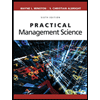
Practical Management Science
6th Edition
ISBN: 9781337406659
Author: WINSTON, Wayne L.
Publisher: Cengage,
expand_more
expand_more
format_list_bulleted
Concept explainers
Topic Video
Question
Demand for a power steering gear assembly is given by
Period |
1 |
2 |
3 |
4 |
5 |
6 |
7 |
8 |
9 |
10 |
Gear |
14 |
12 |
12 |
13 |
5 |
90 |
20 |
20 |
20 |
20 |
Currently there are 50 parts on hand. The lot-sizing rule is, again, fixed order period using two periods. Lead time is three periods.
- Determine the planned order release
schedule for the gear.
- Suppose each gear assembly requires two pinions. Currently there are 100 pinions on hand, the lot-sizing rule is lot-for-lot, and the lead time is one period. Determine the gross requirement and then the planned order release schedule for pinions.
Expert Solution

This question has been solved!
Explore an expertly crafted, step-by-step solution for a thorough understanding of key concepts.
This is a popular solution
Trending nowThis is a popular solution!
Step by stepSolved in 2 steps

Knowledge Booster
Learn more about
Need a deep-dive on the concept behind this application? Look no further. Learn more about this topic, operations-management and related others by exploring similar questions and additional content below.Similar questions
- Develop a lot-for-lot solution and calculate total relevant costs for the gross requirements in the following table*. Period Gross requirements 1 2 20 3 4 56 7 8 9 10 11 12 30 30 60 20 20 80 60 *Holding cost $1.50/unit/week; setup cost $200; lead time = 1 week; beginning inventory = 40. Develop a lot-for-lot solution (enter your responses as whole numbers). Period Gross requirements On-hand at beginning of period On-hand at end of period 1 2 3 4 56 7 8 9 10 11 12 20 30 30 60 20 20 80 60 40 20 30 20 20 Order receipt Order releasearrow_forwardPlease solve correctly. Don't solve if you don't know -arrow_forwardDevelop a lot-for-lot solution and calculate total relevant costs for the gross requirements in the following table*. Period Gross requirements Develop a lot-for-lot solution (enter your responses as whole numbers). Period Gross requirements On-hand at beginning of period On-hand at end of period 1 Order receipt Order release 30 2 3 30 1 30 40 || 4 5 2 6 7 40 70 20 *Holding cost = $3.50/unit/week; setup cost = $150; lead time = 1 week; beginning inventory = 40. 3 4 30 8 9 10 11 12 5 6 7 40 70 20 20 80 8 60 9 10 20 80 11 12 60arrow_forward
- The MRP gross requirements for Item X are shown here for the next 10 weeks. Lead time for A is two weeks, and setup cost is $10. There is a carrying cost of $0.02 per unit per week. Beginning inventory is 72 units. WEEK 1 2 3 4 5 6 7 8 9 10 Gross requirements 21 12 15 45 10 30 100 20 40 150 Use the least total cost lot-sizing method to determine when and for what quantity the first order should be released. Least total cost method indicates that periods units should be ordered to cover the needs forarrow_forwardPlease do not give solution in image format thankuarrow_forwardDevelop a EOQ solution and calculate total relevant costs for the gross requirements in the following table*. Period 1 2 3 4 5 6 7 8 9 10 11 12 Gross requirements 20 30 30 30 20 10 40 60 *Holding cost =$ 2.50/unit/week; setup cost =$ 150; lead time =1 week; beginning inventory =40. What is the average demand per week? with 2 decimal places): Calculate Economic Order Quantity (EOQ) Develop a EOQ solution (enter your responses as whole numbers). Period 1 2 3 4 5 6 7 8 9 10 11 12 Gross requirements 20 30 30 30 20 10 40 60 Scheduled receipt…arrow_forward
- Operations Managementarrow_forward7arrow_forwardExercise 2: The demand per year (D) for product X is 12,100 units. The costs of placing an order (S) are $4.50. The unit cost (C) of the item is $25.00. The maintenance cost (H) per unit per year is 30% of the item's cost. 1. Use the economic order quantity (EOQ) model to determine: *Optimal quantity to order* The expected number of orders*Optimal time between orders*The total annual cost of maintaining that optimal amountNOTE: Show calculations of how you arrived at each amount 2. Answer, what are the potential benefits of using EOQ analysis for inventory management? How can you help businesses strike a balance between inventory holding costs and ordering costs?arrow_forward
arrow_back_ios
arrow_forward_ios
Recommended textbooks for you
- Practical Management ScienceOperations ManagementISBN:9781337406659Author:WINSTON, Wayne L.Publisher:Cengage,Operations ManagementOperations ManagementISBN:9781259667473Author:William J StevensonPublisher:McGraw-Hill EducationOperations and Supply Chain Management (Mcgraw-hi...Operations ManagementISBN:9781259666100Author:F. Robert Jacobs, Richard B ChasePublisher:McGraw-Hill Education
- Purchasing and Supply Chain ManagementOperations ManagementISBN:9781285869681Author:Robert M. Monczka, Robert B. Handfield, Larry C. Giunipero, James L. PattersonPublisher:Cengage LearningProduction and Operations Analysis, Seventh Editi...Operations ManagementISBN:9781478623069Author:Steven Nahmias, Tava Lennon OlsenPublisher:Waveland Press, Inc.
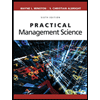
Practical Management Science
Operations Management
ISBN:9781337406659
Author:WINSTON, Wayne L.
Publisher:Cengage,
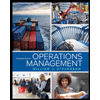
Operations Management
Operations Management
ISBN:9781259667473
Author:William J Stevenson
Publisher:McGraw-Hill Education
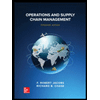
Operations and Supply Chain Management (Mcgraw-hi...
Operations Management
ISBN:9781259666100
Author:F. Robert Jacobs, Richard B Chase
Publisher:McGraw-Hill Education
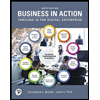
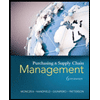
Purchasing and Supply Chain Management
Operations Management
ISBN:9781285869681
Author:Robert M. Monczka, Robert B. Handfield, Larry C. Giunipero, James L. Patterson
Publisher:Cengage Learning
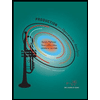
Production and Operations Analysis, Seventh Editi...
Operations Management
ISBN:9781478623069
Author:Steven Nahmias, Tava Lennon Olsen
Publisher:Waveland Press, Inc.