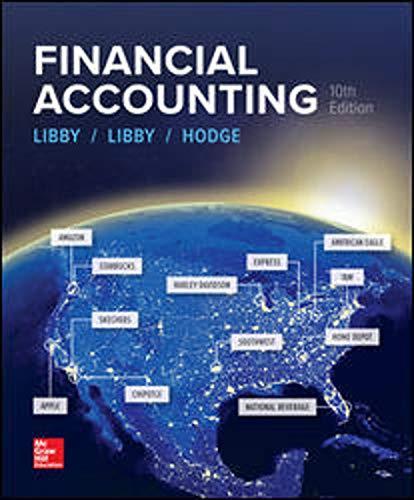
Concept explainers
I Love My Chocolate Company makes dark chocolate and light chocolate. Both products require cocoa and sugar. The following planning information has been made available:
Standard Amount per Case | ||||||
Dark Chocolate | Light Chocolate | Standard Price per Pound | ||||
Cocoa | 9 lbs. | 6 lbs. | $5.30 | |||
Sugar | 7 lbs. | 11 lbs. | 0.60 | |||
Standard labor time | 0.4 hr. | 0.5 hr. |
Dark Chocolate | Light Chocolate | |||
Planned production | 5,000 cases | 11,500 cases | ||
Standard labor rate | $14.50 per hr. | $14.50 per hr. |
I Love My Chocolate Company does not expect there to be any beginning or ending inventories of cocoa or sugar. At the end of the budget year, I Love My Chocolate Company had the following actual results:
Dark Chocolate | Light Chocolate | |||
Actual production (cases) | 4,800 | 12,000 | ||
Actual Price per Pound | Actual Pounds Purchased and Used | |||
Cocoa | $5.40 | 115,800 | ||
Sugar | 0.55 | 161,500 | ||
Actual Labor Rate | Actual Labor Hours Used | |||
Dark chocolate | $14.20 per hr. | 1,750 | ||
Light chocolate | 14.80 per hr. | 6,150 |
Required:
1. Prepare the following variance analyses for both chocolates and the total, based on the actual results and production levels at the end of the budget year:
a. Direct materials price variance, direct materials quantity variance, and total variance.
b. Direct labor rate variance, direct labor time variance, and total variance.
Enter a favorable variance as a negative number using a minus sign and an unfavorable variance as a positive number.
a. | Direct materials price variance | $fill in the blank 1 |
|
Direct materials quantity variance | $fill in the blank 3 |
|
|
Total direct materials cost variance | $fill in the blank 5 |
|
|
b. | Direct labor rate variance | $fill in the blank 7 |
|
Direct labor time variance | $fill in the blank 9 |
|
|
Total direct labor cost variance | $fill in the blank 11 |
|
2. The variance analyses should be based on the
amounts at
volumes. The budget must flex with the volume changes. If the
volume is different from the planned volume, as it was in this case, then the budget used for performance evaluation should reflect the change in direct materials and direct labor that will be required for the
production. In this way, spending from volume changes can be separated from efficiency and price variances.

Trending nowThis is a popular solution!
Step by stepSolved in 3 steps with 10 images

- Standard Amount per Case Dark Chocolate Light Chocolate Standard Price per Pound Cocoa 12 lbs. 8 lbs. $7.25 Sugar 10 lbs. 14 lbs. 1.40 Standard labor time 0.50 hr. 0.60 hr. Dark Chocolate Light Chocolate Planned production 4,700 cases 11,000 cases Standard labor rate $15.50 per hr. $15.50 per hr. I Love My Chocolate Company does not expect there to be any beginning or ending inventories of cocoa or sugar. At the end of the budget year, I Love My Chocolate Company had the following actual results: Dark Chocolate Light Chocolate Actual production (cases) 5,000 10,000 Actual Price per Pound Actual Pounds Purchased and Used Cocoa $7.33 140,300 Sugar 1.35 188,000 Actual Labor Rate Actual Labor Hours Used Dark chocolate $15.25 per hr. 2,360 Light chocolate 15.80 per hr. 6,120 this is all the information i have and i need help calulating the direct labor time variancearrow_forwardStandard Direct Materials Cost per Unit Roanoke Company produces chocolate bars. The primary materials used in producing chocolate bars are cocoa, sugar, and milk. The standard costs for a batch of chocolate (1,730 bars) are as follows: Ingredient Quantity Price Cocoa 570 lbs. $0.30 per lb. Sugar 180 lbs. $0.60 per lb. Milk 150 gal. $1.60 per gal. Determine the standard direct materials cost per bar of chocolate. If required, round to the nearest cent.arrow_forwardProvide answer of this questionarrow_forward
