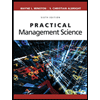
Practical Management Science
6th Edition
ISBN: 9781337406659
Author: WINSTON, Wayne L.
Publisher: Cengage,
expand_more
expand_more
format_list_bulleted
Question
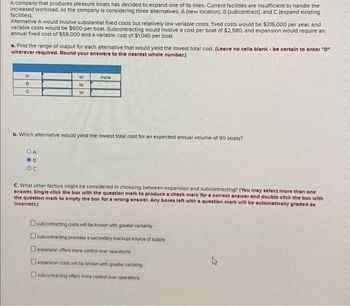
Transcribed Image Text:A company that produces pleasure boats has decided to expand one of its lines. Current facilities are insufficient to handle the
increased workload, so the company is considering three alternatives. A (new location), B (subcontract), and C (expand existing
facilities).
Alternative A would involve substantial fixed costs but relatively low variable costs: fixed costs would be $315,000 per year, and
variable costs would be $600 per boat. Subcontracting would involve a cost per boat of $2,580, and expansion would require an
annual fixed cost of $58,000 and a variable cost of $1,040 per boat.
a. Find the range of output for each alternative that would yield the lowest total cost. (Leave no cells blank be certain to enter "0"
wherever required. Round your answers to the nearest whole number.)
A
B
C
or
to
OA
OB
OC
to
more
b. Which alternative would yield the lowest total cost for an expected annual volume of 90 boats?
c. What other factors might be considered in choosing between expansion and subcontracting? (You may select more than one
answer. Single click the box with the question mark to produce a check mark for a correct answer and double click the box with
the question mark to empty the box for a wrong answer. Any boxes left with a question mark will be automatically graded as
Incorrect.)
subcontracting costs will be known with greater certainty
subcontracting provides a secondary (backup) source of supply
expansion offers more control over operations
expansion costs will be known with greater certainty
subcontracting offers more control over operations
s
Expert Solution

This question has been solved!
Explore an expertly crafted, step-by-step solution for a thorough understanding of key concepts.
This is a popular solution
Trending nowThis is a popular solution!
Step by stepSolved in 5 steps

Knowledge Booster
Similar questions
- The owner of Genuine Subs, Inc., hopes to expand the present operation by adding one new outlet. She has studied three locations. Each would have the same labor and materials costs (food, serving containers, napkins, etc.) of $1.76 per sandwich. Sandwiches sell for $8.00 each in all locations. Rent and equipment costs would be $5,000 per month for location A, $5,500 per month for location B, and $5,800 per month for location C. a. Determine the volume necessary at each location to realize a monthly profit of $10,000. (Do not round Intermediate calculations. Round your answer to the nearest whole number.) Location Monthly Volume A B C b-1. If expected sales at A, B, and C are 21,000 per month, 22,000 per month, and 23,000 per month, respectively, calculate ge profit of the each locations? (Do not round Intermediate calculations. Round your answer to the nearest whole number.) Location A Monthly Profits B C b-2. Which location would yield the greatest profits? e here to search R T J O…arrow_forwardIn deciding on where to locate their next grocery store, Publix narrowed it down to 3 locations (St. Augustine, the Airport area, or the Westside). They are using 2 criteria to make their decisions costs (with a weight of 70%) and customer base (with a weight of 30%). Each item was scored on a 10-point scale with 10 being the highest. St. Augustine rated a score of 4 for cost and 10 for customer base; the Airport area rated a score of 6 for cost and 5 for the customer base, and the Westside rated a score of 8 for cost and 2 for the customer base. __________ 2a. What is the computed mean score for each of the 3 locations? __________ 2b. Which location should be chosen based on the highest score?arrow_forwardMetro has initiated discussions on attracting rail service. A depot would need to be constructed, which would require $2.5million in land and $7.5 million in construction costs. Annual operating and maintenance costs (O&M) for the facility would be $150,000, and personnel costs would be an additional $110,000. Other assorted costs would be born by the railroad and federal authorities. Annual benefits (B) of the rail service are estimated as listed: $120,000 for Railroad annual payments, $25,000 for Rail tax charged to passengers, $20,000 for Convenience benefits to local residents, and $12,000 for Additional tourism dollars for Metro. Apply the B-C ratio method, with a MARR of 8% per year and 20 year study period, to determine if the rail service should be established. a. BC ratio=2.12, good project b. BC ratio=-1.76, good project c. BC ratio=1.69, good project d. BC ratio=0.14, not good projectarrow_forward
