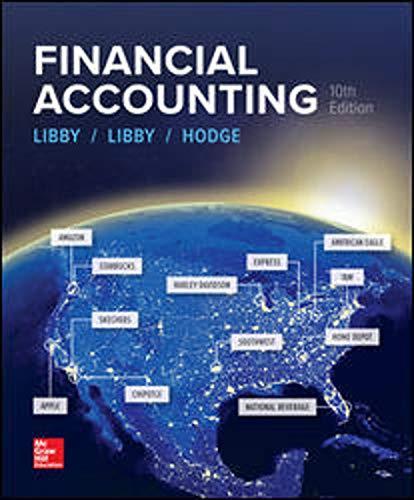
Concept explainers
Rockness asked, "Do you see any problems here? Should we drop any of these products?
Should we reprice any of these products?"
He said, "I am suspicious of these cost data, Rocky. Here we are assigning indirect costs to these products using a 260 percent rate. I really wonder whether that rate is accurate for all products. I want you to dig into the indirect cost data, figure out what drives those costs, and see whether you can give me more accurate cost numbers for these products."
Rocky first learned from production that the process required four activities: (1) setting up production runs, (2) managing production runs, and (3) managing products. The fourth activity did not require labor; it was simply the operation of machinery. Next, he went to the accounting records to get a breakdown of indirect costs. Here is what he found:
---------------------------------------------------IMAGE 2-----------------------------------------------------------------
Then, he began a series of interviews with department heads to see how to assign these costs to cost pools. He found that 40 percent of indirect labor was for scheduling or for handling production runs, including purchasing, preparing the production run, releasing materials for the production run, and performing a first-time inspection of the run. Another 50 percent of indirect labor was used to set up machinery to produce a particular product. The remaining 10 percent of indirect labor was spent maintaining records for each of the four products, monitoring the supply of raw materials required for each product, and improving the production processes for each product. This 10 percent of indirect labor was assigned to the cost driver "number of products."
Interviews with people in the information technology department indicated that $10,000 was allocated to the cola bottling line. Eighty percent of this $10,000 information technology cost was for scheduling production runs. Twenty percent of the cost was for recordkeeping for each of the four products.
- Setups: 560 labor-hours for setups.
- Production runs: 110 production runs.
- Number of products: 4 products,
- Machine-hour capacity: 20,000 Hours.
Diet cola used 200 setup hours, 40 production runs, and 5,000 machine-hours to produce 50,000 units. Regular cola used 60 setup hours, 30 production runs, and 4.000 machine-hours to produce 40,000 units. Cherry cola used 240 setup hours, 30 production runs, and 900 machine hours to produce 9,000 units. Grape cola used 60 setup hours, 10 production runs, and 100 machine-hours to produce 1,000 units. Rocky learned that the production people had a difficult time getting the taste just right for the Cherry and Grape colas, so these products required more time per setup than either the Diet or Regular colas.
Required
- Compute the unit costs for each of the cola products: Diet, Regular, Cherry, and Grape.
- What is the cost of unused capacity? What do you recommend that Rockness Bottling do with this unused capacity?
- Now assume that Rockness is considering producing a fifth product: Vanilla cola. Because Vanilla cola is in high demand in Rockness Bottling's market, assume that it would use 10,000 hours of machine time to make 100,000 units. (Recall that the machine capacity in this case is 20,000 hours, while Diet, Regular, Cherry, and Grape consume only 10,000 hours.) Vanilla cola's per unit costs would be identical to those of Diet cola except for the machine usage costs. What would be the cost of Vanilla cola? Calculate on a per-unit basis, and then in total.
![B
Monthly Report on Cola Bottling Line
Diet
Regular
Cherry
Grape
Total
Sales
$ 75,000
$ 60,000
$ 13,950
$1,650
$150,600
4
Less:
Materials
25,000
20,000
4,680
550
50,230
Direct labor
10,000
8,000
1,800
200
20,000
Fringe benefits on direct labor
4,000
3,200
720
80
8,000
520
52,000
26,000
$ 10,000
20,800
$8,000
4,680
$2,070
Indirect costs (@ 260% of direct labor)
Gross margin
24
300
$ 20,370
9.
