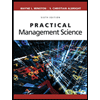
Practical Management Science
6th Edition
ISBN: 9781337406659
Author: WINSTON, Wayne L.
Publisher: Cengage,
expand_more
expand_more
format_list_bulleted
Question
please solve all parts within 30 minutes.
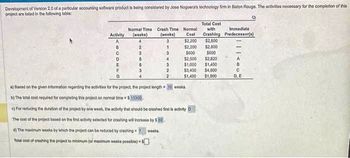
Transcribed Image Text:Development of Version 2.0 of a particular accounting software product is being considered by Jose Noguera's technology firm in Baton Rouge. The activities necessary for the completion of this
project are listed in the following table:
Activity
A
8
C
D
E
F
G
Normal Time Crash Time Normal
(weeks)
49
Cost
2
3
8
Total Cost
with
Immediate
Crashing Predecessor(s)
$2,800
$2,800
$600
$600
$2,500
$2,820
$1,000 $1,450
$3,400
$4,000
$1,400
$1,900
(weeks)
3
1
3
4
3
2
2
d) The maximum weeks by which the project can be reduced by crashing
Total cost of crashing the project to minimum (or maximum weeks possible) $
$2,200
$2,200
a) Based on the given information regarding the activities for the project, the project length - 16 weeks.
b) The total cost required for completing this project on normal time = $13300
c) For reducing the duration of the project by one week, the activity that should be crashed first is activity D
The cost of the project based on the first activity selected for crashing will increase by $ 80-
weeks
D, E
Expert Solution

This question has been solved!
Explore an expertly crafted, step-by-step solution for a thorough understanding of key concepts.
This is a popular solution
Trending nowThis is a popular solution!
Step by stepSolved in 5 steps with 4 images

Knowledge Booster
Similar questions
- Design a SWOT analysis for a IT help desk center. This help desk has 3 tiers: Tier 1: Lower level, can help with small issues on a computer (logging in, website issues). Tier 2: Physical repairs, can help with troubleshooting hardware problems or any problem Tier 1 could not solve. Will replace broken components. Tier 3: Administration, this tier has all the bosses that see over Tier 2 and Tier 1. They will help with Tier 2 if needed, mostly used in disaster scenarios.arrow_forwardHow does the latency of interruptions impact the time it takes to move between tasks?arrow_forwardHello, thanks greatly but why did you use maximum time duration and not shortest time rule in finding the time to make one ball? ( D5 - A14 = 120 SEC )arrow_forward
- Given the following information, assign tasks to work stations using the most followers rule. Assume the cycle time is 60 seconds. Submit for each workstation (1,2,3 etc.), the tasks assigned in order of assignment, the idle time for each work station and the total idle time. (It will help for you to make the diagram but you are not required to submit the diagram) Immediate Task Task Time (seconds) Predecessor 35 50 A. 20 10 25 F\ C.E 40 Edit Format Table Paragraph V BIUA 12pt v Immediate Predecessor Task Time (seconds) Taskarrow_forwardanswer Part d, e and f onlyarrow_forwardFor what kinds of problems does the workflow management system aim to provide a solution?arrow_forward
- Five jobs are ready for processing at time zero through a workstation. The details of the processing time and the due date of completion is provided in the following table. Job A B Processing Time (days) I5 Due Date 11 6 3 16 19 10 D E 15 Using the earliest due date (EDD) rule, the average lateness for the five jobs is decimal place. Round your answer to one Your Answer: Answerarrow_forwardJohn, Jack and Jill are project managers for Jusco Company. All three of them lead their own team, with two supervisors working under them. John’s team has 10 members, Jack has 8 members in his team and Jill has 11 members under his care. Both John and Jack completed their projects on time with the same amount of allocated budgets from top managers. But Jill didn’t manage to complete the project on time this time round. (i) Assuming all three projects have the same scale in terms of size, quality,and complexity, what can we conclude about the effectiveness and efficiency of these three project