- A plastic manufacturing company is considering 2 alternative locations for a new facility. The management considered 2 alternatives: Sta. Rosa and Sta. Rita. The fixed costs for Sta. Rosa is Php1M and variable cost is Php25 per unit. On the other hand, the fixed costs for Sta. Rita is Php1.5M and variable cost is Php23 per unit. 1. If the company plans on producing 50,000 units which location would be more attractive? 2. At what volume the two alternatives equal in cost?arrow_forwardSmart Corporation produces and sells laptops. It has four factories and four shops located in different cities. The management of Smart Corporation has just bought a new machine that can improve its productivity. After using the new machine, Smart Corporation's production has increased by 500 units. Therefore, the management has decided to open a new shop and two cities are under their consideration. The two cities under consideration are City E and City F. The shipping cost per unit (RM), factory supplies, and shop demands are as follows Factory Shop Supply A I || IV Demand B 30 40 35 40 с 30 35 50 30 600 700 D E F 45 55 50 45 40 50 35 60 30 45 40 45 55 45 50 55 400 600 500 500 700 800 700 600 1. Determ the best choice of city to open the new shop. Why? 2. Due to the shipping limitation, no unit shall be shipped from I to City B. What would happen to the answer in (a)?arrow_forwardThe Candle Company plans to open a new retail store in Portland, Maine. The store will sell specialty candles for an average of $10 each. The average variable costs per candle are as follows: Wax $4 Other additives $2 Base $1 The company is negotiating its lease for the new location. The landlord has offered two leasing options: Option A) a lease of $2,500 per month; or Option B) a monthly lease cost of $2,000 plus 10% of the company's monthly sales revenue. The lease option that is more attractive for the company under its current sales expectations is option B, the fixed lease payment plus sales based commission because it results in the lowest total lease costs The indifference point is The company expects to sell approximately 400 candles per month. Requirement 2. At what level of sales (in units) would the company be indifferent between the two lease options? Show your proof. candles. Begin by selecting the equation to determine the indifference point. (Abbreviations used" FC =…arrow_forward
- During a major expansion in 2004, Douwalla’s Import Company developed a new processing line for which the delivered equipment cost was $1.75 million. This year, the board of directors decided to expand into new markets and expects to build the current version of the same line. Estimate the cost if the following factors are applicable: construction cost factor is 0.20, installation cost factor is 0.50, indirect cost factor applied against equipment is 0.25, and the total plant cost index has risen from 2509 to 3713 over the years.arrow_forwardPlease answer the question as quickly as possible A toy company has developed two new toys for possible inclusion in its product line for the upcoming Christmas season. Setting up the production facilities to begin production would cost $50,000 for toy 1 and $80,000 for toy 2. Once these costs are covered, the toys would generate a unit profit of $10 for toy 1 and $15 for toy 2. The company has two factories that are capable of producing these toys. However, to avoid doubling the start-up costs, just one factory would be used, where the choice would be based on maximizing profit. For administrative reasons, the same factory would be used for both new toys if both are produced. Toy 1 can be produced at the rate of 50 per hour in factory 1 and 40 per hour in factory 2. Toy 2 can be produced at the rate of 40 per hour in factory 1 and 25 per hour in factory 2. Factories 1 and 2, respectively, have 500 hours and 700 hours of production time available before Christmas that could…arrow_forwardThe Giant Farmer Company processes food for sale in discount food stores. It has two plants: one in Chicago and one in Houston. The company also operates warehouses in Miami, Florida; Denver, Colorado; Lincoln, Nebraska; and Jackson, Mississippi. Forecasts indicate that demand soon will exceed supply and that a new plant with a capacity of 8,000 cases per week is needed. The question is where to locate the new plant. Three potential sites are Buffalo, Atlanta, and Memphis. The two tables below give data on capacities, forecasted demand, and shipping costs that have been gathered. Plant Chicago Houston Capacity (cases per week) New plant Warehouse Plant Chicago Houston Buffalo (alternative 1) Atlanta (alternative 2) Memphis (alternative 3) For each alternative new plant location, determine the total cost of the shipping pattern that will minimize total transportation costs. Where should the new plant be located? If the new plant is located in Buffalo, the optimal cost is $ (Enter your…arrow_forward
