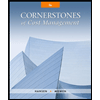
Cornerstones of Cost Management (Cornerstones Series)
4th Edition
ISBN: 9781305970663
Author: Don R. Hansen, Maryanne M. Mowen
Publisher: Cengage Learning
expand_more
expand_more
format_list_bulleted
Question
Labor cost for set-up is $500/hour. The plant plans on level material use and operates 50 days per year to satisfy an annual demand of 5000 units. Dailty production is projected to be 1000 units and lot size is 700. Annual holding cost per unit is projected to be $25. Calculate the time it takes to setup.
Expert Solution

This question has been solved!
Explore an expertly crafted, step-by-step solution for a thorough understanding of key concepts.
Step by stepSolved in 2 steps with 4 images

Knowledge Booster
Similar questions
- A rotational molding operation has fixed costs of $6.000 per year and variable costs of $54 per unit. If the process is automated via conveyor, its fixed cost will be $39,000 per year, but its variable cost will be only $10 per unit. Determine the number of units each year necessary for the two operations to break even. The number of units each year necessary for the two operations to break even is determined to bearrow_forwardA rotational molding operation has fixed costs of $10,000 per year and variable costs of $52 per unit. If the process is automated via conveyor, its fixed cost will be $43,000 per year, but its variable cost will be only $10 per unit. Determine the number of units each year necessary for the two operations to break even. The number of units each year necessary for the two operations to break even, (in units) Round to the nearest two (2) decimal placesarrow_forwardA manual assembly line is being designed for a product with annual demand = 100,000 units. The line will operate 50 wks/year, 5 shifts/wk, and 7.5 hr/shift. Work units will be attached to a continuously moving conveyor. Work content time = 42.0 min. Assume line efficiency E = 0.97, balancing efficiency Eb = 0.92, and repositioning time Tr = 6 sec. Determine: (a) hourly production rate to meet demand, (b) number of workers required.arrow_forward
- Please show workarrow_forwardA company’s demand for a given component for the next 10 years is expected to be 1800/year. They have two options to have the component available for their production requirements, buying (option A) or making the component (option B). Details of the two options are given below: Option A : Three machines X,Y, and Z are needed to produce the component with initial costs of $100,000, $120,000, and $140,000 respectively. Salvage values for X,Y, and Z are $20,000, $30,000, and $40,000. Since the production process will continue for 10 years, an additional unit of any machine will be available for the same price (initial cost) , when needed, and will have the same salvage value at the end of its useful life. Useful lives are 10,5,10 years for machines X,Y, and Z respectively. A total production costs per year is estimated to be $80,000/year. Option B: Buying the component for $100 and saving an amount of $50000/year from utilizing the saved space for different purposes. Use i= 10% to…arrow_forwardUse the following for the next 2 questions: A facility is to be built with construction costs of $50 per square foot amortized over 20 years. Receiving and put-away costs are expected to be $0.02 per box and pick-pack-ship costs are expected to be $0.10 per box. The facility will have an annual upkeep and maintenance cost of $5 per square foot. 1. If the company constructs a 100,000 square foot facility, what is the monthly fixed cost? - $102.500 - $62,500 - $92,500 - $112,500 - $82,500 - $52,500 - $72,500 2. If demand in April is 30,000 boxes, what is the variable cost in April? (assume the number of boxes received in April equals the number of boxes shipped in April) - $3,000 - $1,200 - $3,600 - $2,400 - $600 - $4,200arrow_forward
- The Fence Company is setting up a new production line to produce top rails. The relevant data for two alternatives are shown below. Solve, a. Based on MARR of 8%, determine the annual rate of production for which the alternatives are equally economical. b. If it is estimated that production will be 300 top rails per year, which alternative is preferred and what will be the total annual cost?arrow_forwardthe process for producing a fruit-tree pesticide has a first cost of $200,000 with annual costs of $50,000 and revenue of $90,000 per year. What is the payback period in years?arrow_forwardPlease show workarrow_forward
- Please show workarrow_forwardYour IT company is working on a four-month project for a local mining company. The total planned value of the project (BAC) is $600,000. You are at the end of month three. By the end of month three you scheduled to spend $500,000(PV). The actual cost through this three-month mark is $450,000 (AC). The total work completed at the end of month three is 94 percent. Calculate the earned value, EV=arrow_forwardAria Acoustics, Incorporated (AA), projects unit sales for a new 7-octave voice emulation implant as follows: Year Unit Sales 1 2 3 4 5 74,400 79,800 85,400 82,700 69,500 Production of the implants will require $1,480,000 in net working capital to start and additional net working capital investments each year equal to 15 percent of the projected sales increase for the following year. Total fixed costs are $3,800,000 per year, variable production costs are $143 per unit, and the units are priced at $325 each. The equipment needed to begin production has an installed cost of $18,500,000. Because the implants are intended for professional singers, this equipment is considered industrial machinery and thus qualifies as 7-year MACRS property. In five years, this equipment can be sold for about 20 percent of its acquisition cost. The tax rate is 23 percent and the required return is 17 percent. (MACRS schedule) a. NPV b. IRR a. What is the NPV of the project? (Do not round intermediate…arrow_forward
arrow_back_ios
SEE MORE QUESTIONS
arrow_forward_ios
Recommended textbooks for you
- Cornerstones of Cost Management (Cornerstones Ser...AccountingISBN:9781305970663Author:Don R. Hansen, Maryanne M. MowenPublisher:Cengage LearningEssentials of Business Analytics (MindTap Course ...StatisticsISBN:9781305627734Author:Jeffrey D. Camm, James J. Cochran, Michael J. Fry, Jeffrey W. Ohlmann, David R. AndersonPublisher:Cengage Learning
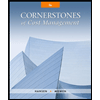
Cornerstones of Cost Management (Cornerstones Ser...
Accounting
ISBN:9781305970663
Author:Don R. Hansen, Maryanne M. Mowen
Publisher:Cengage Learning
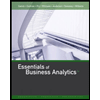
Essentials of Business Analytics (MindTap Course ...
Statistics
ISBN:9781305627734
Author:Jeffrey D. Camm, James J. Cochran, Michael J. Fry, Jeffrey W. Ohlmann, David R. Anderson
Publisher:Cengage Learning