How do I develop a process map for the following scenario? Since arriving at LFP, Tim could not help but feel that there were too many “diamonds in the rough” to ignore. Typical was the process for making the taillight assembly for the Dodge Ram, one of the best-selling trucks in the market. The process began with the back plate. This was a long black piece of extruded ABS plastic (produced in another part of the plant) that contained two concave depressions—one for the turn light and one for the backup light. These were withdrawn from a temporary storage location found near the assembly line. Each back plate was first checked for cosmetic defects. Those that failed this step were placed in a bin where they were eventually used as a source of raw material for regrinds. Any plate passing this test was placed in a metalization chamber, where nickel metal particles were sprayed on using a high-pressure water-based system. Because of the nature of the process, only half of the material ever reached the back plate. The rest either fell to the bottom of the chamber or was vented out. Periodically, the chamber had to be taken off-line and cleaned out. This process took 1 to 2 days and effectively shut down production of this taillight. After the parts were metalized, they were removed from the chamber and checked for completeness and evenness of the coverage. Any rejected parts were place in a bin. Because of the presence of the metal coating, the back plate could not be recycled, so it had to be landfilled. The accepted parts went into a rack where they waited for the arrival of lenses from a supplier. A plastic-wrapped film covered the lenses. Each lens, as it arrived from the supplier, was checked for surface flaws. Any rejected lenses were then put into a recycle bin, where they were used as inputs for any parts requiring low-grade black plastic. The next step in the process was mating. At this stage, each lens was mated to a black plate. This was accomplished by placing the back plate and the lens into two fixtures. These fixtures were then fed into an automated gluing machine. The machine placed a bead of glue on the lens, waited for 10 seconds and then placed the lens onto the back plate. Periodically, the gluing machine had to be purged and cleaned. This was typically done twice a shift, each instance required 30 minutes. This process was fairly messy and required several globs of glue to be expressed through the nozzle. After this was done, the last glob of glue was then expressed, and the nozzle was removed. The machine had four nozzles. The residual glue and nozzles were then thrown into an old 55-gallon barrel. Because this barrel was used as a receptacle for all sorts of scrap (including floor sweepings and cigarette butts), the only disposal option was a landfill. After mating, the back-light assembly was next tested for leaks. Placing the body into a tank of water and then shooting a burst of air through it completed the testing. Again, any assemblies that failed this test were put into a bin for eventual disposal in a landfill site. Those that passed this stage next proceeded to the finishing assembly. It was here that two lightbulb assemblies were first made. These assemblies required one receiver and one lightbulb each. Both the receiver and the lightbulbs were provided by outside suppliers. After they were assembled, the assemblies were inserted into the appropriate holes in the car body. The light assembly was then inspected for performance and surface blemishes. Any problem assemblies were put aside for rework. Those that could not be reworked were set aside for disposal (again landfilled). The remaining “good” assemblies were packed into a cardboard box and shipped out to the Dodge Ram assembly plant. The current practice at LFP was to allocate the total production cost to the number of good assemblies produced. By working with the material requirements planning system at LFP, Tim and others were able to track the following costs associated with waste in the process. For the tail-light assemblies, the line produced 3,600 per shift. Labor and overhead costs were considered to be fixed.
How do I develop a process map for the following scenario?
Since arriving at LFP, Tim could not help but feel that there were too many “diamonds in the rough” to ignore. Typical was the process for making the taillight assembly for the Dodge Ram, one of the best-selling trucks in the market. The process began with the back plate. This was a long black piece of extruded ABS plastic (produced in another part of the plant) that contained two concave depressions—one for the turn light and one for the backup light. These were withdrawn from a temporary storage location found near the assembly line. Each back plate was first checked for cosmetic defects. Those that failed this step were placed in a bin where they were eventually used as a source of raw material for regrinds. Any plate passing this test was placed in a metalization chamber, where nickel metal particles were sprayed on using a high-pressure water-based system. Because of the nature of the process, only half of the material ever reached the back plate. The rest either fell to the bottom of the chamber or was vented out. Periodically, the chamber had to be taken off-line and cleaned out. This process took 1 to 2 days and effectively shut down production of this taillight.
After the parts were metalized, they were removed from the chamber and checked for completeness and evenness of the coverage. Any rejected parts were place in a bin. Because of the presence of the metal coating, the back plate could not be recycled, so it had to be landfilled. The accepted parts went into a rack where they waited for the arrival of lenses from a supplier. A plastic-wrapped film covered the lenses. Each lens, as it arrived from the supplier, was checked for surface flaws. Any rejected lenses were then put into a recycle bin, where they were used as inputs for any parts requiring low-grade black plastic.
The next step in the process was mating. At this stage, each lens was mated to a black plate. This was accomplished by placing the back plate and the lens into two fixtures. These fixtures were then fed into an automated gluing machine. The machine placed a bead of glue on the lens, waited for 10 seconds and then placed the lens onto the back plate. Periodically, the gluing machine had to be purged and cleaned. This was typically done twice a shift, each instance required 30 minutes. This process was fairly messy and required several globs of glue to be expressed through the nozzle. After this was done, the last glob of glue was then expressed, and the nozzle was removed. The machine had four nozzles. The residual glue and nozzles were then thrown into an old 55-gallon barrel. Because this barrel was used as a receptacle for all sorts of scrap (including floor sweepings and cigarette butts), the only disposal option was a landfill.
After mating, the back-light assembly was next tested for leaks. Placing the body into a tank of water and then shooting a burst of air through it completed the testing. Again, any assemblies that failed this test were put into a bin for eventual disposal in a landfill site. Those that passed this stage next proceeded to the finishing assembly. It was here that two lightbulb assemblies were first made. These assemblies required one receiver and one lightbulb each. Both the receiver and the lightbulbs were provided by outside suppliers. After they were assembled, the assemblies were inserted into the appropriate holes in the car body. The light assembly was then inspected for performance and surface blemishes. Any problem assemblies were put aside for rework. Those that could not be reworked were set aside for disposal (again landfilled). The remaining “good” assemblies were packed into a cardboard box and shipped out to the Dodge Ram assembly plant.
The current practice at LFP was to allocate the total production cost to the number of good assemblies produced. By working with the material requirements planning system at LFP, Tim and others were able to track the following costs associated with waste in the process. For the tail-light assemblies, the line produced 3,600 per shift. Labor and overhead costs were considered to be fixed.

Trending now
This is a popular solution!
Step by step
Solved in 2 steps with 1 images

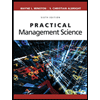
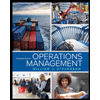
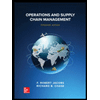
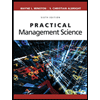
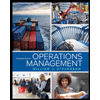
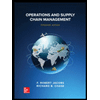
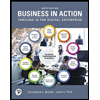
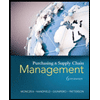
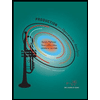