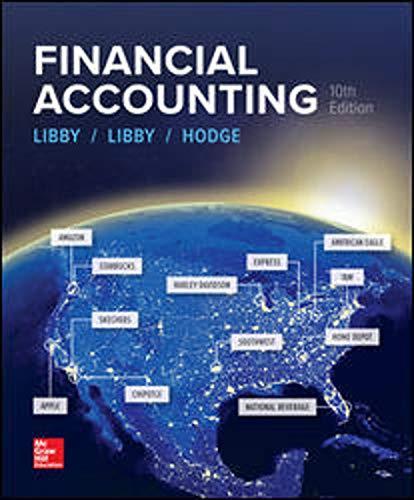
FINANCIAL ACCOUNTING
10th Edition
ISBN: 9781259964947
Author: Libby
Publisher: MCG
expand_more
expand_more
format_list_bulleted
Question
Cledus and Bandit, LLC is a small production facility in Foley, Alabama that produces three products in a joint
Product |
Sales Value
at Split-off |
Separable Processing
Costs after Split-off |
Sales Value at Completion |
A
|
$12
|
$9
|
$21
|
B
|
10
|
4
|
17
|
C
|
15
|
6
|
19
|
If Product A is processed beyond the split-off point, profit will:
Group of answer choices
remain unchanged
increase by $210,000
increase by $ 90,000
increase by $120,000
Expert Solution

This question has been solved!
Explore an expertly crafted, step-by-step solution for a thorough understanding of key concepts.
This is a popular solution
Trending nowThis is a popular solution!
Step by stepSolved in 3 steps with 2 images

Knowledge Booster
Similar questions
- 2. Joint product costing 17 Flora Perfume Company manufactures two perfume products in a joint process. In July, raw materials costing $50,000 were processed at a conversion cost of $80,000. The joint process resulted in 10 litres of product A and 15 litres of product B. Product A can be sold for $2 per millilitres, and product B can be sold for $1.5 per millilitres. Management generally processes each of these chemicals further in separable processes to produce more refined perfume products. Product A is processed separately at a cost of $0.5 per millilitres. The resulting product, product X sells for $5 per millilitres. Product B is processed separately at a cost of $0.75 per millilitres. The resulting product, product Y, sells for $3 per millilitres. Required: Allocate the company's joint production costs for July using: a. The physical unit method b. The relative-sales-value method. c. The net-realizable-value methodarrow_forwardRelyaTech Corporation makes two products, Light and Heavy. These two products emerge from a joint process. Product Light has been allocated $19,300 of the total joint costs of $40,000. A total of 2,600 units of product Light are produced from the joint process. (ID#62183) Product Light can be sold at the split-off point for $13 per unit, or it can be processed further for an additional total cost of $10,600 and then sold for $15 per unit Q) If product Light is processed further and sold, what would be the financial advantage (disadvantage) for RelyaTech Corporation compared with sale in its unprocessed form directly after the split-off point? Multiple Choice ($13,900) ($27300) $(5,400) $28,400 Help Save & Exitarrow_forwardCorporation manufactures three products from a joint process. The three products are in industrial grade form at the split off point. They can either be sold at that point or processed further into premium grade. Costs related to each batch of this process is as follows: Product 1 Product 2 Product 3 Sales Price at split-off point $16 $12 $5 Allocated joint costs $6,000 $6,000 $6,000 Sales Price after further processing $20 $18 $14 Cost of further processing $6,360 $1,420 $2,650 Product Quantity 1,000 lb. 1,000 lb. 1,000 Ib. Q. What would be the additional amount of profit that Corp. would gain from further processing the product(s) that is/are more profitable to process further rather than be sold at the split-off point?arrow_forward
- Barrett Chemicals manufactures four chemicals, Chem-1, Chem-2, Chem-3, and Chem-4, from a joint process. The total joint costs in May were $564,000. Additional information follows: Product Units Produced Sales Value at Split-Off If Processed Further Additional Costs Sales Values Chem-1 302,000 $ 234,000 $ 34,100 $ 274,000 Chem-2 190,000 278,000 30,800 304,000 Chem-3 206,000 163,600 26,300 194,000 Chem-4 158,000 260,400 27,700 284,000 856,000 $ 936,000 $ 118,900 $ 1,056,000 Required: Barrett Chemicals uses the net realizable value method to allocate joint costs. What joint costs would be allocated to each product in May? Note: Round percentages