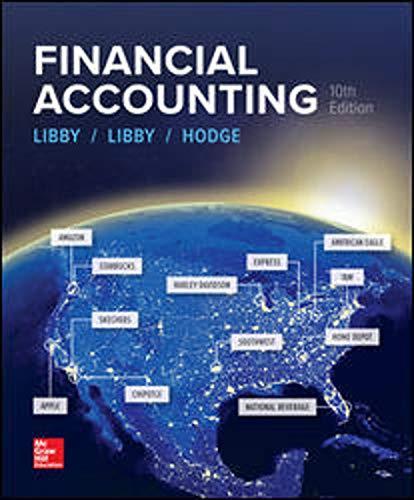
Concept explainers
PLEASE SEE ATTACHED, please answer all questions.
Required:
a. Recompute the unit costs for each of the cola products: Diet, Regular, Cherry, and Grape.
b. What is the cost of unused capacity?
c. Now assume that Rockness is considering producing a fifth product: Vanilla cola. Because Vanilla cola is in high demand in Rockness Bottling’s market, assume that it would use 20,200 hours of machine time to make 202,000 units. (Recall that the machine capacity in this case is 40,400 hours, while Diet, Regular, Cherry, and Grape consume only 20,200 hours.) Vanilla cola’s per unit costs would be identical to those of Diet cola except for the machine usage costs. What would be the cost of Vanilla cola? Calculate on a per-unit basis, and then in total.
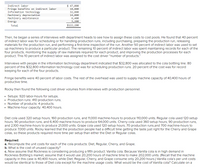
![Howard Rockness was worried. His company, Rockness Bottling, showed declining profits over the past several years despite an
increase in revenues. With profits declining and revenues increasing, Rockness knew there must be a problem with costs.
Rockness sent an e-mail to his executive team under the subject heading, “How do we get Rockness Bottling back on track?" Meeting
in Rockness's spacious office, the team began brainstorming solutions to the declining profits problem. Some members of the team
wanted to add products. (These were marketing people.) Some wanted to fire the least efficient workers. (These were finance people.)
Some wanted to empower the workers. (These people worked in the human resources department.) And some people wanted to
install a new computer system. (It should be obvious who these people were.)
Rockness listened patiently. When all participants had made their cases, Rockness said, "We made money when we were a smaller,
simpler company. We have grown, added new product lines, and added new products to old product lines. Now we are going
downhill. What's wrong with this picture?"
Rockness continued, "Here, look at this report. This is last month's report on the cola bottling line. What do you see here?" He handed
copies of the following report to the people assembled in his office.
Monthly Report on Cola Bottling Line
Diet
$297,000
Regular
$172, 800
Cherry
$57,750
Total
Grape
$19,950
Sales
$547,500
Less:
91, 200
14,000
5,600
36,400
$ 25,600
14.8%
64, 000
31,920
4,200
1,680
Materials
141,000
28,000
11, 200
13,250
277,370
Direct labor
800
47,000
Fringe benefits on direct labor
Indirect costs (@260% of direct labor)
Gross margin
Return on sales (see note [a])
Volume
320
18,800
72,800
$ 44, 000
10,920
$ 9,030
15.6%
2,080
$ 3,500
122, 200
$ 82,130
14.8%
110,000
$4
17.5%
15.0%
Unit price
Unit cost
21,000
$ 2.75
7,000
$ 2.85
202,000
%24
$4
2.70
2.70
2.71
2.30
2$
2.30
$4
2.32
$4
2.35
2.30
a Return on sales before considering selling, general and administrative expenses.
Rockness asked, "Do you see any problems here? Should we drop any of these products? Should we reprice any of these products?"
The room was silent for a moment, and then everybody started talking at once. Nobody could see any problems based on the data in
the report, but they all made suggestions to Rockness ranging from "add another cola product" to "cut costs across the board" to "we
need a new computer system so that managers can get this information more quickly." A not-so-patient Rockness stopped the
discussion abruptly and adjourned the meeting.
He then turned to the quietest person in the room-his son, Rocky-and said, "I am suspicious of these cost data, Rocky. Here we are
assigning indirect costs to these products using a 260 percent rate. I really wonder whether that rate is accurate for all products. I want
you to dig into the indirect cost data, figure out what drives those costs, and see whether you can give me more accurate cost
numbers for these products."
