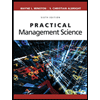
Practical Management Science
6th Edition
ISBN: 9781337406659
Author: WINSTON, Wayne L.
Publisher: Cengage,
expand_more
expand_more
format_list_bulleted
Question
Consider a product with a daily demand of 500 units, a setup cost per production run of $100, a daily holding cost per unit of $0.20, and an annual production rate of 219,000 units. The firm operates and experiences demand 365 days per year. Suppose that management mistakenly used the basic EOQ model to calculate the batch size instead of using the production order quantity model. How much money per year has that mistake cost the company?
Expert Solution

This question has been solved!
Explore an expertly crafted, step-by-step solution for a thorough understanding of key concepts.
This is a popular solution
Trending nowThis is a popular solution!
Step by stepSolved in 3 steps

Knowledge Booster
Similar questions
- A medical equipment has an average monthly demand is 134 units. Its unit cost is $385. It costs $486 to place an order, and the inventory carrying cost is $44 per unit per year. The equipment requires a 95% of service level with a safety stock requirement of 20 units. What is the equipment's minimum annual total inventory cost?arrow_forwardA manufacturing company produces 500 units of a product per day. If the setup cost for production is $1000 and the holding cost is $2 per unit per year, calculate the Economic Order Quantity (EOQ).arrow_forwardA manufacturer procures a subassembly from a supplier. The annual demand is 145,000 units, the cost per unit is $4, the inventory-carrying charge is 12 percent, and the order cost is $225. For orders between 10,000 but less than 30,000, a five percent discount is applied, and for orders exceeding 30,000, a eight percent discount is applied. What is the optimal order quantity? Use the Quantity Discount Excel template to find your answer.arrow_forward
- Tyler decided to open a bakery because everyone he knew told him that his baked goods were "out of this world." He had a little bit of a business school background because he got his Bachelor's from SPS at UIW recently. He remembered his teacher telling him that inventory models can be used for both the raw materials as well as the finished products for a business like his. So, he decided to see if he could use the basic EOQ model for identifying how much quantity to order of raw materials such as eggs, flour, sugar, etc. To get started, he decided to create a model for flour based on the information he had on hand regarding potential costs as follows: Usage per month 100 Ibs Purchase cost $1 per Ib. Order cost $10.00 per order sent Annual Holding Rate 10% of purchase price per Ib. • 52-week year 300 working days per year • Lead time 2 days Fill in the following table based on this information: Optimal Inventory Policy Answer Type 7 Reorder Point r Ibs. 8 Number of Orders Per Year…arrow_forwardUsing the fixed-order-quantity model, which of the following is the total ordering cost of inventory given an annual demand of 25,000 units, a cost per order of $80, and a holding cost per unit per year of $16?arrow_forwardA manufacturer’s annual demand is 6000 units. The current units per order is $100. The setup cost is $50 per order and the holding cost is $7 per unit. The cost per unit is $2.50. The Number of work days is 250 per year. What is the annual setup cost? What is the annual holding cost? What is the optimal order quantity (EOQ)? Using the EOQ, how many orders should be placed per year? What is the interval between orders? What is the inventory administration cost? What is the total cost of inventory?arrow_forward
- An electronic store uses continuous review policy to manage the inventory of its high selling monitor model. The monitor has the following characteristics. The annual demand for the monitor is (4000 *2) units per week. The monitors are bought from an offshore supplier at a unit price of 7000 AED per unit and each order costs 80000 AED. The holding cost of laptops is 25% of the value of the product. Calculate the annual demand using the no 2 What is the economic order quantity? EOQ? What would be the average number of orders in a week? What would be the average time between orders (in weeks)? What would be the average inventory level? The electronic store is considering a local supplier. The ordering cost of the new supplier is 65000 AED however the unit price of the monitor is 9000 AED. Should the electronic store change its supplier?arrow_forwardAnnual demand for a product is 11,960 units; weekly demand is 230 units with a standard deviation of 50 units. The cost of placing an order is $125, and the time from ordering to receipt is four weeks. The annual inventory carrying cost is $0.80 per unit. To provide a 98 percent service probability, what must the reorder point be? Suppose the production manager is told to reduce the safety stock of this item by 125 units. If this is done, what will the new service probability be?arrow_forwardThe Hodson Gallery and Art Museum distributes a printed guide for its visitors. There are about 18000 visitors per year. Holding costs for the brochures are 20% and it costs $30 to place an order with the printer. A. Assuming the cost for each guide is $2.50, how many should be printed at a time? B. Now assume the printer has offered the following discount schedule: Category Order Size Unit Cost 1 0 - 1499 $2.50 2 1500 - 2999 $2.20 3 3000 and over $1.80 Now how many brochures should be printed at a time?arrow_forward
arrow_back_ios
arrow_forward_ios
Recommended textbooks for you
- Practical Management ScienceOperations ManagementISBN:9781337406659Author:WINSTON, Wayne L.Publisher:Cengage,Operations ManagementOperations ManagementISBN:9781259667473Author:William J StevensonPublisher:McGraw-Hill EducationOperations and Supply Chain Management (Mcgraw-hi...Operations ManagementISBN:9781259666100Author:F. Robert Jacobs, Richard B ChasePublisher:McGraw-Hill Education
- Purchasing and Supply Chain ManagementOperations ManagementISBN:9781285869681Author:Robert M. Monczka, Robert B. Handfield, Larry C. Giunipero, James L. PattersonPublisher:Cengage LearningProduction and Operations Analysis, Seventh Editi...Operations ManagementISBN:9781478623069Author:Steven Nahmias, Tava Lennon OlsenPublisher:Waveland Press, Inc.
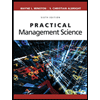
Practical Management Science
Operations Management
ISBN:9781337406659
Author:WINSTON, Wayne L.
Publisher:Cengage,
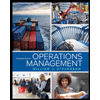
Operations Management
Operations Management
ISBN:9781259667473
Author:William J Stevenson
Publisher:McGraw-Hill Education
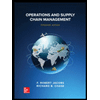
Operations and Supply Chain Management (Mcgraw-hi...
Operations Management
ISBN:9781259666100
Author:F. Robert Jacobs, Richard B Chase
Publisher:McGraw-Hill Education
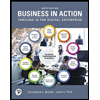
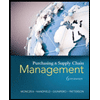
Purchasing and Supply Chain Management
Operations Management
ISBN:9781285869681
Author:Robert M. Monczka, Robert B. Handfield, Larry C. Giunipero, James L. Patterson
Publisher:Cengage Learning
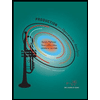
Production and Operations Analysis, Seventh Editi...
Operations Management
ISBN:9781478623069
Author:Steven Nahmias, Tava Lennon Olsen
Publisher:Waveland Press, Inc.