporated has estimated the following manufacturing overhead costs for the next fiscal year: 16,500 22,500 22,500 Total Amount $ 825,400 5,699,500 875,000 540,100 884,500 $8,824,500. 64,500 166,500…arrow_forwardim.arrow_forwardCHS is a large multidivision firm. One division, Health Services, is well known Inside CHS for its efficient Information technology (IT). A smaller division, Optics, has approached Health Services with a proposal that it provide IT support in the form of machine time for some of Optics's billing and administrative work. After an analysis of the demands that Optics would place on the system, the IT manager of Health Services notes that Health Services would have to lease a new server because of the additional load. The lease rates for the current server are a fixed annual lease of $3,280 and it averages machine time of 2,900 hours annually. The new server leases for an annual rate of $5,040. Because the new server is a faster machine, Health Services can complete its current requirements In only 2,040 hours. The work for Optics is estimated to be 1,110 hours. In addition to leasing a new server, there are two other changes Health Services would have to make in IT. First, it will have to…arrow_forward
- Culver Company manufactures equipment. Culver’s products range from simple automated machinery to complex systems containing numerous components. Unit selling prices range from $200,000 to $1,500,000 and are quoted inclusive of installation. The installation process does not involve changes to the features of the equipment and does not require proprietary information about the equipment in order for the installed equipment to perform to specifications. Culver has the following arrangement with Winkerbean Inc. ● Winkerbean purchases equipment from Culver for a price of $1,040,000 and contracts with Culver to install the equipment. Culver charges the same price for the equipment irrespective of whether it does the installation or not. The cost of the equipment is $581,000. ● Winkerbean is obligated to pay Culver the $1,040,000 upon the delivery and installation of the equipment. Culver delivers the equipment on June 1, 2020, and completes the installation of the equipment…arrow_forwardCalculating Transfer PriceBurt Inc. has a number of divisions, including the Indian Division, a producer of liquid pumps,and Maple Division, a manufacturer of boat engines.Indian Division produces the h20-model pump that can be used by Maple Division in theproduction of motors that regulate the raising and lowering of the boat engine’s stern drive unit.The market price of the h20-model is $720, and the full cost of the h20-model is $540.Required:1. If Burt has a transfer pricing policy that requires transfer at full cost, what will the transferprice be? Do you suppose that Indian and Maple divisions will choose to transfer at thatprice? 2. If Burt has a transfer pricing policy that requires transfer at market price, what wouldthe transfer price be? Do you suppose that Indian and Maple divisions would choose totransfer at that price?3. Now suppose that Burt allows negotiated transfer pricing and that Indian Divisioncan avoid $120 of selling expense by selling to Maple Division. Which…arrow_forwardDomesticarrow_forward
- AccountingAccountingISBN:9781337272094Author:WARREN, Carl S., Reeve, James M., Duchac, Jonathan E.Publisher:Cengage Learning,Accounting Information SystemsAccountingISBN:9781337619202Author:Hall, James A.Publisher:Cengage Learning,
- Horngren's Cost Accounting: A Managerial Emphasis...AccountingISBN:9780134475585Author:Srikant M. Datar, Madhav V. RajanPublisher:PEARSONIntermediate AccountingAccountingISBN:9781259722660Author:J. David Spiceland, Mark W. Nelson, Wayne M ThomasPublisher:McGraw-Hill EducationFinancial and Managerial AccountingAccountingISBN:9781259726705Author:John J Wild, Ken W. Shaw, Barbara Chiappetta Fundamental Accounting PrinciplesPublisher:McGraw-Hill Education
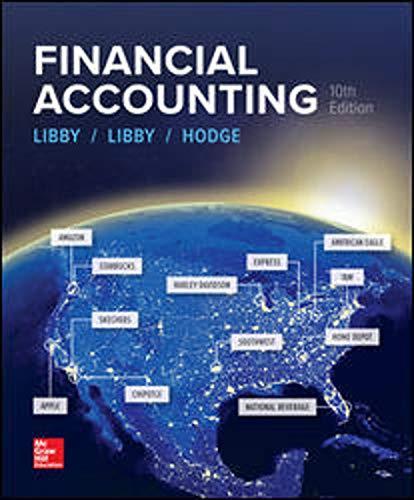
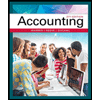
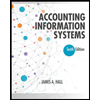
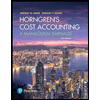
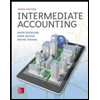
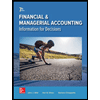