Consider the beam problem shown below. The beam is made of aluminum (2014 Alloy) with a modulus of elasticity E = 1.06x107 psi and Poisson's ratio of 0.33. At the current design, the beam length is 15 in. and the cross-section's width and height are 1.5 in. The load is P = 1000 lbf acting at the tip of the beam as shown. Design variables (I,w,h) are varied three times. For example, the width design variable is changed from its lower bound of 0.5 to 1.0 in., then to its upper bound of 1.5 in. Similarly, three changes take place for the height and length design variables, respectively. These changes in design variables are combined to create 27 (3 x 3 x 3) scenarios. The design goal is to optimize the beam design for a "minimum volume" subject to Displacement <0.1 in. and stress <65 psi by varying its length as well as the width and height of the cross-section. Using Solidworks, setup the design study to calculate the optimum values for I, w, and h?
Consider the beam problem shown below. The beam is made of aluminum (2014 Alloy) with a modulus of elasticity E = 1.06x107 psi and Poisson's ratio of 0.33. At the current design, the beam length is 15 in. and the cross-section's width and height are 1.5 in. The load is P = 1000 lbf acting at the tip of the beam as shown. Design variables (I,w,h) are varied three times. For example, the width design variable is changed from its lower bound of 0.5 to 1.0 in., then to its upper bound of 1.5 in. Similarly, three changes take place for the height and length design variables, respectively. These changes in design variables are combined to create 27 (3 x 3 x 3) scenarios. The design goal is to optimize the beam design for a "minimum volume" subject to Displacement <0.1 in. and stress <65 psi by varying its length as well as the width and height of the cross-section. Using Solidworks, setup the design study to calculate the optimum values for I, w, and h?
Mechanics of Materials (MindTap Course List)
9th Edition
ISBN:9781337093347
Author:Barry J. Goodno, James M. Gere
Publisher:Barry J. Goodno, James M. Gere
Chapter5: Stresses In Beams (basic Topics)
Section: Chapter Questions
Problem 5.6.13P: A two-axle carriage that is part of an over head traveling crane in a testing laboratory moves...
Related questions
Question
100%

Transcribed Image Text:Consider the beam problem shown below. The beam is made of aluminum (2014
Alloy) with a modulus of elasticity E= 1.06x107 psi and Poisson's ratio of 0.33. At the
current design, the beam length is 15 in. and the cross-section's width and height are
1.5 in. The load is P =1000 lbf acting at the tip of the beam as shown. Design variables
(1,w,h) are varied three times. For example, the width design variable is changed from
its lower bound of 0.5 to 1.0 in., then to its upper bound of 1.5 in. Similarly, three
changes take place for the height and length design variables, respectively. These
changes in design variables are combined to create 27 (3 x 3 x 3) scenarios. The
design goal is to optimize the beam design for a "minimum volume" subject to
Displacement <0.1 in. and stress <65 psi by varying its length as well as the width and
height of the cross-section. Using Solidworks, setup the design study to calculate
the optimum values for I, w, and h?
PRT CSY'S DEF
15 in
Front edge for load
End face
for Constraint
1000 lbf
1.5in
1.5in
Expert Solution

This question has been solved!
Explore an expertly crafted, step-by-step solution for a thorough understanding of key concepts.
Step by step
Solved in 3 steps with 6 images

Knowledge Booster
Learn more about
Need a deep-dive on the concept behind this application? Look no further. Learn more about this topic, mechanical-engineering and related others by exploring similar questions and additional content below.Recommended textbooks for you
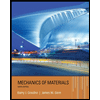
Mechanics of Materials (MindTap Course List)
Mechanical Engineering
ISBN:
9781337093347
Author:
Barry J. Goodno, James M. Gere
Publisher:
Cengage Learning
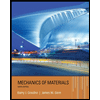
Mechanics of Materials (MindTap Course List)
Mechanical Engineering
ISBN:
9781337093347
Author:
Barry J. Goodno, James M. Gere
Publisher:
Cengage Learning