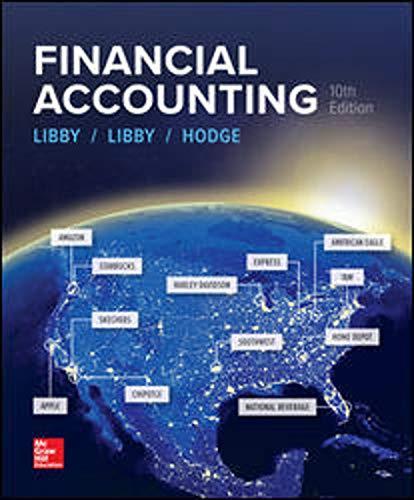
Concept explainers
Determining cost relationships
Midstate Containers Inc. manufactures cans for the canned food industry. The operations manager of a can manufacturing operation wants to conduct a cost study investigating the relationship of tin content in the material (can stock) to the energy cost for enameling the cans. The enameling was necessary to prepare the cans for labeling. A higher percentage of tin content in the can stock increases the cost of material. The operations manager believed that a higher tin content in the can stock would reduce the amount of energy used in enameling. During the analysis period, the amount of tin content in the steel can stock was increased for every month, from April to September. The following operating reports were available from the controller:
April | May | June | July | August | September | ||||||||||||
Materials | $14,000 | $34,800 | $33,000 | $21,700 | $28,800 | $33,000 | |||||||||||
Energy | 13,000 | 28,800 | 24,200 | 14,000 | 17,100 | 16,000 | |||||||||||
Total cost | $27,000 | $63,600 | $57,200 | $35,700 | $45,900 | $49,000 | |||||||||||
Units produced | ÷ 50,000 | ÷ 120,000 | ÷ 110,000 | ÷ 70,000 | ÷ 90,000 | ÷ 100,000 | |||||||||||
Cost per unit | $0.54 | $0.53 | $0.52 | $0.51 | $0.51 | $0.49 |
Differences in materials unit costs were entirely related to the amount of tin content. In addition, inventory changes are negligible and are ignored in the analysis.
Calculate the total cost per unit for each month. Round your answers to the nearest cent.
Total Cost per Unit |
||
April | $fill in the blank 1 | |
May | $fill in the blank 2 | |
June | $fill in the blank 3 | |
July | $fill in the blank 4 | |
August | $fill in the blank 5 | |
September | $fill in the blank 6 |
Interpret your results.
The calculations reveals that the tin content and energy costs are related. That is, as the materials cost increased due to higher tin content, the energy costs by more. Thus, the recommendation should be to raw can stock with the tin content at the $0.33-per-unit level(September level). This is the material that the total production cost for this set of data. Additional data could be used to determine the optimal tin content, or the point where energy cost savings fail to overcome additional material costs.

Trending nowThis is a popular solution!
Step by stepSolved in 2 steps with 1 images

- Barbara, the manager of Metlock, is analyzing the company's MOH costs from last year. Metlock had always followed an actual costing system when determining the costs of its customizable telescopes. Barbara wondered if it would be better to switch to a normal costing system, as she had heard a number of people talking about that at an industry conference she attended the previous month. Since Metlock has a highly machine-intensive operation, machine hours are used as its MOH cost driver. Here are the costs and other MOH information Barbara is analyzing: Budgeted MOH cost Actual MOH cost Budgeted machine hours Actual machine hours $426,240 Actual MOH rate $ 419,040 Determine the actual MOH rate and the budgeted MOH rate Metlock would have used last year under actual costing and normal costing, respectively. (Round answers to 2 decimal places, e.g. 52.75.) Budgeted MOH rate $ 96,000 108,000 /machine hour /machine hourarrow_forwardVishanuarrow_forwardBaird Chairs, Incorporated makes two types of chairs. Model Diamond is a high-end product designed for professional offices. Model Gold is an economical product designed for family use. Jane Silva, the president, is worried about cut-throat price competition in the chairs market. Her company suffered a loss last quarter, an unprecedented event in its history. The company's accountant prepared the following cost data for Ms. Silva: Direct Cost per Unit Direct materials Direct labor Category Unit level Batch level Product level Facility level Total Model Diamond (D) $19.50 per unit $ 19.10/hour x 2.00 hours production time Type of Product Estimated Cost $ 247,500 825,000 704,000 572,000 $ 2,348,500 a. Model Diamond a. Model Gold b. Model Diamond b. Model Gold Cost Driver Number of units. Number of setups Number of TV commercials Number of machine hours The market price for office chairs comparable to Model Diamond is $118 and to Model Gold is $75. Cost per Unit Model Gold (G) $9.90 per…arrow_forward
