Part-2 (70%) A food factory uses hot water to wash and clean foods. The drained water, which has a mass flow rate of 0.1 kg/s, still have a temperature of 62°C. Consider a concept design solution of waste heat recovery for pre-heating fresh water, which has an inlet temperature of 15°C and mass flow rate of 0.2 kg/s inside tube flow. The following information can be used for your design: • 2 shell-pass and any multiple of four tube passes (4, 8, 12, etc., tube passes) heat exchanger may be considered. The shell side heat transfer coefficient could be assumed as 300 W/m²K. • The most popular copper pipe of 15 mm internal diameter could be used. Total pipe length should not be longer than 60 meters. • For inside pipe flow, fully developed turbulent flow and Dittus and Boelter correlation may be assumed, Nu = 0.023Re 0.8 pr.n 0.7 ≤ Pr ≤ 160 Re > 10,000 where n = 0.4 for heating, n = 0.3 for cooling of fluid flowing through the tube A clear justification of the heat exchanger design and calculations should be included, also to state why it should be deployed in terms of energy saving. Assumptions: steady operating conditions, the heat exchanger is well insulated, properties are constant, the thermal properties for the shell side water can be assumed based on 45°C, and the thermal properties in tube side water can be assumed based on 25°C; no kinetic & potential energies changes, the overall heat transfer coefficient is constant, the thickness of the tube wall is negligible. (NB: The total cost of the heat exchanger including the installation could be about £30k, and the factory may not be interested in any project that has a payback period of more than 2.5 years. If the cost of natural gas is 30 pence per kWh.)
Part-2 (70%) A food factory uses hot water to wash and clean foods. The drained water, which has a mass flow rate of 0.1 kg/s, still have a temperature of 62°C. Consider a concept design solution of waste heat recovery for pre-heating fresh water, which has an inlet temperature of 15°C and mass flow rate of 0.2 kg/s inside tube flow. The following information can be used for your design: • 2 shell-pass and any multiple of four tube passes (4, 8, 12, etc., tube passes) heat exchanger may be considered. The shell side heat transfer coefficient could be assumed as 300 W/m²K. • The most popular copper pipe of 15 mm internal diameter could be used. Total pipe length should not be longer than 60 meters. • For inside pipe flow, fully developed turbulent flow and Dittus and Boelter correlation may be assumed, Nu = 0.023Re 0.8 pr.n 0.7 ≤ Pr ≤ 160 Re > 10,000 where n = 0.4 for heating, n = 0.3 for cooling of fluid flowing through the tube A clear justification of the heat exchanger design and calculations should be included, also to state why it should be deployed in terms of energy saving. Assumptions: steady operating conditions, the heat exchanger is well insulated, properties are constant, the thermal properties for the shell side water can be assumed based on 45°C, and the thermal properties in tube side water can be assumed based on 25°C; no kinetic & potential energies changes, the overall heat transfer coefficient is constant, the thickness of the tube wall is negligible. (NB: The total cost of the heat exchanger including the installation could be about £30k, and the factory may not be interested in any project that has a payback period of more than 2.5 years. If the cost of natural gas is 30 pence per kWh.)
Oh no! Our experts couldn't answer your question.
Don't worry! We won't leave you hanging. Plus, we're giving you back one question for the inconvenience.
Submit your question and receive a step-by-step explanation from our experts in as fast as 30 minutes.
You have no more questions left.
Message from our expert:
It looks like you may have submitted a graded question that, per our Honor Code, experts cannot answer. We've credited a question to your account.
