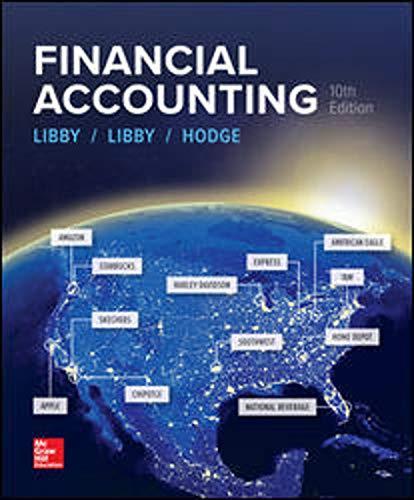
Concept explainers
Joint-cost allocation. SW Flour Company buys 1 input of standard flour and refines it using a special sifting process to 3 cups of baking flour and 9 cups of bread flour. In May 2017, SW bought 12,000 inputs of flour for $89,000. SW spent another $47,800 on the special sifting process. The baking flour can be sold for $3.60 per cup and the bread flour for $4.80 per cup. SW puts the baking flour through a second process so it is super fine. This costs an additional $1.00 per cup of baking flour and the process yields ½ cup of super-fine baking flour for every one cup of baking flour used. The super-fine baking flour sells for $9.60 per cup.
SW Flour Company has decided that their bread flour may sell better if it was marketed for gourmet baking and sold with infused spices. This would involve additional cost for the spices of $0.80 per cup. Each cup could be sold for $5.50.
Q.If SW uses the physical-measure method, what combination of products should SW sell to maximize profits?

Trending nowThis is a popular solution!
Step by stepSolved in 3 steps with 9 images

- In a joint processing operation, Scarecrow Gardens Ltd. manufactures three varieties of products from a common input, corn. Joint processing costs up to the split-off point total $90,000 per year. The company allocates these costs to the joint products on the basis of their total sales value at the split-off point. These sales values are as follows: whole corn $57,000; dried corn kernels $65,000; and ground corn meal $74,500. Each product may be sold at the split-off point or processed further. Additional processing requires no special facilities. The additional processing costs and the sales value after further processing for each product (on an annual basis) are shown below: Product Additional Processing Costs Sales Value Whole Corn $27,175 $95,250 Dried Corn Kernels $29,760 $104,470 Ground Corn Meal $20,400 $92,300 REQUIRED: Which product or products should be sold at the split-off point, and which product or products should be processedfurther. Explain why…arrow_forwardPlease answer in text form without imagearrow_forwardTulsa Milling buys oats at $0.60 per pound and produces TPM Oat Flour, TPM Oat Flakes, and TPM Oat Bran. The process of separating the oats into oat flour and oat bran costs $0.30 per pound. The oat flour can be sold for $1.50 per pound, the oat bran for $2.00 per pound. Each pound of oats has 0.2 pounds of oat bran and 0.8 pounds of oat flour. A pound of oat flour can be made into oat flakes for a fixed cost of $240,000 plus a variable cost of $0.60 per pound. Tulsa Milling plans to process 1 million pounds of oats in 20X0, at a purchase price of $600,000. Requirements 1. Allocate all the joint costs to oat flour and oat bran using the physical-units method. 2. Allocate all the joint costs to oat flour and oat bran using the relative-sales-value method. 3. Suppose there were no market for oat flour. Instead, it must be made into oat flakes to be sold. Oat flakes sell for $2.90 per pound. Allocate the joint cost to oat bran and oat flakes using the relative-sales-value method.…arrow_forward
- Y Company produces two joint products: Sweet and Sour. Joint cost is allocated using the net realizable value method at split-off point. Joint production cost is $70,000. Neither product is salable at split-off point. During May, the additional costs incurred beyond split-off point are as follows: Sweet $ 32,000 Sour $ 48,000 Production: Sweet: 3,200 units Sour: 1,600 units Selling prices: Sweet: $50.00 per unit Sour: $ 90.00 per unit What is the amount of joint cost allocated to Sweet and Sour using the NRV Method at split-off point. (Must show calculations or no credit) Joint cost allocated to Sweet: $_____________________________ Joint cost allocated to Sour:…arrow_forwardLally, Inc. produces universal remote controls. Lally uses a JIT costing system. One of the company's products has a standard direct materials cost of $9 per unit and a standard conversion cost of $35 per unit. During January 2018, Lally produced 500 units and sold 495 units on account at $45 each. It purchased $4,800 of direct materials on the account and incurred actual conversion costs totaling $14,000. Requiremets : 1. Prepare summary jounal entries for January. 2. The January 1, 2018, balance of the Raw and In-Process inventory account was $70. Use a T - account to find the January 31 balance. 3. Use a T - account to determine wheither conversion costs are overallocated or unerallocated for the month. By how much? Prepare the journal entry to adjust the Conversion Costs account.arrow_forwardDinesharrow_forward
