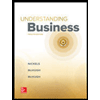
AccuSound Corporation manufactures printed circuits for stereo amplifiers. A common product defect is a “drift” caused by failure to maintain precise heat levels during the production process. Rejects from the 100 percent testing program can be reworked to acceptable levels if the defect is drift. However, in a recent analysis of customer complaints, Marie Allen, the assistant controller, and the quality control engineer determined that normal rework does not bring the circuits up to standard. Sampling showed that about half of the reworked circuits will fail after extended amplifier operation. The incidence of failure in the reworked circuits is projected to be about 10 percent over five years.
Unfortunately, there is no way to determine which reworked circuits will fail, because testing will not detect the problem. The rework process could be changed to correct the problem, but the cost-benefit analysis for the suggested change indicates that it is not economically feasible. AccuSound’s marketing analyst has indicated that this problem will have a significant impact on the company’s reputation and customer satisfaction. Consequently, the board of directors would interpret this problem as having serious negative implications for the company’s profitability.
Allen included the circuit failure and rework problem in her report prepared for the upcoming quarterly meeting of the board of directors. Due to the potential adverse economic impact, Allen followed a long-standing practice of highlighting this information. After reviewing the reports to be presented, the plant manager and his staff complained to the controller that he should control his people better. “We can’t upset the board with this kind of material. Tell Allen to tone that down. Maybe we can get it by the board in this meeting and have some time to work on it. People who buy those cheap systems and play them that loud shouldn’t expect them to last forever.”
The controller called Allen into his office and said, “Marie, you’ll have to bury this one. The probable failure of reworks can be mentioned briefly in the oral presentation, but it should not be mentioned or highlighted in the advance material mailed to the board.”
Allen feels strongly that the board will be misinformed on a potentially serious loss of income if she follows the controller’s orders. Allen discussed the problem with the quality control engineer, who simply remarked, “That’s your problem, Marie.”
What should Marie Allen do?
(You may select more than answer)
Option A : Protect the interests of the company, others in the company and herself.
Option B : Allen must take some action to reduce her vulnerability.
Option C : Allen should write a report to the controller detailing the probable failure of reworks, the analysis made by her and the quality control engineer, and the controller's instructions in this matter.

Trending nowThis is a popular solution!
Step by stepSolved in 2 steps

- The school board is trying to evaluate a new math program introduced to second-graders in five elementary schools across the county this year. A sample of the student scores onstandardized math tests in each elementary school yielded the following data: Construct a c-chart for test errors, and set the control limits to con tain 99 .73% of the random variation in test scores. What does the chart tell you? Has the new math program been effective?arrow_forwardBuilder UB, situated in Toronto, specialises in home and land packages throughout the North and South Islands. The team in charge of construction inspection examined a sample of newly constructed homes for flaws and leaks. Ten samples were examined for flaws or compliance issues. Each sample had a 50-unit size. The outcomes are listed below. Please offer your thoughts on C and P charts for process control.arrow_forwardExplain the concept of the control chart and identify out-of-control signals on a control chart. Within your answer, explain what you would do if you were a Quality Manager making your rounds throughout the plant and found a control chart that indicated an out-of-control situation.arrow_forward