Your Question:
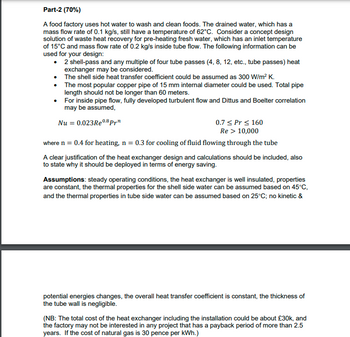
Transcribed Image Text:Part-2 (70%)
A food factory uses hot water to wash and clean foods. The drained water, which has a
mass flow rate of 0.1 kg/s, still have a temperature of 62°C. Consider a concept design
solution of waste heat recovery for pre-heating fresh water, which has an inlet temperature
of 15°C and mass flow rate of 0.2 kg/s inside tube flow. The following information can be
used for your design:
•
2 shell-pass and any multiple of four tube passes (4, 8, 12, etc., tube passes) heat
exchanger may be considered.
The shell side heat transfer coefficient could be assumed as 300 W/m²K.
•
The most popular copper pipe of 15 mm internal diameter could be used. Total pipe
length should not be longer than 60 meters.
•
For inside pipe flow, fully developed turbulent flow and Dittus and Boelter correlation
may be assumed,
Nu = 0.023Re 0.8 pr.n
0.7 ≤ Pr ≤ 160
Re > 10,000
where n = 0.4 for heating, n = 0.3 for cooling of fluid flowing through the tube
A clear justification of the heat exchanger design and calculations should be included, also
to state why it should be deployed in terms of energy saving.
Assumptions: steady operating conditions, the heat exchanger is well insulated, properties
are constant, the thermal properties for the shell side water can be assumed based on 45°C,
and the thermal properties in tube side water can be assumed based on 25°C; no kinetic &
potential energies changes, the overall heat transfer coefficient is constant, the thickness of
the tube wall is negligible.
(NB: The total cost of the heat exchanger including the installation could be about £30k, and
the factory may not be interested in any project that has a payback period of more than 2.5
years. If the cost of natural gas is 30 pence per kWh.)
Recommended textbooks for you
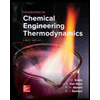
Introduction to Chemical Engineering Thermodynami…
Chemical Engineering
ISBN:
9781259696527
Author:
J.M. Smith Termodinamica en ingenieria quimica, Hendrick C Van Ness, Michael Abbott, Mark Swihart
Publisher:
McGraw-Hill Education
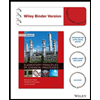
Elementary Principles of Chemical Processes, Bind…
Chemical Engineering
ISBN:
9781118431221
Author:
Richard M. Felder, Ronald W. Rousseau, Lisa G. Bullard
Publisher:
WILEY
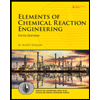
Elements of Chemical Reaction Engineering (5th Ed…
Chemical Engineering
ISBN:
9780133887518
Author:
H. Scott Fogler
Publisher:
Prentice Hall
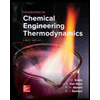
Introduction to Chemical Engineering Thermodynami…
Chemical Engineering
ISBN:
9781259696527
Author:
J.M. Smith Termodinamica en ingenieria quimica, Hendrick C Van Ness, Michael Abbott, Mark Swihart
Publisher:
McGraw-Hill Education
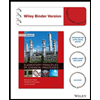
Elementary Principles of Chemical Processes, Bind…
Chemical Engineering
ISBN:
9781118431221
Author:
Richard M. Felder, Ronald W. Rousseau, Lisa G. Bullard
Publisher:
WILEY
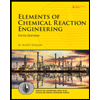
Elements of Chemical Reaction Engineering (5th Ed…
Chemical Engineering
ISBN:
9780133887518
Author:
H. Scott Fogler
Publisher:
Prentice Hall
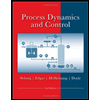
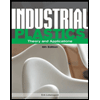
Industrial Plastics: Theory and Applications
Chemical Engineering
ISBN:
9781285061238
Author:
Lokensgard, Erik
Publisher:
Delmar Cengage Learning
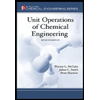
Unit Operations of Chemical Engineering
Chemical Engineering
ISBN:
9780072848236
Author:
Warren McCabe, Julian C. Smith, Peter Harriott
Publisher:
McGraw-Hill Companies, The