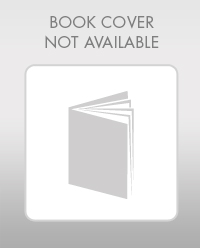
it a concrete encased steel composite column. It consists of a steel UC (universal column), with 8 additional steel longitudinal reinforcement bars which is then encased in concrete.
Dimensions of the UC – obtain from Liberty Steel hot-rolled section properties product guide Spacing is the distance from the edge of the UC to the centre of the reinforcing bar
Cover is the distance from the edge of the concrete to the centre of the reinforcing bar:
Material properties are Esteel = 200 GPa Econcrete = 28 GPa, and both materials experience linearly elastic behaviour.
The member is used as a column and is subjected to axial compression.
UC type : 200UC52.2
steel bar diameter ds(mm): 16
spacing: 2.5 ds
cover :70mm
column height (L/duc):24
fsteel,max = 95MPa
fconcrete,max= 12MPa
strain (concrete)max = 425 x 10^-6
max shortening =2.25 mm
the column must satisfy the various stress, strain and absolute shortening limits
What is the maximum axial load P to satisfy all the design criteria?
Your answer should clearly show the values of steel and concrete stress and strain, and axial
shortening, for this value of P.
The engineer decides to move the location of the steel reinforcing bars by slightly increasing the spacing dimensions, with a corresponding decrease in the cover dimensions. The overall concrete dimensions do not change. How will that impact the sharing of load between the steel and concrete compared to the original?

Trending nowThis is a popular solution!
Step by stepSolved in 2 steps with 4 images

- #1 will upvote to anyone who will answerarrow_forwardQ Search MT ACTIVITY 2M Close Activity File Home Insert Draw View Help Open in Desktop App O Tell me what you want to do v 11 ev Av A A Styles v E Tags v abc v Calibri ... SW The composite bar shown in Fig. P-273 is firmly attached to unyielding supports. An axial force P = 50 kips is applied at 60°F. Compute the stress in each material at 120°F. Assume a = 6.5 × 10- Teams Assignments 国 Calendar Calls 6 in/(in-°F) for steel and 12.8 x 10-6 in/(in-°F) for aluminum. Files Aluminum A = 2 in? E = 10 x 10° psi Steel A = 3 in? E = 29 x 10° psi ... 15 in 10 in 田 Helparrow_forward2.) The following cross Section Roprsonts a composité cylindere! GiVEN: FIND: a) the Composite Centroid b5 the composite conter of grauity Moghessium Alloy A 36 Steel tーarrow_forward
- Required information A steel bar (Es = 210 GPa) and an aluminum bar (Ea = 70 GPa) are bonded together to form the composite bar shown. 8 mm Steel 8 mm 8 mm Aluminum 24 mm Determine the maximum stress in aluminum when the bar is bent about a horizontal axis, with M= 66 N-m. The maximum stress in aluminum is MPа.arrow_forward3) will upvote to anyone who will answerarrow_forwarde7arrow_forward
- The composite bar, firmly attached to unyielding supports, is initially stress-free. What maximum axial load P can be applied if the allowable stresses are 10 ksi for aluminum and 18 ksi for steel?arrow_forwardDetermine if w10x12 (A242) section is Compact, Non-Compact or slender. Show neat handwriting and complete solution.arrow_forwardEstimate the cross-sectional area of a 350S125-27 cold-formed shape.a. If the member is tested in tension, what would be the maximum force the sample could carry before reaching the yield strength if the steel has a yield strength of 33 ksi?b. Would you expect a 96 in. stud to carry the same load in compression?(explain)arrow_forward
- Ce tip.instructure.com Incognito (2) A composite section will be used to support a heavy axial load of P-800 kN with a First Semester SY 2021-2. rigid plate at the top of the section. Determine the average compressive stress in the brass section. Use h=16 mm. Answer in MegaPascals. Home Announcements Brass core (E = 105 GPa) Rigid end plate count Assignments Aluminum plates (E = 70 GPa) Discussions aboard Grades People urses Pages endar Files 300 mm Syllabus |auizes box Modules tory BigBlueButton (Conferences) elp Chat 60 mm T.I.P. Manila Library Video 40 mm Presentation Canvas LMS Satisfactorvarrow_forwardThe composite shaft shown consists of a solid brass segment (1) and a solid aluminum segment (2) that are connected at flange B and securely attached to rigid walls at A and C. Brass segment (1) has a diameter of 18 mm, a length of L₁ 235 mm, and a shear modulus of 39 GPa. Aluminum segment (2) has a diameter of 24 mm, a length of L₂ = 165 mm, and a shear modulus of 28 GPa. If a concentrated torque of 270 N-m is applied to flange B, determine (a) the maximum shear stress magnitudes in segments (1) and (2). (b) the rotation angle of flange B relative to support A. N 235 mm (1) B 165 mm Partial Ans: Max shear stress in Member 1 is 55.7 MPa 270 N-m (2)arrow_forward4. For the composite block shown, determine (a) the value of h if the portion of the load carried by the aluminum plates is half the portion of the load carried by the brass core, (b) the total load if the stress in the brass is 80 Mpa. P Rigid end plate Aluminum Plates (E=70 GPa) Brass Core (E=105 GPa) 40 mm I h 60 mm 300 mmarrow_forward
- Structural Analysis (10th Edition)Civil EngineeringISBN:9780134610672Author:Russell C. HibbelerPublisher:PEARSONPrinciples of Foundation Engineering (MindTap Cou...Civil EngineeringISBN:9781337705028Author:Braja M. Das, Nagaratnam SivakuganPublisher:Cengage Learning
- Fundamentals of Structural AnalysisCivil EngineeringISBN:9780073398006Author:Kenneth M. Leet Emeritus, Chia-Ming Uang, Joel LanningPublisher:McGraw-Hill EducationTraffic and Highway EngineeringCivil EngineeringISBN:9781305156241Author:Garber, Nicholas J.Publisher:Cengage Learning
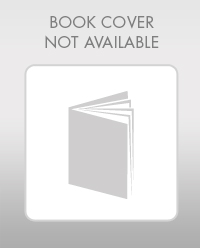
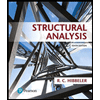
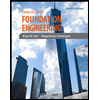
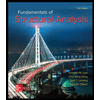
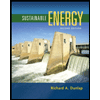
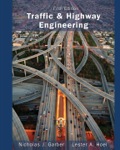