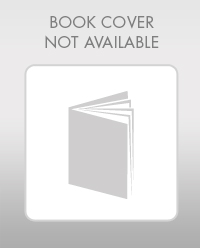
Concept explainers
Jamuna Group is evaluating the proposal of a new RMG factory called Jamuna Fabrics. Jamuna Group is renting a premise of 50,000 Square feet in Savar and Jamuna Fabrics is planning to use 10,000 Square feet from this facility. The rest of the premise will be used by another RMG factory of Jamuna Group called Jamuna Exclusive Fabrics. From these two factories, Jamuna Group expects to have a total output of 50,000 units of cloths at USD 3 per cloth and Jamuna Fabrics will have 40% of this total output. Total capital cost is USD 20,000 and is

Trending nowThis is a popular solution!
Step by stepSolved in 2 steps with 2 images

- Middle Industries produces a sensor for use in manufacturing. It produces the sensor in a plant with an annual practical capacity of 75,000 units. The variable cost of the sensor is $185.00 per unit, and the fixed costs of the plant are $12,375,000 annually. Current annual demand is 55,000 sensors. Middle Industries bought the plant because it was close to its other manufacturing facilities and was available for sale when they were searching for a location. Required: What cost per sensor should the cost system report to facilitate management decision making? What is the cost of excess capacity? What cost per sensor would the cost system report if the smallest manufacturing plant that could be built was able to produce 75,000 sensors? What would be the cost of excess capacity?arrow_forwardOman Chips company have noticed that the demand of their products increased in last few quarters. The company has decided to establish one production facility in Dhank, which will not only cover the demand of Al Dhahira region but also Al Buriami and some parts of Al Dakhiliya. The company purchased a land by using a significant amount and started constructing building and brought plant and machinery. During this whole process, one day they received a letter from public prosecution that this land is controversial and nothing can be done here. Now the case is in high court and it is expected that the company may lose this case. Now it is the responsibility of the company to _____________________. a. Disclose this issue in the annual meeting to come up with more ideas b. Disclose this information as it has a major impact on the balance sheet c. Show all information in their upcoming journal so that investor can get ideas d. None of the optionsarrow_forwardConsider this problem for the next five questions: At Kahel Enterprises, a producer of orange crates sold to growers, they are able to produce 450 crates per 100 logs with their current equipment. They currently purchase 100 logs per day, and each log requires 1.5 labor hours to process. They believe that they can hire a professional buyer who can buy better-quality log at the same cost. If this is the case, they can increase their production to 480 crates per 100 logs. Their total labor hours, on the other hand, will increase by an additional 2 hours per day (this is due to the additional logistics operations needed with the professional buyer). Given below are the cost per component in the system, which includes the labor cost, material cost, capital cost, and energy and utility cost. Cost Component Labor Php 100/labor hour Material (Logs) Php 200/log Capital Php 500 / day Energy & Utility Php 350 / day Question 1: What is the current labor productivity? 4.5 crates per labor hour 3…arrow_forward
- Mehmet Group wants to produce the M machines used in the casting industry in the Big Industry. The planned annual production and sales amount is 20,000 units and the sales price is calculated as "cost x 1.35". Information about this investment and production is given below. What is the sales price per unit of this project? What is the present and future value of the project's profit? TABLE: Workshop building and outbuildings 1.000.000 Usd Machine facilities 4,000,000 usd Staff is 380,000 usd and increasing by 40,000 usd every year Energy 180,000 usd and increasing by 15% every year Financing expenses 750,000 usd and decreasing by 10% each year Management and sales expenses decrease by 280,000 usd and 10,000 usd every year Raw material and auxiliary material 1.700 usd per unit Operation cost is 200,000 usd each year Major repair-maintenance is 150,000 usd in the 10th year Scrap value 8,000,000 usd in the 20th year Economic life 20 years Capital cost 25%arrow_forwardDivision Y has asked Division X of the same company to supply it with 9,000 units of part L763 this year to use in one of its products. Division Y has received a bid from an outside supplier for the parts at a price of $53 per unit. Division X has the capacity to produce 36,000 units of part L763 per year. Division X expects to sell 32,400 units of part L763 to outside customers this year at a price of $58.00 per unit. To fill the order from Division Y, Division X would have to cut back its sales to outside customers. Division X produces part L763 at a varlable cost of $45 per unit. The cost of packing and shipping the parts for outside customers is $2 per unit. These packing and shipping costs would not have to be incurred on sales of the parts to Division Y. Required: a. What is the range of transfer prices within which both the Divisions' profits would increase as a result of agreeing to the transfer of 9,000 parts this year from Division X to Division Y? (Round your final answers…arrow_forwardBoardman Gases and Chemicals is a supplier of highly purified gases to semiconductor manufacturers. A large chip producer has asked Boardman to build a new gas production facility close to an existing semiconductor plant. Once the new gas plant is in place, Boardman will be the exclusive supplier for that semiconductor fabrication plant for the subsequent 10 years. Boardman is considering one of two plant designs. The first is Boardman's "standard" plant which will cost $38.8 million to build. The second is for a "custom" plant which will cost $53.4 million to build. The custom plant will allow Boardman to produce the highly specialized gases required for an emergency semiconductor manufacturing process. Boardman estimates that its client will order $12.8 million of product per year if the standard plant is constructed, but if the custom design is put in place, Boardman expects to sell $17.1 million worth of product annually to its client. Boardman has enough money to build…arrow_forward
