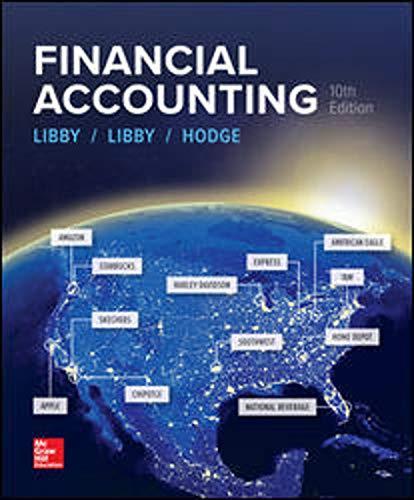
FINANCIAL ACCOUNTING
10th Edition
ISBN: 9781259964947
Author: Libby
Publisher: MCG
expand_more
expand_more
format_list_bulleted
Question
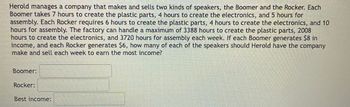
Transcribed Image Text:Herold manages a company that makes and sells two kinds of speakers, the Boomer and the Rocker. Each
Boomer takes 7 hours to create the plastic parts, 4 hours to create the electronics, and 5 hours for
assembly. Each Rocker requires 6 hours to create the plastic parts, 4 hours to create the electronics, and 10
hours for assembly. The factory can handle a maximum of 3388 hours to create the plastic parts, 2008
hours to create the electronics, and 3720 hours for assembly each week. If each Boomer generates $8 in
income, and each Rocker generates $6, how many of each of the speakers should Herold have the company
make and sell each week to earn the most income?
Boomer:
Rocker:
Best income:
SAVE
AI-Generated Solution
info
AI-generated content may present inaccurate or offensive content that does not represent bartleby’s views.
Unlock instant AI solutions
Tap the button
to generate a solution
to generate a solution
Click the button to generate
a solution
a solution
Knowledge Booster
Similar questions
- sarrow_forwardTalbot Industries manufactures two models of wireless headset: TI-12 and TI-28. Each product requires time on a single machine. The machine has a monthly capacity of 540 hours. Total market demand for the two products is limited to 2,000 units of TI-12 and 1,000 units of TI-28 monthly. Talbot is currently producing and selling 1,500 TI-12 models and 780 TI-28 models each month. Cost and machine-usage data for the two products are shown in the following spreadsheet, which analysts at Talbot use for production planning purposes: Price Less variable costs per unit Material Labor Overhead Contribution margin per unit Fixed costs Manufacturing Marketing and administrative Machine hours per unit Machine hours used Machine hours available Quantity produced Maximum demand Profit TI-12 $ 80 Required A Required B 23 29 8 $ 20 0.1arrow_forwardIPort Products makes cases for portable music players in two processes, cutting and sewing. The cutting process has a capacity of 115,000 units per year; sewing has a capacity of 150,000 units per year. Cost information follows. Inspection and testing costs $ 47,500 Scrap costs (all in the cutting dept.) 147,500 Demand is very strong. At a sales price of $15.00 per case, the company can sell whatever output it can produce. IPort Products can start only 115,000 units into production in the Cutting Department because of capacity constraints. Defective units are detected at the end of production in the Cutting Department. At that point, defective units are scrapped. Of the 115,000 units started at the cutting operation, 17,250 units are scrapped. Unit costs in the Cutting Department for both good and defective units equal $11.30 per unit, including an allocation of the total fixed manufacturing costs of $264,500 per year to units. Direct…arrow_forward
- Crede Inc. has two divisions. Division A makes and sells student desks. Division B manufactures and sells reading lamps. Each desk has a reading lamp as one of its components. Division A can purchase reading lamps at a cost of $10.10 from an outside vendor. Division A needs 11,100 lamps for the coming year. Division B has the capacity to manufacture 49,600 lamps annually. Sales to outside customers are estimated at 38,500 lamps for the next year. Reading lamps are sold at $12.09 each. Variable costs are $6.87 per lamp and include $1.41 of variable sales costs that are not incurred if lamps are sold internally to Division A. The total amount of fixed costs for Division B is $75,900. Consider the following independent situations. What should be the minimum transfer price accepted by Division B for the 11,100 lamps and the maximum transfer price paid by Division A? (Round answers to 2 decimal places, e.g. 15.25.) Per unit Minimum transfer price accepted by Division B $_ Maximum transfer…arrow_forwardCarlton’s Kitchens makes two types of pasta makers: Strands and Shapes. The company expects to manufacture 70,000 units of Strands, which has a per-unit direct material cost of $10 and a per-unit direct labor cost of $60. It also expects to manufacture 30,000 units of Shapes, which has a per-unit material cost of $15 and a per-unit direct labor cost of $40. It is estimatedthat Strands will use 140,000 machine