Rocky first learned from production that the process required four activities: (1) setting up production runs, (2) managing production
runs, and (3) managing products. The fourth activity did not require labor; it was simply the operation of machinery. Next, he went to
the accounting records to get a breakdown of indirect costs. Here is what he found:](https://content.bartleby.com/qna-images/question/61ae5430-25ae-4fd0-9dbe-872050663ccf/5fc7ec7b-d062-447a-aa05-a75bc4bd06b7/k450vv_thumbnail.png)

Trending nowThis is a popular solution!
Step by stepSolved in 3 steps with 6 images

- Waterways is thinking of mass-producing one of its special-order sprinklers. To do so would increase unit variable costs for all sprinklers by an average of $0.70. The company also estimates that this change could increase the overall number of sprinklers sold by 10%, and the average unit sales price would increase $0.20. Waterways currently sells 490.000 sprinkler units at an average unit selling price of $28.60. The manufacturing costs are $7,866,260 variable and $2.011,486 fixed. Selling and administrative costs are $2,644.240 variable and $809,370 fixed. If Waterways begins mass-producing its special-order sprinklers, how would this affect the company? (Round ratio answers to O decimal places, e.g. 5X and net income answers to 2 decimal places, e.g. 5,275.25.) Contribution margin ratio Net income Current New % Effect Decrease Increase eTextbook and Media Save for Later Attempts: unlimited Submit Answerarrow_forwardAnswer the following questions. Required 1. Deibler Computers makes 5,600 units of a circuit board, CB76, at a cost of $210 each. Variable cost per unit is $150, and fixed cost per unit is $60. HT Electronics offers to supply 5,600 units of CB76 for $185. If Deibler buys from HT, it will be able to save $25 per unit of fixed costs but continue to incur the remaining $35 per unit. Should Deibler accept HT's offer? Explain. 2. QT Manufacturing is deciding whether to keep or replace an old machine. It obtains the following information: (Click the icon to view the information.) QT Manufacturing uses straight-line depreciation. Ignore the time value of money and income taxes. Should QT replace the old machine? Explain. A Requirement 1. Deibler Computers makes 5,600 units of a circuit board, CB76, at a cost of $210 each. Variable cost per unit is $150, and fixed cost per unit is $60. HT Electronics offers to supply 5,600 units of CB76 for $185. If Deibler buys from HT, it will be able to…arrow_forwardSagararrow_forward
- The Dairy Division of Concord Corporation produces and sells milk to outside customers. The operation has the capacity to produce 200000 gallons of milk a year. Last year’s operating results were as follows: Sales (150000) gallons $675000 Variable costs 292500 Contribution margin 382500 Fixed costs 100000 Net Income $ 282500 Assume the Dairy Division is operating at capacity. If the Yogurt Division wants to purchase 40000 gallons of milk from the Dairy Division, what is the minimum price that will allow the Dairy Division to maintain its current net income? $1.88 per gallon $4.50 per gallon $1.95 per gallon $2.55 per gallonarrow_forwardDivision X makes a part with the following characteristics: Production capacity.. 25,000 units $18 Selling price to outside customers. Variable cost per unit. $11 Fixed cost, total. $100,000 Division Y of the same company would like to purchase 10,000 units each period from Division X. Division Y now purchases the part from an outside supplier at a price of $17 each. Suppose that Division X is operating at capacity and can sell all of its output to outside customers. If Division X sells the parts to Division Y at $17 per unit, the company as a whole will be: Select one: a. better off by $10,000 each period. b. worse off by $20,000 each period. C. worse off by $10,000 each period. d. There will be no change in the status of the company as a whole.arrow_forwardWhitmore Glassware makes a variety of drinking glasses and mugs. The company's designers have discovered a market for a 16 ounce mug with college logos. Market research indicates that a mug like this would sell well in the market priced at $26.65. Whitmore only introduces a product if they can an operating profit of 30 percent of costs. Required: What is the highest acceptable manufacturing cost for which Whitmore would be willing to produce the mugs? (Round your answer to 2 decimal places.) Highest acceptable manufacturing costsarrow_forward