managers based on the informationabove? Justify your answers PLEASE PROVIDE CLEAR EXPLANATION THANK YOU , THIS TOPIC IS UNDER EVOLUTION OF FUNDAMENTAL MANAGEMENT THEORIESarrow_forwardThe following memo is from an exasperated manager to her staff. Obviously, this manager does not have the time to clean up her writing or another set of eyes to review her written material before mailing it. From: Albertina Sindaha, Operations Manager To: All Employees Subject: Cleanup! Message You were all supposed to clean up your work areas last Friday, but that didn't happen. A few people cleaned their desks, but no one pitched in to clean the common areas. So we're going to try again. As you know, we don't have a big enough custodial budget anymore. Everyone must clean up himself. This Friday I want to see action in the copy machine area, things like emptying waste baskets, and you should organize paper and toner supplies. The lunch room is a disaster area. You must do something about the counters, the refrigerator, the sinks, and the coffee machine. And any food left in the refrigerator on Friday afternoon should be thrown out because it stinks by Monday. Finally, the office…arrow_forward
- Please walk me through each step and the reasoning behind the step I don't understandarrow_forwardWhat feature of manufacturing planning and control systems operates under the premise that the planned work input to a work center should never exceed the planned work output?arrow_forwardConsider a project with seven tasks. Three tasks – tasks 3, 4, and 5 – require a specific resource for completion; all needed resources must be available at the site before a task can be started. Task Duration Predecessor (s) Units of Value of Resource Completed Task Needed 3 3 10 $4000 1 10 S3000 3 12 55000 1 4 7 1 2, 5,6 Each resource unit cost $100; no quantity discounts are available. In addition, it costs $2 per unit per time period to hold this resource in stock, and it costs $45 just to place an order for materials (independent of the number of units ordered). When should each task in the project be started and when and how many resources should be ordered to minimize total project costs? 1, 1, en en en en 1, 2. enarrow_forward
arrow_back_ios
SEE MORE QUESTIONS
arrow_forward_ios
Recommended textbooks for you
- Practical Management ScienceOperations ManagementISBN:9781337406659Author:WINSTON, Wayne L.Publisher:Cengage,Operations ManagementOperations ManagementISBN:9781259667473Author:William J StevensonPublisher:McGraw-Hill EducationOperations and Supply Chain Management (Mcgraw-hi...Operations ManagementISBN:9781259666100Author:F. Robert Jacobs, Richard B ChasePublisher:McGraw-Hill Education
- Purchasing and Supply Chain ManagementOperations ManagementISBN:9781285869681Author:Robert M. Monczka, Robert B. Handfield, Larry C. Giunipero, James L. PattersonPublisher:Cengage LearningProduction and Operations Analysis, Seventh Editi...Operations ManagementISBN:9781478623069Author:Steven Nahmias, Tava Lennon OlsenPublisher:Waveland Press, Inc.
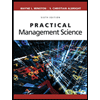
Practical Management Science
Operations Management
ISBN:9781337406659
Author:WINSTON, Wayne L.
Publisher:Cengage,
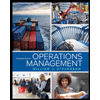
Operations Management
Operations Management
ISBN:9781259667473
Author:William J Stevenson
Publisher:McGraw-Hill Education
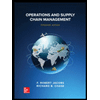
Operations and Supply Chain Management (Mcgraw-hi...
Operations Management
ISBN:9781259666100
Author:F. Robert Jacobs, Richard B Chase
Publisher:McGraw-Hill Education
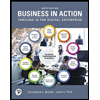
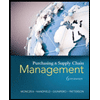
Purchasing and Supply Chain Management
Operations Management
ISBN:9781285869681
Author:Robert M. Monczka, Robert B. Handfield, Larry C. Giunipero, James L. Patterson
Publisher:Cengage Learning
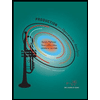
Production and Operations Analysis, Seventh Editi...
Operations Management
ISBN:9781478623069
Author:Steven Nahmias, Tava Lennon Olsen
Publisher:Waveland Press, Inc.