Case 02: The Black & Decker Evolution Known primarily for its power tools, Black & Decker is one of the world’s older multinational corporations. The company was founded in Baltimore, Maryland, in 1910, and by the end of the 1920’s had become a small multinational company with operations in Canada and Britain. Today the company has two well-known brands, Black & Decker consumer powers tools and its DeWalt brand of professional power tools. It sells its products in over 100 nations, and has revenues in excess of $5 billion, more than half of which are generated outside of the United States. The company grew rapidly during the 1950’s and 196’s due to its strong brand name and near monopoly share of the consumer and professional power tools markets. This monopoly was based on Black &Decker's pioneering development of handheld power tools. It was during this period that Black & Decker expanded rapidly in international markets, typically by setting up wholly owned subsidiaries in a nation and giving them the right to develop, manufacture, and market the company’s power tools. As a result, by the early 1980’s, the company had 23 wholly owned subsidiaries in foreign nations and two joint ventures. During its period of rapid international expansion, Black & Decker operated with decentralized organization. In its 1979 annual report, the company described how “In order to be effective in the marketplace, Black & Decker follows a decentralized organizational approach. All business functions (marketing, engineering, manufacturing, etc.) are kept as close as possible to the market to be served.” In effect, each wholly owned subsidiary was granted considerable autonomy to run its own business. By the mid 1980’s, however, this structure was starting to become untenable. New competitors had emerged in the power tool business, including Bosch, Makita, and Panasonic. As a result, Black & Decker’s monopoly position had eroded. Throughout the 1980’s, the company pursued a strategy of rationalization. Factories were closed and the company consolidated production in fewer, more efficient production facilities. This process was particularly evident in Europe, where different national operating companies had traditionally had their own production facilities. By the 1990’s, however, it was clear that this change had not gone far enough. The rise of powerful retailers such as Home Depot and Lowe’s in the United States had further pressured prices in the power tools market. Black & Decker responded by looking for ways to garner additional manufacturing efficiencies. During this period, Black & Decker shut down several more factories in its long-established subsidiaries and started to shift production to new facilities that it opened in Mexico and China. As this process proceeded, any remaining autonomy the managers of local factories enjoyed was virtually eliminated. Corporate managers became much more aggressive about allocating products to different factories based on a consideration of operating costs. In effect, Black & Decker 's factories now had to compete with each other for the right to make products, and those factories that did not do well in this process were shut down. In 2001, Black & Decker announced yet another restructuring initiative. Among other things, the initiative involved reducing the workforce by 700 people, to 4,500, shutting long-established factories in the United States and Britain, and shifting production to low-cost facilities. By 2004 this process reached a logical conclusion when the company reorganized its power tools business into two separate global divisions-one that was charged with the global development, manufacture, and marketing of Black & Decker power tools, and another that was charged with the same for the company’s professional DeWalt brand. At this point, the company operated some 36 manufacturing facilities, 18 outside the United States in Mexico, China, the Czech Republic, Germany, Italy, and Britain. It had seven design centers, and two basic R&D centers, on in the United States and one in Britain. Increasingly, the design and R&D centers in the United States and Britain took on responsibility for new-product development for the global market. Throughout the early 2000’s, successively larger shares of production were allocated to factories in just three nations, China, Mexico, and the Czech Republic, and in its 2004 annual report, Black & Decker indicated that this process was likely to continue. From the above case write the answer of this question. What are the different ENTRY MODE and GLOBAL MARKETPLACE STRATEGY has been used by the company at different stages of international expansion in various regions? Did they make the right choices?
Case 02: The Black & Decker Evolution Known primarily for its power tools, Black & Decker is one of the world’s older multinational corporations. The company was founded in Baltimore, Maryland, in 1910, and by the end of the 1920’s had become a small multinational company with operations in Canada and Britain. Today the company has two well-known brands, Black & Decker consumer powers tools and its DeWalt brand of professional power tools. It sells its products in over 100 nations, and has revenues in excess of $5 billion, more than half of which are generated outside of the United States. The company grew rapidly during the 1950’s and 196’s due to its strong brand name and near
From the above case write the answer of this question. What are the different ENTRY MODE and GLOBAL MARKETPLACE STRATEGY has been used by the company at different stages of international expansion in various regions? Did they make the right choices?

Trending now
This is a popular solution!
Step by step
Solved in 4 steps

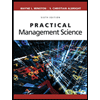
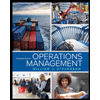
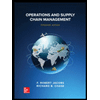
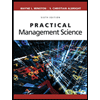
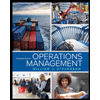
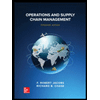
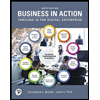
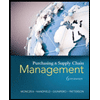
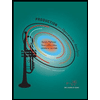