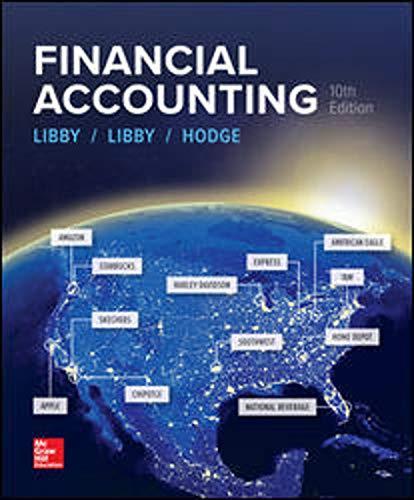
FINANCIAL ACCOUNTING
10th Edition
ISBN: 9781259964947
Author: Libby
Publisher: MCG
expand_more
expand_more
format_list_bulleted
Question
Helmer Containers manufactures a variety of boxes used for packaging. Sales of its Model A20 box have increased significantly to a total of 460,000 A20 boxes. Helmer has enough existing production capacity to make all of the boxes it needs. The variable cost of making each A20 box is $0.82.By outsourcing the manufacture of these A20 boxes, Helmer can reduce its current fixed costs by $115,000. There is no alternative use for the factory space freed up through outsourcing, so it will just remain idle.
What is the maximum Helmer will pay per Model A20 box to outsource production of this box?
Expert Solution

This question has been solved!
Explore an expertly crafted, step-by-step solution for a thorough understanding of key concepts.
This is a popular solution
Trending nowThis is a popular solution!
Step by stepSolved in 3 steps

Knowledge Booster
Similar questions
- Futura Company purchases the 67,000 starters that it installs in its standard line of farm tractors from a supplier for the price of $11.30 per unit. Due to a reduction in output, the company now has idle capacity that could be used to produce the starters rather than buying them from an outside supplier. However, the company's chief engineer is opposed to making the starters because the production cost per unit is $12.00 as shown below: Direct materials Direct labor Supervision Depreciation Variable manufacturing overhead Rent Total product cost Per Unit $ 5.00 3.20 1.60 1.20 0.60 0.40 $ 12.00 Total $ 107,200 $ 80,400 $ 26,800 If Futura decides to make the starters, a supervisor would have to be hired (at a salary of $107,200) to oversee production. However, the company has sufficient idle tools and machinery such that no new equipment would have to be purchased. The rent charge above is based on space utilized in the plant. The total rent on the plant is $87,000 per period.…arrow_forwardFutura Company purchases the 76,000 starters that it installs in its standard line of farm tractors from a supplier for the price of $12.60 per unit. Due to a reduction in output, the company now has idle capacity that could be used to produce the starters rather than buying them from an outside supplier. However, the company's chief engineer is opposed to making the starters because the production cost per unit is $13.70 as shown below: Direct materials Direct labor Supervision Depreciation Variable manufacturing overhead Rent Total product cost Per Unit $ 6.00 3.50 1.80 1.40 0.60 0.40 $ 13.70 Financial advantage Total $ 221,600 $ 136,800 $ 106,400 If Futura decides to make the starters, a supervisor would have to be hired (at a salary of $136,800) to oversee production. However, the company has sufficient idle tools and machinery such that no new equipment would have to be purchased. The rent charge above is based on space utilized in the plant. The total rent on the plant is $86,000…arrow_forwardMemanarrow_forward
- Futura Company purchases the 66,000 starters that it installs in its standard line of farm tractors from a supplier for the price of $10.50 per unit. Due to a reduction in output, the company now has idle capacity that could be used to produce the starters rather than buying them from an outside supplier. However, the company's chief engineer is opposed to making the starters because the production cost per unit is $11.40 as shown below: Direct materials Direct labor Supervision Depreciation Variable manufacturing overhead Rent Total product cost Per Unit $ 4.00 3.50 1.90 1.10 0.50 0.40 $11.40 Total $ 125,400 $ 72,600 $ 26,400 If Futura decides to make the starters, a supervisor would have to be hired (at a salary of $125,400) to oversee production. However, the company has sufficient idle tools and machinery such that no new equipment would have to be purchased. The rent charge above is based on space utilized in the plant. The total rent on the plant is $88,000 per period.