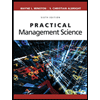
Practical Management Science
6th Edition
ISBN: 9781337406659
Author: WINSTON, Wayne L.
Publisher: Cengage,
expand_more
expand_more
format_list_bulleted
Question
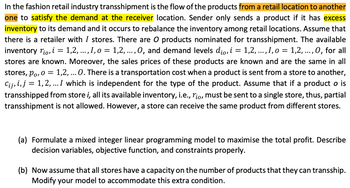
Transcribed Image Text:In the fashion retail industry transshipment is the flow of the products from a retail location to another
one to satisfy the demand at the receiver location. Sender only sends a product if it has excess
inventory to its demand and it occurs to rebalance the inventory among retail locations. Assume that
there is a retailer with I stores. There are O products nominated for transshipment. The available
inventory rio, i = 1,2, ..., I, o = 1,2, ..., 0, and demand levels dio, i = 1,2, ..., I, o = 1,2, ..., 0, for all
stores are known. Moreover, the sales prices of these products are known and are the same in all
stores, po, o = 1,2, ... 0. There is a transportation cost when a product is sent from a store to another,
Cij, i, j = 1, 2, ... I which is independent for the type of the product. Assume that if a product o is
transshipped from store i, all its available inventory, i.e., rio, must be sent to a single store, thus, partial
transshipment is not allowed. However, a store can receive the same product from different stores.
(a) Formulate a mixed integer linear programming model to maximise the total profit. Describe
decision variables, objective function, and constraints properly.
(b) Now assume that all stores have a capacity on the number of products that they can transship.
Modify your model to accommodate this extra condition.
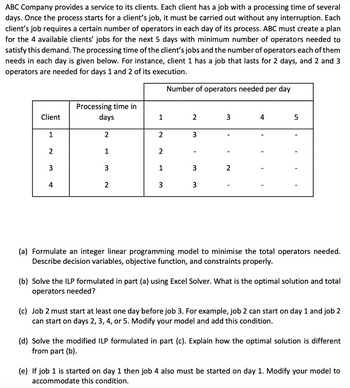
Transcribed Image Text:ABC Company provides a service to its clients. Each client has a job with a processing time of several
days. Once the process starts for a client's job, it must be carried out without any interruption. Each
client's job requires a certain number of operators in each day of its process. ABC must create a plan
for the 4 available clients' jobs for the next 5 days with minimum number of operators needed to
satisfy this demand. The processing time of the client's jobs and the number of operators each of them
needs in each day is given below. For instance, client 1 has a job that lasts for 2 days, and 2 and 3
operators are needed for days 1 and 2 of its execution.
Number of operators needed per day
Client
1
2
3
4
Processing time in
days
2
1
3
2
1
2
2
1
3
2
3
3
3
3
2
4
5
(a) Formulate an integer linear programming model to minimise the total operators needed.
Describe decision variables, objective function, and constraints properly.
(b) Solve the ILP formulated in part (a) using Excel Solver. What is the optimal solution and total
operators needed?
(c) Job 2 must start at least one day before job 3. For example, job 2 can start on day 1 and job 2
can start on days 2, 3, 4, or 5. Modify your model and add this condition.
(d) Solve the modified ILP formulated in part (c). Explain how the optimal solution is different
from part (b).
(e) If job 1 is started on day 1 then job 4 also must be started on day 1. Modify your model to
accommodate this condition.
Expert Solution

This question has been solved!
Explore an expertly crafted, step-by-step solution for a thorough understanding of key concepts.
This is a popular solution
Trending nowThis is a popular solution!