- Hansabenarrow_forwardBucknum Boys, Inc., produces hunting gear for buck hunting. The company’s main productiondepartments are Molding and Finishing. Production of the hunting gear cannot beaccomplished without the supporting tasks of Materials Management and meals for productionemployees provided by the Cafeteria. Cafeteria costs are always higher than MaterialsManagement costs. The company believes that the number of employees in each departmentis the best driver of Cafeteria costs. The number of employees in each department is asfollows:The company also believes that the value of support materials used in each department is thebest driver for Materials Management costs. The support materials used in the Molding andMolding Department 27Finishing Department 30Materials ManagementDepartment 3Cafeteria Department 6Finishing departments are valued at $1,800 and $2,700, respectively. Using the sequentialmethod for support department cost allocation (allocating Cafeteria costs first), determine(a) the…arrow_forwardAs you learned in the previous chapters, Current Designs has two main product lines-composite kayaks, which are handmade and very labor-intensive, and rotomolded kayaks, which require less labor but employ more expensive equipment. Current Designs' controller, Diane Buswell, is now evaluating several different methods of assigning overhead to these products. It is important to ensure that costs are appropriately assigned to the company's products. At the same time, the system that is used must not be so complex that its costs are greater than its benefits. Diane has decided to use the following activities and costs to evaluate the methods of assigning overhead. Activities Cost Designing new models Creating and testing prototypes $120,000 144,000 Creating molds for kayaks 208,000 Operating oven for the rotomolded kayaks 38,000 Operating the vacuum line for the composite kayaks 27,000 192,000 Supervising production employees Curing time (the time that is needed for the chemical processes…arrow_forward
- Mary Jones and Jack Smart have joined forces to start M&J Food Products, a processor of packaged shredded lettuce for institutional use. Jack has years of food processing experience, and Mary has extensive commercial food preparation experience. The process will consist of opening crates of lettuce and then sorting, washing, slicing, preserving, and finally packaging the prepared lettuce. Together, with help from vendors, they think they can adequately estimate demand, fixed costs, revenues, and variable cost per 5-pound bag of lettuce. They think a largely manual process will have monthly fixed cost of $50,000 and a variable cost of $2.50 per bag. They expect to sell 75,000 bags of lettuce per month. They expect to sell the shredded lettuce for $3.25 per 5-pound bag. Jack and Mary has been contacted by a vendor to consider a more mechanized process. This new process will have monthly fixed cost of $125,000 per month with a variable cost of $1.75 per bag. Based on the above…arrow_forwardJT Engineering makes widgets. Widgets first go through Smelting and then go through Polishing. JT has decided to do away with the polishing step, electing to sell unpolished widgets to its customers. How will this process modification impact JT's manufacturing costs and flow of costs? O It will decrease manufacturing costs and eliminate the need for Work in Process accounts. O It will increase manufacturing costs and eliminate the need for Work in Process accounts. O It will decrease manufacturing costs and eliminate the need for a Work in Process-Polishing account. O It will increase manufacturing costs and eliminate