- Tucariz Company processes Duo into two joint products, Big and Mini. Duo is purchase in 1,000-gallon drums for $2,000. Processing costs are $3,000 to process the 1,000 gallons of Duo into 800 gallons of Big and 200 gallons of Mini. The selling price is $9 per gallon for Big and $4 per gallon for Mini. If the sales value at split-off method is used to allocate joint costs to the final products, the per-gallon cost (rounded to the nearest cent) of producing Big is Select one: a. $5.00 per gallon. b. $5.63 per gallon. c. $4.50 per gallon. X d. $3.38 per gallon.arrow_forwardChoi Company manufactures two skin care lotions, Smooth Skin and Silken Skin, from a joint process. The joint costs incurred are $360,000 for a standard production run that generates 170,000 pints of Smooth Skin and 300,000 pints of Silken Skin. Smooth Skin sells for $3.20 per pint, while Silken Skin sells for $5.20 per pint. Required: 1. Assuming that both products are sold at the split-off point, how much of the joint cost of each production run is allocated to Smooth Skin using the relative sales value method? 2. If no separable costs are incurred after the split-off point, how much of the joint cost of each production run is allocated to Silken Skin using the physical measure method? 3. If separable processing costs beyond the split-off point are $1.80 per pint for Smooth Skin and $1.70 per pint for Silken Skin, how much of the joint cost of each production run is allocated to Silken Skin using a net realizable value method? 4. If separable processing costs beyond the split-off…arrow_forwardPT Y manufactures three products using the same production process. The costs incurred up to the split-off point are $200,000. The company decided to further process the three products before they were sold. The number of units produced (based on regular sales), the selling prices per unit of the three products at the split-off point and after further processing, and the additional processing costs are as follows. Product D E F Number of Units Produced 4,000 6,000 2,000 Selling Price at Split-Off Additional Processing Costs Selling Price after Processing $25.00 $26.60 $34.40 $14,000 $20,000 $9,000 $30.00 $31.20 $37.60 Instructions 1) Allocate the $200,000 joint cost to product D, E, and F using these methods: a. Physical-measure method (2%) b. NRV method (5%) 2) Which information is relevant to the decision on whether or not to process the products further? (2%). Explain why this information is relevant (2%). 3) Which product(s) should be processed further and which should be sold at…arrow_forward
- AccountingAccountingISBN:9781337272094Author:WARREN, Carl S., Reeve, James M., Duchac, Jonathan E.Publisher:Cengage Learning,Accounting Information SystemsAccountingISBN:9781337619202Author:Hall, James A.Publisher:Cengage Learning,
- Horngren's Cost Accounting: A Managerial Emphasis...AccountingISBN:9780134475585Author:Srikant M. Datar, Madhav V. RajanPublisher:PEARSONIntermediate AccountingAccountingISBN:9781259722660Author:J. David Spiceland, Mark W. Nelson, Wayne M ThomasPublisher:McGraw-Hill EducationFinancial and Managerial AccountingAccountingISBN:9781259726705Author:John J Wild, Ken W. Shaw, Barbara Chiappetta Fundamental Accounting PrinciplesPublisher:McGraw-Hill Education
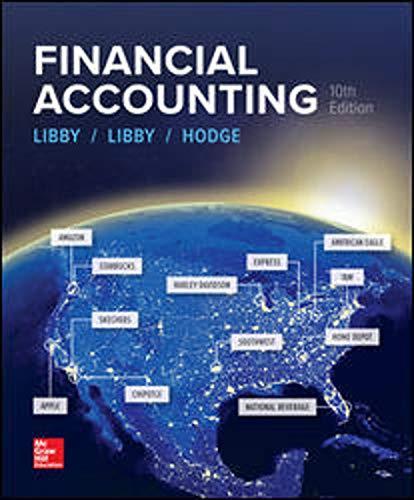
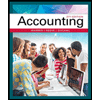
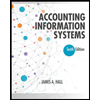
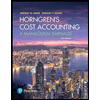
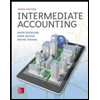
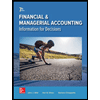