hours and Shapes will require 60,000 machine hours. Historically, the company has used the traditional allocation method and applied overhead at a rate of $21 per machine hour. It was determined that there were three cost pools, and the overhead for each cost pool is shown: A. What is the per-unit cost for each product under the traditional allocation method?B. What is the per-unit cost for each product under ABC costing?arrow_forwardTalbot Industries manufactures two models of wireless headset: TI-12 and TI-28. Each product requires time on a single machine. The machine has a monthly capacity of 540 hours. Total market demand for the two products is limited to 2,000 units of TI-12 and 1,000 units of TI-28 monthly. Talbot is currently producing and selling 1,500 TI-12 models and 780 TI-28 models each month. Cost and machine-usage data for the two products are shown in the following spreadsheet, which analysts at Talbot use for production planning purposes: Price Less variable costs per unit Material Labor Overhead Contribution margin per unit Fixed costs Manufacturing Marketing and administrative Machine hours per unit Machine hours used Machine hours available Quantity produced Maximum demand Profit Required A Required B TI-12 Model TI-28 Model TI-12 $ 80 23 29 8 $ 20 units units 0.1arrow_forward
- .arrow_forwardTrident Ltd makes designer gold bracelets. Their annual costs include shop rent of $12,500, salaries for two jewellers of $118,000, design software costs of $10,000, and other overhead costs of $13,000. An average bracelet is priced at $5,500. It costs $2,000 in raw material, $1,250 in labour, and $250 in other expenses. What is the minimum number of bracelets that need to be sold to earn a profit? a.28 b. 44 c. 77 d. 17arrow_forwardThe Wolverine Corporation is working at full production capacity producing 9,000 units of a unique product, Everlast. Manufacturing cost per unit for Everlast is as follows: (Click the icon to view the cost per unit information.) A customer, the Apex Company, has asked Wolverine to produce 3,500 units of Stronglast, a modification of Everlast. Stronglast would require the same manufacturing processes as Everlast. Apex has offered to pay Wolverine $31 for a unit of Stronglast plus half of the marketing cost per unit. Read the requirements. Requirement 1. What is the opportunity cost to Wolverine of producing the 3,500 units of Stronglast? (Assume that no overtime is worked.) Determine the formula for calculating the opportunity cost, then calculate the opportunity cost of producing the 3,500 units of Stronglast Selling price per unit Total variable cost per unit Units 3,500 38 $ 20 ( ($ Selling price per unit Total variable cost per unit Contribution margin per unit Contribution margin…arrow_forward
arrow_back_ios
arrow_forward_ios
Recommended textbooks for you
- AccountingAccountingISBN:9781337272094Author:WARREN, Carl S., Reeve, James M., Duchac, Jonathan E.Publisher:Cengage Learning,Accounting Information SystemsAccountingISBN:9781337619202Author:Hall, James A.Publisher:Cengage Learning,
- Horngren's Cost Accounting: A Managerial Emphasis...AccountingISBN:9780134475585Author:Srikant M. Datar, Madhav V. RajanPublisher:PEARSONIntermediate AccountingAccountingISBN:9781259722660Author:J. David Spiceland, Mark W. Nelson, Wayne M ThomasPublisher:McGraw-Hill EducationFinancial and Managerial AccountingAccountingISBN:9781259726705Author:John J Wild, Ken W. Shaw, Barbara Chiappetta Fundamental Accounting PrinciplesPublisher:McGraw-Hill Education
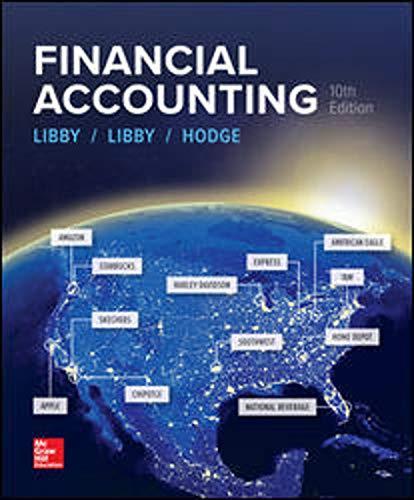
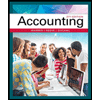
Accounting
Accounting
ISBN:9781337272094
Author:WARREN, Carl S., Reeve, James M., Duchac, Jonathan E.
Publisher:Cengage Learning,
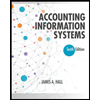
Accounting Information Systems
Accounting
ISBN:9781337619202
Author:Hall, James A.
Publisher:Cengage Learning,
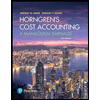
Horngren's Cost Accounting: A Managerial Emphasis...
Accounting
ISBN:9780134475585
Author:Srikant M. Datar, Madhav V. Rajan
Publisher:PEARSON
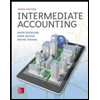
Intermediate Accounting
Accounting
ISBN:9781259722660
Author:J. David Spiceland, Mark W. Nelson, Wayne M Thomas
Publisher:McGraw-Hill Education
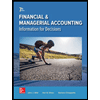
Financial and Managerial Accounting
Accounting
ISBN:9781259726705
Author:John J Wild, Ken W. Shaw, Barbara Chiappetta Fundamental Accounting Principles
Publisher:McGraw-Hill Education