…arrow_forwardVaughn Music produces 60800 blank CDs on which to record music. The CDs have the following costs Direct Materials $10600 Direct Labour 14800 Variable Overhead 2800 Fixed Overhead 6800 None of Vaughni's foxed overhead costs can be reduced, but another product could be made that would increase the operating income by $4400 if the CDs were acquired externally If cost minimization is the major consideration and the company would prefer to buy the CDs, what is the maximum external price that Vaughn would be willing to accept to acquire the 60800 units externallyarrow_forwardAdams Bicycle Manufacturing Company currently produces the handlebars used in manufacturing its bicycles, which are high-quality racing bikes with limited sales. Adams produces and sells only 6,200 bikes each year. Due to the low volume of activity, Adams is unable to obtain the economies of scale that larger producers achieve. For example, Adams could buy the handlebars for $30 each; they cost $33 each to make. The following is a detailed breakdown of current production costs. Item Unit-level costs Materials Labor Overhead Allocated facility-level costs Total Unit Cost $15 9 2 7 $33 Total $ 93,000 55,800 12,400 43,400 $204,600 After seeing these figures, Adams's president remarked that it would be foolish for the company to continue to produce the handlebars at $33 each when it can buy them for $30 each. Required Calculate the total relevant cost. Do you agree with the president's conclusion? Answer is complete but not entirely correct. Per Unit Totalarrow_forward
- The Croydon division of CC Industries supplies the Hauser division with 100,000 units per month of an infrared LED that Hauser uses in a remote control device it sells. The transfer price of the LED is $8, which is the market price. However, Croydon does not operate at or near capacity. The variable cost to Croydon of the LED is $4.80, while Hauser incurs variable costs (excluding the transfer price) of $12 for each remote control. Hauser’s selling price is $32. Hauser’s manager is considering a promotional campaign. The market research department of Hauser has developed the following estimates of additional monthly volume associated with additional monthly promotional expenses. Additional Monthly Promotional Expenses: $80,000 $120,000 $160,000 Additional Monthly Volume (Units) 10,000 15,000 18,000 Q. As the president of CC Industries, what level of spending would you like the Hauser division manager to select?arrow_forwardSweet Acacia Inc. makes unfinished bookcases that it sells for $58. Production costs are $38 variable and $9 fixed. Because it has unused capacity, Sweet Acacia is considering finishing the bookcases and selling them for $72. Variable finishing costs are expected to be $7 per unit with no increase in fixed costs. Prepare an analysis on a per-unit basis that shows whether Sweet Acacia should sell unfinished or finished bookcases. (If an amount reduces the net income then enter with a negative sign preceding the number, e.g. -15,000 or parenthesis, e.g. (15,000).) Sales per unit Variable cost per unit Fixed cost per unit Total per unit cost Net income per unit The bookcases 69 $ Sell ✓processed further. LA GA Process Further $ $ Net Income Increase (Decrease)arrow_forwardCox Electric makes electronic components and has estimated the following for a new design of one of its products. Fixed cost = $23,750 • Material cost per unit = $0.17 • Labor cost per unit = $0.11 • Revenue per unit = $0.66 Note that fixed cost is incurred regardless of the amount produced. Per-unit material and labor cost together make up the variable cost per unit. Assuming that Cox Electric sells all that it produces, profit is calculated by subtracting the fixed cost and total variable cost from total revenue. Construct an appropriate spreadsheet model to find the profit based on a given production level and use the spreadsheet model to answer these questions. (a) Construct a one-way data table with production volume as the column input and profit as the output. Breakeven occurs when profit goes from a negative to a positive value; that is, breakeven is when total revenue = the total cost, yielding a profit of zero. Vary production volume from 0 to 100,000 in increments of 10,000.…arrow_forward