to 2 decimals. Round your final answers to the nearest whole dollar amounts.arrow_forwardA joint production process at the Company results in two products, cherry jelly and cherry jam. The following cost and activity data relate to these two products: Cherry jelly Cherry jam Joint costs allocated $10,000 $12,000 Number of units produced from joint process 2100 2100 Selling price at split-off point $2.70 $1.75 Selling price after processing further $5.00 $2.00 Cost of processing further $2400 $2,000 Cherry jelly can be sold as-is (at the split-off point) for $2.70 per unit, or it can be processed further into a specialty cherry smoothie and then sold for $5.00 per unit. If cherry jelly is processed further into the specialty cherry smoothie, what would be the overall effect on operating income? $2430 net increase in operating income $2430 net decrease in operating income $5670 net increase in operating income $5670 net decrease in operating incomearrow_forwardTango Company produces joint products M, N, and T from a joint process. This information concerns a batch produced in April at a joint cost of $190,000: Product M N T Units Produced and Sold 17,000 11,000 12,000 Product M N T Allocated Joint Cost After Split-Off Total Separable Costs $ 18,800 16,400 3,800 Total Final Sales. Value Required: How much of the joint cost should be allocated to each joint product using the net realizable value method? (Do not round intermediate calculations. Enter your final answers in whole dollars.) $ 230,000 210,000 39,000arrow_forward
- Crane's woodworking business produces two products from its joint process: one main product (sanded and finished trim pieces) and one by-product (sawdust/shavings). The joint process has a cost of $31,000, which results in trim pieces worth $47,000 and sawdust/shavings that can be sold for $2,800. If Crane uses the production method to account for by-products, determine how much of the joint process cost will be allocated to each product. In other words, how much inventory cost will be recorded for each product? Main product By-product Allocated joint costs $arrow_forwardJoint Cost Allocation—Physical Units Method Board-It, Inc., produces the following types of 2 × 4 × 10 wood boards: washed, stained, and pressure treated. These products are produced jointly until they are cut. One batch produces 45 washed boards, 35 stained boards, and 20 pressure treated boards. The joint production process costs a total of $710 per batch. Using the physical units method, allocate the joint production cost to each product. Round your answers to two decimal places. Joint Product Allocation Washed $ Stained Pressure treated Totals $arrow_forwardJoint cost allocation — physical units method Board-It, Inc., produces the following types of 2 × 4 × 10 wood boards: washed, stained, and pressure treated. These products are produced jointly until they are cut. One batch produces 50 washed boards, 40 stained boards, and 10 pressure treated boards. The joint production process costs a total of $800 per batch. This information has been collected in the Microsoft Excel Online file. Open the spreadsheet, perform the required analysis, and input your answers in the question below. Open spreadsheet Using the physical units method, allocate the joint production cost to each product. Round your answers to the nearest cent. Joint Product Allocation Washed $fill in the blank 2 Stained fill in the blank 3 Pressure treated fill in the blank 4 Totals $fill in the blank 5arrow_forward