- Caspian Sea Drinks is considering the purchase of a plum juicer – the PJX5. There is no planned increase in production. The PJX5 will reduce costs by squeezing more juice from each plum and doing so in a more efficient manner. Mr. Bensen gave Derek the following information. What is the NPV of the PJX5? (ROUND TO 2 DECIMAL PLACES.) a. The PJX5 will cost $1.83 million fully installed and has a 10 year life. It will be depreciated to a book value of $284,956.00 and sold for that amount in year 10. b. The Engineering Department spent $44,242.00 researching the various juicers. c. Portions of the plant floor have been redesigned to accommodate the juicer at a cost of $20,794.00. d. The PJX5 will reduce operating costs by $438,196.00 per year. e. CSD’s marginal tax rate is 27.00%. f. CSD is 63.00% equity-financed. g. CSD’s 16.00-year, semi-annual pay, 5.71% coupon bond sells for $958.00. h. CSD’s stock currently has a market value of $24.35 and Mr. Bensen believes the market estimates that…arrow_forwardSandy Bank, Incorporated, makes one model of wooden canoe. Partial information is given below. Required: 1. Complete the following table. 2. Suppose Sandy Bank sells its canoes for $540 each. Calculate the contribution margin per canoe and the contribution margin ratio. 3. This year Sandy Bank expects to sell 760 canoes for $540 each. Prepare a contribution margin income statement for the company. 4. Calculate Sandy Bank's break-even point in units and in sales dollars. Sandy Bank sells its canoes for $540 each. 5. Suppose Sandy Bank wants to earn $76,000 profit this year. Calculate the number of canoes that must be sold to achieve this target. Sandy Bank sells its canoes for $540 each. Complete this question by entering your answers in the tabs below. Required 1 Required 2 Required 3 Required 4 Required 5 This year Sandy Bank expects to sell 760 canoes for $540 each. Prepare a contribution margin income statement for the company. Note: Round your intermediate calculations to 2 decimal…arrow_forwardBroomfield Corp. has 1,000 carton of oranges that cost $50 per carton in direct costs and $26.50 per carton in indirect costs and sold for $70 per carton. The oranges can be processed further into orange juice at an additional cost of $22.50 and sold at a price of $126. The incremental income (loss) from processing the oranges into orange juice would be: Multiple Choice ($100,500). $103,500. $92,500. $100,500. $93,500.arrow_forward
- AccountingAccountingISBN:9781337272094Author:WARREN, Carl S., Reeve, James M., Duchac, Jonathan E.Publisher:Cengage Learning,Accounting Information SystemsAccountingISBN:9781337619202Author:Hall, James A.Publisher:Cengage Learning,
- Horngren's Cost Accounting: A Managerial Emphasis...AccountingISBN:9780134475585Author:Srikant M. Datar, Madhav V. RajanPublisher:PEARSONIntermediate AccountingAccountingISBN:9781259722660Author:J. David Spiceland, Mark W. Nelson, Wayne M ThomasPublisher:McGraw-Hill EducationFinancial and Managerial AccountingAccountingISBN:9781259726705Author:John J Wild, Ken W. Shaw, Barbara Chiappetta Fundamental Accounting PrinciplesPublisher:McGraw-Hill Education
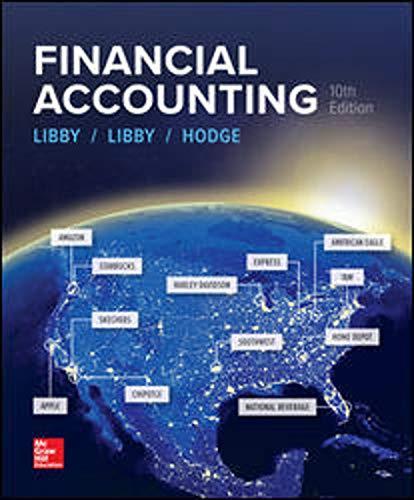
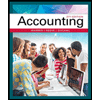
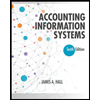
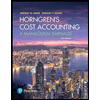
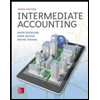
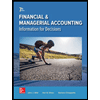