- Standard Direct Materials Cost per Unit Crazy Delicious Inc. produces chocolate bars. The primary materials used in producing chocolate bars are cocoa, sugar, and milk. The standard costs for a batch of chocolate (2,800 bars) are as follows: Ingredient Quantity Price Cocoa 540 lbs. $0.30 per lb. Sugar 150 lbs. $0.60 per lb. Milk 120 gal. $1.40 per gal. Determine the standard direct materials cost per bar of chocolate. If required, round to the nearest cent.$per bararrow_forward1.arrow_forwardQuestion 1) Crazy Delicious Inc. produces chocolate bars. The primary materials used in producing chocolate bars are cocoa, sugar, and milk. The standard cost for a batch of chocolate (2,880 bars) are as follows: Ingredient Quantity Price Cocoa 540lbs $0.30 per lb. Sugar 150lbs $0.60 per lb. Milk 120gal $1.50 per gal. Determine thte standard direct materials cost per bar of chocolate. If required, round to the nearest cent. $_______ per bar __________________________________________________________ Question 2) Refer to the picturearrow_forward
- Pick-Me-Up Company is introducing a new high caffeine coffee in its stores and must decide what price to set for the coffee beans. An estimated demand schedule for the product is as follows: Price 1 Lb. units demanded $4.50 85,600 $6.00 74,500 $7.50 56,000 $9.00 49,100 $10.50 34,800 $12.00 27,100 Estimated costs are as follows: Variable manufacturing costs per unit $1.50 Fixed manufacturing cost per year $38,200 Variable selling & administrative costs per unit $0.50 Fixed selling & administrative costs per year $20,900 Prepare a schedule showing management the total revenue, total cost, and total profit or loss for each selling price.At what price do you recommend Pick-Me-Up Company should choose.arrow_forwardStandard Direct Materials Cost per Unit Roanoke Company produces chocolate bars. The primary materials used in producing chocolate bars are cocoa, sugar, and milk. The standard costs for a batch of chocolate (2,600 bars) are as follows: Ingredient Quantity Price Cocoa 480 Ibs. $0.30 per Ib. Sugar 150 Ibs. $0.60 per Ib. Milk 120 gal. $1.30 per gal. Determine the standard direct materials cost per bar of chocolate. If required, round to the nearest cent. per bararrow_forwardTropikal Co makes fizzy drinks. One of its products, the Opop, requires the following standard input for a litre of output: Materials Litres Cost per litre ($) ($) Carbonated water 1.50 0.90 0.6 0.3 Flavoured syrup 2.00 0.60 Sugar water 0.3 0.80 0.24 1.2 1.74 During June, 6,000 litres of the Opop were made and sold using the following inputs: Materials Actual litres used Actual cost per litre ($) Carbonated water 3,800 1.40 Flavoured syrup 1,400 2.10 Sugar water 1,500 0.95 6,700 What was the favourable yield variance for the Opop for June? Select... V Select... $725 $740 $15 $732arrow_forward
- AccountingAccountingISBN:9781337272094Author:WARREN, Carl S., Reeve, James M., Duchac, Jonathan E.Publisher:Cengage Learning,Accounting Information SystemsAccountingISBN:9781337619202Author:Hall, James A.Publisher:Cengage Learning,
- Horngren's Cost Accounting: A Managerial Emphasis...AccountingISBN:9780134475585Author:Srikant M. Datar, Madhav V. RajanPublisher:PEARSONIntermediate AccountingAccountingISBN:9781259722660Author:J. David Spiceland, Mark W. Nelson, Wayne M ThomasPublisher:McGraw-Hill EducationFinancial and Managerial AccountingAccountingISBN:9781259726705Author:John J Wild, Ken W. Shaw, Barbara Chiappetta Fundamental Accounting PrinciplesPublisher:McGraw-Hill Education
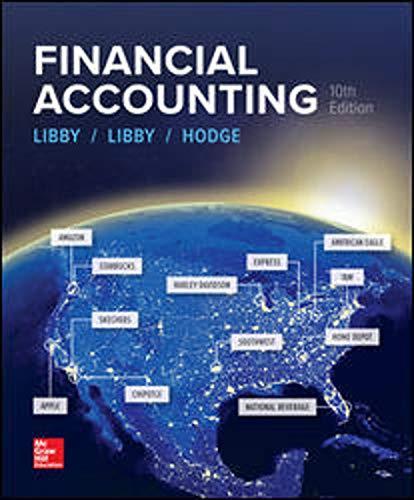
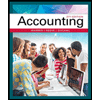
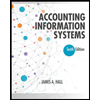
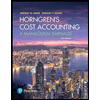
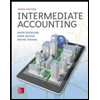
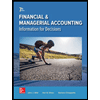