- Lawn Products produces two products (X and Y) and a by-product (Z) from a joint process using a raw material (Alpha). The company chooses to allocate the costs on the basis of the physical quantities method. Last month, it processed 23,000 pounds of Alpha at a total cost of $99,000. The output of the process consisted of 28,800 units of product X, 35,200 units of product Y, and 7,100 units of by-product Z. By-product Z can be sold for $12,000. This is considered to be its net realizable value, which is deducted from the processing costs of the main products. Required: What amount of joint costs should be assigned to each of product X and product Y? Product X Product Y Joint Costsarrow_forwardNorthern Company processes 100 gallons of raw materials into 75 gallons of product GS-50 and 25 gallons of GS-80. GS-50 is further processed into 50 gallons of product GS-505 at a cost of $7,250, and GS-80 is processed into 50 gallons of product GS-805 at a cost of $5,750. The production process starts at point 1. A total of $20,000 in joint manufacturing costs are incurred in reaching point 2. Point 2 is the split-off point of the process that manufactures GS-50 and GS-80. At this point, GS-50 can be sold for $725 a gallon, and GS-80 can be sold for $145 a gallon. The process is completed at point 3-products GS-505 and GS-805 have a sales price of $585 a gallon and $225 a gallon, respectively. Required: Allocate the joint product costs and then compute the cost per unit using each of the following methods: (1) physical measure, (2) sales value at split-off, and (3) net realizable value. (Do not round intermediate calculations. Round your final answers to nearest whole dollar amount.)…arrow_forwardThe Marshall Company has a joint production process that produces two joint products and a by-product. The joint products are Ying and Yang, and the by-product is Bit. Marshall accounts for the costs of its products using the net realizable value method. The two joint products are processed beyond the split-off point, incurring separable processing costs. There is a $1,500 disposal cost for the by- product. A summary of a recent month's activity at Marshall is shown below: Ying 75,000 75,000 $ 210,000 $ 15,000 $ 6.00 Total joint costs for Marshall in the recent month are $211,000, of which $90,730 is a variable cost. Units sold Units produced Separable processing costs-variable Separable processing costs-fixed Sales price Manufacturing cost per unit Total gross margin Yang 60,000 60,000 $ 65,000 $ 10,000 $ 12.50 Required: 1. Calculate the manufacturing cost per unit for each of the three products. (Round manufacturing cost per unit answers to 2 decimal places.) 2. Calculate the total…arrow_forward
arrow_back_ios
SEE MORE QUESTIONS
arrow_forward_ios
Recommended textbooks for you
- AccountingAccountingISBN:9781337272094Author:WARREN, Carl S., Reeve, James M., Duchac, Jonathan E.Publisher:Cengage Learning,Accounting Information SystemsAccountingISBN:9781337619202Author:Hall, James A.Publisher:Cengage Learning,
- Horngren's Cost Accounting: A Managerial Emphasis...AccountingISBN:9780134475585Author:Srikant M. Datar, Madhav V. RajanPublisher:PEARSONIntermediate AccountingAccountingISBN:9781259722660Author:J. David Spiceland, Mark W. Nelson, Wayne M ThomasPublisher:McGraw-Hill EducationFinancial and Managerial AccountingAccountingISBN:9781259726705Author:John J Wild, Ken W. Shaw, Barbara Chiappetta Fundamental Accounting PrinciplesPublisher:McGraw-Hill Education
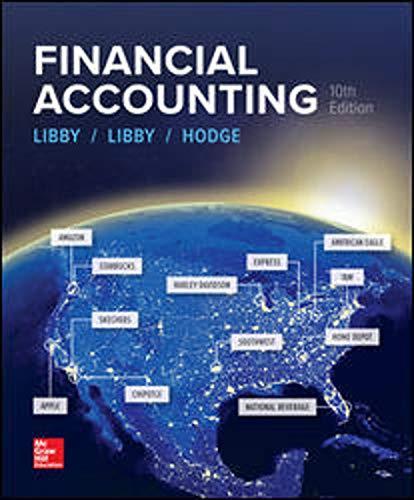
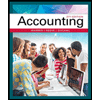
Accounting
Accounting
ISBN:9781337272094
Author:WARREN, Carl S., Reeve, James M., Duchac, Jonathan E.
Publisher:Cengage Learning,
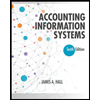
Accounting Information Systems
Accounting
ISBN:9781337619202
Author:Hall, James A.
Publisher:Cengage Learning,
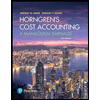
Horngren's Cost Accounting: A Managerial Emphasis...
Accounting
ISBN:9780134475585
Author:Srikant M. Datar, Madhav V. Rajan
Publisher:PEARSON
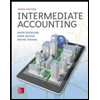
Intermediate Accounting
Accounting
ISBN:9781259722660
Author:J. David Spiceland, Mark W. Nelson, Wayne M Thomas
Publisher:McGraw-Hill Education
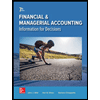
Financial and Managerial Accounting
Accounting
ISBN:9781259726705
Author:John J Wild, Ken W. Shaw, Barbara Chiappetta Fundamental Accounting Principles
Publisher:McGraw-Hill Education