10
Return on sales (see note [a])
13.3%
13.3%
14.8%
18.2%
13.5%
11 Volume
50,000
40,000
9,000
1,000
100,000
12 Unit price
$4
1.50
$4
1.50
24
1.55
$ 1.65
%24
1.506
13 Unit cost
24
1.30
$4
1.30
%24
1.32
$ 1.35
%24
1.302
14
15 a. Retun on sales before considering selling, general, and administrative expenses.
16](https://content.bartleby.com/qna-images/question/c66d3ec5-e5e8-4988-a672-d4378aa9f4df/50ea1b74-5c51-48d4-abb7-13b1e1efe4f0/n5o806_thumbnail.jpeg)
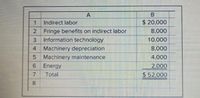

Trending nowThis is a popular solution!
Step by stepSolved in 6 steps

- I keep seeing this "P/A" thing in Cost Analysis problems but I can't figure out what it is or how to use it. Excel doesn't seem to recognize it. What do I need to do?arrow_forwardPls provide proper steps with explanationarrow_forwardNote:- Do not provide handwritten solution. Maintain accuracy and quality in your answer. Take care of plagiarism. Answer completely. You will get up vote for sure.arrow_forward
- An operations manager is deciding on the level of automation for a new process. The fixed cost for automation includes the equipment purchase price, installation, and initial spare parts. The variable costs per unit for each level of automation are primarily labor related. Each unit can be sold for $81. As in many cases, you have the default alternative of doing nothing ($0 fixed cost, $0 variable costs). Hint: For these questions, also consider the “Do Nothing” option as a viable option when making your decision. Alternative Fixed Costs Variable Costs per Unit A $100,000 $54 B $272,000 $31 C $560,000 $20 Recommended: graph each alternative with units on the x-axis and $ on the y-axis. Also, include revenue on the chart. Identify the break-even points and points of indifference.arrow_forwardClarke, Inc. manufactures door panels. Suppose Clarke, Inc. is considering spending the following amounts on a new total quality management (TQM) program: View the spending amounts. Clarke, Inc. expects the new program would save costs through the following: View the savings amounts. Requirements 1. Classify each cost as a prevention cost, an appraisal cost, an internal failure cost, or an external failure cost. 2. Should Clarke, Inc. implement the new quality program? Give your reason. Requirement 1. Classify each cost as a prevention cost, an appraisal cost, an internal failure cost, or an external failure cost. Type of Cost Strength-testing one item from each batch of panels Training employees in TQM Training suppliers in TQM Identifying suppliers who commit to on-time delivery of perfect-quality materials Lost profits from lost sales due to disappointed customers Rework and spoilage Inspection of raw materials Warranty costs Savings Avoid lost profits from lost sales due to…arrow_forwardI need help with this accounting problemarrow_forward
- AccountingAccountingISBN:9781337272094Author:WARREN, Carl S., Reeve, James M., Duchac, Jonathan E.Publisher:Cengage Learning,Accounting Information SystemsAccountingISBN:9781337619202Author:Hall, James A.Publisher:Cengage Learning,
- Horngren's Cost Accounting: A Managerial Emphasis...AccountingISBN:9780134475585Author:Srikant M. Datar, Madhav V. RajanPublisher:PEARSONIntermediate AccountingAccountingISBN:9781259722660Author:J. David Spiceland, Mark W. Nelson, Wayne M ThomasPublisher:McGraw-Hill EducationFinancial and Managerial AccountingAccountingISBN:9781259726705Author:John J Wild, Ken W. Shaw, Barbara Chiappetta Fundamental Accounting PrinciplesPublisher:McGraw-Hill Education
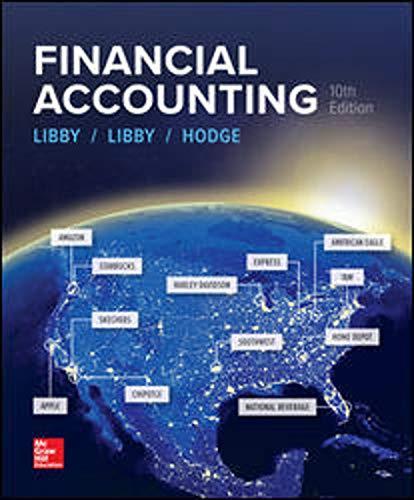
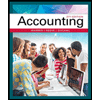
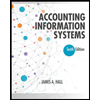
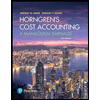
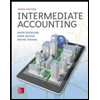
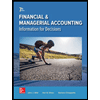