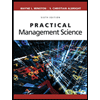
Practical Management Science
6th Edition
ISBN: 9781337406659
Author: WINSTON, Wayne L.
Publisher: Cengage,
expand_more
expand_more
format_list_bulleted
Concept explainers
Question
A home improvement store sells hydrangea plants during the spring planting season. The hydrangeas cost the store $15 per unit, and sell to customers for $45, but any leftovers at the end of the season are salvaged to a local landscaper for $7/unit. A competitor has advertised that it guarantees 99% of customers find the product they’re looking for in stock. The competitor’s posted price for hydrangeas is $50, and they salvage to the same local landscaper for $7/ hydrangea plant. If the competitor’s advertised service level is correct for hydrangeas and they follow an optimal stocking policy, what does it imply their cost per hydrangea is?
Expert Solution

This question has been solved!
Explore an expertly crafted, step-by-step solution for a thorough understanding of key concepts.
Step by stepSolved in 2 steps

Knowledge Booster
Learn more about
Need a deep-dive on the concept behind this application? Look no further. Learn more about this topic, operations-management and related others by exploring similar questions and additional content below.Similar questions
- Currently, a company places orders for diaries to give away as tokens for its customers. Each diary costs the company $137.50. It costs the company $0.65 to place an order for the diaries and $0.87 to carry each diary annually in its inventory. The suppliers wish to offer the company a deal on the cups, by having it pay $85 for each diary, but ONLY if the company orders in sizes of 500 instead of the usual amount. Annual demand for the cups is 8000. Should the company accept the deal?arrow_forwardConsider a two-tier supply chain with one manufacturer and one retailer whointeract in a single selling season. The manufacturer sells a product to the retailer, who in turn sells in the market. Demand E is uncertain with cumulative distribution function F (·)and probability density function f (·). Since the production lead time is much longer thanthe selling season, the retailer must place a single order before demand is realized and cannotreplenish her inventory during the season. The retailer sells the product at an exogenousand fixed retail price r. The manufacturer produces the product at a unit cost of c. Themanufacturer uses a linear sales rebate contract and determines the following contract terms:For each unit ordered, he charges the retailer a wholesale price w, and for each unit sold, hepays the retailer a rebate s. Assume that the product has zero salvage value at the end ofthe season, and the inventory holding cost during the season is…arrow_forwardAlgro Inc. keeps a wide range of parts and materials on hand for use in its production processes. Management has recently had difficulty managing parts inventory as demand for its finished goods has increased; they frequently run out of some critical parts while having an endless supply of others. They would like to classify their parts inventory according to the ABC approach to better control inventory. The following is a list of parts, along with their annual usage and unit value: Item Annual Unit Item Annual Unit Number Usage Cost Number Usage Cost 1 36 $350 2 510 30 3 50 23 4 300 45 5 18 1900 6 500 8 7 710 4 8 80 26 9 344 28 10 67 440 11 510 2 12 682 35 13 1216 95 50 14 10 3 15 820 1 KARAN2222222222 16 60 $610 17 120 20 18 270 15 19 45 50 20 19 3200 21 910 3 12 4750 23 30 2710 24 24 1800 25 870 105 26 244 30 27 750 15 28 45 110 29 46 160 30 165 25 a. Classify the inventory items according to the ABC approach using the dollar value of annual demand. b. Clearly explain why you…arrow_forward
- The army is attempting to determine the optimal replacement age for a piece of field equipment. The equipment costs $280,000 to replace. The manufacturer will supply a rebate toward the next purchase that declines at a rate of 20 percent per year. Maintenance costs for the first year are estimated to be $1,000, and they increase roughly at the rate of 18 percent per year. Estimate the number of years that the army should hold the equipment before making a replacement.