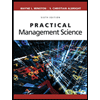
Practical Management Science
6th Edition
ISBN: 9781337406659
Author: WINSTON, Wayne L.
Publisher: Cengage,
expand_more
expand_more
format_list_bulleted
Concept explainers
Topic Video
Question
ABC Company is planning to stock its product which is classified as an inventory item. The company has developed the following information: Annual usage is 16,200 units, cost of the inventory per unit is P730; ordering cost is P220 per order; carrying cost is 28% of inventory value per year. Determine the optimum number of units per order.
Expert Solution

This question has been solved!
Explore an expertly crafted, step-by-step solution for a thorough understanding of key concepts.
This is a popular solution
Trending nowThis is a popular solution!
Step by stepSolved in 2 steps

Knowledge Booster
Learn more about
Need a deep-dive on the concept behind this application? Look no further. Learn more about this topic, operations-management and related others by exploring similar questions and additional content below.Similar questions
- answer in text form please (without image)arrow_forwardA company has an annual demand for a specific item of 12,000 units. The carrying cost per unit per year is R.50, and the cost to place an order is R80. Calculate the Economic Order Quantity (EOQ) and also explain the following related terms • Re-order Level, • Ordering Point, • and Minimum Level.arrow_forwardThe seasonal demand for a particular product is given below: Period 12 3 4 56 Demand 300 450 100 450 450 100 The fixed parameters are: Fixed Cost $8 Unit Production Cost $1 Holding Cost $1.3 Calculate total ordering cost using the following three methods: i) Lot-for-Lot ii) Wagner-Whitin algorithm iii) Fixed order quantityarrow_forward
- The distribution manager for Putnam Corporation is trying to establish the most economic ordering policy for the standard model of its best-selling microwave oven. He has control of the finished goods warehouse for the factory and must satisfy wholesaler demand. The following information is available: Wholesale value $100 Annual demand 50,000 units Std. Deviation of Demand 30 units per day Working year 250 days Production lead time 9 days Ordering cost for production $1,800 Holding cost per unit per year 20% of value Desired service level 96 percent: If Putnam wishes to use the periodic review system, what should be the safety stock, reorder point? If the current on hand inventory is 1,000 units, how many units should be ordered?arrow_forwardThe seasonal demand for a particular product is given below: Period 1 2 3 4 5 6 Demand 300 450 100 450 450 100 The fixed parameters are: Fixed Cost $8 Unit Production Cost $1 Holding Cost $ 1.3 Calculate total ordering cost using following three methods: i) Lot-for-Lot ii) Wagner-Whitin algorithm iii) Fixed order quantity Which method you will chose to order and why? Please do fast... ASAP... do fastarrow_forwardDouble T appliance is a retailer of small appliances in West Texas. Double T gets all of their merchandise from GE which it then sells to the people of the South Plains. Their annual demand is 10,000 units and the ordering cost is $100 per order. The carrying cost per unit is $50.00 What is their expected annual carrying cost (not including the costs of the goods) if the Economic Order Quantity is used and is equal to 200 units?arrow_forward
- a) What is the economic order quantity? b) Find the annual holding costs.c) Find the annual ordering costs.d) What is the reorder point?arrow_forwardGiven the following information, formulate an inventory management system. The item is demanded 50 weeks a year. Item cost $ 8.00 Standard deviation of weekly demand 25 per week Order cost $ 298.00 Lead time 4 weeks Annual holding cost (%) 29 % of item cost Service probability 98 % Annual demand 28,100 Average demand 562 per week a. Determine the order quantity and reorder point. (Use Excel's NORMSINV() function to find the correct critical value for the given α-level. Do not round intermediate calculations. Round "z" value to 2 decimal places and final answer to the nearest whole number.) Optimal order quantity units Reorder point units b. Determine the annual holding and order costs. (Round your answers to 2 decimal places.) Holding cost $ Ordering cost $ c. Assume a price break of $50 per order was offered for purchase quantities of 2,100 or more units per order. If…arrow_forwardPls solve this question correctly in 5 min i will give u like for sure Question # 1 Teresa Cohan is attempting to perform an inventory analysis on one of her most popular products. Annual demand for this product is 5,000 units; unit cost $200; carrying cost is considered to be approximately 10% of the unit price. Order costs for her company typically run nearly $30 per order and lead time averages 10 days. Discounted unit cost of Rs. $150 (carrying cost remain the same) for more than 300 units is also being offered. (Assume a 50-week year. a)What is economic order quantity? b)What is the reorder point? c)What is the total carrying + ordering cost? d)What is optimal number of orders per year? e)Would you recommend availing the discount?arrow_forward
