A co-polymer AB2 is to be made from its constituent monomers A and B according to the equation where C is a catalyst required for the reaction. It is known that the reaction also generates an impurity I at a rate of 0.001 moles of I/ mole of AB2 generated. A manufacturing process is set up in such a way that a feed stream containing pure A and B are sent to the reactor along with another stream of catalyst C which contains 400 ppm of I. It is known that a 5% excess of B has been charged into the reactor. The exit stream from the reactor is sent to a separator which generates a product A and B Catalyst +I A + 2B+C →→→ AB2 + C Reactor 3 Separator Figure 2: Polymer synthesis 5 Products and unreacted reactants Catalyst +I stream containing AB2 and any unreacted reactants and a catalyst stream containing the recovered catalyst and any impurities. Assuming a basis of 45 moles/h of product AB2 and steady state, (a) Without performing any calculations, identify the limiting reagent in this reaction. (b) Calculate the composition of the feed stream. (c) How much of the catalyst mixture (C+I) is required for the assumed basis? (d)) Calculate the composition of the catalyst stream leaving the separator (e) In order to reduce the cost of the catalyst, it is suggested that all the recovered catalyst be recycled completely back into the reactor. Is there any issue with this set up? If there are any issues, how can they be rectified? (f) A modified recycle stream is shown in Figure 3. It is desired to maintain the impurity concen- tration at 400 ppm at the inlet to the reactor. How much of the fresh Catalyst (0 ppm of I) must be charged to the reactor to maintain this constraint ? (g) How much of the recovered catalyst is purged? (h) If pure catalyst costs $125/mole and the impure catalyst (400 ppm) costs $ 85/mole, compute if including the recycle stream is cost effective. Fresh catalyst 2 A and B Reactor Separator Recycle 6 Products and unreacted reactants Figure 3: Polymer synthesis with recycle 5 Catalyst +I Purge
A co-polymer AB2 is to be made from its constituent monomers A and B according to the equation where C is a catalyst required for the reaction. It is known that the reaction also generates an impurity I at a rate of 0.001 moles of I/ mole of AB2 generated. A manufacturing process is set up in such a way that a feed stream containing pure A and B are sent to the reactor along with another stream of catalyst C which contains 400 ppm of I. It is known that a 5% excess of B has been charged into the reactor. The exit stream from the reactor is sent to a separator which generates a product A and B Catalyst +I A + 2B+C →→→ AB2 + C Reactor 3 Separator Figure 2: Polymer synthesis 5 Products and unreacted reactants Catalyst +I stream containing AB2 and any unreacted reactants and a catalyst stream containing the recovered catalyst and any impurities. Assuming a basis of 45 moles/h of product AB2 and steady state, (a) Without performing any calculations, identify the limiting reagent in this reaction. (b) Calculate the composition of the feed stream. (c) How much of the catalyst mixture (C+I) is required for the assumed basis? (d)) Calculate the composition of the catalyst stream leaving the separator (e) In order to reduce the cost of the catalyst, it is suggested that all the recovered catalyst be recycled completely back into the reactor. Is there any issue with this set up? If there are any issues, how can they be rectified? (f) A modified recycle stream is shown in Figure 3. It is desired to maintain the impurity concen- tration at 400 ppm at the inlet to the reactor. How much of the fresh Catalyst (0 ppm of I) must be charged to the reactor to maintain this constraint ? (g) How much of the recovered catalyst is purged? (h) If pure catalyst costs $125/mole and the impure catalyst (400 ppm) costs $ 85/mole, compute if including the recycle stream is cost effective. Fresh catalyst 2 A and B Reactor Separator Recycle 6 Products and unreacted reactants Figure 3: Polymer synthesis with recycle 5 Catalyst +I Purge
Introduction to Chemical Engineering Thermodynamics
8th Edition
ISBN:9781259696527
Author:J.M. Smith Termodinamica en ingenieria quimica, Hendrick C Van Ness, Michael Abbott, Mark Swihart
Publisher:J.M. Smith Termodinamica en ingenieria quimica, Hendrick C Van Ness, Michael Abbott, Mark Swihart
Chapter1: Introduction
Section: Chapter Questions
Problem 1.1P
Related questions
Question
Please only answer parts d, e, f

Transcribed Image Text:A co-polymer AB2 is to be made from its constituent monomers A and B according to the equation
where C is a catalyst required for the reaction. It is known that the reaction also generates an
impurity I at a rate of 0.001 moles of I/ mole of AB2 generated. A manufacturing process is set up
in such a way that a feed stream containing pure A and B are sent to the reactor along with another
stream of catalyst C which contains 400 ppm of I. It is known that a 5% excess of B has been charged
into the reactor. The exit stream from the reactor is sent to a separator which generates a product
A and B
Catalyst
+I
A + 2B+C →→→ AB2 + C
Reactor
3
Separator
Figure 2: Polymer synthesis
5
Products and
unreacted reactants
Catalyst
+I
stream containing AB2 and any unreacted reactants and a catalyst stream containing the recovered
catalyst and any impurities.