Step by stepSolved in 4 steps with 8 images

Knowledge Booster
Similar questions
- Answer the given question with a proper explanation and step-by-step solution. An E-commerce firm has four regional fulfillment centers (warehouses). Weekly demand for an item (Product_A) at each warehouse is random and is normally distributed with a mean of 10,000 per week and a standard deviation of 2,000 units per week. Product_A’s unit cost is $10. The inventory holding cost of the company is 25% per year. Assume 50 weeks per year. Each replenishment order from the supplier of Product_A costs $1,000, which includes the costs associated with placing the order, transportation, receiving, inspection, and put-away labor expenses. The replenishment lead time from the supplier is 1 week. The company’s service level goal is 95% (probability of having sufficient inventory to meet demand). On average, how long does a unit of inventory spend in the warehouse before being sold? Hint: Think Little's Law 2.5 weeks 6.6 weeks 5.3 weeks 1.3 weeksarrow_forwardDaily demand for a type of sandwich sold at DoorRed Cafe (DRC) is normally distributed with a mean of 65 and a standard deviation of 27. DRC orders the sandwiches from a wholesaler (everyday morning before 5:30 AM) at a wholesale price of $4 per sandwich and sells them at a retail price of $7 per sandwich. Pursuant to the contract between DRC and its wholesaler, the transportation cost is currently borne by the wholesaler. The wholesaler does not take back any unsold sandwiches. However, DRC can sell any unsold inventory at a discounted price of $3 after 5:00 PM every day. d) Now suppose that the contract between DRC and its wholesaler expires and pursuant to the new contract, if DRC orders more than 56 sandwiches (anything more than or equal to 57), the transportation cost is no longer borne by the wholesaler and DRC will have to pay $30 for transportation. If DRC orders less than or equal to 56, the transportation cost for DRC is still zero. What is DRC’s optimal order quantity for…arrow_forwardJack Ltd is a market leader in the manufacture of apple juice. They operate areorder level system of inventory management, and the following information isavailable for green apples:Average usage 800 per dayMinimum usage 540 per dayMaximum usage 1260 per dayLead time for replenishment 16-20 dayReorder quantity 19,500 applesRequired:ii Calculate the maximum level of inventoryarrow_forward
- A wallpaper company estimates the demand for a certain pattern to be 925 rolls per year. It costs $750 to set up the presses to print the pattern, plus $150 to print each roll. If the company can store a roll of wallpaper for a year at a cost of $4, how many rolls should it print at a time and how many printing runs on average will it need in a year to minimize production costs? (Assume the wallpaper sells steadily throughout the year, and the company reorders more whenever the stock runs out. Round the number of rolls per print to the nearest whole number and the average number of printing runs per year to two decimal places.) rolls per print rolls print runs per year runsarrow_forwardhello, can someone help me with this question?: if a company regularly holds 50 units of safety stock of a product and places orders in quantities of 500 units for the same product, what would be the average warehouse inventory for that product?arrow_forwardThe extra inventory we keep just in case the replenishment is delayed is referred to as Group of answer choices a)customer service inventory b)unanticipated excess inventory c)safety stock d) unexplained inventoryarrow_forward
- The following data represent the beginning inventory and, in order of occurrence, the purchases and sales of Meow, Inc. for an operating period. Units Unit Total Units Cost Cost Sold Beginning Inventory 50 $62 $3,100 Sale No. 1 40 Purchase No. 1 30 50 1,500 Sale No. 2 32 Purchase No. 2 40 44 1,760 Totals 120 $6,360 72 Assuming Meow, Inc. uses LIFO perpetual inventory procedures, the ending inventory cost is:arrow_forwardKen Ramsing has been in the lumber business for most of his life. Ken’s biggest competitor is Pacific Woods. Through many years of experience, Ken knows that the ordering cost for an order of plywood is $25 and that the carrying cost is 25% of the unit cost. Both Ken and Pacific Woods receive plywood in loads that cost $100 per load. Furthermore, Ken and Pacific Woods use the same supplier of plywood, and Ken was able to find out that