- ARP Engines is a producer of outboard motors and ships worldwide. The company has recently set up a new distribution centre and wants to decide on an inventory policy for one of its products. It has determined the following pertinent information: expected average weekly demand weekly demand standard deviation holding cost production setup cost delivery lead time 400 motors 50 motors $25/motor $5,000/order 3 weeks The company plans to operate 5 days per week, 50 weeks per year. a. Compute the Economic Order Quantity (ignore the variation in demand) given the informa- tion gathered by the company. What is the time between orders and the total cost of operating the EOQ inventory policy? b. The company is considering using the EOQ as the order quantity in a continuous review system. Compute the reorder point and safety stock to meet a service level of 99%. What is the cost of this Q system inventory policy? c. If the company thinks to use the TBO (computed in part a) as the period for a…arrow_forwardgainesvile cigar stocks cuban cigars that have variable lead times because of the difficulty in importing the product: lead time is normally distributed with an average of 6 weeks and a standard deviation of 2 weeks. demand is also a variable and normally distributed with a mean of 200 cigars per week and a standard deviation of 25 cigars. a) for a 90% of service level, what is the rop?arrow_forwardPaulin’s muffler shop has one standard muffler that fits a large variety of cars. The shop wishes to establish a periodic review system to manage inventory of this standard muffler. Use the information table to determine the optimal inventory target level (or order-up to level). Annual demand 3,910 mufflers ordering cost $75 per order S/D of daily demand 6 mufflers/wk. day service probability 87% Item cost $ 27.00 per muffler lead time 2 wk. Days Annual holding cost 36 % of item value wk. Days 230 per year Review period 18 working days What is the optimal target levels (order up to levels) use excels NORMSINVI() function to find the correct critical value for the given a-level. Do not round intermediate calculations. Round value 2 decimal places and final answer to the nearest whole number If the service probability is 90%, the optimal target level will increase, decrease or…arrow_forward
arrow_back_ios
SEE MORE QUESTIONS
arrow_forward_ios
Recommended textbooks for you
- Practical Management ScienceOperations ManagementISBN:9781337406659Author:WINSTON, Wayne L.Publisher:Cengage,Operations ManagementOperations ManagementISBN:9781259667473Author:William J StevensonPublisher:McGraw-Hill EducationOperations and Supply Chain Management (Mcgraw-hi...Operations ManagementISBN:9781259666100Author:F. Robert Jacobs, Richard B ChasePublisher:McGraw-Hill Education
- Purchasing and Supply Chain ManagementOperations ManagementISBN:9781285869681Author:Robert M. Monczka, Robert B. Handfield, Larry C. Giunipero, James L. PattersonPublisher:Cengage LearningProduction and Operations Analysis, Seventh Editi...Operations ManagementISBN:9781478623069Author:Steven Nahmias, Tava Lennon OlsenPublisher:Waveland Press, Inc.
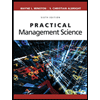
Practical Management Science
Operations Management
ISBN:9781337406659
Author:WINSTON, Wayne L.
Publisher:Cengage,
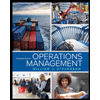
Operations Management
Operations Management
ISBN:9781259667473
Author:William J Stevenson
Publisher:McGraw-Hill Education
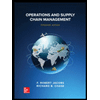
Operations and Supply Chain Management (Mcgraw-hi...
Operations Management
ISBN:9781259666100
Author:F. Robert Jacobs, Richard B Chase
Publisher:McGraw-Hill Education
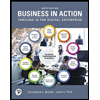
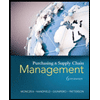
Purchasing and Supply Chain Management
Operations Management
ISBN:9781285869681
Author:Robert M. Monczka, Robert B. Handfield, Larry C. Giunipero, James L. Patterson
Publisher:Cengage Learning
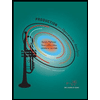
Production and Operations Analysis, Seventh Editi...
Operations Management
ISBN:9781478623069
Author:Steven Nahmias, Tava Lennon Olsen
Publisher:Waveland Press, Inc.