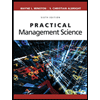
Concept explainers
Astro Winter LLC makes snowplowing equipment. The company buys the engines from a 3rd party vendor – Marshall Engines. Astro Winter has the following production
Marshall Engines makes and delivers the products to Astro Winter during the month the engines are due. Marshall Engines can only manufacture 40 engines in February; 60 in March; 90 in April; and 50 in May. During the same time that Astro Winter makes their snowplows, Marshall Engines has a large order with another client.
Marshall Engine is exploring several options to meet Astro Winter’s production schedule. It can produce up to 30 engines in November, December, and January and carry them in inventory at a cost of $50 per engine per month until it ships them to Astro Winter. For instance, Marshall could build an engine in November, and deliver it to Astro Winter in February and incur $150 in inventory cost. Marshal Engines could also manufacture up to 20 engines in the month they are due on an overtime basis, with an additional cost of $400 per engine.
Marshall Engine wants to determine the least costly production schedule that will meet Astro Winter’s schedule.
Instructions:
1) Develop the LP model and determine the optimal production schedule for Marshall Engine.

Trending nowThis is a popular solution!
Step by stepSolved in 2 steps with 1 images

- Embassy Motorcycles (EM) manufactures two lightweight motorcycles designed for easy handling and safety. The EZ-Rider model has a new engine and a low profile that make it easy to balance. The Lady-Sport model is slightly larger, uses a more traditional engine, and is specifically designed to appeal to women riders. Embassy produces the engines for both models at its Des Moines, Iowa, plant. Each EZ-Rider engine requires 6 hours ofarrow_forwardInventory A certain bookstore chain has two stores, one in San Francisco and one in Los Angeles. It stocks three kinds of books: hardcover, softcover, and plastic (for infants). At the beginning of January, the central computer showed the following books in stock. Hard Soft Plastic San Francisco 1,000 3,000 6,000 Los Angeles 1,000 6,000 3,000 Its sales in January were as follows: 600 hardcover books, 1,300 softcover books, and 1,900 plastic books sold in San Francisco, and 300 hardcover, 300 softcover, and 500 plastic books sold in Los Angeles. The bookstore chain actually maintained the same sales figures for the first 6 months of the year. Each month, the chain restocked the stores from its warehouse by shipping 500 hardcover, 1,400 softcover, and 1,400 plastic books to San Francisco and 600 hardcover, 600 softcover, and 600 plastic books to Los Angeles. (a) Use matrix operations to determine the total sales over the 6 months, broken down by store and type of book.…arrow_forwardHudson Corporation is considering three options for managing its data processing operation: continuing with its own staff, hiring an outside vendor to do the managing (referred to as outsourcing), or using a combination of its own staff and an outside vendor. The cost of the operation depends on future demand. The annual cost of each option (in thousands of dollars) depends on demand as follows: Demand Staffing Options High Medium Low Own staff 600 550 350 Outside vendor 900 650 450 Combination 700 600 400 a. If the demand probabilities are 0.4, 0.25, and 0.35, which decision alternative will minimize the expected cost of the data processing operation? Own Staff What is the expected annual cost associated with that recommendation? If required, round your answer to the nearest thousand of dollars. Expected annual cost = $ ___________arrow_forward
- Zucchero Sugar, Inc. has six processing departments for refining sugar—Affination, Carbonation, Decolorization, Boiling, Recovery, and Packaging. Conversion costs are added evenly throughout each process. Data from the month of August for the Recovery Department are as follows: Metric Tons Beginning Work−in−Process Inventory 0 Transferred in 22,000 Ending Work−in−Process Inventory 6,000 Costs Beginning Work−in−Process Inventory $0 Costs added during August : Direct materials 530,000 Direct labor 250,000 Manufacturing overhead 105,000 Total costs added during August $885,000 The ending Work−in−Process Inventory is 100% and 95% complete with respect to direct materials and conversion costs, respectively. The weighted−average method is used. How many metric tons of sugar were refined and transferred to the Packaging Department in August? A. 6,000 metric tons B.…arrow_forwardFive to six times a year, Kicker puts on tent sales in various cities throughout Oklahoma and the surrounding states. The tent sales are designed to show Kicker customers new products, engender enthusiasm about those products, and sell soon to be out-of-date products at greatly reduced prices. Each tent sale lasts one day and requires parking lot space to set up the Kicker semitrailer; a couple of show cars; a disc jockey playing music; a tent to sell Kicker merchandise, distribute brochures, and so on. Last year, the Austin, TX tent sale was held in a corner of the parking lot outside the city exhibition hall where the automotive show was in progress. Because most customers were interested more in the new model cars than in the refurbishment of their current cars, foot traffic was low. In addition, customers did not want to carry speakers and amplifiers all the way back to where they had originally parked. Total direct costs for this tent sale were $14,300. Direct costs…arrow_forwardA linear programming computer package is needed. The Silver Star Bicycle Company will be manufacturing both men's and women's models for its Easy-Pedal 10-speed bicycles during the next two months. Management wants to develop a production schedule indicating how many bicycles of each model should be produced in each month. Current demand forecasts call for 150 men's and 125 women's models to be shipped during the first month and 200 men's and 150 women's models to be shipped during the second month. Additional data are shown. Model Men's Women's Production Costs men's model in month 1 women's model in month 1 $120 men's model in month 2 $90 Labor Requirements (hours) Assembly Manufacturing 2.0 1.6 bicycles 1.5 Last month the company used a total of 1,000 hours of labor. The company's labor relations policy will not allow the combined total hours of labor (manufacturing plus assembly) to increase or decrease by more than 100 hours from month to month. In addition, the company charges…arrow_forward
- Practical Management ScienceOperations ManagementISBN:9781337406659Author:WINSTON, Wayne L.Publisher:Cengage,Operations ManagementOperations ManagementISBN:9781259667473Author:William J StevensonPublisher:McGraw-Hill EducationOperations and Supply Chain Management (Mcgraw-hi...Operations ManagementISBN:9781259666100Author:F. Robert Jacobs, Richard B ChasePublisher:McGraw-Hill Education
- Purchasing and Supply Chain ManagementOperations ManagementISBN:9781285869681Author:Robert M. Monczka, Robert B. Handfield, Larry C. Giunipero, James L. PattersonPublisher:Cengage LearningProduction and Operations Analysis, Seventh Editi...Operations ManagementISBN:9781478623069Author:Steven Nahmias, Tava Lennon OlsenPublisher:Waveland Press, Inc.
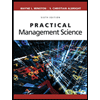
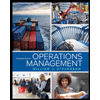
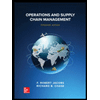
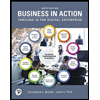
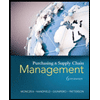
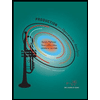