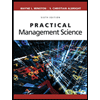
Practical Management Science
6th Edition
ISBN: 9781337406659
Author: WINSTON, Wayne L.
Publisher: Cengage,
expand_more
expand_more
format_list_bulleted
Question
Given the following |
|||
determine the total cost of a plan that uses regular time | |||
production output of 600 units per month, overtime is | |||
used when needed up to a maximum of 60 units per | |||
month, and subcontracting is used if additional units are needed to meet the forecast | |||
Regular time cost | $ 40.00 | per unit | |
Overtime cost | $ 60.00 | per unit (60 max) | |
subcontracting cost | $ 80.00 | per unit | |
holding cost | $ 10.00 | per unit per month | |
month 1 forecast 563 month 2 forecast 608 month 3 forecast 648 month 4 forecast 668 month 5 forecast 666 month 6 forecast 688
Show in Excel |
Expert Solution

This question has been solved!
Explore an expertly crafted, step-by-step solution for a thorough understanding of key concepts.
Step by stepSolved in 2 steps

Knowledge Booster
Learn more about
Need a deep-dive on the concept behind this application? Look no further. Learn more about this topic, operations-management and related others by exploring similar questions and additional content below.Similar questions
- A 126,000 square foot office building in Plano, Texas is fully leased to the Dr. Pepper Snapple Group at a base rent of $2.50 per square foot per month. The building’s expenses total $0.90 per square foot per month and an expense stop in the Dr. Pepper lease is set at $6.00 per square foot per year. What is the annual NOI? a. $3,024,000 b. $3,175,200 c. $3,780,000 d. $2,419,200arrow_forwardForecast Data is given within problem. Cost Data is attached Southeast Soda Pop, Inc., has a new fruit drink for which it has high hopes. John Mittenthal, the production planner, has assembled the following cost data and demand forecast: LOADING... Click the icon to view the demand forecast. LOADING... Click the icon to view the cost data. John's job is to develop an aggregate plan. The three initial options he wants to evaluate are: • Plan A: a strategy that hires and fires personnel as necessary to meet the forecast. • Plan B: a level strategy. • Plan C: a level strategy that produces 1,000 cases per quarter and meets the forecast demand with inventory and subcontracting. Part 2 a) Which strategy is the lowest-cost plan? Try hiring and layoffs (to meet the forecast) as necessary (enter your responses as whole numbers). Hiring and Layoff Plan Quarter Forecast Production Hire (Units) Layoff (Units)…arrow_forwardExplain the figures and mention the disadvantages and advantages of the following figures based on the operation management perspective: leading demand with an incremental expansion, leading demand with one-step expansion, lagging demand with incremental expansion, attempts to have an average capacity that straddles demand with incremental expansionarrow_forward
- A store’s demand figures are given in the table. According to this, what is the linear regression forecast for Week 12?arrow_forwardWrite an essay titled "Here, There, and Everywhere" on the construction and hardware supply company FOUR ACES.arrow_forwarda) GOT7 Soda Pop, Inc., has a new fruits drink. The production planner has assembled the following cost data and demand forecast as follow: [GOT7 Soda Pop, Inc., mempunyai minuman buah-buahan yang baru, Perancang pengeluaran telah mengumpul data tentang kos dan ramalan permintaan seperti berikut:] Quarter Demand 1,800 First Second 1,200 Third 1,600 Fourth 1,300 Table 1: Cost and demand forecast [Jadual 1: Kos dan ramalan permintaan] Previous quater's output 1,300 cases Beginning inventory 0 cases Stockout cost Inventory holding cost Hiring employees Terminating employees Subcontracting cost Unit cost on regular time Overtime cost RM150 RM40 per case at the end of quater RM40 per case RM80 per case RM60 per case RM30 per case RM15 extra per case You as the production planner need to develop an aggregate planning. You are required to: [Anda sebagai perancang pengeluaran perlu membangunkan perancangan agregat Anda dikehendaki untuk:] i) Assess plan A: strategy that hires and fires…arrow_forward
- Please do not write in column A Problem 6 Given the following forecast and cost information, determine the total cost of a plan that uses regular time production output of 600 units per month, overtime is used when needed up to a maximum of 60 units per month, and subcontracting is used if additional units are needed to meet the forecast. Regular time cost $ 40.00 per unit Overtime cost $ 60.00 per unit subcontracting cost $ 80.00 per unit holding cost $ 10.00 per unit per month Production Inventory Costs Month Forecast Level Production Overtime Subcontracting Total Holding Cost Regular Time Overtime Subcontracting Total Cost 1 563 0 2 608 3 648 4 668 5 666 6 688 Totalsarrow_forwardplease help me with Question 3 thanks! Demand forecasts for 2021 are as follows: Month Demand Jan 140,000 Feb 78,900 Mar 85,800 Apr 89,100 May 123,600 Jun 136,350 Jul 120,450 Aug 106,950 Sep 121,950 Oct 135,750 Nov 87,000 Dec 93,300 Each worker can produce 900 products per month and is paid $1500 per month. Assume that at the end of last year, the company has 100 employees working on the production line. Hiring and layoff (firing) decisions are made at the beginning of each month, and associated costs are charged at that time. It costs the company $400 to hire and $800 to lay off a worker. The company incurs holding cost for the amount of ending inventory in each month, and incurs backorder cost at the end of each month for any unfilled orders. The company incurs $2 per month for holding one unit in inventory and $4 per unit backorder. 1 Prepare a level aggregate plan. Under this level aggregate plan, how…arrow_forwardDemand at Nature Trails Ski Resort has a seasonal pattern.Demand is highest during the winter, as this is the peak ski season.However, there is some ski demand in the spring and even fallmonths. Th e summer months can also be busy as visitors oft encome for summer vacation to go hiking on the mountain trails.Th e owner of Nature Trails would like to make a forecast for eachseason of the next year. Total annual demand has been estimatedat 4000 visitors. Given the last two years of historical data, what isthe forecast for each season of the next year?arrow_forward
- The Cheyenne Hotel in Big Sky, Montana, has accumulated records of the total electrical costs of the hotel and the number of occupancy-days over the last year. An occupancy-day represents a room rented for one day. The hotel’s business is highly seasonal, with peaks occurring during the ski season and in the summer. Month Occupancy-Days Electrical Costs January 2,630 $ 10,783 February 3,130 $ 12,833 March 3,640 $ 13,583 April 1,090 $ 4,469 May 1,770 $ 7,257 June 1,730 $ 7,093 July 4,440 $ 14,854 August 3,860 $ 13,815 September 2,170 $ 8,897 October 1,210 $ 4,961 November 1,790 $ 7,339 December 2,930 $ 12,013 Required: 1. Using the high-low method, estimate the fixed cost of electricity per month and the variable cost of electricity per occupancy-day. (Do not round your intermediate calculations. Round your Variable cost answer to 2 decimal places and Fixed cost element answer to nearest whole dollar amount.) What other factors in addition to…arrow_forwardVartan Information Technologies has a division called Useless Transistors. It is considering an « overhaul » of Useless Transistors’ operations or moving Useless overseas. Inventory management is receiving considerable attention. Vartan collected data for the years 2014, 2015, and a forecast for 2016. This data is provided below. What would be Useless Transistors’ weeks of supply for 2015? Projected 2014 2015 2016 Sales $127,890,000 $148,900,000 $192,340,000 Beginning Inventory $3,897,234 $5,467,983 $6,183,230 Ending Inventory $5,467,983 $6,183,230 $4,654,129 Cost of Goods Sold $16,876,400 $20,376,548 $22,346,786 Group of answer choicesarrow_forwardThe total planned expenditures is called as aggregate demand Select one: True Falsearrow_forward
arrow_back_ios
SEE MORE QUESTIONS
arrow_forward_ios
Recommended textbooks for you
- Practical Management ScienceOperations ManagementISBN:9781337406659Author:WINSTON, Wayne L.Publisher:Cengage,Operations ManagementOperations ManagementISBN:9781259667473Author:William J StevensonPublisher:McGraw-Hill EducationOperations and Supply Chain Management (Mcgraw-hi...Operations ManagementISBN:9781259666100Author:F. Robert Jacobs, Richard B ChasePublisher:McGraw-Hill Education
- Purchasing and Supply Chain ManagementOperations ManagementISBN:9781285869681Author:Robert M. Monczka, Robert B. Handfield, Larry C. Giunipero, James L. PattersonPublisher:Cengage LearningProduction and Operations Analysis, Seventh Editi...Operations ManagementISBN:9781478623069Author:Steven Nahmias, Tava Lennon OlsenPublisher:Waveland Press, Inc.
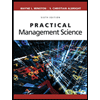
Practical Management Science
Operations Management
ISBN:9781337406659
Author:WINSTON, Wayne L.
Publisher:Cengage,
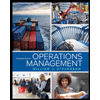
Operations Management
Operations Management
ISBN:9781259667473
Author:William J Stevenson
Publisher:McGraw-Hill Education
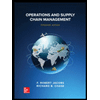
Operations and Supply Chain Management (Mcgraw-hi...
Operations Management
ISBN:9781259666100
Author:F. Robert Jacobs, Richard B Chase
Publisher:McGraw-Hill Education
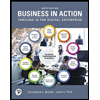
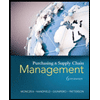
Purchasing and Supply Chain Management
Operations Management
ISBN:9781285869681
Author:Robert M. Monczka, Robert B. Handfield, Larry C. Giunipero, James L. Patterson
Publisher:Cengage Learning
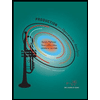
Production and Operations Analysis, Seventh Editi...
Operations Management
ISBN:9781478623069
Author:Steven Nahmias, Tava Lennon Olsen
Publisher:Waveland Press, Inc.