Pacific Woods orders in quantities of 4,000 loads at a time. Ken also knows that 4,000 loads is the EOQ for Pacific Woods. What is the annual demand in loads of plywood for Pacific Woods?arrow_forwardACold Inc is a frozen food distributor with 10 warehouses across the country. Ivan Tory, one of the warehouse managers, wants to make sure that the inventory policies used by the warehouse are minimizing inventory while still maintaining quick delivery to ACold's customers. Since the warehouse carries hundreds of different products, Ivan decided to study one. He picked Caruso's Frozen Pizza (CFP). Average daily demand for CFPs is normally distributed with a mean of 384 and a standard deviation of 158. Since ACold orders at least one truck from their supplier each day, ACold can essentially order any quantity of CFP it wants each day. In fact, ACold's computer system is designed to implement an order-up-to policy for each product. Ivan notes that any order for CFPs arrives 5 days after the order. a. Suppose an order-up-to level of 2472 is used. What is the expected on-hand inventory? Use Table 14.1 and round to nearest integer. b. Suppose an order-up-to level of 2404 is used. What is…arrow_forward
- The quantity consumed or patronage—store visits—during a specific period is called A. trial. B. service inventory. C. usage rate. D. consumption rate. E. turnover.arrow_forwardIt takes approximately 2 weeks (14 days) for an order of steel bolts to arrive once the order has been placed. The demand for bolts is fairly constant; on the average, the manager, Michelle Wu, has observed that the hardware store sells 500 of these bolts each day. Because the demand is fairly constant, Michelle believes that she can avoid stockouts completely if she orders the bolts at the correct time. What is the reorder point? The reorder point is? units (enter your response as a whole number).arrow_forwardA product has a reorder point of 110 units and is ordered four times a year on average. The following table shows the historical distribution of demand values observed during lead time. Managers have noted that stockouts occur 30 percent of the time with this policy, and they question whether a change in inventory policy, to include some safety stock, might be an improvement. The managers realize that any safety stock would increase the service level, but they are worried about the increased costs of carrying the safety stock. Currently, stockouts are valued at $20 per unit per occurrence, while inventory carrying costs are $10 per unit per year. Demand Probability 100 0.20 110 0.35 120 0.30 130 0.15 What level of safety stock is best?arrow_forward
arrow_back_ios
SEE MORE QUESTIONS
arrow_forward_ios
Recommended textbooks for you
- Practical Management ScienceOperations ManagementISBN:9781337406659Author:WINSTON, Wayne L.Publisher:Cengage,Operations ManagementOperations ManagementISBN:9781259667473Author:William J StevensonPublisher:McGraw-Hill EducationOperations and Supply Chain Management (Mcgraw-hi...Operations ManagementISBN:9781259666100Author:F. Robert Jacobs, Richard B ChasePublisher:McGraw-Hill Education
- Purchasing and Supply Chain ManagementOperations ManagementISBN:9781285869681Author:Robert M. Monczka, Robert B. Handfield, Larry C. Giunipero, James L. PattersonPublisher:Cengage LearningProduction and Operations Analysis, Seventh Editi...Operations ManagementISBN:9781478623069Author:Steven Nahmias, Tava Lennon OlsenPublisher:Waveland Press, Inc.
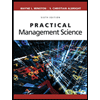
Practical Management Science
Operations Management
ISBN:9781337406659
Author:WINSTON, Wayne L.
Publisher:Cengage,
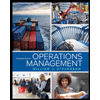
Operations Management
Operations Management
ISBN:9781259667473
Author:William J Stevenson
Publisher:McGraw-Hill Education
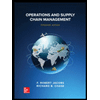
Operations and Supply Chain Management (Mcgraw-hi...
Operations Management
ISBN:9781259666100
Author:F. Robert Jacobs, Richard B Chase
Publisher:McGraw-Hill Education
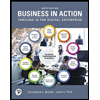
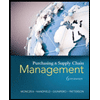
Purchasing and Supply Chain Management
Operations Management
ISBN:9781285869681
Author:Robert M. Monczka, Robert B. Handfield, Larry C. Giunipero, James L. Patterson
Publisher:Cengage Learning
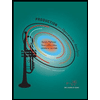
Production and Operations Analysis, Seventh Editi...
Operations Management
ISBN:9781478623069
Author:Steven Nahmias, Tava Lennon Olsen
Publisher:Waveland Press, Inc.