- Describe the difference between six sigma and three sigma certificates. What percentage of products have no defects under six-sigma and three-sigma for Johnson & Johnsonarrow_forwardA shirt manufacturer buys cloth by the 100-yard roll from a supplier. For setting up a control chart to manage the irregularities (e.g., loose threads and tears), the following data were collected from a sample provided by the supplier. SAMPLE 1 2 3 4 5 6 7 8 9 10 IRREGULARITIES 3 5 2 6 5 4 6 3 4 5 Determine the c¯�¯ , Sc�� , UCL and LCL for a c-chart with z = 2. Note: Round your answers to 2 decimal places. Suppose the next five rolls from the supplier had three, two, five, three, and seven irregularities. Is the supplier process under control? multiple choice Yes Noarrow_forwardTwenty samples of 100 items each were inspected when a process was considered to be operating satisfactorily. In the 20 samples, a total of 140 items were found to be defective. (a) What is an estimate of the proportion defective when the process is in control? (b) What is the standard error of the proportion if samples of size 100 will be used for statistical process control? (Round your answer to four decimal places.) (c) Compute the upper and lower control limits for the control chart. (Round your answers to four decimal places.) UCL = LCL =arrow_forward
- Costs incurred by a nonconforming product detected before it is shipped to customers are: a. internal failure costs b. prevention costs c. appraisal costs d. external failurearrow_forwardWalton Company has measured its quality costs for the past two years. After the company gathers its quality cost data, it summarizes those costs using the four categories shown below: Last Year This Year Prevention costs $ 349,900 $ 617,500 Appraisal costs $ 449,500 $ 523,200 Internal failure costs $ 805,800 $ 520,000 External failure costs $ 1,111,000 $ 673,200 1. Calculate the total cost of quality last year and this year. 2. For last year, calculate the cost in each of the four categories as a percent of the total cost of quality. 3. For this year, calculate the cost in each of the four categories as a percent of the total cost of quality.arrow_forwardThe smallest defect in a computer chip will render the entire chip worthless. Therefore, tight quality control measures must be established to monitor these chips. In the past, the percent defective at Chieh Lee's Computer Chips has been 1.5%. The sample size is 1,000. Determine upper and lower control chart limits for these computer chips. Use z = 3. Upper Control Limit (UCL) = (round your response to four decimal places). Lower Control Limit (LCLp) = (round your response to four decimal places).arrow_forward
- The manufacturer bakery had provided us with their specification limit, which was 145 g -155 g. Out of the 50 biscuit packets, it was observed that 5% weighed between 145.5 g and 146 g while 2% of the packets weighed between 153.95 g and 154.5 g. Which of the following groups can be categorised as bad quality? The 5% of the sample that weighed between 145.5 g and 146 g. The 2% of the sample that weighed between 153.95g and 154.5g. Both of the groups. None of the above.arrow_forwardWhat is the effect on the cost of quality to the customer when in an agreement with a supplier to ensure all parts are within tolerance before shipment? My answer: Prevention and appraisal costs will increase while internal failure costs can either increase or decrease and external will decrease.arrow_forwardWalton Company has measured its quality costs for the past two years. After the company gathers its quality cost data, it summarizes those costs using the four categories shown below: Last Year This Year Prevention costs $ 349,900 $ 617,500 Appraisal costs $ 449,500 $ 523,200 Internal failure costs $ 805,800 $ 520,000 External failure costs $ 1,111,000 $ 673,200 1. Calculate the change in total cost of quality over the two-year period. 2. Is performance trending in a favorable or unfavorable direction?arrow_forward
- Understanding BusinessManagementISBN:9781259929434Author:William NickelsPublisher:McGraw-Hill EducationManagement (14th Edition)ManagementISBN:9780134527604Author:Stephen P. Robbins, Mary A. CoulterPublisher:PEARSONSpreadsheet Modeling & Decision Analysis: A Pract...ManagementISBN:9781305947412Author:Cliff RagsdalePublisher:Cengage Learning
- Management Information Systems: Managing The Digi...ManagementISBN:9780135191798Author:Kenneth C. Laudon, Jane P. LaudonPublisher:PEARSONBusiness Essentials (12th Edition) (What's New in...ManagementISBN:9780134728391Author:Ronald J. Ebert, Ricky W. GriffinPublisher:PEARSONFundamentals of Management (10th Edition)ManagementISBN:9780134237473Author:Stephen P. Robbins, Mary A. Coulter, David A. De CenzoPublisher:PEARSON
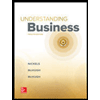
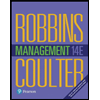
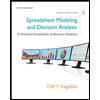
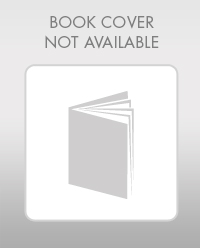
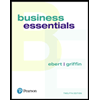
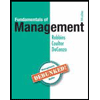