- K Subway, with more than 27,000 outlets in the U.S., is planning for a new restaurant in Buffalo, New York. Three locations are being considered. The following table gives the factors for each site. Factor Space Costs Traffic density Neighborhood income Zoning laws a) Based on the given information, the best location in Buffalo for Subway to open the new restaurant is Weight 0.25 0.25 0.20 0.15 0.15 Maitland 65 40 55 45 85 Baptist Church 75 85 85 70 20 Northside Mall 80 25 55 35 85 with aarrow_forwardProblem 8-4 (Algo) A company that produces pleasure boats has decided to expand one of its lines. Current facilities are insufficient to handle the increased workload, so the company is considering three alternatives, A (new location), B (subcontract), and C (expand existing facilities). Alternative A would involve substantial fixed costs but relatively low variable costs: fixed costs would be $285,000 per year, and variable costs would be $570 per boat. Subcontracting would involve a cost per boat of $2,570, and expansion would require an annual fixed cost of $59,000 and a variable cost of $1,040 per boat. a. Find the range of output for each alternative that would yield the lowest total cost. (Leave no cells blank - be certain to enter "0" wherever required. Round your answers to the nearest whole number.) A B с Answer is not complete. or to to more b. Which alternative would yield the lowest total cost for an expected annual volume of 70 boats? C. What other factors might be…arrow_forwardThe As-You-Like-It Hamburger Shop is considering adding a new location. The investment at each of the four potential sites is the same. The price they can charge for hamburgers is set by the competition in the area. Given the information below, which site is expected to be the most profitable? Factor Site A Site B Site C Site D Fixed Cost $10,000 $8,000 $6,000 $11,000 Variable Cost per Unit $ 0.70 $ 0.70 $ 0.85 $ 0.65 Price per Unit $ 1.30 $ 1.20 $ 1.25 $ 1.10 Forecast Volume (Units) 20,000 22,000 18,000 24,000arrow_forward
arrow_back_ios
SEE MORE QUESTIONS
arrow_forward_ios
Recommended textbooks for you
- Practical Management ScienceOperations ManagementISBN:9781337406659Author:WINSTON, Wayne L.Publisher:Cengage,Operations ManagementOperations ManagementISBN:9781259667473Author:William J StevensonPublisher:McGraw-Hill EducationOperations and Supply Chain Management (Mcgraw-hi...Operations ManagementISBN:9781259666100Author:F. Robert Jacobs, Richard B ChasePublisher:McGraw-Hill Education
- Purchasing and Supply Chain ManagementOperations ManagementISBN:9781285869681Author:Robert M. Monczka, Robert B. Handfield, Larry C. Giunipero, James L. PattersonPublisher:Cengage LearningProduction and Operations Analysis, Seventh Editi...Operations ManagementISBN:9781478623069Author:Steven Nahmias, Tava Lennon OlsenPublisher:Waveland Press, Inc.
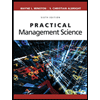
Practical Management Science
Operations Management
ISBN:9781337406659
Author:WINSTON, Wayne L.
Publisher:Cengage,
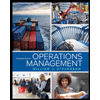
Operations Management
Operations Management
ISBN:9781259667473
Author:William J Stevenson
Publisher:McGraw-Hill Education
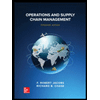
Operations and Supply Chain Management (Mcgraw-hi...
Operations Management
ISBN:9781259666100
Author:F. Robert Jacobs, Richard B Chase
Publisher:McGraw-Hill Education
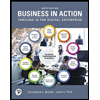
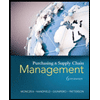
Purchasing and Supply Chain Management
Operations Management
ISBN:9781285869681
Author:Robert M. Monczka, Robert B. Handfield, Larry C. Giunipero, James L. Patterson
Publisher:Cengage Learning
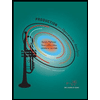
Production and Operations Analysis, Seventh Editi...
Operations Management
ISBN:9781478623069
Author:Steven Nahmias, Tava Lennon Olsen
Publisher:Waveland Press, Inc.