- Futura Company purchases the 71,000 starters that it installs in its standard line of farm tractors from a supplier for the price of $13.00 per unit. Due to a reduction in output, the company now has idle capacity that could be used to produce the starters rather than buying them from an outside supplier. However, the company's chief engineer is opposed to making the starters because the production cost per unit is $14.20 as shown below: Direct materials Direct labor Supervision Depreciation Variable manufacturing overhead Rent Total product cost Per Unit Total $ 7.00 3.00 B 1.90 $ 134,900 1.40 $ 99,400 0.50 0.40 $ 28,400 $14.20 If Futura decides to make the starters, a supervisor would have to be hired (at a salary of $134,900) to oversee production. However, the company has sufficient idle tools and machinery such that no new equipment would have to be purchased. The rent charge above is based on space utilized in the plant. The total rent on the plant is $82,000 per period.…arrow_forwardBlue Spruce Tech produces 60,000 iPhone adapters with the following costs:arrow_forwardCampbell Bicycle Manufacturing Company currently produces the handlebars used in manufacturing its bicycles, which are high- quality racing bikes with limited sales. Campbell produces and sells only 7,700 bikes each year. Due to the low volume of activity, Campbell is unable to obtain the economies of scale that larger producers achieve. For example, Campbell could buy the handlebars for $33 each; they cost $36 each to make. The following is a detailed breakdown of current production costs. Item Unit Cost Total Unit-level costs $13 $100, 100 92,400 23,100 61,600 Materials Labor 12 Overhead Allocated facility-level costs 8 Total $36 $277,200 After seeing these figures, Campbell's president remarked that it would be foolish for the company to continue to produce the handlebars at $36 each when it can buy them for $33 each. Required Calculate the total relevant cost. Do you agree with the president's conclusion? Per Unit Total Total relevant cost Do you agree with the president's…arrow_forward
arrow_back_ios
SEE MORE QUESTIONS
arrow_forward_ios
Recommended textbooks for you
- AccountingAccountingISBN:9781337272094Author:WARREN, Carl S., Reeve, James M., Duchac, Jonathan E.Publisher:Cengage Learning,Accounting Information SystemsAccountingISBN:9781337619202Author:Hall, James A.Publisher:Cengage Learning,
- Horngren's Cost Accounting: A Managerial Emphasis...AccountingISBN:9780134475585Author:Srikant M. Datar, Madhav V. RajanPublisher:PEARSONIntermediate AccountingAccountingISBN:9781259722660Author:J. David Spiceland, Mark W. Nelson, Wayne M ThomasPublisher:McGraw-Hill EducationFinancial and Managerial AccountingAccountingISBN:9781259726705Author:John J Wild, Ken W. Shaw, Barbara Chiappetta Fundamental Accounting PrinciplesPublisher:McGraw-Hill Education
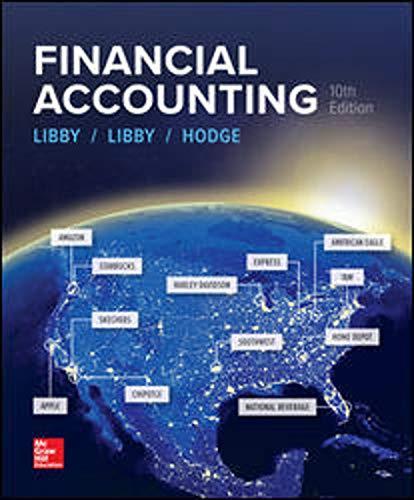
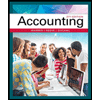
Accounting
Accounting
ISBN:9781337272094
Author:WARREN, Carl S., Reeve, James M., Duchac, Jonathan E.
Publisher:Cengage Learning,
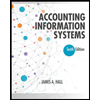
Accounting Information Systems
Accounting
ISBN:9781337619202
Author:Hall, James A.
Publisher:Cengage Learning,
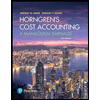
Horngren's Cost Accounting: A Managerial Emphasis...
Accounting
ISBN:9780134475585
Author:Srikant M. Datar, Madhav V. Rajan
Publisher:PEARSON
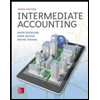
Intermediate Accounting
Accounting
ISBN:9781259722660
Author:J. David Spiceland, Mark W. Nelson, Wayne M Thomas
Publisher:McGraw-Hill Education
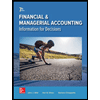
Financial and Managerial Accounting
Accounting
ISBN:9781259726705
Author:John J Wild, Ken W. Shaw, Barbara Chiappetta Fundamental Accounting Principles
Publisher:McGraw-Hill Education