the need for a Work in Process-Polishing account.arrow_forwardClarke, Inc. manufactures door panels. Suppose Clarke, Inc. is considering spending the following amounts on a new total quality management (TQM) program: View the spending amounts. Clarke, Inc. expects the new program would save costs through the following: View the savings amounts. Requirements 1. Classify each cost as a prevention cost, an appraisal cost, an internal failure cost, or an external failure cost. 2. Should Clarke, Inc. implement the new quality program? Give your reason. Requirement 1. Classify each cost as a prevention cost, an appraisal cost, an internal failure cost, or an external failure cost. Type of Cost Strength-testing one item from each batch of panels Training employees in TQM Training suppliers in TQM Identifying suppliers who commit to on-time delivery of perfect-quality materials Lost profits from lost sales due to disappointed customers Rework and spoilage Inspection of raw materials Warranty costs Savings Avoid lost profits from lost sales due to…arrow_forward
- Hall, Incorporated manufactures two components, Standard and Ultra, that are designed for the same function, but are made of different metals for operational performance reasons. The metal used in Standard is easy to work with and there are few quality issues or reworking required on the machines. The metal used in Ultra is more difficult to work with and often needs additional machine time and rework. Data on expected operations and direct costs for the next fiscal year follow: Account Administration Engineering Machine operation and maintenance Standard Miscellaneous Supervision Total 48,000 144,000 24,000 Ultral $ 3,384,000 2,520,000 Units produced Direct labor-hours used Machine-hours used Direct materials costs $5,163,000 Direct labor costs 855,000 The planning process team at Hall, Incorporated has estimated the following manufacturing overhead costs for the next fiscal year: 16,500 22,500 22,500 Total Amount $ 825,400 5,699,500 875,000 540,100 884,500 $8,824,500. 64,500 166,500…arrow_forwardNizam Company produces speaker cabinets. Recently, Nizam switched from a traditional departmental assembly line system to a manufacturing cell in order to produce the cabinets. Sup-pose that the cabinet manufacturing cell is the cost object. Assume that all or a portion of the following costs must be assigned to the cell:a. Depreciation on electric saws, sanders, and drills used to produce the cabinetsb. Power to heat and cool the plant in which the cell is locatedc. Salary of cell supervisord. Wood used to produce the cabinet housingse. Maintenance for the cell’s equipment (provided by the maintenance department)f. Labor used to cut the wood and to assemble the cabinetsg. Replacement sanding beltsh. Cost of janitorial services for the planti. Ordering costs for materials used in productionj. The salary of the industrial engineer (she spends about 20 percent of her time on work forthe cell)k. Cost of maintaining plant and grounds l. Cost of plant’s personnel officem. Depreciation on…arrow_forward
- AccountingAccountingISBN:9781337272094Author:WARREN, Carl S., Reeve, James M., Duchac, Jonathan E.Publisher:Cengage Learning,Accounting Information SystemsAccountingISBN:9781337619202Author:Hall, James A.Publisher:Cengage Learning,
- Horngren's Cost Accounting: A Managerial Emphasis...AccountingISBN:9780134475585Author:Srikant M. Datar, Madhav V. RajanPublisher:PEARSONIntermediate AccountingAccountingISBN:9781259722660Author:J. David Spiceland, Mark W. Nelson, Wayne M ThomasPublisher:McGraw-Hill EducationFinancial and Managerial AccountingAccountingISBN:9781259726705Author:John J Wild, Ken W. Shaw, Barbara Chiappetta Fundamental Accounting PrinciplesPublisher:McGraw-Hill Education
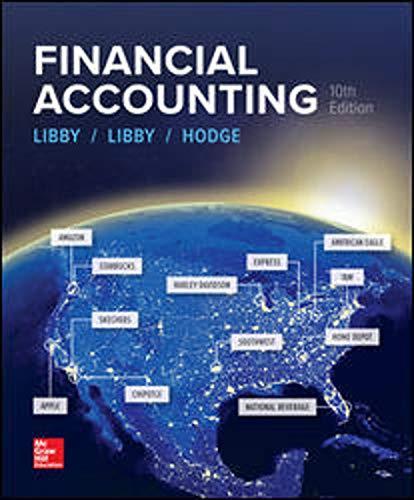
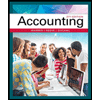
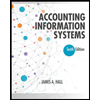
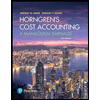
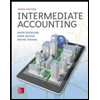
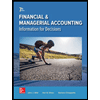