Assuming a basis of 45 moles/h of product AB2 and steady state,

Transcribed Image Text:(a) Without performing any calculations, identify the limiting reagent in this reaction.
(b) Calculate the composition of the feed stream.
(c) How much of the catalyst mixture (C+I) is required for the assumed basis?
(d)) Calculate the composition of the catalyst stream leaving the separator
(e) In order to reduce the cost of the catalyst, it is suggested that all the recovered catalyst be
recycled completely back into the reactor. Is there any issue with this set up? If there are any
issues, how can they be rectified?
(f) A modified recycle stream is shown in Figure 3. It is desired to maintain the impurity concen-
tration at 400 ppm at the inlet to the reactor. How much of the fresh Catalyst (0 ppm of I)
must be charged to the reactor to maintain this constraint ?
(g) How much of the recovered catalyst is purged?
(h) If pure catalyst costs $125/mole and the impure catalyst (400 ppm) costs $ 85/mole, compute
if including the recycle stream is cost effective.
Fresh
catalyst
2
A and B
Reactor
Separator
Recycle
6
Products and
unreacted reactants
Figure 3: Polymer synthesis with recycle
5 Catalyst
+I
Purge
AI-Generated Solution
Unlock instant AI solutions
Tap the button
to generate a solution
Recommended textbooks for you
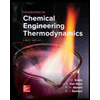
Introduction to Chemical Engineering Thermodynami…
Chemical Engineering
ISBN:
9781259696527
Author:
J.M. Smith Termodinamica en ingenieria quimica, Hendrick C Van Ness, Michael Abbott, Mark Swihart
Publisher:
McGraw-Hill Education
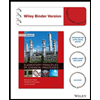
Elementary Principles of Chemical Processes, Bind…
Chemical Engineering
ISBN:
9781118431221
Author:
Richard M. Felder, Ronald W. Rousseau, Lisa G. Bullard
Publisher:
WILEY
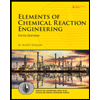
Elements of Chemical Reaction Engineering (5th Ed…
Chemical Engineering
ISBN:
9780133887518
Author:
H. Scott Fogler
Publisher:
Prentice Hall
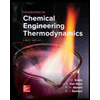
Introduction to Chemical Engineering Thermodynami…
Chemical Engineering
ISBN:
9781259696527
Author:
J.M. Smith Termodinamica en ingenieria quimica, Hendrick C Van Ness, Michael Abbott, Mark Swihart
Publisher:
McGraw-Hill Education
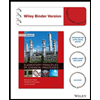
Elementary Principles of Chemical Processes, Bind…
Chemical Engineering
ISBN:
9781118431221
Author:
Richard M. Felder, Ronald W. Rousseau, Lisa G. Bullard
Publisher:
WILEY
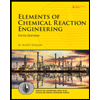
Elements of Chemical Reaction Engineering (5th Ed…
Chemical Engineering
ISBN:
9780133887518
Author:
H. Scott Fogler
Publisher:
Prentice Hall
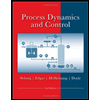
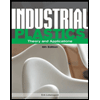
Industrial Plastics: Theory and Applications
Chemical Engineering
ISBN:
9781285061238
Author:
Lokensgard, Erik
Publisher:
Delmar Cengage Learning
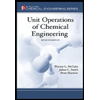
Unit Operations of Chemical Engineering
Chemical Engineering
ISBN:
9780072848236
Author:
Warren McCabe, Julian C. Smith, Peter Harriott
Publisher:
McGraw-Hill Companies, The