- In 1926 Branky scott and his wife GV started a small company in India that pioneered the use of plastics in the manufacturing of marine products. Branky Manufacturing has evolved to produce thousands of products under the Branky Trademark which are sold into the fishing, marine, outdoor, and firefighting industries worldwide. To manage production costs, Branky is considering implementing a JIT production system. The following are the estimated costs and benefits of JIT production:- Annual additional tooling costs would be $400,000- Annual inventory would decline by 80 percent from the current level of $4,000,000- Insurance, material handling, and set-up costs which currently total $1,200,000 annually, would decline by 25%- Rework would be reduced by 30 percent. Branky currently incurs $800,000 in annual rework costs.Improved product quality under JIT production would enable Branky to raise the price of its products by $8 per unit. Scotty sells 80,000 units per year.- Branky required…arrow_forward1. Jamuna Group is evaluating the proposal of a new RMG factory called Jamuna Fabrics. Jamuna Group is renting a premise of 50,000 Square feet in Savar and Jamuna Fabrics is planning to use 10,000 Square feet from this facility. The rest of the premise is currently being used by another RMG factory of Jamuna Group called Jamuna Exclusive Fabrics. The Jamuna Exclusive Fabrics has already started its production. For Jamuna Fabrics, the total capital cost is USD 40,000 and is depreciated using the straight-line method over five years to a zero-salvage value. The monthly salary expense will be USD 2500, whereas annual utility and other expense will be USD 2,000. The annual total rent of 50,000 Square feet premise is USD 25,000. Jamuna Fabrics will need to annually pay USD 6000 as staff’s festival bonus. The cash flow from asset for Jamuna Fabrics is USD 28000 in the first year, followed by USD 12000 in the second year. Assume, initially Jamuna Fabrics will require USD 2,000 in working…arrow_forwardAn automobile spare part manufacturer has set up a project for developing a new machine for one of its production lines. The engineering department has provided a project proposal that estimates the following investment requirements: ) An initial investment of RM 300,000 to be paid for purchasing the new machine. i) An additional cost is needed to install the machines and integrate it into the overall production system and it is estimated to take one (1) year for completion. There are three cost categories involved: • Engineering labor cost, estimated to be 1200 hours at a cost of RM 100/hour. • None-engineering labor cost, estimated to be 3000 hours at a cost of RM 50/hour. Assorted material cost, estimated to be RM 100,000. iv) The machine has to be overhauled every 2 year, and it costs RM 20.000 beginning the third year of the project. They will not overhaul the machine in the last year of its life. v) The production will be started in the second year, and it will be up-to-speed by…arrow_forward
- Due to rising labor costs in Malaysia, Domain Computer, based in Singapore, is considering shifting part of its production facilities from Malaysia to an emerging market, Vietnam, to better integrate its supply chain in the South east Asia region. John Lawson, the CFO of the company, estimates that Domain Computer needs to invest USD735,000 to acquire an existing factory in Vietnam and another USD285,000 in renovations and installation of new machineries. The cost of training new workers is estimated to be USD310,000. He believes that the new factory will lead to an estimated USD928,000 savings in labor costs and another USD417,000 savings in logistics expenses. Required: Use cost-benefit analysis to recommend whether Domain Computer should shift parts of its production facilities from Malaysia to Vietnam. Explain your answer. You are required to write 500 to 800 words. ( Currently I have completed my Cost-benefit analysis; but I am confused as to how to use PESTLE's analysis with…arrow_forwardVikrambhaiarrow_forwardMr. Waqar is employed in a furniture manufacturing concern and he is currently working a total of 11 hours per day to produce 10 chairs. He thinks that by adopting a new method he can increase his rate to 12 chairs per day. The total material cost for each chair is approximately Rs. 600; he has to invest Rs. 700 in the necessary supplies (expendables) per day; energy costs are assumed to be only Rs. 550 per day. Viewing this from a total (multifactor) productivity perspective, what is his productivity at present and with the new method?arrow_forward
- Essentials Of InvestmentsFinanceISBN:9781260013924Author:Bodie, Zvi, Kane, Alex, MARCUS, Alan J.Publisher:Mcgraw-hill Education,
- Foundations Of FinanceFinanceISBN:9780134897264Author:KEOWN, Arthur J., Martin, John D., PETTY, J. WilliamPublisher:Pearson,Fundamentals of Financial Management (MindTap Cou...FinanceISBN:9781337395250Author:Eugene F. Brigham, Joel F. HoustonPublisher:Cengage LearningCorporate Finance (The Mcgraw-hill/Irwin Series i...FinanceISBN:9780077861759Author:Stephen A. Ross Franco Modigliani Professor of Financial Economics Professor, Randolph W Westerfield Robert R. Dockson Deans Chair in Bus. Admin., Jeffrey Jaffe, Bradford D Jordan ProfessorPublisher:McGraw-Hill Education
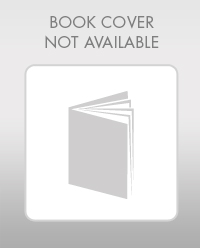
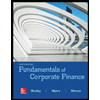
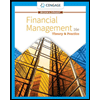
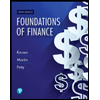
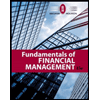
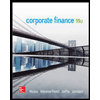