(Production and Operation Analysis by Steven Nahmias, 7th edition, pg.774 Problem # 24)arrow_forwardLPM Corp. produces and sells two types of frozen burgers, Turkey Burgers and Veggie Burgers. In the most recent month, the firm sold 12,000 Turkey Burgers and 8,000 Veggie Burgers. Turkey Burgers sold for $14.00 per box and variable costs were $7.40 per box. The Veggie Burgers sold for $16.00 per box and variable costs were $8.25 per box. The fixed expenses of the entire company were $41,160. If the sales mix were to shift toward the Turkey Burgers product line with total sales volume remaining constant at 20,000, the overall break-even point for the entire company:arrow_forwardJasmine owns 12 apartment buildings in a college town, which it rents exclusively to students. Each apartment building contains 120 rental units, but the owner is having cash flow problems due to an average vacancy rate of nearly 50 percent. The apartments in each building have comparable floor plans, but some buildings are closer to campus than others. Jasmine’s accumulated data from last year on the number of apartments rented, the rental price (in dollars), and the amount spent on advertising (in hundreds of dollars) at each of the 12 apartments are available below. These data, along with the distance (in miles) from each apartment building to campus, are presented below. Jasmine is looking for expert advice on the available data to inform administrative and business policy. By applying this scenario, help her regress the quantity demanded of her apartments on price, advertising, and distance datasets by using Excel or SPSS. Observation or (Number of Apartments) Quantity…arrow_forward
- A manufacturing plant procures 100,000 filters per year. Each unit has a fixed order cost is $50. To maintain the inventory in optimal conditions, there is a carrying cost rate of 10% per year. The vendor of filters has offered the following price breaks: for orders of more than 5,000 filters, cost is $4.50/unit; for orders between 1,000 and 5,000 filters, cost is $4.75/unit; orders less than 1,000 filters have a cost of $5.00/unit. Find the economic order quantity. Calculate the average annual cost for the optimal solution.arrow_forwardTaylor Smith owns a small clothing company, Cuteness for You, that offers an online subscription and personal shopping service targeted at busy families with children aged newborn to five years old. Currently, Taylor has one level of subscription service, the standard service. For $100 a month, the standard service provides its customers a monthly delivery of 10 clothing items carefully chosen to match the child's size, gender, and emerging style. The online clothing subscription market is fairly new but is growing rapidly and thus Taylor is considering extending the product line to increase its market share and profits. Taylor is debating whether to add a premium subscription service featuring profitable high-markup items for $125 per month, a basic subscription service that contains lower-markup popular items priced at $75 per month, or possibly both. Taylor knows that the new product lines provide an opportunity to attract more customers and possibly increase revenues and profit,…arrow_forward
arrow_back_ios
arrow_forward_ios
Recommended textbooks for you
- Practical Management ScienceOperations ManagementISBN:9781337406659Author:WINSTON, Wayne L.Publisher:Cengage,Operations ManagementOperations ManagementISBN:9781259667473Author:William J StevensonPublisher:McGraw-Hill EducationOperations and Supply Chain Management (Mcgraw-hi...Operations ManagementISBN:9781259666100Author:F. Robert Jacobs, Richard B ChasePublisher:McGraw-Hill Education
- Purchasing and Supply Chain ManagementOperations ManagementISBN:9781285869681Author:Robert M. Monczka, Robert B. Handfield, Larry C. Giunipero, James L. PattersonPublisher:Cengage LearningProduction and Operations Analysis, Seventh Editi...Operations ManagementISBN:9781478623069Author:Steven Nahmias, Tava Lennon OlsenPublisher:Waveland Press, Inc.
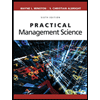
Practical Management Science
Operations Management
ISBN:9781337406659
Author:WINSTON, Wayne L.
Publisher:Cengage,
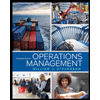
Operations Management
Operations Management
ISBN:9781259667473
Author:William J Stevenson
Publisher:McGraw-Hill Education
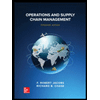
Operations and Supply Chain Management (Mcgraw-hi...
Operations Management
ISBN:9781259666100
Author:F. Robert Jacobs, Richard B Chase
Publisher:McGraw-Hill Education
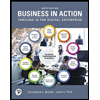
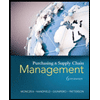
Purchasing and Supply Chain Management
Operations Management
ISBN:9781285869681
Author:Robert M. Monczka, Robert B. Handfield, Larry C. Giunipero, James L. Patterson
Publisher:Cengage Learning
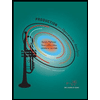
Production and Operations Analysis, Seventh Editi...
Operations Management
ISBN:9781478623069
Author:Steven Nahmias, Tava Lennon Olsen
Publisher:Waveland Press, Inc.