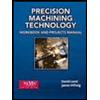
Precision Machining Technology (MindTap Course List)
2nd Edition
ISBN: 9781285444543
Author: Peter J. Hoffman, Eric S. Hopewell, Brian Janes
Publisher: Cengage Learning
expand_more
expand_more
format_list_bulleted
Concept explainers
Question
thumb_up100%
In the formulation, how many constraints (i.e., constraint equations) are there and which involves two variables? How many objective functions are there?

Transcribed Image Text:A manufacturing firm produces two components for electric scooters. An axle requires 2.4 min of molding time and
5.0 min of assembly time. The profit for axles is $0.60 per unit. A single handlebar grip requires 3.0 min of molding
time and 2.5 min of finishing time. The profit for grips is $0.70 per unit. The molding department has 1,200 minutes
of time per week to allocate to these products. The finishing department has idle capacity of 600 minutes per week,
and the assembly department can supply 1,500 minutes of capacity per week. The firm wants to determine the
optimum production amounts of axles and grips this week using a linear programming method.
Expert Solution

This question has been solved!
Explore an expertly crafted, step-by-step solution for a thorough understanding of key concepts.
Step by stepSolved in 3 steps with 10 images

Knowledge Booster
Learn more about
Need a deep-dive on the concept behind this application? Look no further. Learn more about this topic, mechanical-engineering and related others by exploring similar questions and additional content below.Similar questions
- The monthly usage for a component supplied to an assembly plant is 3,400 parts. There are 21 working days in the month and the effective operating time of the plant is 450 min per day. Currently, the defect rate for the component is 1.2%, and the equipment used to produce the part is down for repairs an average of 18 min per day. Determine the takt time for this part.arrow_forwardThe Old Hickory Furniture Company manufactures chairs on the basis of the BOM shown below. At the present time, the inventories of parts and lead times are as follows:The firm would like to produce 600 chairs in week 5 and 300 chairs in week 6. a. Develop a materials plan for all the parts. b. What actions should be taken now? c. Assume it takes one hour to assemble backs, one hour to assemble legs, and two hours to finish completed chairs. Total assembly time for all three types of assembly is limited to 1000 hours per week. Will this capacity constraint cause a bottleneck in assembly? I it does, what can be done? d. What is the effect of changing the master schedule to 300 chairs in week 5 and 400 chairs in week 6?arrow_forwardThe MPS start quantities for product A calls for the assembly department to begin final assembly accordingto the following schedule: 100 units in week 2; 200 units in week 4; 120 units in week 6; 180 units in week 7;and 60 units in week 8. Develop a material requirements plan for the next 8 weeks for items B, C, and D.The BOM for A is shown in Figure 11.26, and data from the inventory records are shown in Table 11.4.arrow_forward
- 8Aarrow_forwardA robot is used for loading and unloading of parts to automated flexible machines. Loading time is 1 minute; unloading time is 1.5 minutes; machining time 15 minutes; Robot travel time between the machines including the inspection time is 3 minutes. Cost of robot C,=30 TL/Hour; cost of machines C2=40 TL/Hour. How many machines (integer number) should be assigned to the robot so that the total robot and machine costs per cycle are minimized? 8 - 176 a) 4 b) 3 c) 2 d) e) 6.arrow_forwardILLUSTRATION 2: An operator manufactures 50 jobs in 6 hours and 30 minutes. If this time includes the time for setting his machine. Standard time allowed for the job was: Setting time = 35 min Production time per piece = 8 min %3Darrow_forward
- Please solve it complete please don't copy pastearrow_forwardQ1. A power-shift crawler tractor is excavating hard materials of earth (clay) and pushing it a distance of 100 ft. The hourly cost of a power-shift crawler tractor is $200. Maximum reverse speeds are: first range, 6 mph; second range, 9 mph; and third range, 11 mph. Rated blade capacity is 18 LCY. Estimate dozer production if the job efficiency factor is 50 min/hr and what is the expected unit cost for dozer work ($/BCY)?arrow_forwardThe BOM for product A is shown in Figure 11.40, and datafrom the inventory records are shown in Table 11.9. In theMPS for product A, the MPS start row has 100 units in week 3and 200 in week 6. Develop the material requirements planfor the next 6 weeks for items C, D, and E.a. Develop the material requirements plan for the next6 weeks for items C, D, and E.b. What specific managerial actions are required inweek 1?arrow_forward
- A batch of 35 parts is ordered by a customer about every six months. The parts are currently processed sequentially through five conventional machines, listed in the following table with setup times and work cycle times per piece. These machines all require an operator to be in attendance during the work cycle. There is a delay of 10 hr/machine dueto transport between machines and waiting in queues of other parts processed by thesemachines. A recommendation has been made to process the parts on a new multitaskingmachine that would complete the batch in one setup, which would involve a simple fixtureand a setup time of 2.0 hr. The work cycle on the multitasking machine consists of thesame operations that are accomplished by the five machines, but the cycle time would beless than the sum of the five cycle times by one-half because of tool path improvementsand reduced part handling. Determine the manufacturing lead time (how long it takes tocomplete the batch of 35 parts, including…arrow_forwardA production process at Kenneth Day Manufacturing is shown in the figure below. The drilling operation occurs separately from, and simultaneously with, the sawing and sanding, which are independent sequential operations. A product needs to go through only one of the three assembly operations (the operations are in parallel). 2.1 units/hr Sawing 7 units/hr Sanding Drilling 6 units/hr Welding 2.5 units/hr a) Sawing is the bottleneck. b) The bottleneck time is 28.57 minutes per unit (round your response to two decimal places). c) The throughput time of the overall system is minutes (round your response to two decimal places). Assembly 0.8 units/hr Assembly 0.8 units/hr Assembly 0.8 units/hrarrow_forwardTask 1: 1. The quantity of sandwiches, Q, made in a small coffee shop is given by the equation Q = -2L³ +12L? where L is the number of labour-hours hired. (a) Write down the equations for the marginal product of labour (MP1) and average product of labour (APL). Give a verbal description of MP1 and APL at L = 1.5. (b) Calculate the units of labour at which MP1 and APL are maximised, and plot both graphs on the same diagram. Confirm algebraically that MPL and APL are equal when APL is at a maximum. (c) Find the turning points and point of inflection for the production function. Plot the pro- duction function. (d) Use the graphs and any other results calculated in (a) and (b) to describe how productivity (Q= number of sandwiches) and the rate of change in productivity as the number of labour units employed (L) increase. Is there any relationship between the turning points and points of inflection in the graphs plotted in (b) and (c)?arrow_forward
arrow_back_ios
SEE MORE QUESTIONS
arrow_forward_ios
Recommended textbooks for you
- Precision Machining Technology (MindTap Course Li...Mechanical EngineeringISBN:9781285444543Author:Peter J. Hoffman, Eric S. Hopewell, Brian JanesPublisher:Cengage Learning
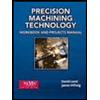
Precision Machining Technology (MindTap Course Li...
Mechanical Engineering
ISBN:9781285444543
Author:Peter J. Hoffman, Eric S. Hopewell, Brian Janes
Publisher:Cengage Learning